The seam welder is a welding machine that is widely used in modern industrial manufacturing and has become an indispensable tool in many industries due to its efficient and continuous welding characteristics. In this article, we will introduce in detail the basic principles, classification, application areas and its importance in actual production of seam welders to provide readers with a comprehensive understanding and knowledge.
What is seam welder?
A seam welder is a type of welding equipment that is used to perform continuous welding operations, mainly for welding two metal workpieces together along a certain path. It works similarly to a spot welder, but the difference is that a seam welder can perform continuous welding, not just spot welding.
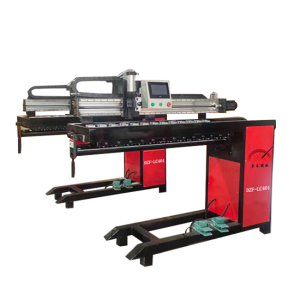
Working principle of seam welder
A seam welder works similarly to a spot welder, but it uses roller electrodes instead of the fixed electrodes of a spot welder. Two oppositely rotating circular electrodes roll continuously during the welding process, and the metal workpiece to be welded moves between the electrodes, forming a continuous weld seam by applying current and pressure. This type of welding not only realizes high production efficiency, but also ensures the uniformity and firmness of the weld seam, which is suitable for the manufacture of workpieces that need to be continuously welded for a long period of time.
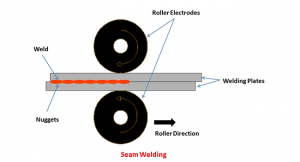
Image courtesy[1]
What is the process of seam welding?
1. Preparation phase: the metal workpiece to be welded is placed between the roller electrodes, making sure that the welding surfaces of the workpiece are clean and in close contact.
2. Pressurization stage: The roller electrode applies pressure to make the contact surface of the workpiece fit closely.
3. Energizing stage: The electric current flows through the contact surface of the workpiece through the roller electrode, generating resistance heat to melt the metal.
4. Cooling stage: stop energizing, the roller continues to rotate, the molten metal cools and solidifies, forming a continuous weld.
Difference between seam welding and spot welding
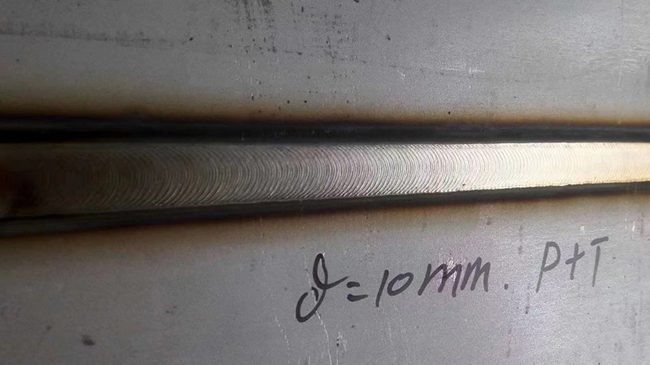
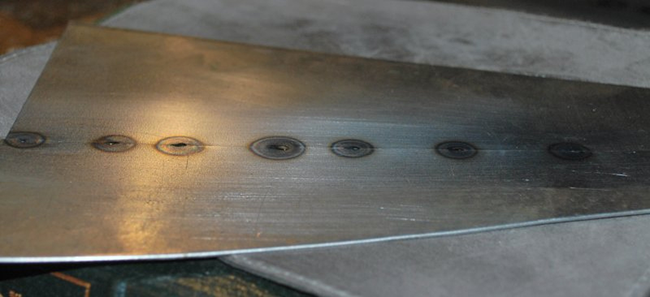
Image courtesy [2]
Welding effect
Spot Welding:
Weld joint characteristics: Weld joints are dispersed and independent, suitable for structures that do not require a continuous weld seam, strength and aesthetics: Weld joints are strong, but may not be as aesthetically pleasing as a continuous seam
Seam Welding:
Weld Seam Characteristics:The weld seam is continuous and is suitable for structures that require high strength and sealing.
Strength and Aesthetics:Welded joints are uniform in strength and smooth in appearance, suitable for products requiring a high quality appearance.
Spot welding is suitable for localized area welding with dispersed weld joints, suitable for welding thin plates and products that do not require continuous weld seams.
Seam welding is suitable for the occasions that need continuous welding, the weld seam is continuous, suitable for the products that need high strength and sealing.
Types of seam welders
According to different application requirements and material characteristics, seam welder can be divided into the following types:
• AC and DC seam welders
• Hot seam welder
• Seam welder for gas tightness
• Automatic seam welder
The importance of seam welders?
The seam welder has irreplaceable importance in actual production:
• Improve production efficiency: continuous welding method greatly improves the welding speed, suitable for mass production.
• Ensure welding quality: By precisely controlling the welding parameters, it ensures uniform and solid weld seams and reduces welding defects.
• Reduce production cost: Efficient welding process reduces labor cost and time cost, and improves the overall efficiency of the production line.
• Enhance product performance: High-quality welding effect improves the durability and safety of the product and meets the high standard production requirements.
Application areas of seam welder
Seam welders play an important role in several industries, mainly including:
• Automobile manufacturing: used for welding automobile bodies, fuel tanks, exhaust systems and other components to ensure their strength and tightness.
• Metal container manufacturing: in the manufacture of oil drums, metal tanks, pressure vessels, etc., to provide a continuous and well-ventilated weld seam.
• Home appliance manufacturing: such as the metal shell welding of refrigerators and washing machines to ensure the durability and aesthetics of the product.
• Aerospace: used for welding structural parts of airplanes and spacecraft, requiring high strength and reliability.
Where to find the best seam welding company?
Most companies will be able to meet your seam welding needs But finding the best seam welding supplier can be difficult But here at Shanghai Dolmu it's part of our business to provide you with a wide range of seam welding programs as well as seam welding machines and equipment.
Who can give you the best seam welders and equipment?
You can get the best and most practical seam welding equipment from Shanghai Duomu.
We are the most trusted and popular company when it comes to seam welding. You will never regret choosing to work with us!
Whether you need circumferential, longitudinal or any other type of seam welding equipment, you can count on us! Contact us!
Post time: Jul-27-2024