There are many different welding methods, each with its own unique principles, advantages and disadvantages, and areas of application. The following is a detailed description of common welding methods, including principles, characteristics, advantages and disadvantages, areas of application, and comparative analysis with other welding methods.
1. Classification of welding methods
Welding methods can be roughly divided into the following categories:
• Melt welding (e.g., arc welding, laser welding, etc.): fusion of metals by heating them to a molten state.
• Pressure welding (e.g., friction welding, diffusion welding, etc.): joining of metals by the action of pressure, without melting.
• Brazing (e.g. soft brazing, hard brazing): joining workpieces using low melting point filler materials.
2. Common Welding Methods Explained
2.1 SMAW - Shielded Metal Arc Welding
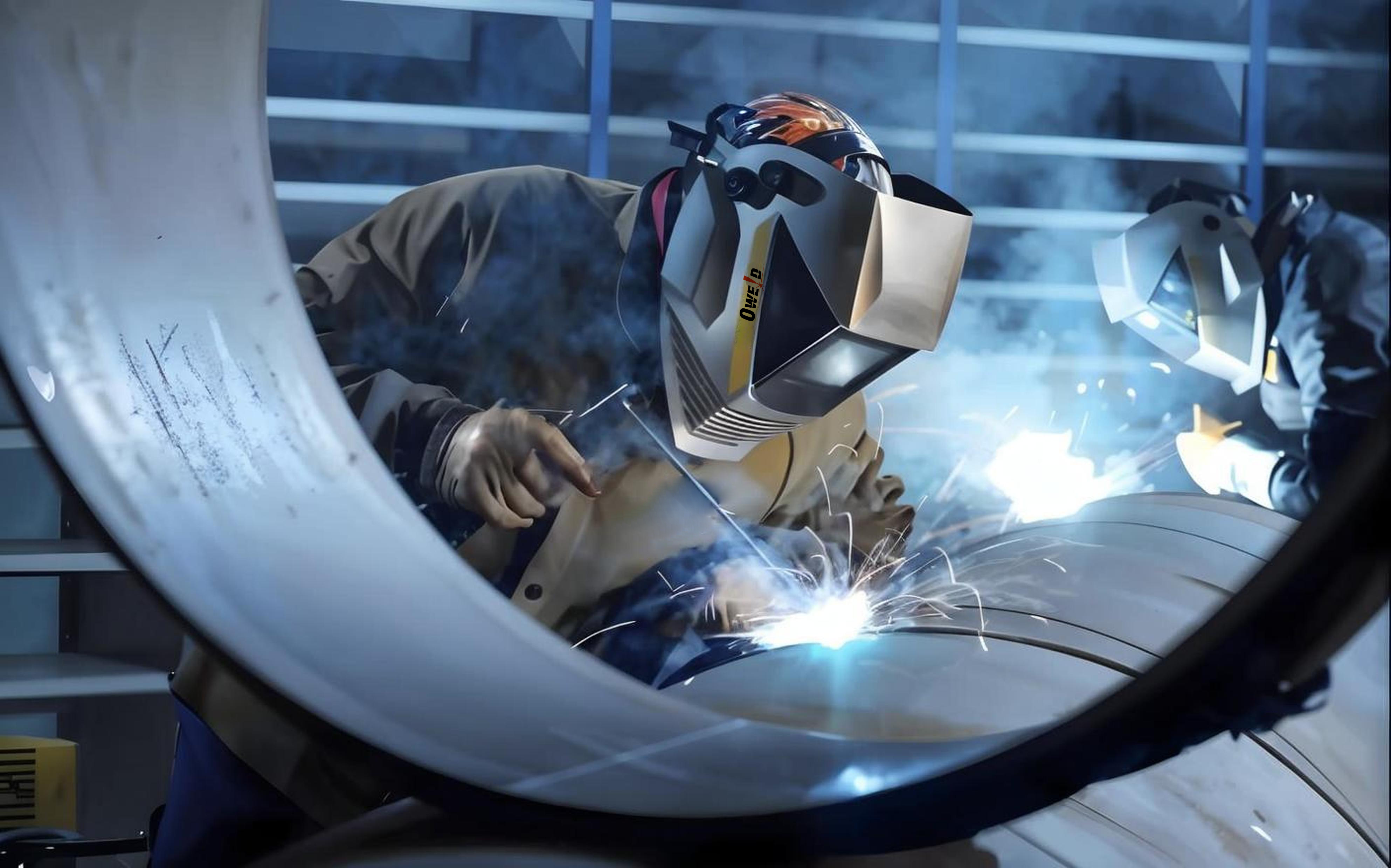
Principle: Manual arc welding utilizes an arc between the electrode and the base material to generate high temperatures (about 4000°C) to melt the electrode and the base material and form a weld. The electrode coating produces protective gas during the welding process to prevent the weld from being oxidized.
