Plasma Welding Torch is widely used as an efficient welding tool for high precision welding work. As its working principle involves high temperature arc and gas flow, some common problems may occur when using it. The following is a list of common problems with plasma welding torches and how to solve them:
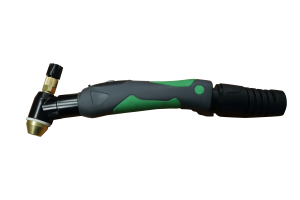
1. Welding arc instability
Cause analysis:
- The output of the welding power supply is unstable and the current fluctuates greatly.
- The nozzle or electrode of the welding gun is damaged, resulting in uneven gas flow.
- Gas supply pressure is unstable or the gas quality is not good (e.g., too much oxygen, argon impurities).
- Welding current is too low or the arc is not properly adjusted.
Solution:
- Check the welding power supply to ensure that the voltage and current are stable.
- Check and replace damaged electrodes or nozzles, maintain good electrode and nozzle clearance.
- Check the gas pressure and flow rate to ensure the purity of the supplied gas.
- Adjust the welding current and arc length so that they are within the normal operating range.
2. Unstable welding melt pool, uneven weld seam occurs
Cause analysis:
- Improperly set welding current, too high or too low may affect the stability of the molten pool.
- The gas flow rate is too large or too small, resulting in insufficient gas coverage and affecting the weld shape.
- The distance between the welding torch and the workpiece is too far or too close, resulting in an unstable arc.
Solution:
- Adjust the current and voltage appropriately according to the welding material and plate thickness.
- Adjust the gas flow to ensure uniform gas coverage and prevent gas holes or inclusions.
- Adjust the distance between the welding torch and the workpiece to maintain the proper arc length.
3. Electrode is worn out or burned out too quickly.
Cause analysis:
- Welding current is too high, resulting in overheating of the electrode.
- Insufficient gas flow and poor cooling effect.
- The presence of pollutants (such as oil, moisture, etc.) in the welding environment leads to arc instability, which in turn increases electrode wear.
Solution:
- Check and adjust the welding current to avoid too high or too low.
- Increase the gas flow to ensure good cooling effect.
- Keep the welding environment clean and avoid contamination of the workpiece surface.
4. Clogged nozzles or carbon deposits
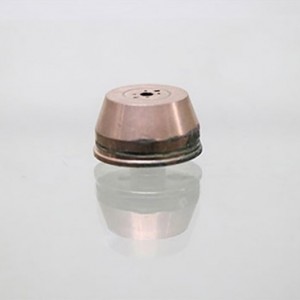
Cause Analysis:
- Insufficient or unstable gas flow leads to carbon buildup inside the nozzle.
- Use of unsuitable current or excessive arc length during welding, increasing the burden on the nozzle.
- The quality of the welding material produces excessive soot or impurities.
Solution:
- Check and clean the nozzle regularly to ensure smooth airflow.
- Adjust the current and arc length to avoid overheating the nozzle.
- Use high quality welding materials to minimize the generation of impurities.
5. Welding gun overheating
Cause analysis:
- Welding current is too high, resulting in the welding torch working too often and not enough heat dissipation.
- Excessive use of the welding process, resulting in the welding torch heat dissipation is not timely.
- Welding gun cooling system (such as water cooling or air cooling) failure or not efficient enough.
Solution:
- Control the welding time and frequency, avoid working continuously for too long.
- Check and repair the torch cooling system to ensure proper operation.
- Use proper current and welding parameters to avoid overheating. 6.
6. Gas leakage
Cause Analysis:
- Loose or deteriorated gas piping, fittings or valves, resulting in gas leakage.
- Poor sealing of the torch connection area, or high temperatures generated during welding have damaged the sealing material.
Solution:
- Periodically inspect gas piping and fittings to ensure tight connections.
- Replace deteriorated or damaged seals to avoid gas leakage.
- Use a suitable sealing material to ensure that it does not fail at high temperatures.
7. Porosity during welding

Cause analysis:
- The gas supply is unstable or impure, resulting in the protective gas not being able to completely cover the weld.
- The presence of oil, moisture or other impurities on the surface of the workpiece during welding contaminates the molten pool.
- Welding current is too low, resulting in incomplete molten pool, the gas can not effectively escape.
Solution:
- Ensure stable gas supply and qualified gas purity.
- Clean the surface of the workpiece to ensure that there is no oil, moisture or other contaminants.
