Laser welders are commonly used as welding and cladding equipment. Are you concerned that portable laser welders add portability while missing certain features compared to traditional laser welders? Curious about the benefits and some of the shortcomings of a portable laser welder versus a traditional laser welder? Watch this article to learn everything you need to know about portable laser welders!
Laser cladding meets portable design
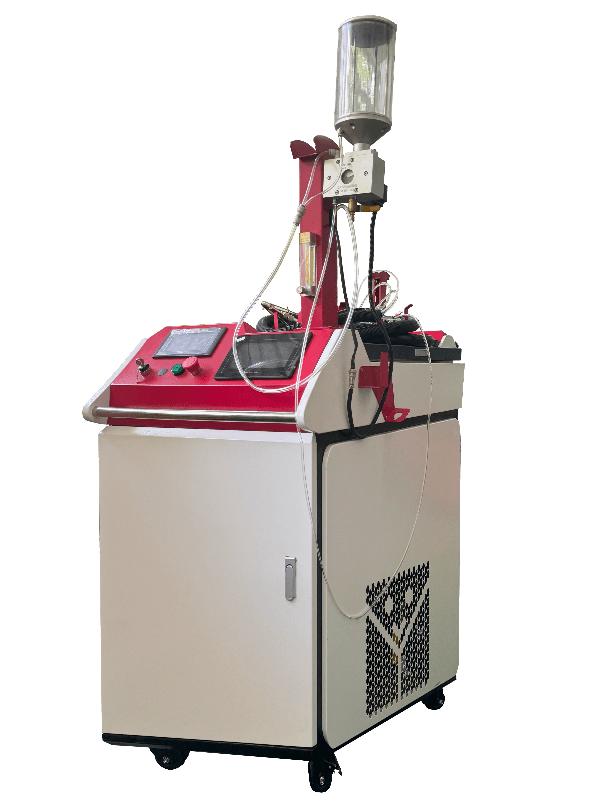
Portable laser cladding welding machine not only continues the core advantages of laser cladding technology, but also through the innovative portable design, so that it can play an efficient role in a wider range of application scenarios. Whether it is for on-site repair of large equipment, maintenance of equipment under complex working conditions, or small batch precision machining, this equipment can provide stable and reliable welding and repair results.
Features of Portable Laser Welder
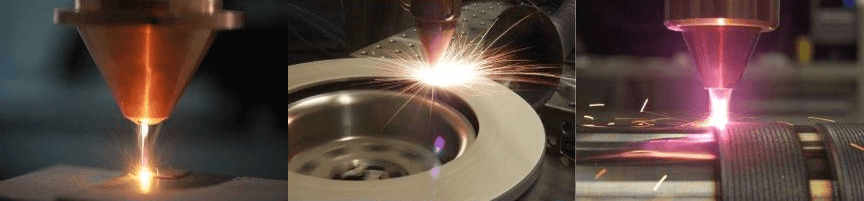
● Compact design, convenient operation: the equipment is lightweight, small size, easy to carry and on-site installation and operation, especially suitable for large equipment that is difficult to move or off-site operating environment. The welding machine can easily cope with a variety of industrial sites, reducing workpiece handling and downtime, significantly improving operational efficiency.
● Precise energy control and excellent welding quality: The laser cladding welding machine is able to precisely regulate the laser energy to achieve very high cladding accuracy. By controlling the laser output power and welding parameters, it ensures that the material is not thermally damaged during the welding process, and the cladding layer is tightly bonded to the base material, forming a wear-resistant, corrosion-resistant and heat-resistant surface.
Structure of Portable Laser Welder
The structure of portable laser welding machine is designed to meet the technical requirements of efficient welding, but also to take into account the portability and ease of operation. Its structure usually contains the following core components:
1. laser
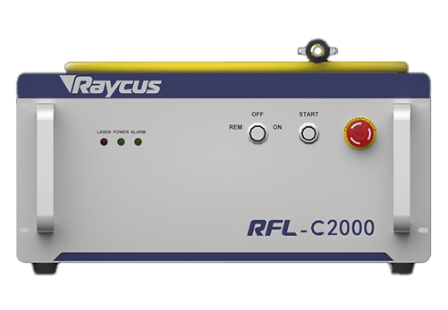
- Types: Portable laser welding machines usually use fiber lasers or semiconductor lasers. These two types of lasers are smaller and more energy efficient for portable equipment.
