Laser cladding principle and introduction
Cladding process: Laser cladding can be roughly divided into two categories according to the supply method of cladding materials, namely preset laser cladding and synchronous laser cladding.
Pre-set laser cladding is to place the cladding material on the cladding part of the substrate surface in advance, and then use laser beam irradiation to scan and melt. The cladding material is added in the form of powder or wire, and the form of powder is the most commonly used.
Synchronous laser cladding is to send powder or wire cladding materials into the molten pool synchronously through the nozzle during the cladding process. The cladding material is added in the form of powder or wire, among which the form of powder is the most commonly used.
The main process of preset laser cladding is: substrate cladding surface pretreatment---preset cladding material---preheating---laser cladding---post heat treatment.
The main process flow of synchronous laser cladding is: substrate cladding surface pretreatment---preheating---synchronous laser cladding---post heat treatment.
According to the process flow, the processes related to laser cladding are mainly the substrate surface pretreatment method, the cladding material feeding method, preheating and post heat treatment.
Laser working principle:
The complete set of laser cladding equipment consists of: laser, cooling unit, powder feeding mechanism, processing table, etc.
Selection of lasers: mainstream laser types support laser cladding process, such as CO2 lasers, solid-state lasers, fiber lasers, semiconductor lasers, etc.
Process parameters
The process parameters of laser cladding mainly include laser power, spot diameter, cladding speed, defocus amount, powder feeding speed, scanning speed, preheating temperature, etc. These parameters have a great influence on the dilution rate of cladding layer, cracks, surface roughness and compactness of cladding parts. The parameters also affect each other, which is a very complicated process, and reasonable control methods must be used to control these parameters within the allowable range of the laser cladding process.
Laser cladding has 3 important process parameters
laser power
The greater the laser power, the greater the amount of molten cladding metal, and the greater the probability of porosity. As the laser power increases, the depth of the cladding layer increases, the surrounding liquid metal fluctuates violently, and the dynamic solidification crystallizes, so that the number of pores is gradually reduced or even eliminated, and the cracks are also gradually reduced. When the cladding layer depth reaches the limit depth, as the power increases, the surface temperature of the substrate rises, and the deformation and cracking phenomenon intensifies. If the laser power is too small, only the surface coating melts, and the substrate does not melt. At this time, local cracking occurs on the cladding layer surface. Pilling, voids, etc., fail to achieve the purpose of surface cladding.
Spot diameter
The laser beam is generally circular. The cladding layer width mainly depends on the spot diameter of the laser beam, the spot diameter increases, and the cladding layer becomes wider. Different spot sizes will cause changes in the energy distribution on the surface of the cladding layer, and the obtained cladding layer morphology and microstructure properties are quite different. Generally speaking, the quality of the cladding layer is better when the spot size is small, and the quality of the cladding layer decreases as the spot size increases. However, the spot diameter is too small, which is not conducive to obtaining a large-area cladding layer. [3]
Cladding speed
The cladding speed V has a similar effect to the laser power P. If the cladding speed is too high, the alloy powder cannot be completely melted, and the effect of high-quality cladding is not achieved; if the cladding speed is too low, the molten pool exists for too long, the powder is over-burned, the alloy elements are lost, and the heat input of the matrix is large. will increase the amount of deformation.
Laser cladding parameters do not independently affect the macroscopic and microscopic quality of the cladding layer, but influence each other. In order to illustrate the comprehensive effect of laser power P, spot diameter D and cladding speed V, the concept of specific energy Es is proposed, namely:
Es=P/(DV)
That is, the irradiation energy per unit area, and factors such as laser power density and cladding speed can be considered together.
The reduction of specific energy is beneficial to reduce the dilution rate, and it also has a certain relationship with the cladding layer thickness. Under the condition of constant laser power, the cladding layer dilution rate decreases with the increase of spot diameter, and when the cladding speed and spot diameter are constant, the cladding layer dilution rate increases with the increase of laser beam power. In addition, as the cladding speed increases, the melting depth of the substrate decreases, and the dilution rate of the cladding layer from the substrate material decreases.
In multi-pass laser cladding, the overlap rate is the main factor affecting the surface roughness of the cladding layer. When the overlap rate increases, the surface roughness of the cladding layer decreases, but the uniformity of the overlapped part is difficult to be guaranteed. The depth of the overlapping area between the cladding tracks is different from the depth of the center of the cladding tracks, which affects the uniformity of the entire cladding layer. Moreover, the residual tensile stress of multi-pass cladding will be superimposed, which will increase the local total stress value and increase the crack sensitivity of the cladding layer. Preheating and tempering can reduce the crack tendency of the cladding layer.
