In high temperature, high pressure, corrosive media and other harsh conditions, the traditional globe valve seat, valve flap vulnerable to wear, corrosion, scouring, resulting in seal failure, shortening the service life and increasing maintenance costs. Plasma welding technology (PTA), as an advanced surface strengthening process, can form a high hardness, wear-resistant, corrosion-resistant alloy coatings in the critical parts of the globe valve, significantly improving the service life and reliability of the valve. Compared with traditional welding, automated plasma welding technology has higher welding accuracy, more stable coating thickness and more excellent wear and corrosion resistance, has become the core technology of high-end valve manufacturing. Cut-off valve plasma welding machine is now available!
I. Understanding globe valves
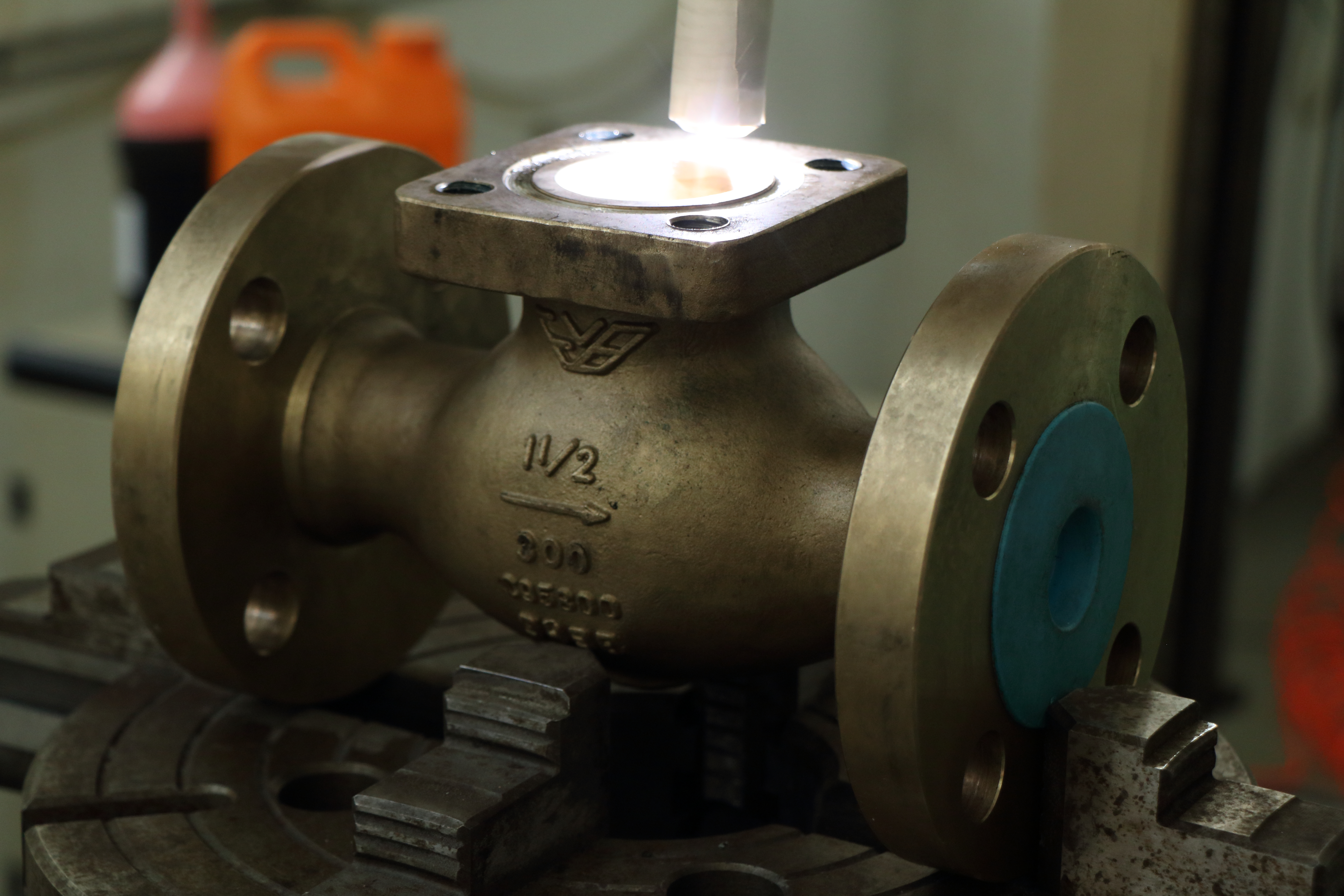
Globe Valve (Globe Valve) is a valve used to control the flow of fluid, usually used to completely close, completely open or regulate the flow. Its working principle is to rotate the handwheel to drive the valve stem up and down, so that the valve flap and the valve seat close contact or leave, so as to control the flow of media.
