Robotic Laser cladding System for blades
Innovation
Laser cladding technology is the use of high-energy laser beam (104-106w/cm2) irradiation of the metal surface, simultaneous melting, expansion and solidification, the substrate surface plated with a layer of materials with special physical, chemical or mechanical properties, so as to form a new layer of alloy with a very low dilution rate, to compensate for the performance of the original substrate material, according to the requirements of the performance of the product, to obtain the heat-resistant, abrasion-resistant, resistance to electricity, corrosion, fatigue or optical, electrical and magnetic properties of the surface layer. According to the performance requirements of the products, the surface layer of heat-resistant, wear-resistant, resistance to resistance, corrosion-resistant, fatigue-resistant, or optical, electrical, magnetic and other properties. Laser cladding technology is a new technology with high efficiency and benefit, which can prepare high-performance alloy surfaces on cheap metal substrates without affecting the nature of the substrate, reducing costs and saving precious and rare metal materials.
Configuration
Item | Mode | Qty | Brand | Mark |
Laser power supply | RFL-C6000 | 1 | Raycus | Power: 6KW |
laser torch | LC300 | 1 | Duomu | Spot:2x14mm |
Powder feeder | DM-S03 | 1 | Duomu | |
Water machine | TFLW-6000WDR | 1 | TFZL | |
Robot | GP25 | 1 | Yaskawa | Load: 25KG |
