S-TIG (Super Tungsten Inert Gas Welding) is an improved welding method based on the traditional TIG (Tungsten Inert Gas Welding) process, which significantly increases the depth of penetration and efficiency by optimizing the shape of the tungsten electrode and adjusting the welding parameters. By optimizing the shape of the tungsten electrode and adjusting the welding parameters, it can significantly improve the welding depth and efficiency.S-TIG deep welding is especially suitable for single-sided welding and double-sided forming of thick plate materials, thus reducing the number of welding passes and improving productivity.
I. Working Principle of S-TIG Deep Melt Welding
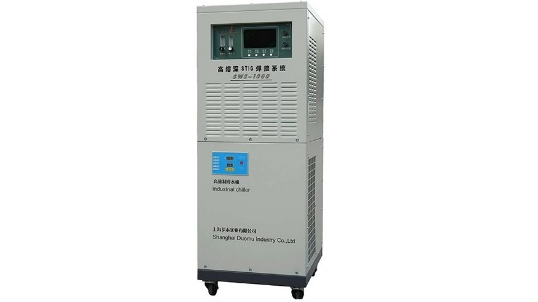
S-TIG deep fusion welding adopts specially designed tungsten electrode and enhances the welding performance through the following technical means:
1. Special shape of tungsten electrode:
- The tungsten electrode adopts optimized conical structure (e.g. smaller taper or with special groove design), which helps to concentrate the arc energy.
- This helps to concentrate the arc energy. It improves the stability of the arc, making it more concentrated and deeper, thus increasing the depth of fusion.
2. Optimized welding current:
- Use higher current densities (typically 2-3 times that of conventional TIG welding) to enhance welding heat input.
- Pulsed current regulation further increases the depth of fusion and reduces the heat affected zone.
3. Gas protection:
- Use pure argon or argon mixtures (e.g. helium or hydrogen) as the shielding gas to improve the protective effect of the weld zone and reduce oxidation.
- Adjust the gas flow appropriately to avoid arc flutter and improve welding stability.
4. Enhanced arc force:
- Utilize electromagnetic field adjustment technology to increase the impact force of the arc on the molten pool, making the molten pool deeper and narrower.
- Improve the fluidity of the molten pool, so as to realize the effect of deep melting.
II. The advantages of S-TIG deep melting welding
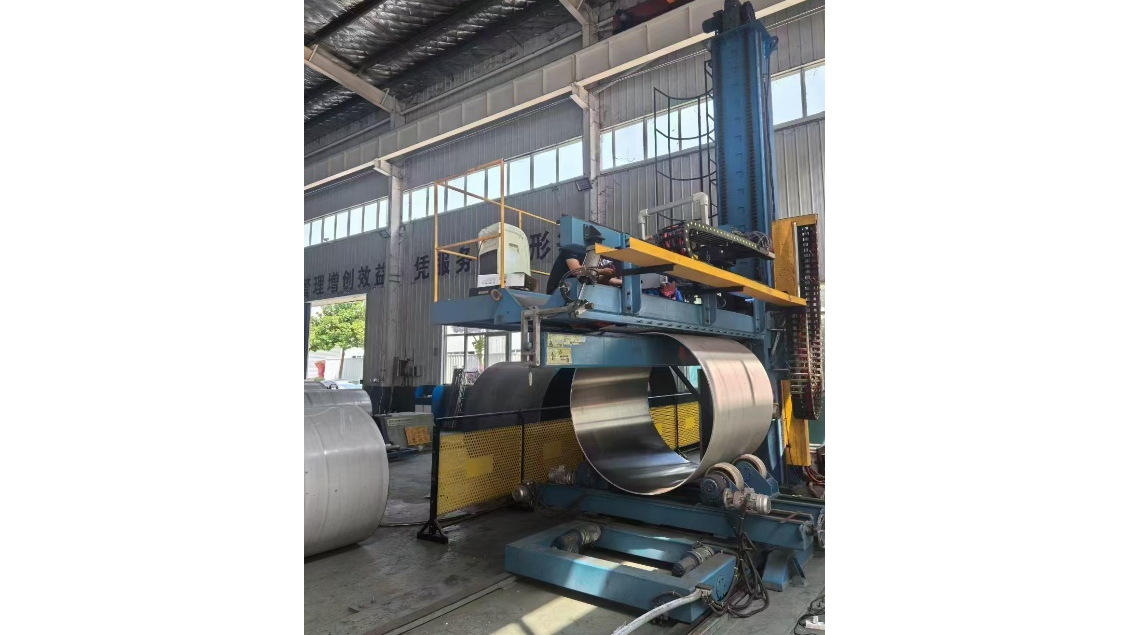
1. Significantly improve the melting depth:
- Under the same welding conditions, the melting depth of S-TIG welding increases by 2-3 times compared with conventional TIG welding, which reduces the need for multi-pass welding.
2. Reduced welding costs:
- Due to the increased depth of fusion, the number of welding passes and the use of filler material can be reduced, thus lowering the overall welding cost.
3. Higher productivity:
- Single-sided welding allows for double-sided molding, significantly reducing assembly time and welding cycle time.
4. Higher weld quality:
- Deeper molten pool and less shrinkage reduces weld distortion.
- Suitable for thick plate welding, reducing the heat-affected zone and residual stress.
5. Environmental protection and safety:
- S-TIG welding produces less fumes and harmful gases, which is more environmentally friendly than the traditional welding process.
III.Application areas of S-TIG deep melting welding

• Thick plate welding:
- Especially suitable for one-side welding of thick plates over 8mm, commonly used in pressure vessels, chemical equipment, pipelines and storage tanks.
• High-strength steel and stainless steel welding:
- In the welding of high-strength steel and heat-resistant stainless steel, S-TIG welding has good welding performance, suitable for aerospace, shipbuilding and nuclear industry.
• Repair welding:
- Due to its good penetration capacity and low heat input, S-TIG welding is also suitable for welding repair of important equipment, such as turbine blades and large castings.
IV.S-TIG deep melting welding and other welding process comparison
- Compared with conventional TIG welding, S-TIG welding has a greater depth of fusion and higher welding speed.
- Compared with MIG/MAG welding, S-TIG welding quality is higher, but the speed is relatively slow.
- Compared with plasma welding, S-TIG welding in thick plate welding performance is better, and equipment costs are relatively low.
V. Precautions for S-TIG Deep Melt Welding
1. Selection and grinding of tungsten electrode:
- Need to use a special S-TIG tungsten electrode, and ensure that the grinding direction of the tungsten electrode and the arc direction is the same, in order to reduce the arc shift.
2. Control of gas flow:
- Adjust the flow rate of protective gas appropriately to avoid the arc being affected by the gas flow and destabilized.
3. Setting of welding parameters:
- Adjust the current, voltage and welding speed according to the thickness and material of the weldment to ensure the melting depth and weld forming quality.
As an improved process of traditional TIG welding, S-TIG deep fusion welding has significant advantages in thick plate welding and high quality requirement welding. Through the optimization of tungsten electrode and welding parameters, S-TIG welding can achieve deeper penetration and higher efficiency, which is an advanced welding technology worth promoting and applying in modern manufacturing industry.
Post time: Nov-14-2024