With the progress of industrial technology, oil, natural gas, chemical, electric power and other industries on the durability of the valve requires more and more high. Traditional valves are susceptible to wear and tear under high temperature, high pressure and corrosive media, increasing maintenance costs and downtime.
What is a valve?
A valve is a mechanical device used to control the flow of a fluid (gas, liquid, slurry, etc.). It plays a vital role in a variety of industrial and everyday applications.
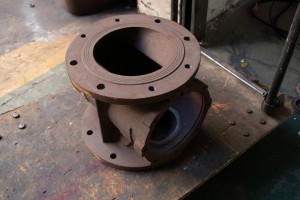
The specific features include:
• Opening and closing function: the valve can open or close the fluid channel in the pipeline, so as to control the flow of fluid or blocking.
• Adjust the flow: by adjusting the opening of the valve, you can control the flow of fluid flow through, to achieve the purpose of precise regulation.
• Prevent backflow: certain valves (such as check valves) can prevent fluid backflow in the pipeline to ensure system safety and stability.
• Pressure regulation: Valves can be used to regulate and maintain pressure in a system within a set range.
• Distributing flow: Multi-channel valves can change the direction of fluid flow, directing it to different pipes or equipment.
• Protecting equipment: When the system pressure is too high, safety valves and other valves can automatically release the pressure to protect the equipment from damage.
The core principle of valve cladding technology

Plasma cladding technology is a kind of process through the wear-resistant, corrosion-resistant alloy material fused and uniformly deposited on the surface of the valve. The alloy coating formed by this technology is not only able to effectively resist high temperature, high pressure and chemical corrosion, but also can significantly improve the wear resistance of the valve. Through this surface modification, the valve's service life in extreme operating conditions can be extended, while also reducing the frequency and cost of equipment maintenance.
Technical advantages of plasma cladding
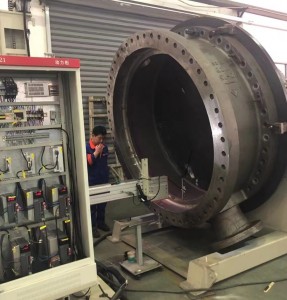
• Abrasion resistance: The fusion coating consists of a high hardness alloy material, which can effectively resist friction damage from particles and fluid media, ensuring that the valve is in the best working condition for a long time.
• Corrosion resistance: when operating in corrosive fluids or gaseous media, the fused coating provides a strong barrier for the valve, reducing performance degradation due to corrosion.
• High temperature resistance: specially designed alloy materials can withstand high temperature environments and are suitable for high temperature process areas such as oil refining and chemical industry, ensuring that the valves do not deform or fail at high temperatures.
• Extended service life: By reducing wear and corrosion, the cladding technology significantly extends the service life of the valves, reduces the frequency of replacement and downtime for maintenance, and improves the overall production efficiency.
Common types of valves
Valves can be categorized into various types depending on their function, structure and application scenarios. The following are some common types of valves.
• Globe valve
• Gate Valve
• ball valve
• butterfly valve
• check valve
• safety valve
• pressure reducing valve
• control valve
• diaphragm valve
• needle valve
• plug valve
• isolation valve
• foot valve
These valves are widely used in various industries such as petroleum, natural gas, chemical, electric power, water treatment, paper making, pharmaceuticals and so on. It is vital to select the right type of valve according to the specific working condition requirements to ensure efficient operation and safety of the system.
Post time: Aug-23-2024