The choice between plasma cladding and thermal spraying is a difficult one. Plasma cladding and thermal spraying are two widely used surface enhancement technologies, but their individual characteristics make them suitable for different application scenarios. In this article, we'll provide you with complete details on each process so you can better understand what they are, their drawbacks, and their advantages.
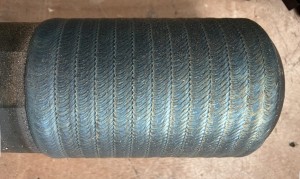
Understanding cladding and spraying
• Cladding
Cladding is a process whereby an additive material is heated to a molten state and then deposited on the surface of a substrate to form a protective or restorative layer. The process usually requires high temperatures to form a good bond between the additive material and the surface of the substrate.
• Spraying
Spraying is the process of applying a cladding material (liquid or solid) in the form of a spray to the surface of a substrate to form a cladding to provide protection, decoration or functional improvement.
Plasma cladding or thermal spraying: which is better for you?
The best way to compare plasma cladding and thermal spraying is to look at what they can both do!
Advantages of plasma cladding
Plasma cladding is a high-temperature, high-energy processing technology in which powdered material is melted and deposited onto the surface of a workpiece at high speeds by means of a plasma arc. Its advantages include:
• High bonding strength: The high bonding strength of the cladding layer to the substrate significantly improves the wear and corrosion resistance of the surface.
• Precise control: The thickness and shape of the cladding layer can be precisely controlled by adjusting the process parameters, making it suitable for workpieces with complex geometries.
• Applicable to a wide range of materials: plasma cladding can be used on a wide range of materials, including metals, ceramics, alloys, etc., to meet different industrial needs.
This technology is particularly suitable for applications that require a high degree of wear, heat or corrosion resistance, such as aerospace, oil and gas, offshore and high-temperature and high-pressure equipment.
Disadvantages of plasma cladding
Although plasma cladding has many advantages, it also has some disadvantages and limitations:
• High equipment cost: initial investment and maintenance costs are high.
• Complexity of the process: precise control of parameters and highly skilled operation are required.
• Material limitations: not all materials are suitable for cladding, especially some high melting point materials.
l Heat-affected zone: there is still some thermal influence on the substrate, which may lead to deformation.
• Thickness limitation: suitable for medium thickness claddings, too thick may cause problems.
Advantages of Thermal Spraying
Thermal spraying is another method of surface treatment in which a protective layer is formed by heating a material and spraying it onto the surface of a workpiece. The main advantages of thermal spraying are:
• High efficiency: Thermal spraying is fast to process, making it suitable for large areas and high throughput production needs.
• Cost-effective: Compared to plasma cladding, thermal spraying equipment and materials are relatively inexpensive, making it more suitable for projects with limited budgets.
• Versatility: Thermal spraying is suitable for a wide range of processes, such as flame spraying, plasma spraying and arc spraying.Visit news website for more technology news.
Thermal spraying is widely used where abrasion and corrosion resistance or repair of workpiece surfaces is required, such as in the paper, textile, metallurgical and automotive industries.
Disadvantages of Thermal Spraying
Disadvantages of thermal spraying include:
• High equipment costs: initial equipment investment and maintenance costs are high.
• Operational complexity: skilled operators are required and process parameter control is demanding.
• Cladding porosity: claddings may have tiny pores that affect their densification and corrosion resistance.
• Adhesion limitations: In some cases, the adhesion of the cladding to the substrate may not be as good as other processes such as fusion cladding.
• Material waste: material utilization during the spraying process is low and some material may be wasted.
These disadvantages may limit the widespread use of thermal spraying in some applications.
How do I choose?
The choice between plasma cladding and thermal spraying depends on your specific needs. If your application requires a high degree of precision and bonding strength, and you have the budget for it, plasma cladding is the better choice. If your project requires fast processing, cost control, and relatively loose surface requirements, then thermal spraying is definitely the more cost-effective solution.
Summarize
Regardless of which technology you choose, understanding its features and benefits will help you make a more informed decision and maximize your return on investment. Our team of experts is ready to provide you with expert advice to ensure that you choose the surface treatment technology that best suits your needs.
Contact Us
For more information or technical support, please feel free to contact our team. We are committed to providing you with the best possible surface preparation solutions.
Post time: Sep-04-2024