- Adjust the current and welding parameters to ensure that the molten pool is fully formed to avoid gas blockage.
8. Cracks on the surface of the weld
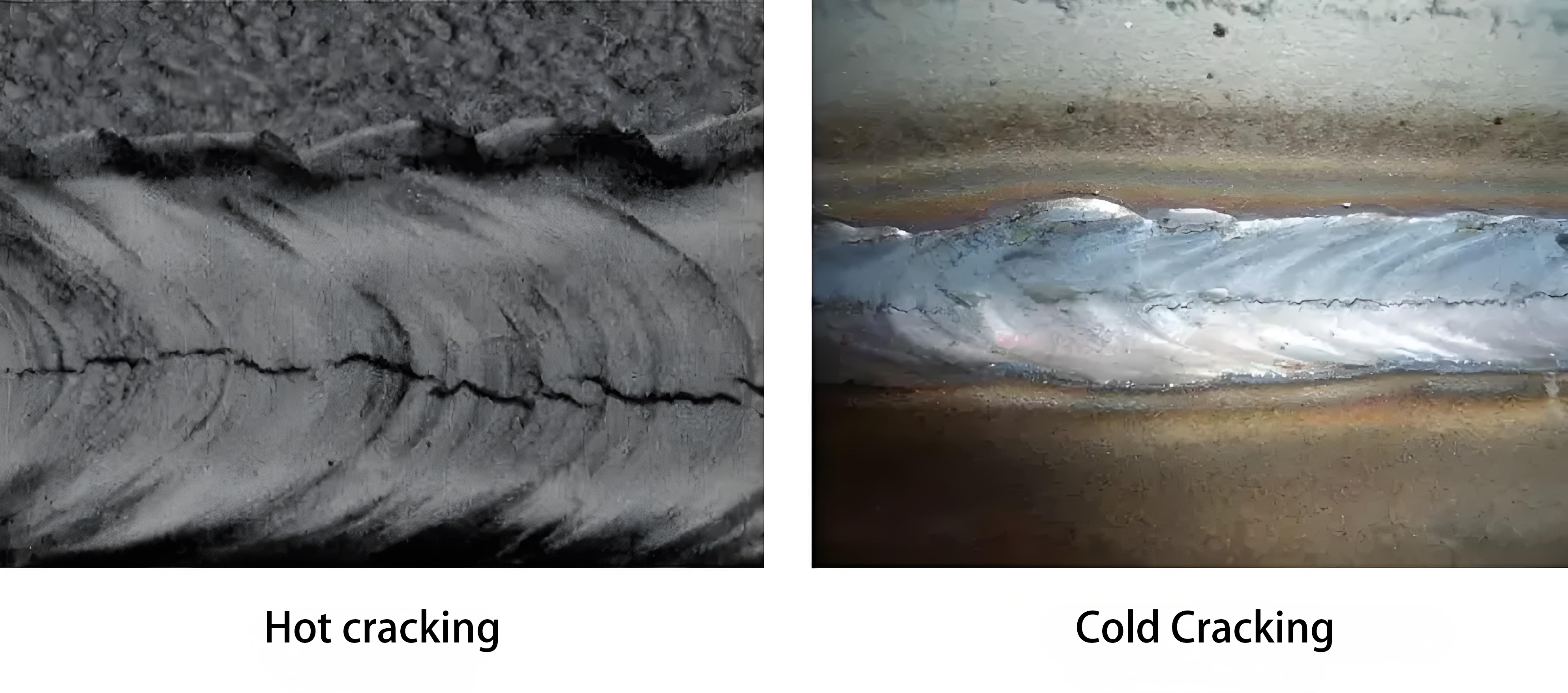
Cause analysis:
- The cooling rate during welding is too fast, resulting in excessive thermal stress.
- Poor compatibility between the welding material and the base material, or improper selection of the welding material.
- Improper welding process (such as excessive heating or uneven cooling).
Solution:
- Control the cooling rate of welding. Preheating or post-heat treatment can be used to reduce thermal stress.
- Select the appropriate welding material and make sure it is compatible with the base material.
- Adjust the welding process to avoid excessive heating or uneven cooling.
The plasma torch may encounter many problems during use, which are usually related to welding current, gas flow, nozzle and electrode maintenance, welding environment and other factors. For different problems, taking appropriate measures to adjust and repair can effectively improve the welding quality and prolong the service life of the equipment.
Post time: Nov-28-2024