Fully automated laser cladding systems[1] are an advanced manufacturing technology used to form coatings on the surface of substrates that are resistant to abrasion, corrosion or other properties. The technology combines laser technology and materials science and has a wide range of applications in industry, particularly in the aerospace, automotive, energy and manufacturing industries. Below are the key features and benefits of fully automated laser cladding systems:
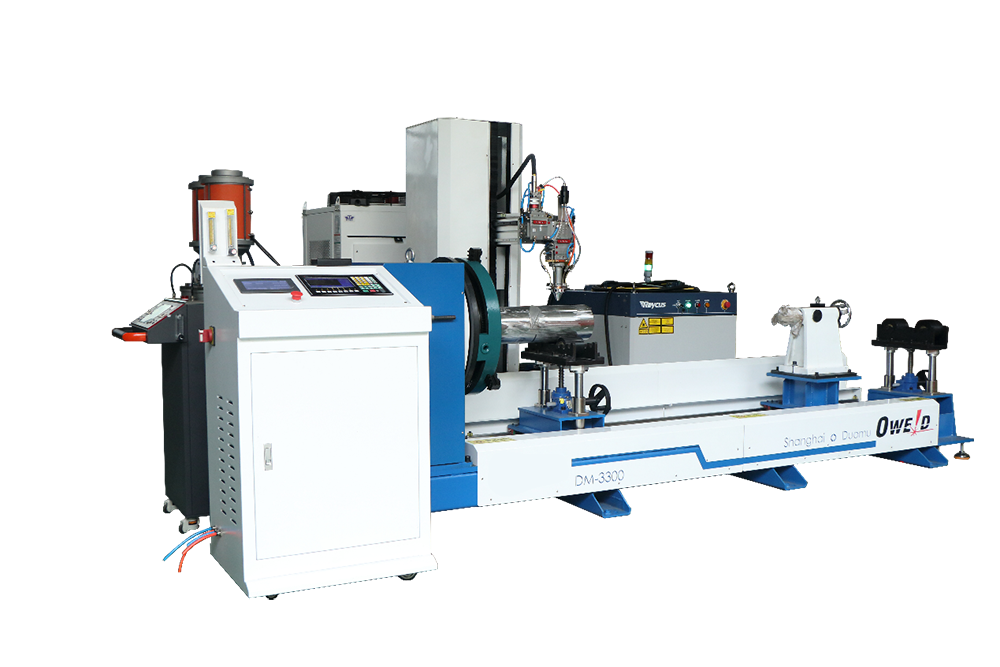
Main features
1. High-precision control: Fully-automatic laser cladding system can accurately control the laser power, scanning speed and cladding path to ensure the uniformity of coating and stable quality.
2. High degree of automation: The system integrates advanced automation technology, including numerical control (CNC)[2] system, robot arm and sensors, which can realize unattended automatic operation.
3. Multi-material compatibility: capable of handling a wide range of powder materials, such as metal alloys, ceramics and composites, to meet the needs of different applications.
Selection & Application of Welding Cladding Powders
4. Wide range of application: It can be used for repairing worn parts, manufacturing new parts and functionalizing surfaces to meet the needs of different industrial applications.
Advantages
1. Efficient production: Due to the high degree of automation and high precision of the system, production efficiency is greatly improved, reducing manual intervention and production cycle time.
2. Excellent Coating Performance: Laser cladding is able to form a coating metallurgically bonded to the substrate on the surface of the substrate, which significantly improves the hardness, abrasion resistance and corrosion resistance of the coating.
3. Material saving: Precise material control and efficient utilization reduces material waste and lowers production costs.
4. Strong Flexibility: The system can be adjusted according to different workpiece shapes and sizes, providing strong flexibility and adaptability.
5. Environmentally friendly: The laser cladding process is relatively clean and produces less pollution, which contributes to environmental protection.
Application Examples
1. Aerospace: Used for surface repair and enhancement of key components such as turbine blades, combustion chambers and landing gears.
2. Automotive industry: for surface treatment of engine parts, gearboxes and transmission systems.
3. Energy industry: for wear-resistant coatings on oil drill bits, pumps and valves.
4. Manufacturing industry: for surface functionalization of molds, tools and machine parts.
Conclusion
Fully-automatic laser cladding system is an important technical means in modern manufacturing industry and has a wide range of application prospects. Its high precision, high efficiency and multifunctionality give it significant advantages in enhancing product performance and extending service life.
If you have specific needs or questions, please feel free to explain in detail and we can provide more targeted suggestions or answers.
Post time: Jul-15-2024