Features:
Welding with welding rod (core + flux coating).
Suitable for welding in different positions, such as stand-up welding and back-up welding.
Can be operated outdoors with low environmental requirements.
Advantages:
Simple equipment, flexible operation, suitable for field or maintenance work.
Can weld various metals, such as carbon steel, stainless steel, cast iron, etc.
Suitable for welding complex shaped workpieces.
Disadvantages:
Low welding efficiency, welding rod needs to be replaced frequently.
The quality of weld is greatly affected by the welder's technique, and it is easy to produce welding defects (such as porosity and slag).
Welding produces more fumes and dust, which is more polluting to the environment.
Applications:
Suitable for construction, maintenance, bridge, pipeline, shipbuilding and other industries.
Suitable for small-scale projects and field operations.
2.2 GMAW - Gas Metal Arc Welding
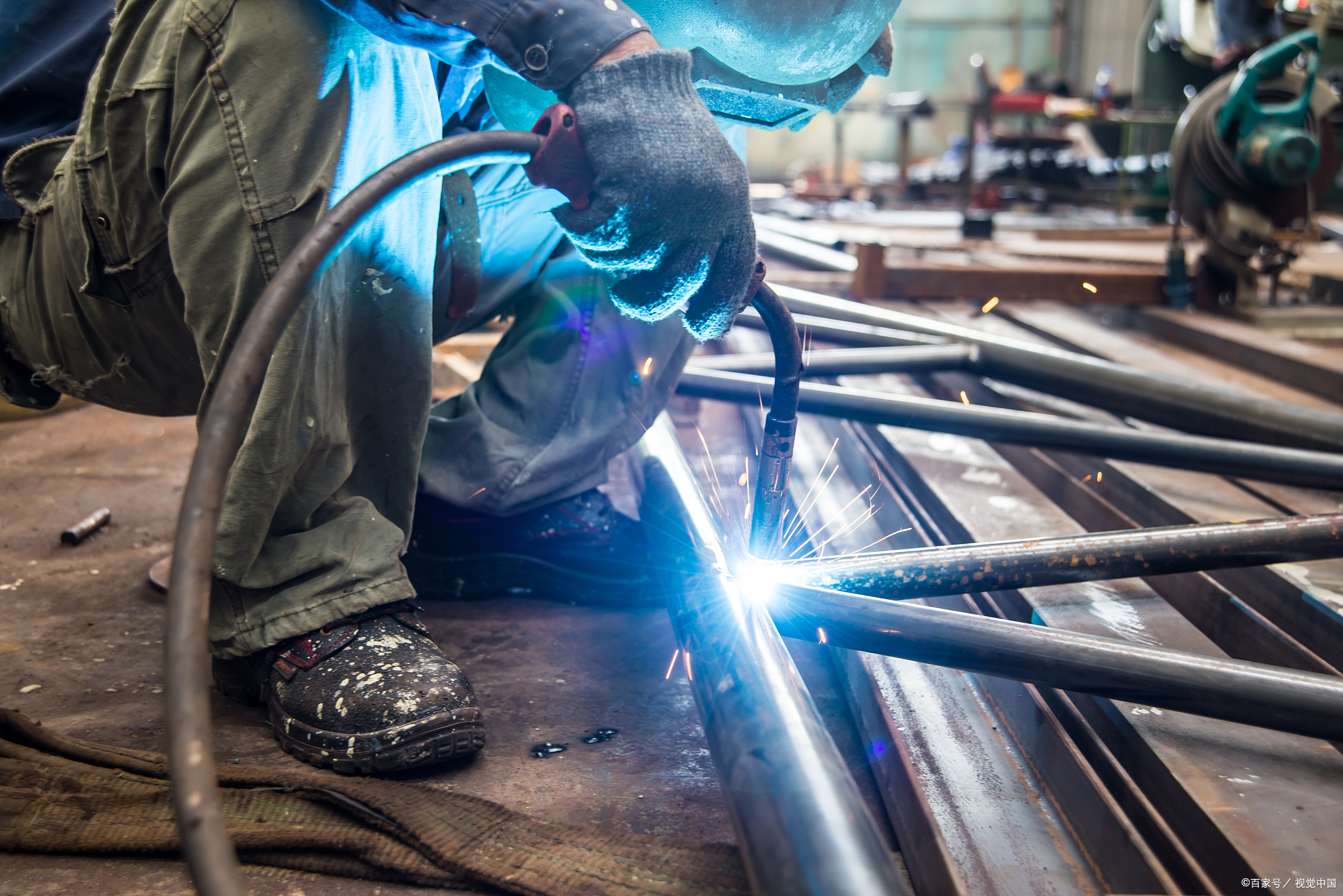
Principle: Gas shielded welding uses a continuously fed wire as the electrode, generating an arc in a protective gas (such as argon, carbon dioxide) environment, melting the wire and base material to form a weld.
