PTA - Plasma Transferred Arc is a high-precision, high-performance welding and cladding process, mainly used to manufacture and repair wear-resistant, high-temperature and corrosion-resistant parts. Despite its wide range of applications in the industrial field, there are some cold knowledge that may not be fully understood even by those in the industry!
1. PTA is not ordinary plasma welding!
Although PTA sounds like regular Plasma Arc Welding (PAW), there is a big difference:
- PAW (Plasma Arc Welding): Used for welding, similar to TIG welding, but with a more focused arc and deeper weld.
- PTA (Plasma Transfer Arc Welding): Mainly used for Cladding, which accurately deposits alloy powder to enhance the surface properties of the workpiece.
PTA is more of a high-end coating process than just welding!
2. Is the PTA cladding harder than diamond?
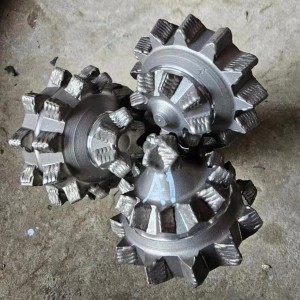
PTA can be used to overlay tungsten carbide (WC), chromium carbide (Cr₃C₂) and other super-hard alloys, with a hardness of up to HRC 70 or more, close to that of diamond (HRC 90+).
Typical applications: excavator buckets, mining drills, valve sealing surfaces, mold surface strengthening, etc.
3. How can PTA be used in rocket engines?
Aerospace organizations such as NASA and SpaceX use PTA to overlay copper alloys on the inside walls of rocket engine combustion chambers to enhance heat resistance. Because the weld layer of PTA forms a metallurgical bond with the substrate (a stronger bond than laser cladding), it can be used for long periods of time at high temperatures and pressures.
4. Stronger than laser cladding, but thicker than plasma spraying!
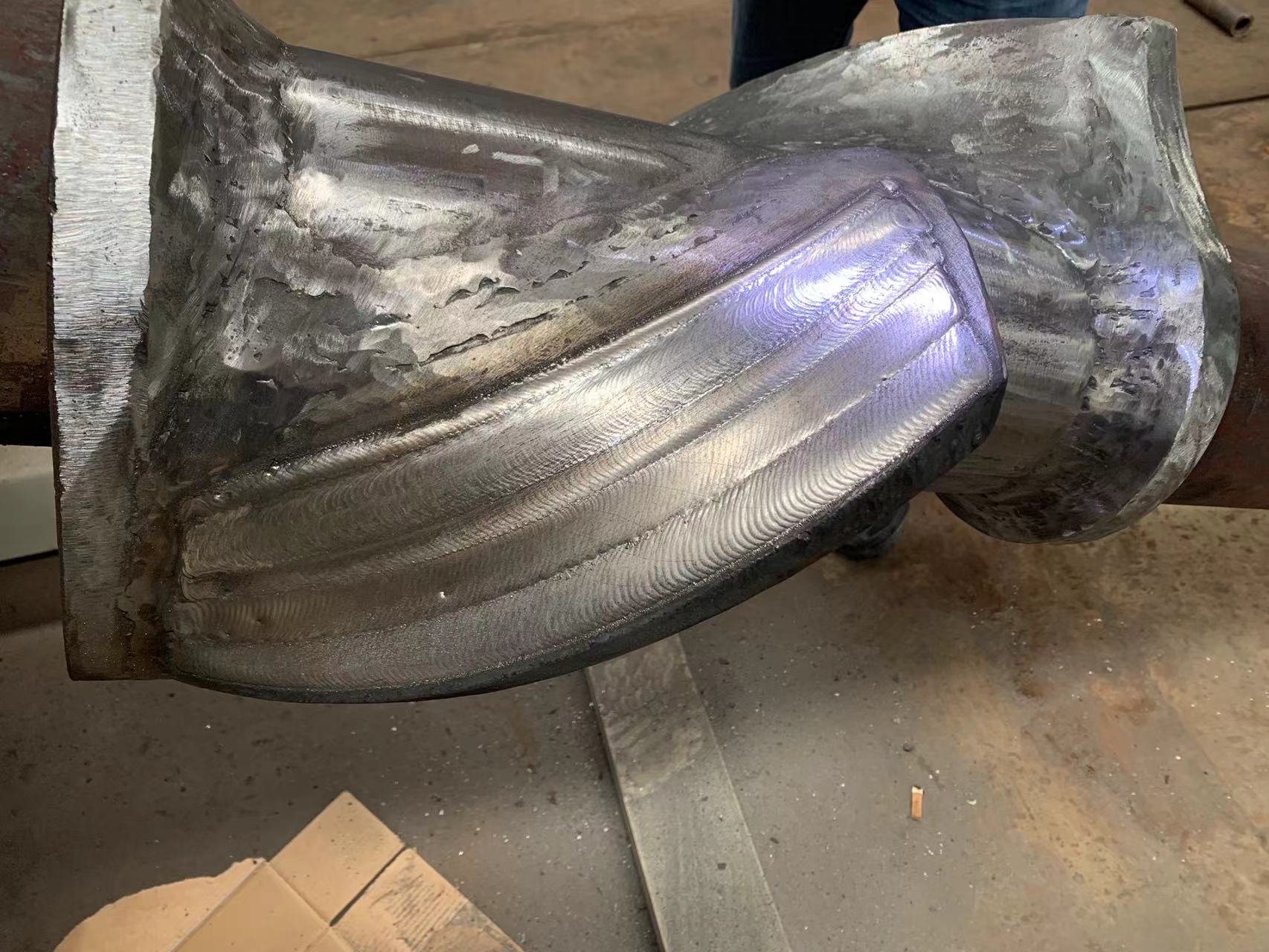
Many people confuse PTA, laser cladding (LC) and plasma spraying (APS), but the difference is clear:
Process | Bonding method | Coating thickness | Scope of application |
PTA welding | Metallurgical bonding | 0.5-5mm | Wear-resistant, corrosion-resistant, high temperature-resistant |
Laser cladding | Metallurgical bonding | 0.2-2mm | Strengthening of precision parts |
Plasma cladding | Mechanical bonding | 50-500μm | High-temperature heat-insulating coating |
5. The powder saving rate of PTA is 30% higher than that of laser cladding!
When PTA cladding, the powder utilization is as high as 85%-95%, while laser cladding usually has a utilization of only 50%-70%. This means that PTA cladding is much cheaper, especially when using expensive powders (e.g. nickel- and cobalt-based alloys), which can result in significant savings in material costs!
6. Can PTA also “fix” broken parts?
- Broken molds, turbine blades, valves, bearings and other high-value parts, PTA can be directly cladding repair, cheaper than replacing new products by more than 80%!
- Aviation, automotive, paper, steel industry are using PTA to extend equipment life.
7. PTA + Robotics = High precision unmanned welding!
With the PTA + Robotic Welding System, it can be done:
- Automated and precise welding
- High consistency of welded seams
- Remote monitoring, unattended production
- Combined with AI visual inspection, intelligent repair can be realized.
In the future, PTA may become one of the core processes of intelligent manufacturing! PTA welding is far more powerful than it seems, not only for high-end manufacturing (aerospace, nuclear, military), but also for everyday mechanical repairs and enhancements. It is more wear-resistant, more material-efficient, has higher bond strengths than conventional welding, and is even more cost-effective than some laser technologies! If you are interested in a specific application of PTA welding? Contact us!
Post time: Mar-28-2025