How to use plasma to clad TC bearings?TC bearings usually refer to deep groove ball bearings with rubber seals, which are widely used in a variety of mechanical equipment, especially where good sealing performance is required. Long-term exposure to this environment will inevitably cause wear and corrosion. Plasma is used to melt and clad the inside of TC bearings to obtain a high hardness wear and corrosion resistant cladding. This saves the cost of replacement.
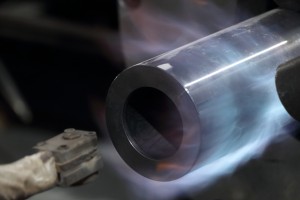
Principle of plasma cladding technology
Plasma cladding is a process in which an alloy powder is melted by a plasma arc and sprayed onto the surface of a substrate to form a high-performance coating. It is characterized by the formation of a metallurgical bond between the coating and the substrate, which significantly improves the performance of the substrate.
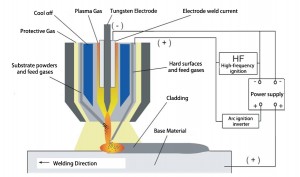
Preparation work before plasma cladding of TC bearing bore
The following is a complete set of solutions for plasma cladding of TC bearing bores, covering the process flow, technical parameters, material selection and post-treatment methods, to ensure that the performance of the bearing bores can be effectively repaired or enhanced.
What is the purpose of TC bearing cladding?
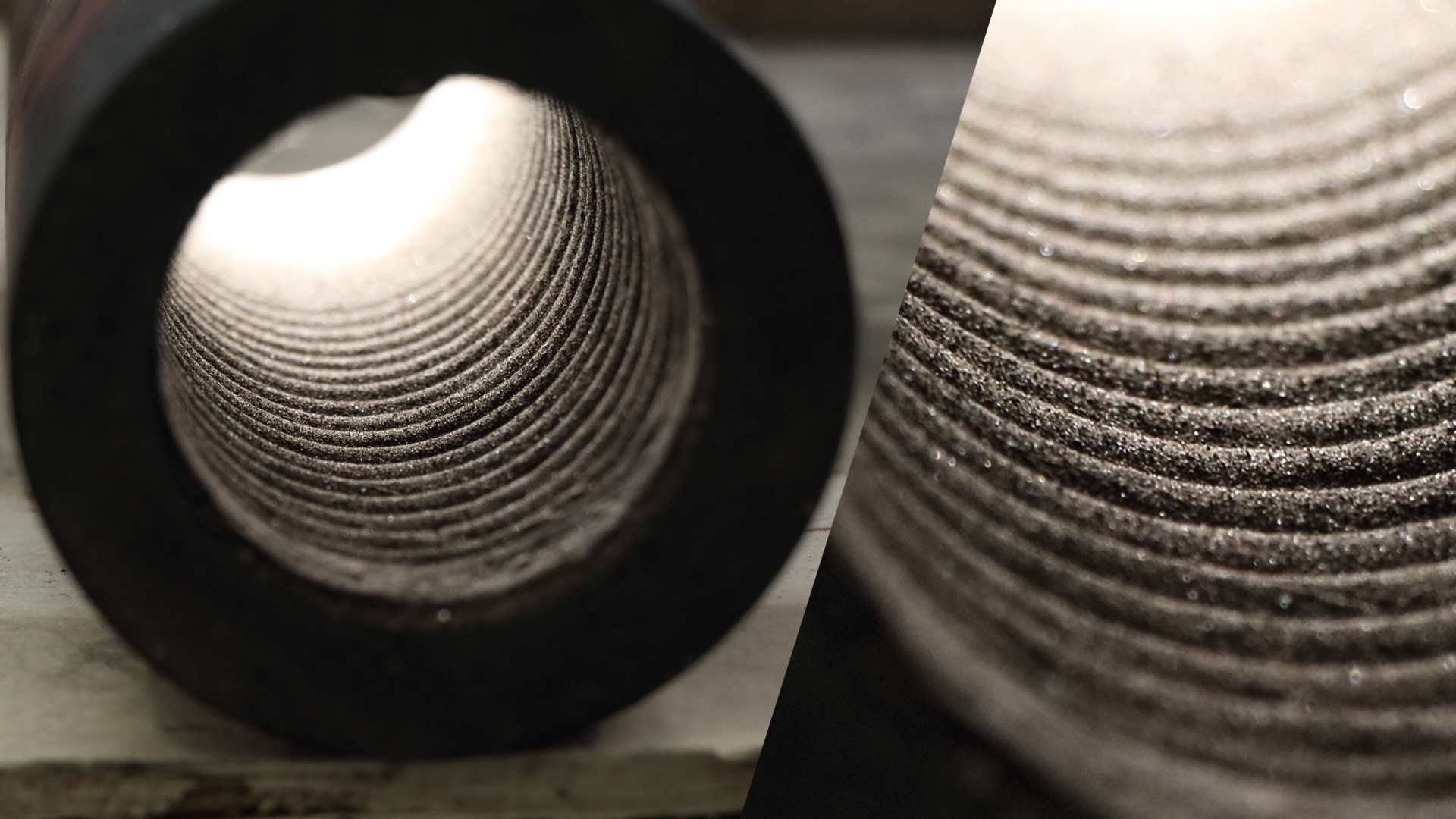
1. Restore worn or corroded bore dimensions and enhance accuracy.
2. Enhance the wear resistance, corrosion resistance and high temperature performance of the surface of the bore.
3. Improve the overall life of the bearing to meet the needs of severe working conditions.
Solution
1. Preparation
- Inspection and evaluation:
- Use CMM to detect the dimensional deviation of the bearing bore and evaluate the amount of repair.