Classification:
MIG (Metal Inert Gas) Welding: using inert gas (such as argon), suitable for aluminum alloys, stainless steel and other materials.
MAG (Metal Active Gas) welding: the use of active gas (carbon dioxide or mixed gas), suitable for mild steel, structural steel welding.
Features:
Adopting automatic wire feeding to improve welding efficiency.
Smooth weld surface and stable welding quality.
Sensitive to environment (wind, humidity), not suitable for outdoor construction.
Advantages:
Fast welding speed, suitable for mass production.
Can be used for thin plate welding, small deformation.
Easy to realize automated welding, such as robot welding.
Disadvantages:
Higher equipment cost, need gas supply system.
Cannot be used in a strong wind environment, otherwise the protective gas is blown away, affecting the quality of the weld.
Suitable for clean metal surfaces, not suitable for serious rust or oil stained workpieces.
Applications:
Automobile manufacturing, ships, bridges, home appliance industry, etc.
Suitable for high efficiency and high quality industrial production.
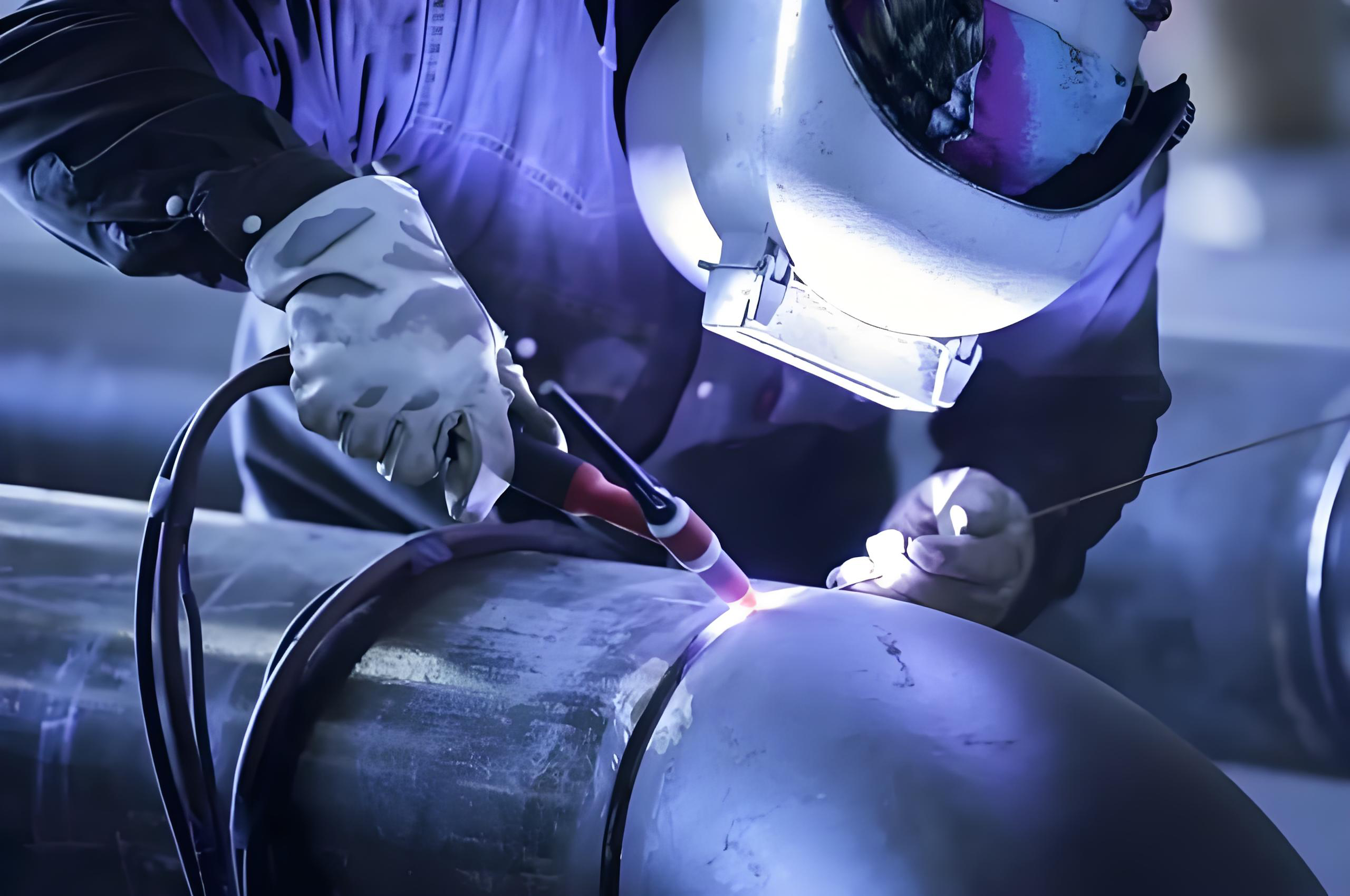
Principle: TIG welding uses a non-meltable tungsten electrode to generate an arc, which melts the base metal and filler metal under argon protection to form a weld.
Features:
High weld quality, smooth and beautiful weld.
Suitable for high-precision welding, such as aerospace, medical equipment.
Suitable for thin plate and non-ferrous metal (aluminum, copper, titanium) welding.
Advantages:
Weld seam without spatter, high quality, suitable for precision welding.
Suitable for dissimilar metal welding.
Protective gas (argon) effectively prevents oxidation of the weld.
Disadvantages:
Slow welding speed, low efficiency.
Expensive equipment, high skill requirements for welders.
Affected by wind, not suitable for outdoor welding.
Applications:
Aerospace, electronics, medical, precision manufacturing industries.
Stainless steel pipe, aluminum alloy structural parts welding
2.4 SAW - Submerged Arc Welding