II.what is the globe valve plasma welding machine?
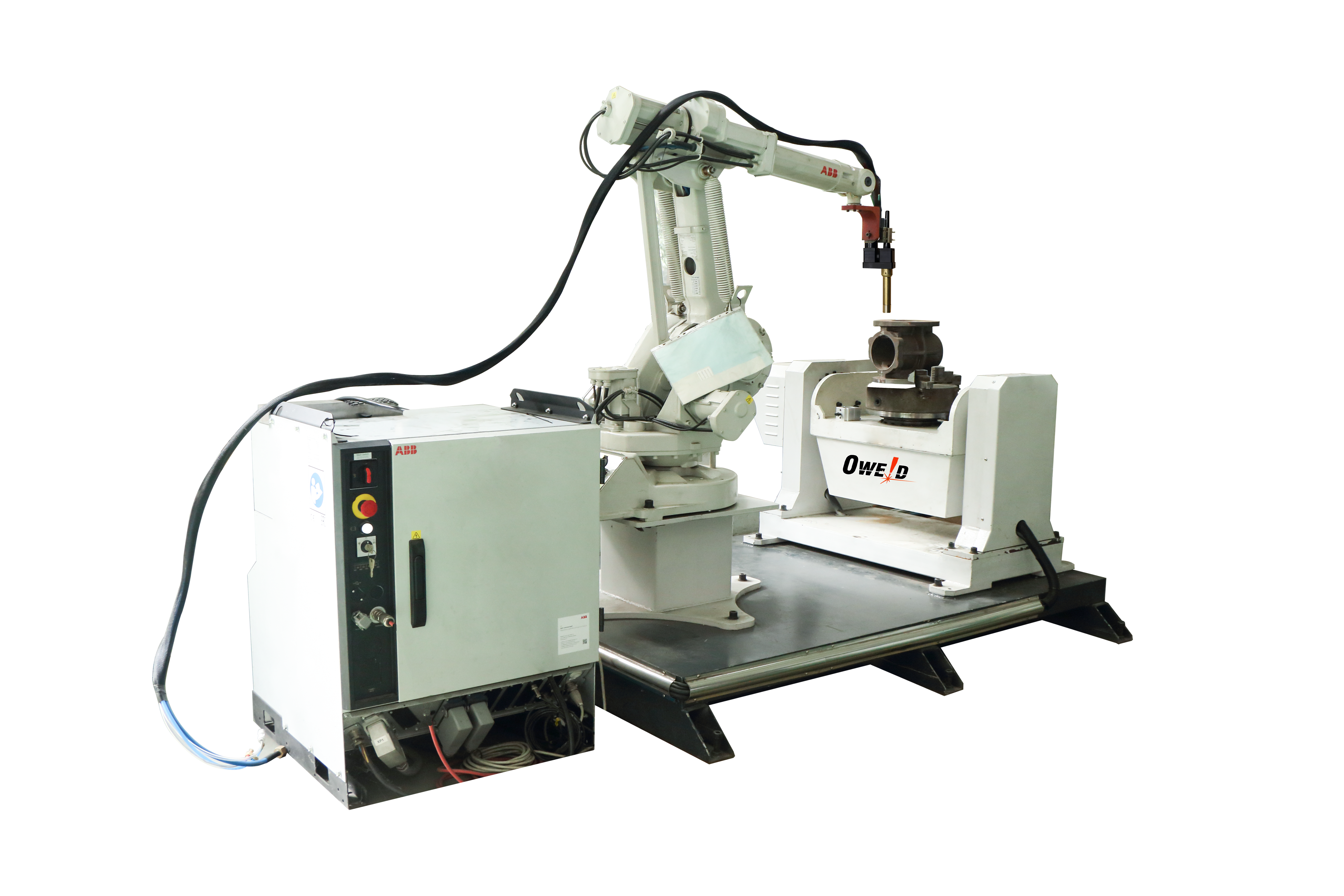
Cut-off valve plasma welding machine is a high-end welding equipment specializing in valve sealing surface strengthening and repairing, using plasma arc as a heat source, the alloy powder is not fused on the surface of the valve substrate, which significantly improves the valve's corrosion resistance, abrasion resistance and sealing performance. The technology is widely used in petroleum, chemical, electric power and other industries in the field of high-end valve manufacturing and repair.
