In the paper industry, the reliability and durability of production equipment directly affects the productivity and operating costs of an organization. As one of the core components in paper machinery, the screw plays a vital role in the pulp transfer and mixing process. However, spirals are often exposed to harsh operating environments that are highly abrasive and corrosive, and face an extremely high risk of wear and tear. In order to solve this problem, surface cladding technology has been developed, which significantly improves the wear and corrosion resistance of spiral parts by providing them with a strong protective layer, thus extending the service life of the equipment.
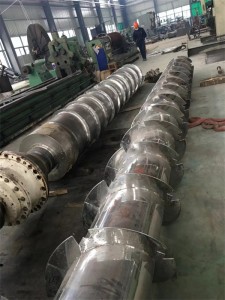
The Importance of Spiral Surfacing
In the paper production line, the spiral parts are responsible for the transmission of pulp and fiber, and at the same time, the pulp for mixing and blending. During this process, the spiral is subjected to abrasive particles in the pulp, high humidity environment and chemical erosion, resulting in rapid surface wear and corrosion. If not maintained and replaced in a timely manner, the worn spiral will not only reduce the operating efficiency of the equipment, but may also lead to production stagnation, bringing huge economic losses to the enterprise.
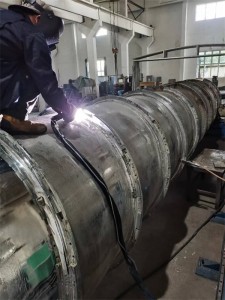
Surface cladding technology significantly improves the service life and working performance of spirals by depositing a layer of wear-resistant and corrosion-resistant alloy material on the spiral surface to form a strong protective layer. This process provides paper companies with effective equipment maintenance solutions, reducing downtime and maintenance costs due to equipment failure, thus improving overall production efficiency.
Application and Advantages of Surfacing Technology
The application of spiral surface cladding technology involves a number of key aspects such as material selection, cladding process and quality control. According to the different needs of papermaking process, commonly used surfacing materials include high chromium alloy, nickel-based alloy and tungsten carbide. These materials not only have excellent wear resistance and corrosion resistance, but also can maintain stable performance under high temperature and high pressure conditions.

● Enhancement of wear resistance: Wear in the papermaking process mainly comes from abrasive particles in the pulp and friction under high-speed rotation. By surfacing high hardness materials, the wear resistance of the spiral surface is greatly improved, which can effectively resist the erosion of abrasive particles and maintain the working efficiency of the spiral.
● Enhanced corrosion resistance: chemicals used in the paper making process, such as bleach, acidic solutions, etc., have a strong corrosive effect on the spiral surface. The high corrosion resistance of the cladding material enables the spiral to operate stably for a long time in the corrosive medium, and reduces the material failure and equipment downtime caused by corrosion.
● Extend the service life: the cladding process extends the service life of the spiral by covering the alloy material evenly on the surface of the spiral, forming a dense protective layer. This not only reduces the need for frequent equipment replacement, but also significantly lowers the operating costs of the organization.
● Repair and remanufacturing: Surfacing technology is also applicable to worn spiral parts. Through the cladding process, the worn parts of the spiral surface can be repaired and restored to their original dimensions and performance, extending the service life of the equipment and avoiding the high cost of replacing them with new parts.
Surfacing technology process and quality control
Spiral surface cladding is a complex process involving multiple steps, including surface pretreatment, cladding material selection, cladding process control and subsequent treatment. Strict control of each step is crucial to ensure the quality and stability of the surfacing layer.
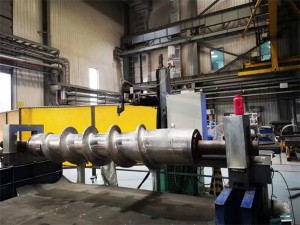
● Surface pretreatment: Before cladding, pretreatment of the spiral surface is a key step. First, the spiral surface needs to be cleaned to remove oxidized layers, oils and other impurities to ensure that the cladding material will bond firmly to the base material. Common pretreatment methods include sandblasting, grinding and chemical cleaning.
● Overlay material selection: According to the specific application requirements of the spiral in the paper making process, it is crucial to select the appropriate overlay material. Different alloys have different hardness, abrasion resistance and corrosion resistance, so it is necessary to choose the right material according to the working environment and load of the spiral, such as high-chromium alloy is suitable for high abrasion environment, nickel-based alloy is suitable for high temperature and corrosive environments, and tungsten carbide is suitable for extreme wear resistance requirements.
● Surfacing process control: Temperature control, welding speed, material filler and other parameters in the surfacing process directly affect the quality of the surfacing layer. Modern cladding equipment is usually equipped with automated control systems, which can precisely adjust these parameters to ensure the uniformity and denseness of the cladding layer, and to avoid defects such as porosity and cracks.
● Subsequent treatment: After the surfacing is completed, it is usually necessary to carry out subsequent treatment processes, such as surface grinding and heat treatment, in order to eliminate stress and improve the adhesion and hardness of the surfacing layer. The grinding process can make the spiral surface reach the required smoothness, thus reducing the friction resistance in operation. Heat treatment can improve the organizational structure of the cladding layer and enhance its comprehensive performance.
● Quality inspection: The spiral after cladding needs to go through strict quality inspection, including non-destructive testing, micro-hardness testing, coating thickness measurement, etc., to ensure that the uniformity, denseness and performance index of the cladding layer meet the design requirements. These testing methods can effectively detect possible defects in the cladding process and ensure the stable and reliable quality of each spiral component.
Industry Development and Future Trends
With the rapid development of material science, welding technology and automated equipment, spiral surface overlay welding technology is also advancing. In today's highly competitive paper industry, companies have higher and higher requirements for equipment performance and life, prompting the development of surfacing technology in the direction of greater efficiency and precision.
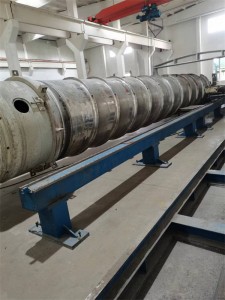
● Application of new materials: In the future, with the progress of material science, more new cladding materials will be developed and applied, such as nanocomposites and ceramic matrix composites. These materials can not only provide higher wear resistance and corrosion resistance, but also maintain stable performance under extreme working conditions to meet the higher requirements of the production environment.
● Automation and Intelligent Development: With the development of Industry 4.0, cladding technology is gradually realizing automation and intelligence. Modern cladding equipment is equipped with advanced automation control systems, which can realize real-time monitoring and adjustment of the cladding process, thus improving production efficiency and quality stability. In the future, the introduction of artificial intelligence and machine learning technology will further optimize the surfacing process parameters and improve production flexibility and precision.
● Green manufacturing and sustainable development: In the context of increasingly stringent environmental protection requirements, cladding technology is also developing in the direction of green manufacturing. The application of environmentally friendly surfacing materials and low-energy processes not only reduces energy consumption and pollution in the surfacing process, but also promotes the sustainable development of the paper industry. In the future, more environmentally friendly technologies and materials will be introduced into the surfacing process, helping the industry's green transformation.
● Repair technology innovation: With the prolongation of the equipment life cycle, the demand for repair of spiral parts will gradually increase. Future cladding repair technology will pay more attention to efficiency and quality, through more advanced technology and equipment, can quickly and accurately restore the performance of the spiral, reduce equipment maintenance costs.
Post time: Aug-24-2024