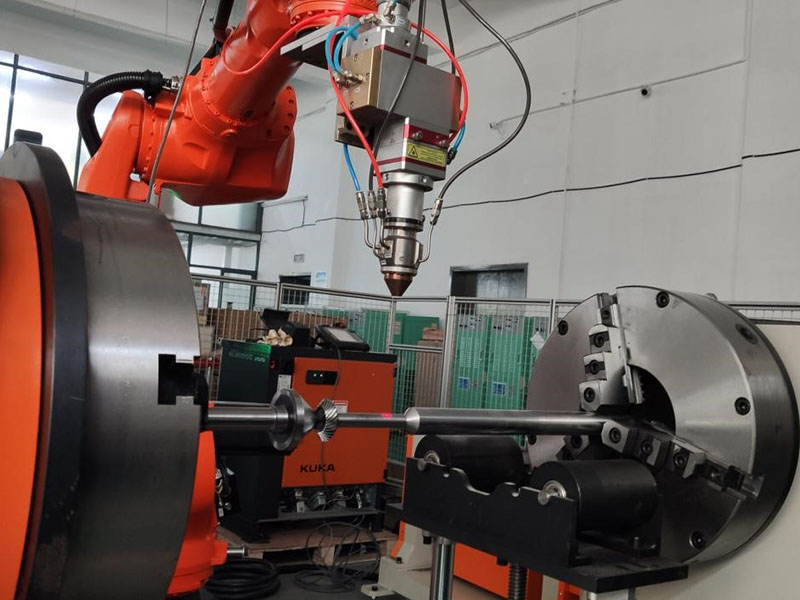
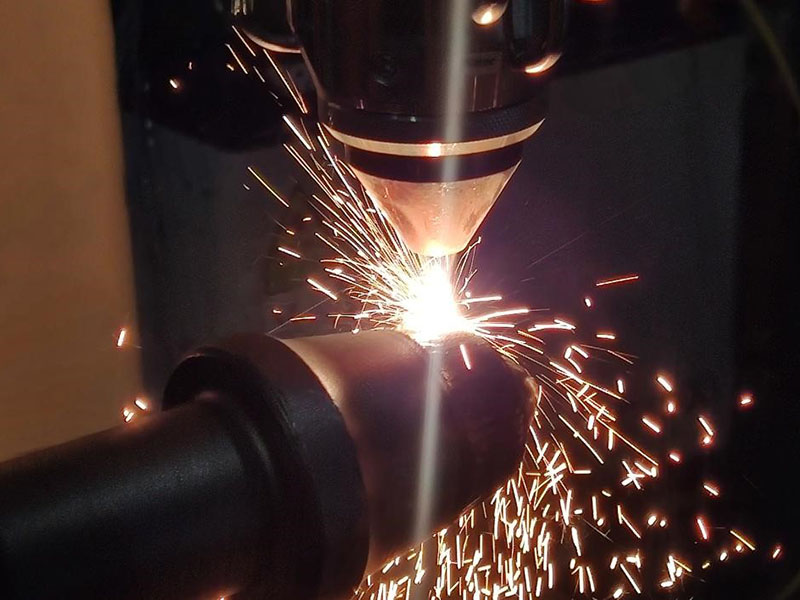
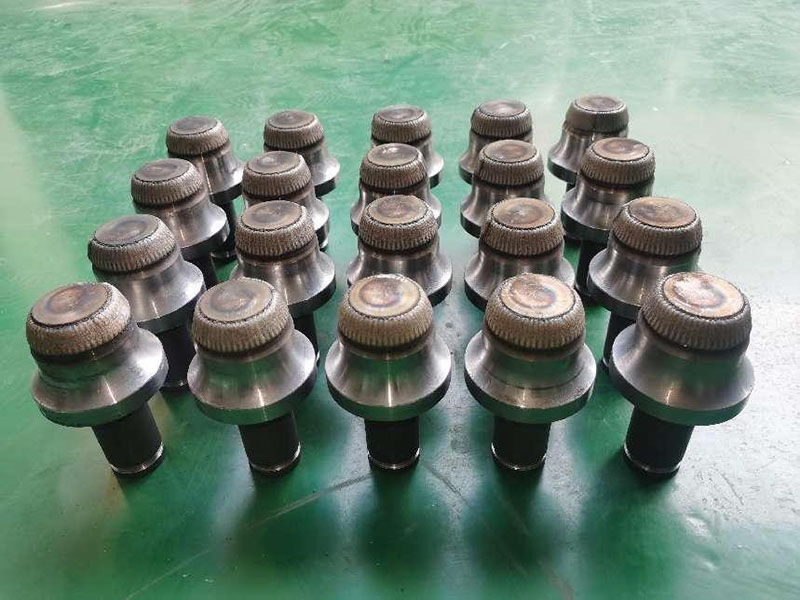
Post time: Aug-15-2023