- Function: The laser is the core component of the welder and is responsible for generating a high energy laser beam. The beam is transmitted to the welding head through an optical fiber to complete the welding process.
- Features: Small size, high energy density, small heat affected zone, able to precisely control the welding area, suitable for welding thin-walled materials or precision parts.
2. Fiber optic transmission system
- Fiber Optic Beam Transmission: Fiber optics are used to transmit the laser beam generated by the laser from the host to the welding head to ensure concentrated laser energy transmission. The high efficiency and flexibility of the fiber optic transmission system is a key part of the structural design of the portable laser welder.
- Protection: The outer layer of the fiber is protected against damage and environmental interference to ensure stability during transmission.
3. Welding head
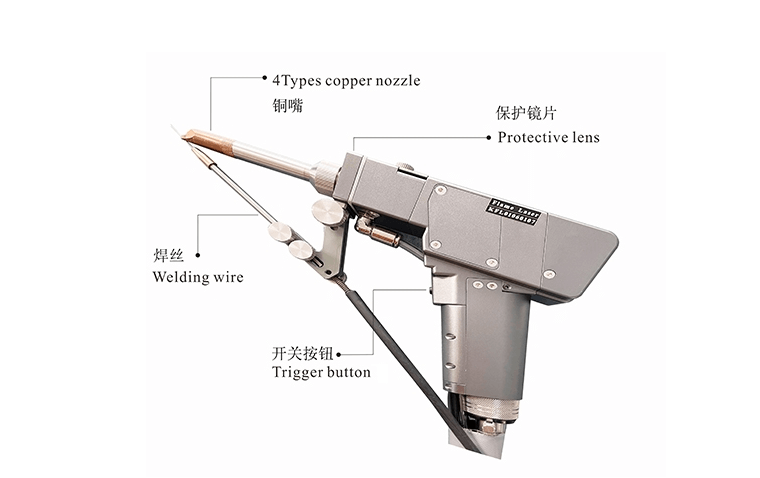
- Focusing system: The welding head is equipped with a high-precision focusing lens for focusing the laser beam to the welding spot. By adjusting the focusing distance and spot diameter, the energy distribution in the welding area can be accurately controlled to realize precision welding.
- Cooling System: Welding heads are usually equipped with an air or water cooling system to prevent overheating over long periods of time and to improve the service life of the welding head.
- Hand-held design: Welding heads are usually designed with a lightweight, ergonomic hand-held design that makes it easy for the operator to work at different angles and in tight spaces. The handheld head has integrated control buttons to quickly start or stop the welding process.
4. Control system
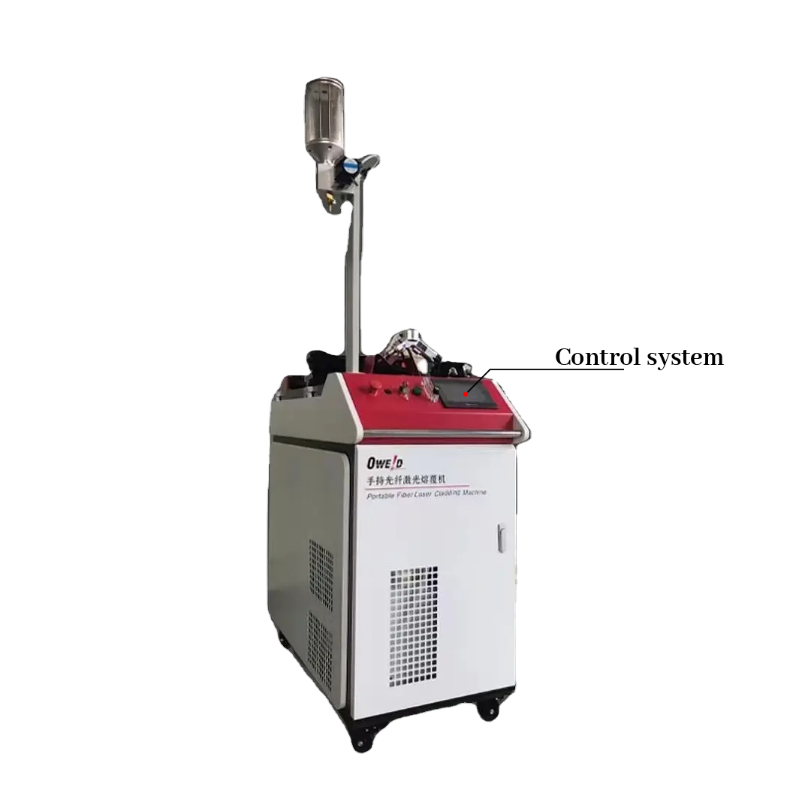
- Main Control Module: The welder has a built-in intelligent control system for monitoring and adjusting key parameters such as laser output power, pulse frequency, focus position, etc. to ensure a stable welding process.