Cabinet for robot | C4 | 1 | KUKA | |
Pendant | 1 | KUKA | ||
Laser control system | Customized | 1 | Duomu | Screen(Weinview) |
Table for workpiece | Customized | 1 | Duomu | |
Fume Extractor | Standard | 1 | DBYT | Power: 3KW |
Others | Customized | Some | Duomu | |
Ocuppied space | L:3.5m W:2.3m H:1.8m |
Cladding Process
●The surface of the item without oil, rust or chrome coating need to be polished or sandblasted.
●The item position, identify the solder spot, input welding parameters, simulate walking path, realize automatic surfacing.
●Selection of powder: according to the powder properties (wear resistance, corrosion resistance, high temperature resistance, etc.). The available powder: stainless steel, nickel base alloy, iron base alloy, cobalt base alloy, nickel base tungsten carbide, etc.
●Surfacing process: Preheating----Clamping----Positioning----Parameters adjustment----Execution----Finish----Dismantle----Heat preservation----Post processing.
●Ambient temperature: generally 15-25 degrees is proper, the room is with air conditioning. It must replaced with antifreeze when the temperature is below zero in case the water tank doesn’t work.
●2mm machining allowance shall be left as surfacing.

Laser metal deposition for blades in workshop↑
Hardfacing Effect ↓
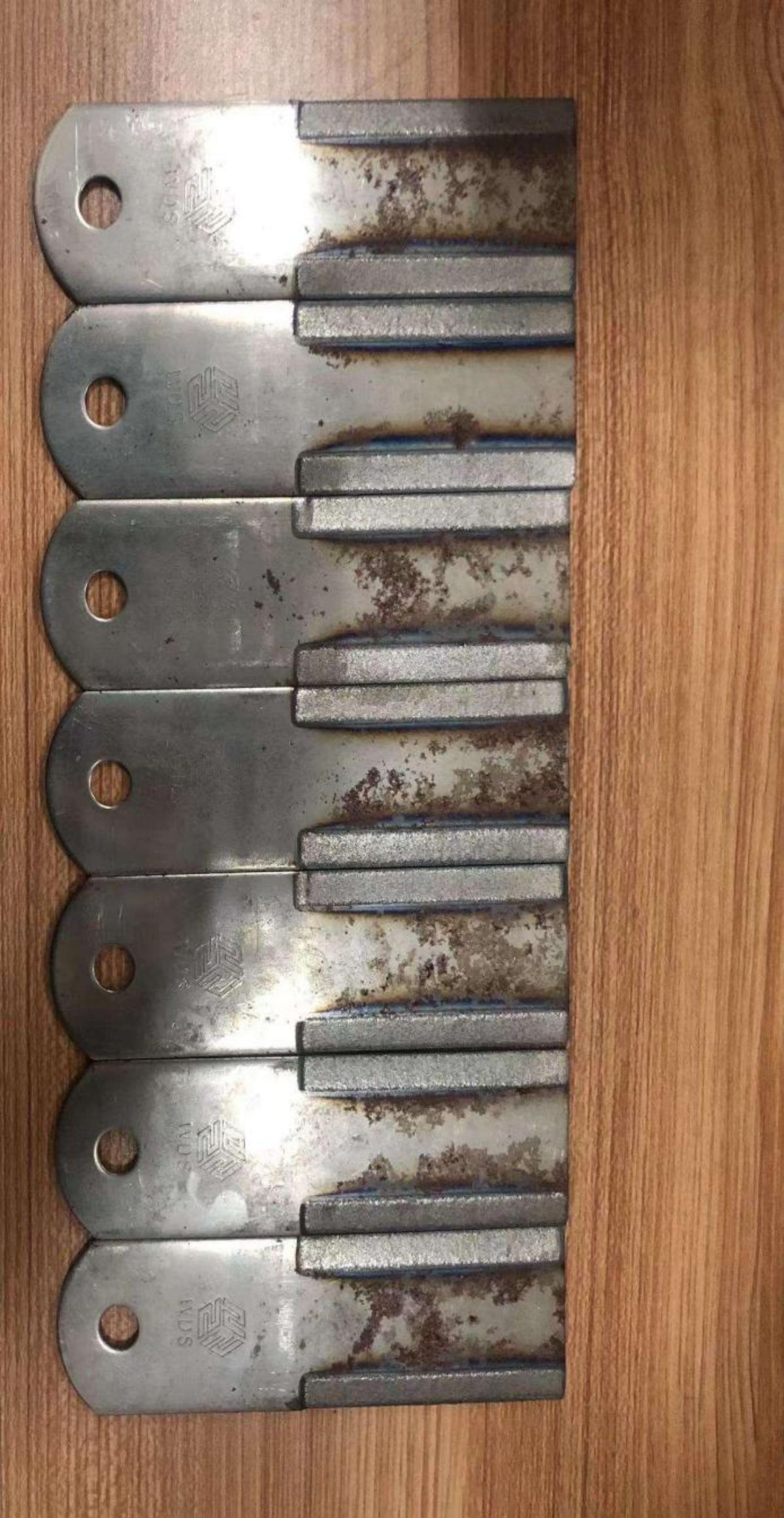
Laser metal deposition performance for blades↑
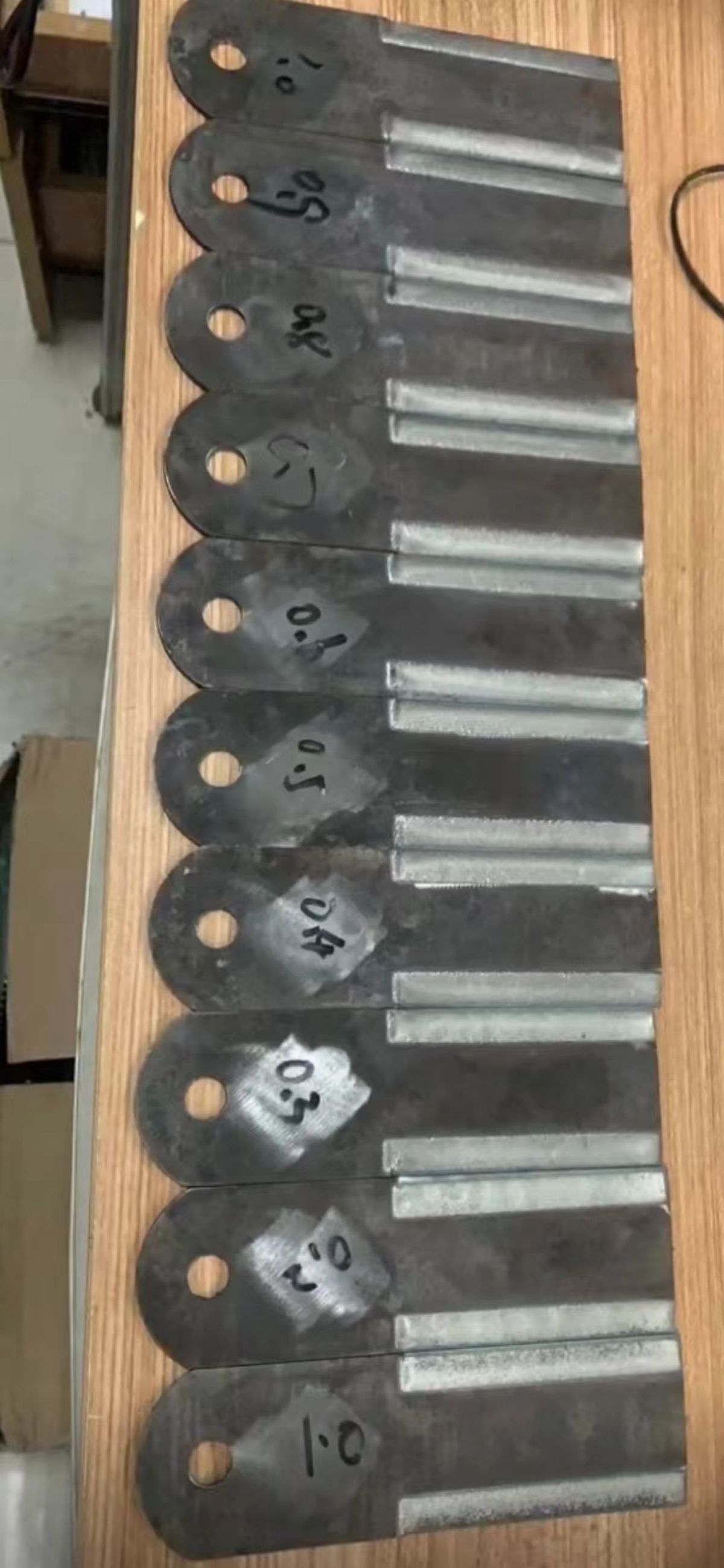
Laser cladding performance for blades↑