III. the main advantages of plasma clad globe valve
1.Improve the wear resistance and corrosion resistance of globe valve
✅ High hardness welding layer: plasma welding can form a hard alloy layer (such as cobalt-based, nickel-based, iron-based alloys) on the surface of the valve seat and valve flap, which significantly improves abrasion resistance and reduces the wear failure of the valve.
✅ Corrosion resistance enhancement: high temperature, acid and alkali resistant alloy materials can be used, such as Stellite (Stellite) alloy, to improve the corrosion resistance of the globe valve in the chemical industry, oil and gas, high temperature steam and other harsh environments.
2. Enhance the service life of globe valve
✅ Reduce scouring wear: the high hardness and denseness of the fusion welding layer reduces the scouring damage of the medium on the valve seat and valve flap, thus prolonging the service life of the globe valve and reducing the maintenance cost.
✅ Reduce frequent replacement: Compared with ordinary carbon steel and stainless steel valves, the durability of fused clad globe valves is increased several times, especially suitable for high-frequency switching and piping systems in harsh environments.
3. Improve the sealing performance of globe valve
✅ Precision welding process: the plasma welding layer has extremely low porosity, which ensures high sealing between the valve flap and the valve seat, effectively reducing the risk of leakage.
✅ High temperature and high pressure resistance: suitable for steam pipelines, boiler systems, petrochemical plants and other high-temperature and high-pressure working conditions, the sealing surface can still maintain stable performance under extreme conditions.
4. High productivity and stable quality
✅ Automated operation with high stability:
Traditional welding process relies on manual operation and the welding quality is unstable, while automated plasma welding can precisely control the temperature, welding thickness and alloy ratio to ensure quality consistency.
Adopting CNC system to control the welding process reduces human error and improves production efficiency.
✅ Uniform layer thickness and controllability:
The thickness of the welding layer can be precisely controlled between 0.5mm-3mm, which is more uniform and dense than traditional welding, reducing the subsequent machining workload.
Effectively reduce the risk of valve failure due to welding deformation, stress concentration.
5. Wide range of application, adapt to a variety of working conditions
✅ Can be applied to a variety of material globe valves: plasma welding can be applied to globe valves with different base materials such as carbon steel, stainless steel, chrome molybdenum steel, titanium alloy and so on.
✅ Applicable to high temperature, high pressure, corrosive media: widely used in petrochemical, electric power, metallurgy, natural gas, nuclear power, ocean engineering and other industries.
IV.The common application areas of globe valve
• Oil and gas: high-pressure pipeline globe valves, valves for refining and chemical plants.
• Chemical industry: corrosion-resistant globe valve, such as acid and alkali media transportation pipeline.
• Power industry: boiler steam globe valve, condensate system.
• Metallurgical industry: high temperature and high pressure gas globe valve, metallurgical furnace valve.
• Marine engineering: seawater transportation valves to prevent seawater corrosion.
V. Conventional welding vs. automated plasma welding
Comparison items | Conventional welding | Automated plasma welding |
Welding quality | High human influence, unstable quality | Automation control, stable and consistent quality |
Wear resistance | Low hardness due to material limitation | Can be clad with high hardness alloy, strong wear resistance |
Corrosion resistance | General corrosion resistance | Suitable for high temperature, high pressure, corrosive environment |
Uniformity of welding layer | Uneven thickness, need a lot of machining | Uniform layer thickness, minimize subsequent processing |
Service life | Fast wear, frequent replacement | 2-5 times longer service life |
Production efficiency | Slow speed, high labor cost | Automated welding improves efficiency and reduces costs |
Applicable working conditions | Suitable for general environment | Suitable for high temperature, high pressure, corrosive environment |
IV.How to buy cost-effective plasma welding machine?
1. Clear process requirements
According to the valve material (such as stainless steel, cast steel), the thickness of the welding layer and the type of alloy to choose the type of equipment
2. Focus on the core configuration
Plasma power supply stability; - powder feeding system precision; equipment automation level.
3. Manufacturer's service capabilities
Priority is given to the provision of technical training, process program debugging and after-sales maintenance of ion welding machine manufacturers.
Fortunately, as the top supplier of plasma welding equipment in the industry, Shanghai Dolmu can meet any of your welding needs at the same time with high cost-effective. Interested in our equipment? Click here. Want to learn more? Contact us!
Post time: Feb-27-2025