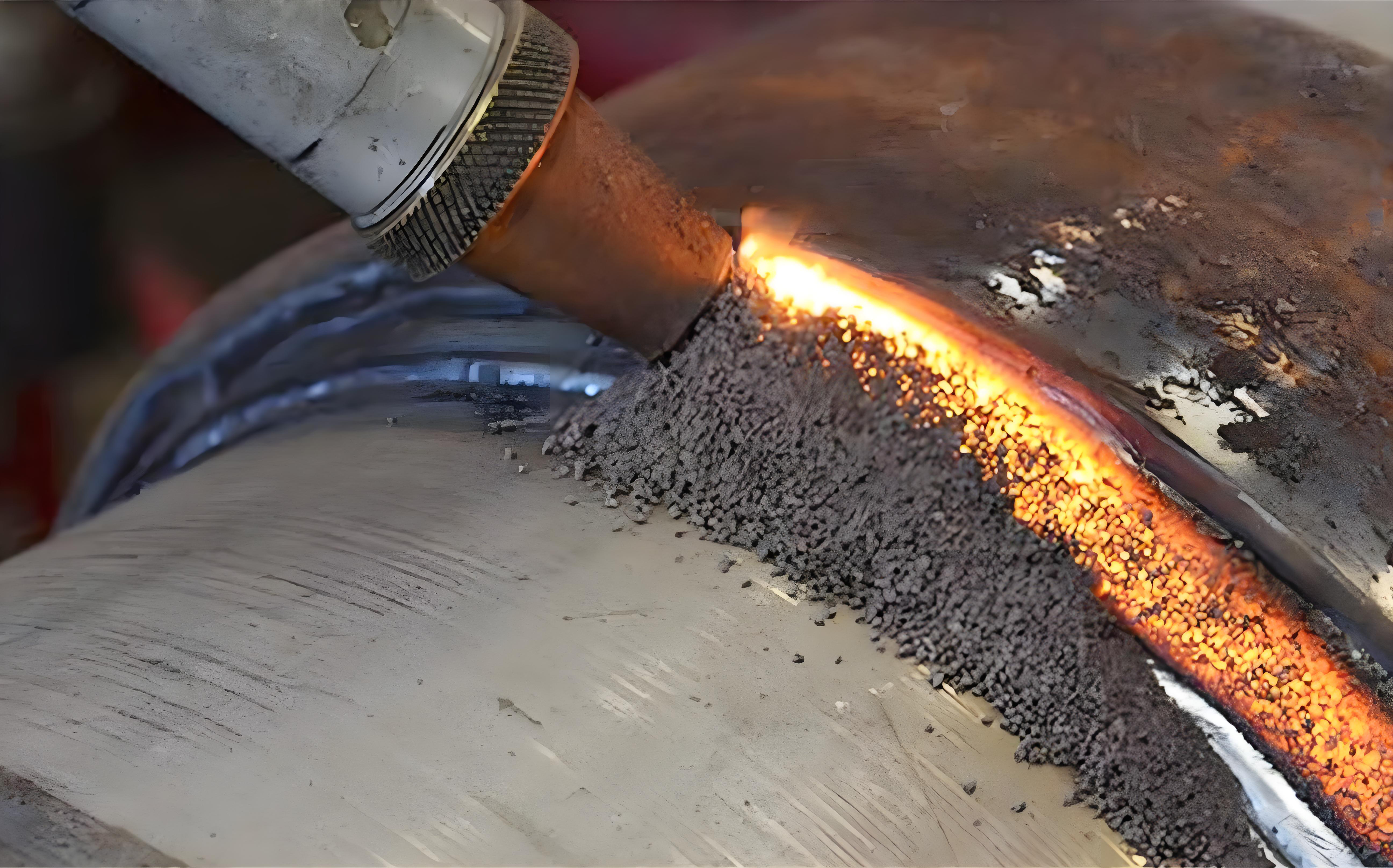
Principle: Submerged arc welding uses a flux to cover the arc, which melts at high temperatures to form a protective layer that keeps the weld free from air.
Features:
Suitable for thick plate welding, such as bridges, boiler manufacturing.
Can only be used for horizontal welding, not applicable to vertical welding, elevation welding and other positions.
Advantages:
Fast welding speed, high efficiency, suitable for mass production.
High weld quality, flux prevents welding defects (porosity, cracks).
No arc exposure, less welding fumes, improved working environment.
Disadvantages:
Can only be used for straight line welding, not applicable to complex shape welding.
Larger equipment, not suitable for small parts welding.
Applications:
Thick plate, pipe, bridge, pressure vessel welding.
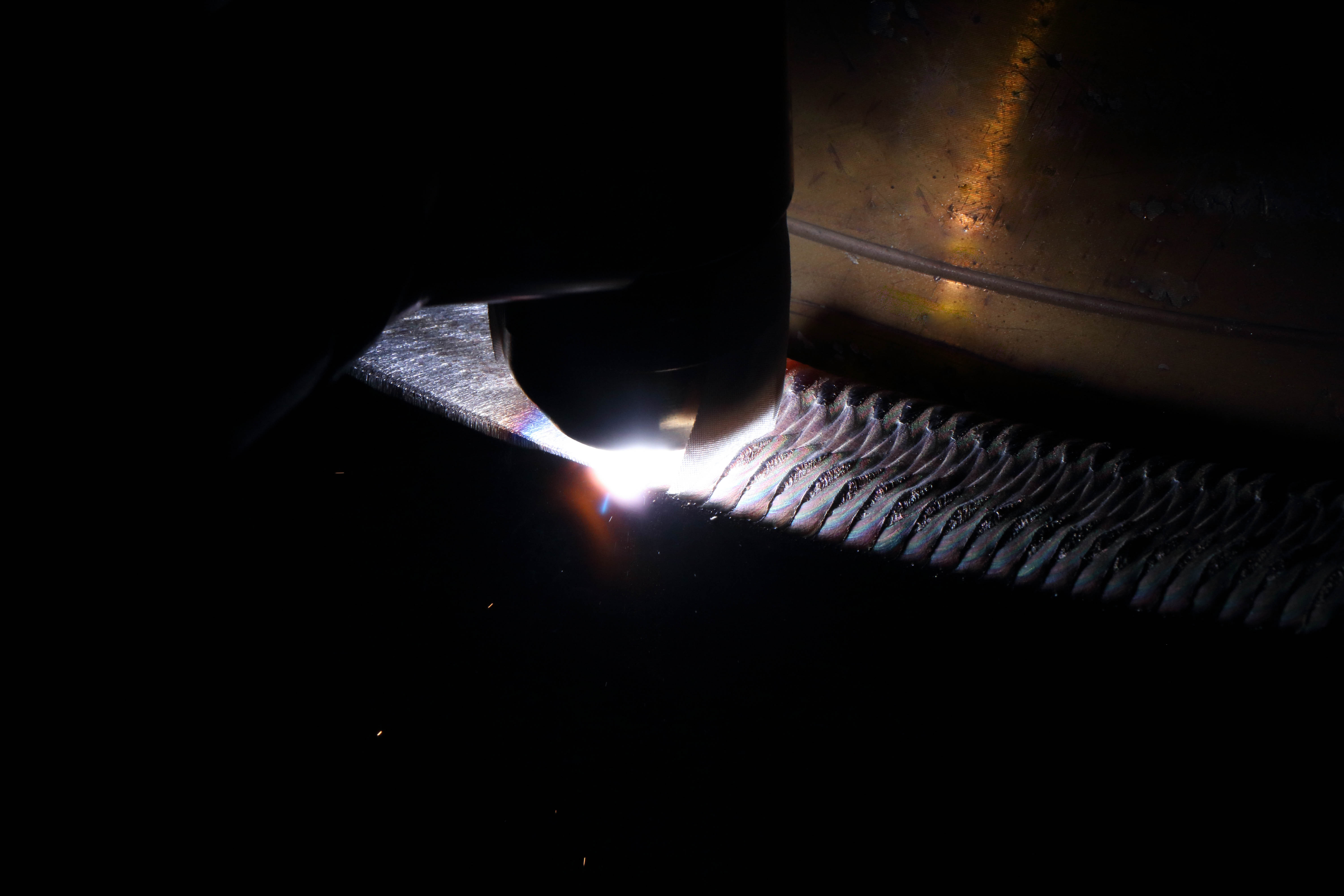
Principle: Welding using a high-temperature plasma arc to melt metal.
Advantages:
Concentrated energy, small welding distortion.