- Analyze the working environment and determine the performance of the bore to be enhanced (e.g. wear resistance, corrosion resistance, etc.).
- Surface pre-treatment:
- Clean the bearing bore to remove oil, oxidized layer and corrosion on the surface.
- Use sandblasting or machining to increase the surface roughness of the bore (Ra 6.3-12.5 μm) and improve coating adhesion.
2. Selection of fusion material
According to the working conditions of the bearings (such as load, speed, temperature) to choose the appropriate cladding material:
- Nickel-based alloy powder:
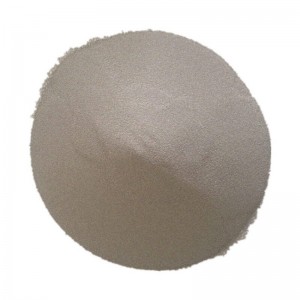
- Applicable scene: high temperature, high corrosion environment.
- Characteristics: wear-resistant, corrosion-resistant, hardness up to 50-60 HRC.
- Cobalt-based alloy powder (e.g. Stellite series):

- Scenario: high temperature, high load environment.
- Characteristics: high temperature oxidation resistance, good impact resistance, hardness up to 40-60 HRC.
- Iron-based alloy powder:
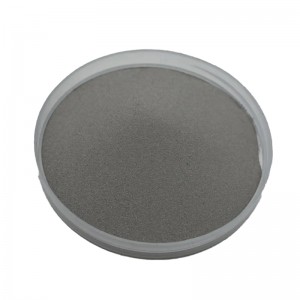
- Application Scenario: General industrial equipment, economic choice.
- Characteristics: moderate wear resistance, low cost.
3. Plasma cladding process
- Equipment selection:
- Adopt high precision CNC plasma cladding equipment to ensure the uniformity of the cladding layer.
- Equipped with a small nozzle for internal hole cladding, suitable for workpieces with limited bearing internal diameters.
- Process parameters:
- Melting current: 80-120 A (adjusted according to the material).
- Melting speed: 10-50 mm/min.
- Gas flow: 15-20 L/min (protective gas: argon).
- Melting thickness: 0.5-2.0 mm, repair a larger amount of layered melting.
- Interlayer temperature control: not more than 150 ° C, to avoid heat accumulation leading to deformation of the substrate.
- Melting process:
1. Adjust the center of the inner hole to align with the melting nozzle to ensure the uniformity of the melting.
2. bottoming layer, forming a uniform metallurgical bonding layer.
3. according to the design of the thickness of layered cladding, each layer is completed for natural cooling or auxiliary cooling.
4. Subsequent treatment
- Machining treatment:
- After the cladding is completed, the bore is machined to the designed size by internal grinding or precision turning to ensure that the dimensional tolerance and surface roughness meet the requirements (e.g. Ra≤0.4 μm).
- Heat treatment (optional):
- Stress relief heat treatment of the fused cladding layer to prevent cracks caused by residual stress.
- Cladding inspection:
- Hardness test: The hardness of the coating surface should meet the design requirements (e.g. 50-60 HRC).
- Non-destructive testing: Ultrasonic or magnetic particle testing of the coating for cracks or pores.
- Bonding strength test: The bonding strength between the coating and the base material should meet the requirements (generally ≥30 MPa).
Advantages of plasma cladding TC bearings
1. Cost-effectiveness: Compared with replacing the bearings with new ones, plasma cladding repair is less expensive and saves material costs.
2. Performance improvement: the performance of the coated material is better than that of the original material, which prolongs the service life.
3. Flexibility of process: different coating materials can be selected according to the actual working conditions of the bearings.
4. Reusable: bearings can be repaired many times after damage.
What do we need to pay attention to TC bearing cladding?
1. Heat input control:
Avoid overheating of the base material during the cladding process, which may lead to deformation or performance degradation of the bearing.
2. Dimensional tolerance:
After cladding, the bore should be precision machined to within tolerance (e.g. H7 or H6 level).
3. Adaptation to the operating environment:
Optimize the cladding material and process parameters according to the operating conditions of the bearing (e.g. temperature, medium).
Application areas for plasma cladding of TC bearings
• Mining machinery: bearing bores need to be repaired due to heavy load wear.
• Automotive industry: repairing the bore of high-precision bearings to improve durability.
• Construction machinery: enhancement of wear resistance and corrosion resistance of bearings in hydraulic systems.
• General industrial equipment: extend the service life of general-purpose bearings.
Post time: Dec-24-2024