- Display and operation interface: generally equipped with LCD display or touch screen, real-time display of equipment status, welding parameters and fault alarm information. The operation interface is designed to be simple and easy to operate.
- Programmable function: some portable laser welding machine has programmable function, users can preset the welding program, for different materials and processes to quickly switch parameters to adapt to different welding needs.
5. Power supply system
- Built-in or external power supply: In order to ensure portability, some laser welding machines are powered by built-in batteries, and some devices are equipped with external power modules. The built-in power supply makes the equipment suitable for on-site operation, especially in environments where power supply is inconvenient.
- Efficient energy management: The power supply system is equipped with an intelligent energy management function, which can adjust the output according to the actual power demand during the welding process, reduce energy consumption and increase the endurance time.
6. Cooling system
- Water-cooled or air-cooled: In order to ensure the stability of long-time work, portable laser welding machine is usually equipped with water-cooled or air-cooled system. The main task of the cooling system is to dissipate heat for the laser, welding head and other components to prevent high temperature affecting performance.
- Compact structure: the cooling system is designed to be compact and will not add excessive weight and volume to the equipment, maintaining portability.
7. Housing and Rack
- Lightweight materials: In order to ensure portability, the welder's casing is usually made of lightweight, strong materials (such as aluminum alloy or high-strength plastics), with impact resistance, dust and corrosion resistance.
- Integrated design: Simple structural design, the welder's modules are compactly arranged, easy to carry and transport. It usually comes with a portable carrying handle or shoulder strap so that it can be easily moved under different working conditions.
8. Safety system
- Protection devices: The laser welding machine integrates a variety of safety protection measures, such as overheating protection, overload protection, laser shield, etc., to ensure the safety of the operator.
- Fault Alarm: An intelligent fault monitoring system is set up inside the equipment. When the laser output is abnormal, the temperature is too high or the cooling system is malfunctioning, the equipment will automatically alarm and stop working to prevent further damage.
Summarize
The structure of portable laser welding machine integrates laser, fiber optic transmission system, handheld welding head, intelligent control system, power supply and cooling system. It not only has the advantages of high efficiency and precision of traditional laser welding machines, but also realizes high mobility and on-site operation possibilities through its lightweight design and flexible operating system. This design makes the portable laser welder an ideal tool for all types of industrial welding, repair, and surface treatment work.
Convenient Laser Welder vs Conventional Laser Welder
Portable laser welder is significantly different from traditional laser welder in terms of structure, function and application scenarios. The following is a detailed comparison of the two in many aspects:
1. Volume and portability
- Portable laser welding machine:
- Small size and light weight: compact design, usually made of lightweight materials, such as aluminum alloy or high-strength plastics, the weight is usually between 10-50 kg, easy to carry and transport.
- High portability: particularly suitable for on-site operation and mobility needs, such as equipment maintenance, site work or welding tasks in remote locations. Usually comes with a carrying handle or strap for easy carrying by the operator.
- Conventional laser welder:
- Large size and heavy weight: due to the high output power and complex cooling system, conventional laser welders are usually heavy and have a large footprint, requiring fixed installation.
- Fixed use: mainly used in factories or production workshops, difficult to move, suitable for large-scale production lines or environments that do not require frequent changes of workplace.
2. Laser power and welding capacity
- Portable laser welder:
- Medium power output: the power is usually between 500W and 2000W, which is enough to meet most on-site welding and repair needs. Mainly used for precision welding of small and medium-sized parts, such as metal parts repair and thin plate welding.
- Suitable for medium-thickness materials: Suitable for welding thin-walled materials and small workpieces, capable of high-precision welding, but may be limited when dealing with extremely thick or large-area metals.
- Conventional laser welder:
-High power output: power is usually above 2000W to 10000W, suitable for industrial-grade, high-intensity welding tasks, capable of welding thick metal materials or large-area parts.
