Valve cores working in high temperature, high pressure and corrosive environments for a long time often face wear, corrosion and fatigue problems, which puts forward very high technical requirements for manufacturing and maintenance. The introduction of plasma cladding technology provides a new solution to optimize the performance of valve cores.
What is the role of the valve core?
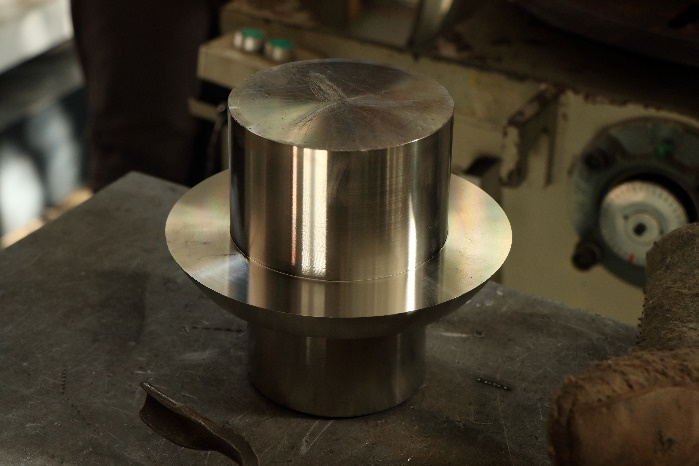
The valve core is the core component of an industrial valve that controls the direction, speed and pressure of fluid flow. It is located inside the valve and controls the passage of fluid by adjusting its position or shape.
Technical principle and advantages of plasma cladding
Plasma cladding is a surface strengthening technology that utilizes plasma arc as a heat source to rapidly melt and spray metal or ceramic powder onto the surface of the substrate to form a coating with high densification and high adhesion. Its coating has the following characteristics:
• High hardness and abrasion resistance: the hardness of the coating can reach HRC60 or above, which greatly enhances the abrasion resistance of the spool surface.
• Corrosion resistance: By choosing the right coating material (e.g. nickel-based, cobalt-based alloys or ceramic powders), the spool's corrosion resistance in strong acid, alkali and high salt environments is significantly improved.
• Strong bonding: The plasma fusion coating is metallurgically bonded to the substrate, avoiding the risk of coating flaking or crack extension.
Areas of application for valve cores
As a key determinant of valve performance, spools are used in a wide range of applications including
• Petroleum
• Chemical
• Power
• metallurgy
• ocean engineering and other fields.
Plasma welding valve core need to pay attention to 6 matters
1. Material selection
- Make sure the base material is compatible with the coating material, commonly used nickel-based, cobalt-based or ceramic powder coating.
2. Process parameters
- Control the melting temperature, powder feeding rate and scanning speed to avoid over-melting or insufficient bonding of the coating.
3. Surface treatment
- The substrate should be cleaned, degreased and preheated to ensure the adhesion of the coating.
4. Thickness of fusion coating
- According to the working conditions to determine the thickness of the coating, to avoid excessive thickness leading to cracks or deformation.
5. Quality Inspection
- Check the hardness, bonding strength and uniformity of the coating to prevent porosity or flaking problems.
6. Environment and safety
- Ensure that the environment is pollution-free, and pay attention to the safety protection of high temperature and plasma arc during operation.
Post time: Dec-20-2024