Surface fusion cladding of glass molds is a key surface strengthening technology used to enhance the durability and performance of molds in high temperature and high abrasion environments. By coating the surface of the mold with a layer of abrasion-, corrosion-, and high-temperature-resistant material, the cladding process effectively extends the service life of the glass mold and improves the production quality of glass products.
What is a glass mold?
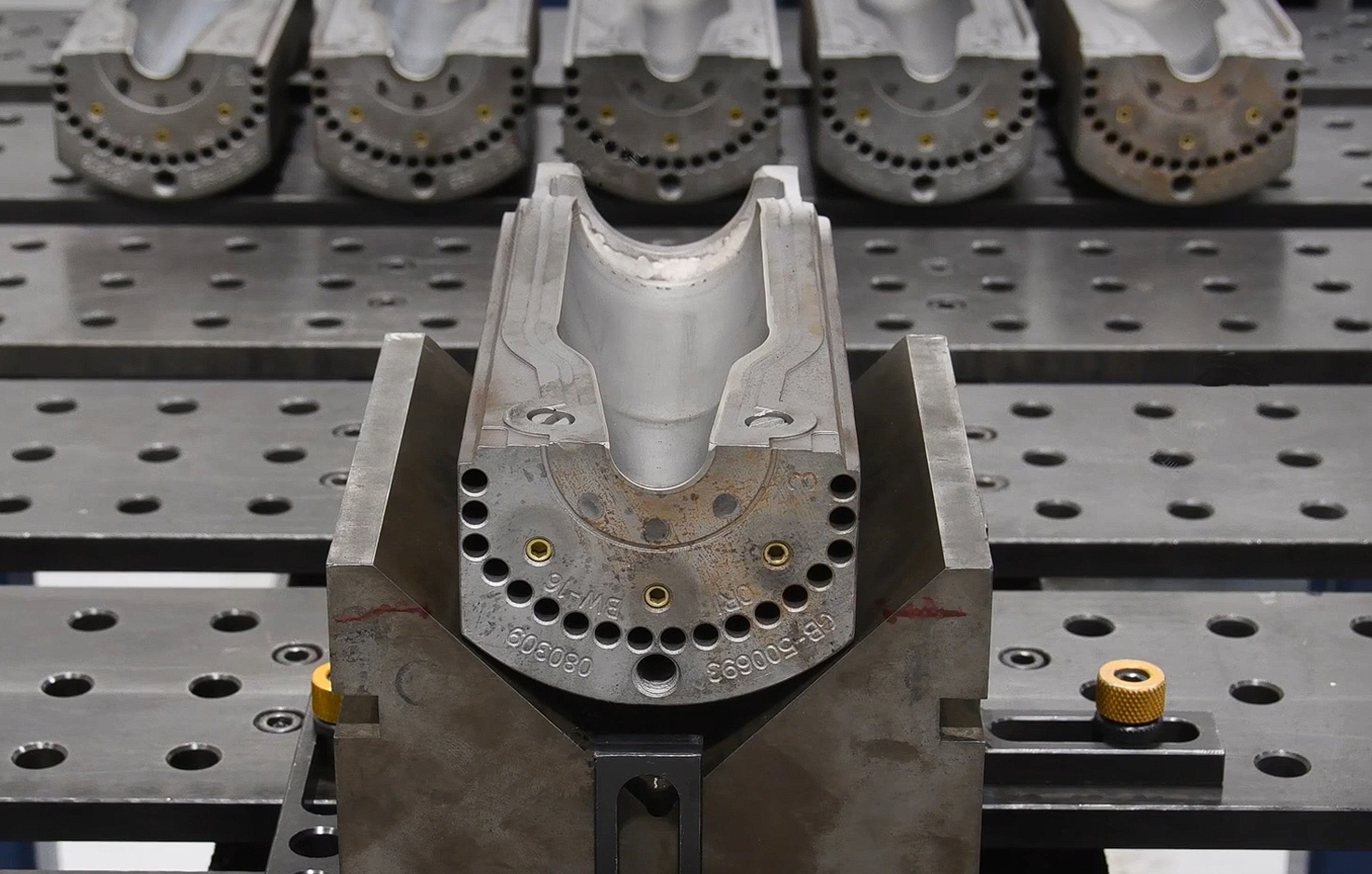
The main function of a glass mold is to form the glass after it has been melted, to cool it and to fix it into a predetermined shape.