Suitable for precision welding, such as thin-walled materials.
Disadvantages:
High cost of equipment, complex maintenance.
High operating skill requirements.
Applications: aerospace, medical equipment, electronics industry.
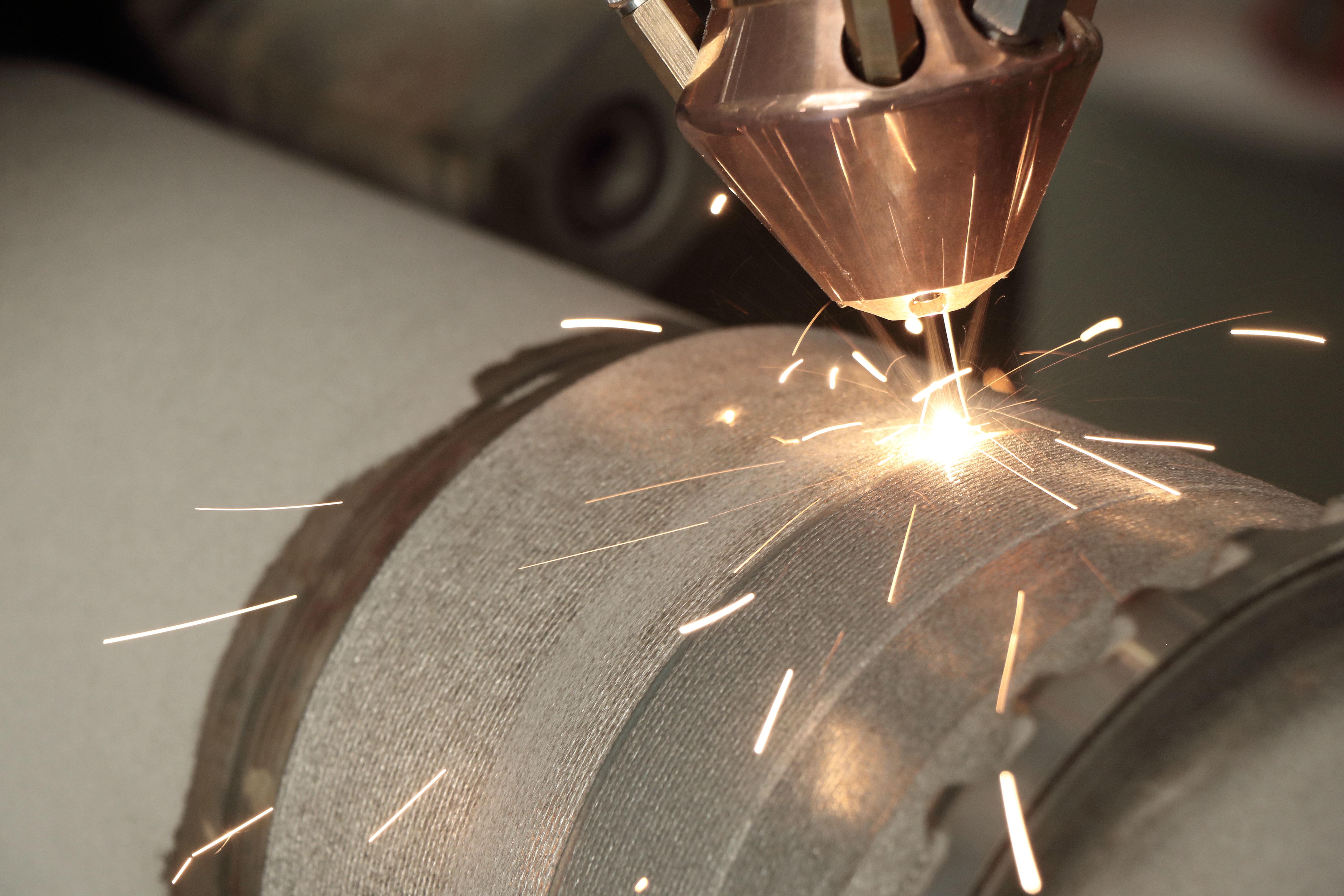
Principle: Using high energy density laser beam to melt metal for welding, narrow weld seam, small heat affected zone.
Advantages:
High precision, suitable for tiny parts welding.
Small heat affected zone, small deformation.
Disadvantages:
Expensive equipment, high maintenance costs.
Requires high precision assembly, small weld gap.
Applications: electronics, automotive, medical devices, optical equipment.
2.7 EBW - Electron Beam Welding
Principle: Melts the welding material using a high-energy electron beam in a vacuum environment.
Advantages:
High melting point materials (titanium, tungsten, zirconium) can be welded.
Large welding depth, suitable for welding thick plates.
Disadvantages:
Needs to be performed in a vacuum environment, expensive equipment.