- Powerful welding capability: Conventional welders can weld a wide variety of materials, including thick steel plates, aluminum alloys, and other large-volume parts, making them especially suitable for batch production lines or tasks that require handling high workloads.
3. Application Scenarios
- Portable laser welding machine:
- On-site repair and maintenance: especially suitable for on-site repair of large equipment or workpieces that cannot be moved, such as shipbuilding, petrochemical equipment, mining equipment, etc..
- Small-scale production: for small batch production of high-precision parts welding or repair, suitable for aerospace, automotive maintenance, mold repair and other fields.
- Difficult to access the operating environment: flexible operating characteristics make it more advantageous for welding operations in narrow spaces or complex working conditions.
- Traditional laser welding machine:
- Batch production line: widely used in large-scale automated production lines, such as automobile manufacturing, shipbuilding, aerospace industry, etc., suitable for high-volume and high-efficiency industrial welding tasks.
- Precision Manufacturing: Used for high-precision processing of large workpieces, such as welding, repairing and molding of large equipment components, suitable for high-intensity, continuous operation.
4. Flexibility and operation
- Portable laser welding machine:
- High flexibility: due to the equipment is lightweight, easy to carry, flexible operation, suitable for multi-angle, multi-position welding, especially in irregular or narrow operating space is more advantageous.
- Handheld operation-based: usually designed for handheld, the operator can adjust the angle and welding position according to the actual demand, suitable for personalized, small-scale welding operations.
- Traditional laser welding machine:
- Operation is relatively fixed: most traditional laser welders are fixed in one position, the object of operation is usually a standard workpiece, less flexible, requiring the workpiece to be moved to the welder for processing.
- Combination of automation and robotic arm: usually integrated with robotic arm and automated production line, high degree of operation automation, suitable for large-scale, high-precision continuous welding work.
5. Cooling system
- Portable laser welding machine:
- Lightweight cooling: due to the low power, portable welding machines usually use air cooling or small water cooling system, compact structure, lower cooling needs.
- Portable design: cooling system design is more compact in order to carry the main, suitable for short time or intermittent welding operations.
- Conventional laser welders:
- Large water-cooling system: Conventional welders with higher power usually require a complex water-cooling system for heat dissipation in order to safeguard the stability of the laser under long hours of continuous operation.
- Suitable for long time work: the cooling system is large and efficient, and can support the equipment for a long time uninterrupted high power welding.
6. Operational complexity
- Portable laser welding machine:
- Simple operation: the design pays more attention to simplicity, usually equipped with intelligent control panel or touch screen, users can quickly adjust the laser power, focal length and other parameters, easy to start. Few debugging: suitable for field operations that do not require complex programming or settings.
- Few debugging: suitable for field operations that do not require complex programming or setup, the user can adjust the welding parameters in real time according to the working conditions.
- Traditional laser welding machine:
- Complicated operation: usually requires specialized personnel to operate, more complex settings, especially when integrated with automation systems, operation and programming requirements are higher.
- Suitable for demanding processes: requires precise control of laser output power, focus position, scanning speed, etc., suitable for complex welding tasks.
7. Cost
- Portable laser welder:
- Lower cost: Due to its more simplified design of power, cooling system, etc., the purchase and maintenance cost of portable laser welder is usually lower than that of traditional laser welder, which is suitable for small and medium-sized enterprises or maintenance industry.
- Conventional laser welder:
- Higher cost: equipment purchase costs are higher, as well as maintenance and operating costs, especially in high-power, complex process industrial applications with significant input costs.
8. Maintenance and repair
- Portable laser welder:
- Simple maintenance: due to the compact design and relatively simple structure, portable laser welders are easier to maintain and repair, with lower equipment failure rates.
- Easy on-site repair: If a malfunction occurs, overhaul and replacement parts can usually be quickly performed on-site.
- Conventional laser welder:
- complex maintenance: complex equipment systems, the need for regular maintenance, and troubleshooting usually requires specialized technicians, maintenance cycle is longer.
- High maintenance cost: Due to the large equipment and high technical requirements, maintenance costs are often high, especially when it comes to high power lasers and cooling systems.
Summary
Portable laser welders excel in environments that require on-site operation, flexible welding and repair due to their lightweight, flexible and adaptable nature. Traditional laser welders, on the other hand, are better suited for batch production and long, high-power industrial applications due to their robust welding capabilities, automation and high power output. Both have their own advantages, and users can choose the right type of equipment for their specific application needs.
Post time: Sep-21-2024