Common glass molds
• Container glass
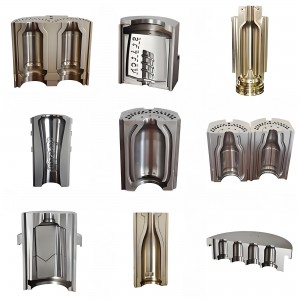
• Optical glass
• Flat glass
The main role of glass mold surface cladding
• Enhancement of wear resistance: Glass molds are subjected to a great deal of wear and tear on their surfaces when molding glass at high temperatures. Fusion coated hard wear-resistant coating can significantly improve the wear resistance of the mold surface, thus prolonging the life of the mold.
• Improvement of high temperature oxidation resistance: In the process of glass molding, the mold is exposed to high temperature for a long time, which is easy to be oxidized. Coating high temperature resistant materials, such as nickel or cobalt based alloys, can effectively reduce the oxidation loss of the mold.
• Enhance corrosion resistance: certain fusion-coated materials (such as ceramics, nickel-based alloys) have strong corrosion resistance, which can prevent corrosion and wear of molds in hot and humid environments.
• Improvement of mold surface finish: High-quality fusion cladding can increase the flatness and finish of the mold surface, resulting in a glossy and high-quality surface for glass products.
• Reduced maintenance costs: Glass molds after fusion cladding treatment are more resistant to abrasion and high temperatures, reducing the need for frequent replacement and repair, and lowering maintenance and production costs.
Commonly used materials for glass mold surface cladding
Choosing the right cladding material is important for the repair of molds to increase wear resistance and corrosion resistance commonly used materials are:
• Cobalt-based alloy
• Nickel-based alloys
• Ceramic coatings
• Metal-ceramic composite coating
Glass mold surface cladding process methods
Glass mold surface cladding mainly adopts the following methods:
1. Plasma cladding
The powder material is melted and coated on the surface of the mold by high temperature plasma arc. The cladding layer of plasma cladding has high denseness and strong bonding force, which is suitable for glass molds with complex shapes.
2. Laser cladding