Applications: aerospace, nuclear energy, precision instrument manufacturing.
2.8 FW - Friction Welding
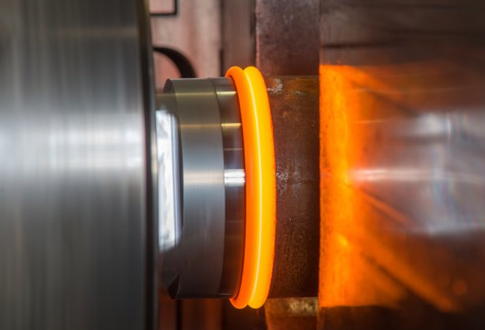
Principle: Friction welding utilizes two workpieces rotating at high speed and contacting each other to generate frictional heat, softening the contact surfaces and applying pressure to form a strong connection.
Characteristics
No melting, solid state welding, avoiding the defects of fusion welding (such as porosity, cracks).
Suitable for dissimilar metal welding, such as aluminum-copper, stainless steel-carbon steel, etc.
Fast welding speed, usually in a few seconds.
Advantages
High weld quality, no filler material required
Suitable for automated production with high repeatability.
Low welding distortion, excellent mechanical properties.
Disadvantages
Suitable for round or regular shaped workpieces, such as shaft parts.
Higher equipment costs.
Applications
Automobile drive shafts, drilling tools, spacecraft parts, etc.
Rail transportation, aviation engine manufacturing.
Post time: Mar-14-2025