With the continuous development of manufacturing technology, welding cladding technology has become an important method to improve the performance of metal materials. Choosing the right welding cladding powder can not only improve the wear resistance, corrosion resistance and fatigue resistance of the material, but also extend the service life of the equipment. This paper will discuss in detail the types of weld cladding powders, selection principles and their application in industry.
1. Welding cladding powder definition and classification
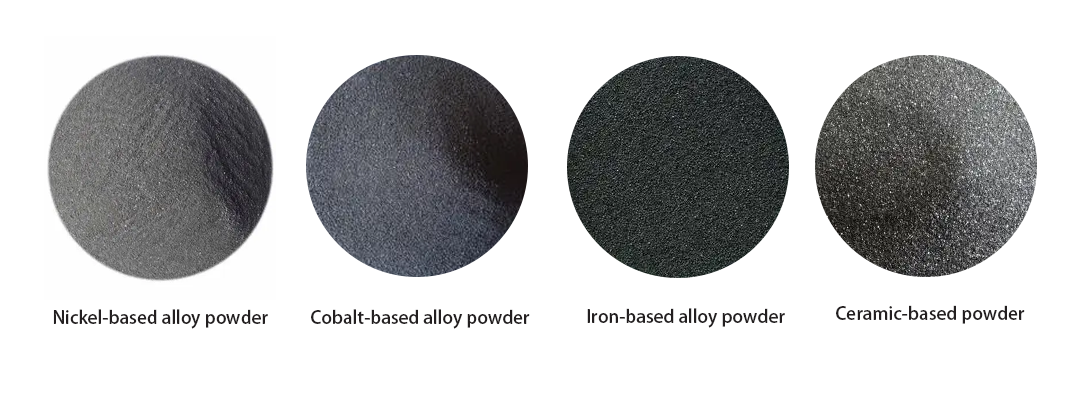
Diagrams 1Laser welding machine&plasma welding machine
Welding cladding powder is a kind of material used for surface modification and repair, which is melted and deposited on the surface of the base material by a heat source to form a layer of cladding with specific properties. According to chemical composition and usage, weld cladding powders are mainly classified into the following categories:
- Nickel-based alloy powder: with excellent high temperature and corrosion resistance, it is commonly used in high temperature and high pressure environments, such as gas turbine blades and chemical equipment.
- Cobalt-based alloy powder: with excellent wear resistance, corrosion resistance and high temperature oxidation resistance, widely used in valves, moulds and other high wear parts.
- Iron-based alloy powder: relatively inexpensive, suitable for general wear and corrosion resistance requirements, commonly used in mining equipment, agricultural machinery and so on.
- Ceramic-based powder: mainly used to enhance the wear resistance of the material, such as aluminium oxide, tungsten carbide, etc., suitable for applications under extreme wear conditions.
2. Principles for selecting welding cladding powders
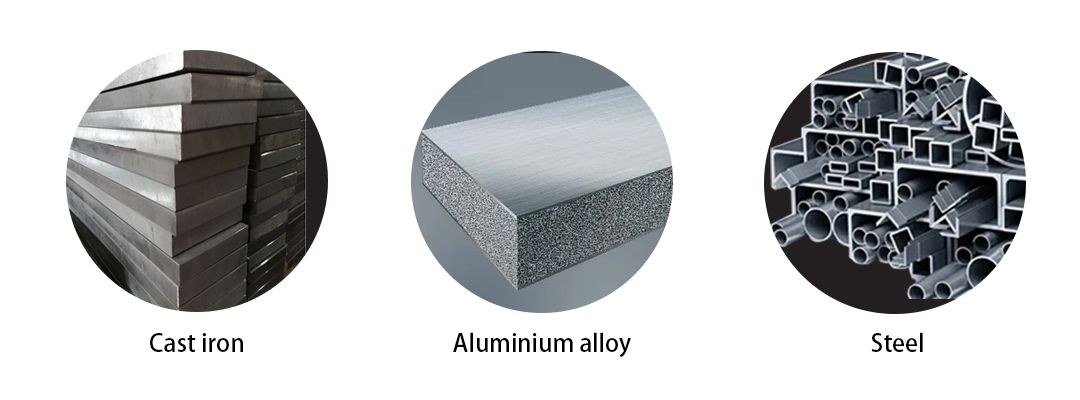
Diagrams 2 Base material
Selecting the appropriate welding cladding powder is the key to ensuring the quality of the cladding layer. The following are several important factors that should be considered when selecting welding cladding powder:
- Base material properties: different base materials (such as steel, cast iron, aluminium alloys, etc.) have different compatibility requirements for cladding powder, need to choose the right powder according to the physical and chemical properties of the base material.
- Working environment: Considering the working temperature of the cladding layer, the type of wear, corrosive media and other factors, choose the type of powder that can meet the needs of a specific working environment.
- Coating process: different coating processes (such as laser coating, plasma spraying, oxyacetylene flame spraying, etc.) on the powder particle size, morphology and mobility have different requirements, should be based on the specific process to select the appropriate powder.
- Cost-effectiveness: Under the premise of meeting the performance requirements, the economy of the powder should be considered comprehensively and the cost-effective material should be selected.
3. Welding cladding powder applications in industry
3.1 Petrochemical field
In the petrochemical field, equipment is often exposed to high temperature, high pressure and corrosive media, nickel-based alloy powder has become the preferred material for petrochemical equipment repair due to its excellent corrosion resistance. Through the cladding process, the durability of the equipment can be greatly improved, extending its service life and reducing downtime and maintenance costs.
3.2 Aerospace
The aerospace industry has very high requirements for lightweight and high strength materials and high temperature resistance. Due to its excellent high temperature performance, cobalt-based alloy powder is commonly used in the repair and surface strengthening of aero-engine parts to ensure reliable operation in extreme environments.
3.3 Mechanical Manufacturing
In the mechanical manufacturing industry, cladding powders are widely used to repair and enhance the performance of mechanical parts. Due to its lower cost and good wear-resistant performance, iron-based alloy powder is commonly used to repair worn parts of agricultural machinery, mining equipment, etc., which greatly improves the use efficiency and life of the equipment.
3.4 Automotive industry
In the automotive industry, engines, transmissions and other key components need to have high wear resistance and corrosion resistance. Surface cladding using ceramic-based powders can significantly improve the performance of parts, extend their service life and reduce maintenance costs.
4. Future prospects
With the continuous progress of science and technology, the prospects for the application of welding cladding powder in materials science and manufacturing will be broader. In the future, the development of more diversified and functionalised cladding powders will become a trend. Through the combination of innovative materials and advanced fusion cladding technology, the material performance will be further enhanced, providing strong support for the sustainable development of various industries.
For more information, please contact us!
Disclaimer:The information provided herein is for reference only, please select and adjust according to the actual application.
Note:If you wish to reprint this article, please indicate the source.
Post time: Jul-04-2024