Drilling tool stabilizer is an important tool to prevent well slope change in oil, gas and geological exploration drilling project, and it has the widest use, no matter it is one of the indispensable tools for increasing and decreasing slope section, or stabilizing the slope and leveling section.
Challenges for Drill Tool Stabilizers
Exposed to high temperatures, high pressures and complex chemical environments for long periods of time, the surfaces of conventional drilling tool stabilizers are susceptible to wear and corrosion, affecting their service life and operational effectiveness.
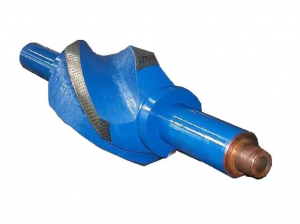
Principle and process of cladding technology
Plasma cladding technology uses plasma cladding to uniformly melt and adhere the cladding material to the surface of the tool stabilizer. This process not only ensures a high degree of densification and homogeneity of the cladding layer, but also enables the cladding material to be firmly bonded to the substrate material, forming a strong composite layer.
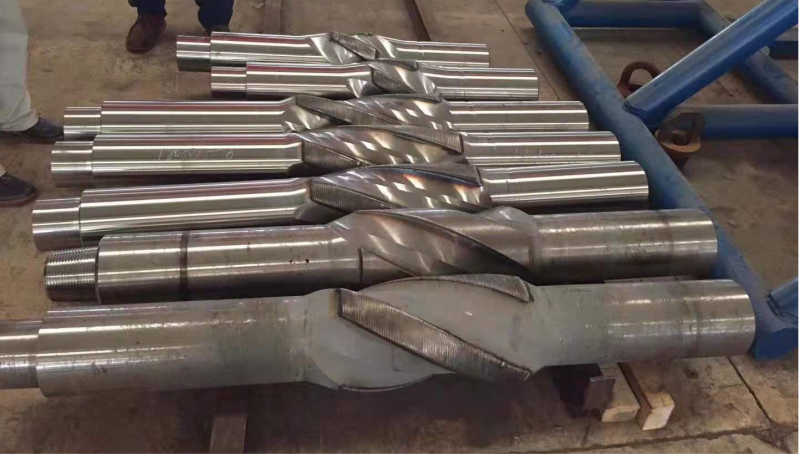
The choice of cladding material is based on “nickel-based alloys” or “cobalt-based alloys”, which are known for their excellent resistance to wear and corrosion. The surface hardness of the drilling tool stabilizers is significantly increased by the cladding treatment, which also provides excellent impact and fatigue resistance. Experimental results show that the thickness of the cladding can be adjusted to meet the needs of different downhole environments, resulting in optimal durability and economy.
Multiple advantages of cladding technology
1. Extended service life
Coating technology significantly increases the wear resistance of the tool stabilizers and reduces the rate of wear during downhole operations. This means that the life of the stabilizers is significantly extended, reducing downtime and replacement costs associated with frequent stabilizer changes.
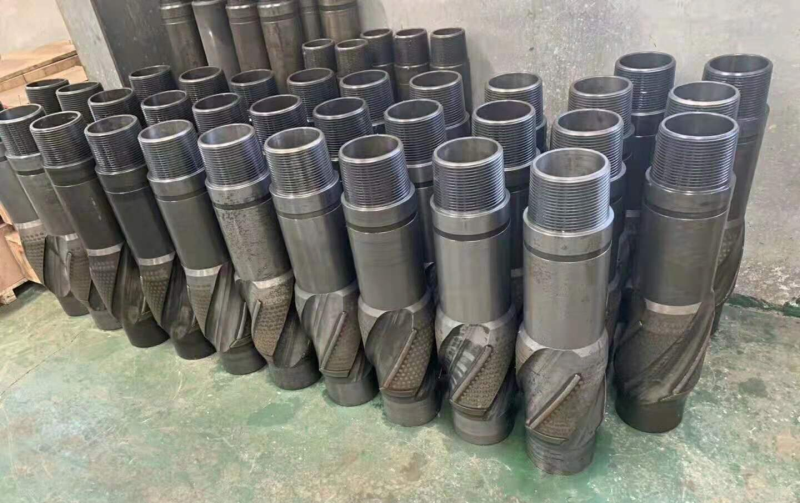
2. Improved drilling accuracy
Stabilizers maintain stable structural strength and surface integrity in the downhole environment over a long period of time, which helps to reduce borehole deviation and improve drilling accuracy. This is especially critical in deep and ultra-deep wells, where the drilling success rate can be improved.
3. Reduced operating costs
As the stabilizer life is extended, the maintenance and replacement frequency of downhole equipment is significantly reduced. At the same time, the continuity of drilling operations is ensured, reducing the additional costs associated with unscheduled downtime.
4. Enhanced Adaptability
The cladding can be customized to meet the needs of different operating environments, thus ensuring that the stabilizer can maintain excellent performance under various complex downhole conditions. Whether it is a high temperature, high pressure environment or corrosive geological conditions, the cladding technology provides effective protection.
As oil and gas exploration advances into deeper and more complex formations, the performance requirements for drilling tool stabilizers continue to increase. Shanghai DuoMu is committed to the continuous research, development and optimization of fusion cladding technology, aiming to provide the industry with better wear and corrosion resistant solutions. Contact us to learn more about cladding technology!
Post time: Aug-30-2024