Using a high-energy laser beam to instantly heat, melt and adhere to the surface of the mold, forming a dense coating with high hardness and low porosity. Laser cladding is suitable for small precision molds, but the cost is higher.
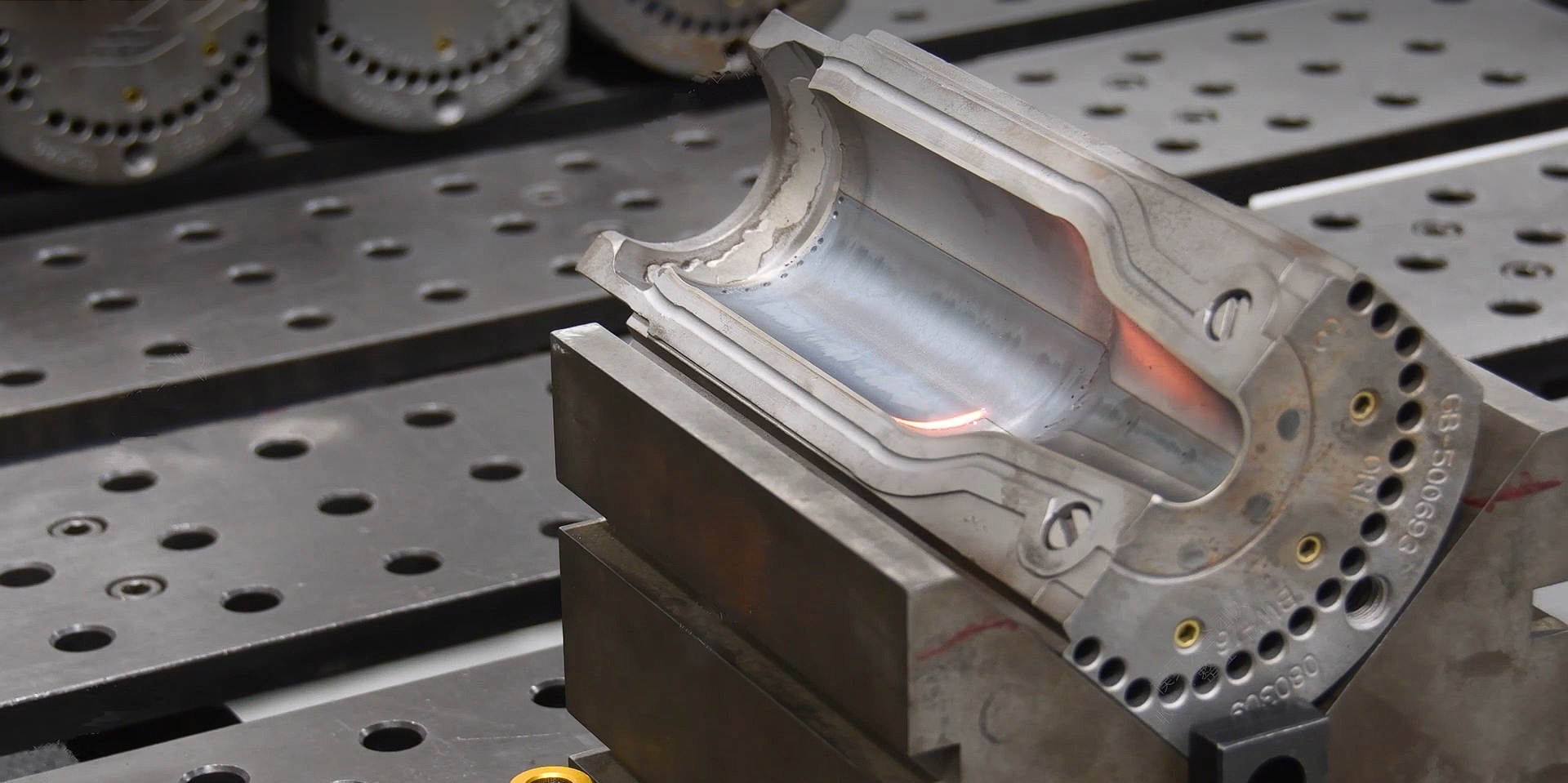
3. Hypersonic flame spraying (HVOF)
The coating material is melted and accelerated by a high-speed flame and sprayed onto the mold surface to form a dense layer with high bonding strength. It is suitable for glass molds with high abrasion resistance requirements.
The operation process of glass mold surface fusion cladding
1.Pre-treatment: The surface of the mold is cleaned to remove oil, oxide and other impurities. The surface roughness is usually increased by sandblasting to improve the adhesion of the cladding layer.
2.Preparation of cladding material: Select the appropriate cladding material according to the specific needs of the mold, such as cobalt-based, nickel-based alloy or ceramic powder.
3.Cladding operation: Fix the mold on the cladding table, select the appropriate cladding process and parameters (e.g. temperature, spraying speed, etc.), and control the thickness and uniformity of the cladding layer.
4.Cooling and post-treatment: Let the mold cool naturally after the cladding is completed to avoid cracks or deformation caused by rapid cooling. Surface grinding or polishing treatment is carried out as needed to improve the surface finish of the mold and coating precision.
5.Quality Inspection: Non-destructive testing (e.g. ultrasonic, X-ray) is used to inspect the uniformity and thickness of the coating to ensure that the quality of the fusion cladding layer meets the requirements.
The surface cladding technology of glass molds can effectively improve the wear resistance, corrosion resistance and heat resistance of the molds, and significantly reduce the maintenance cost of the molds while improving the quality of glass products. With the development of cladding technology, its application in glass molds will be more extensive, and will further enhance the service life and processing effect of glass molds.
Post time: Oct-31-2024