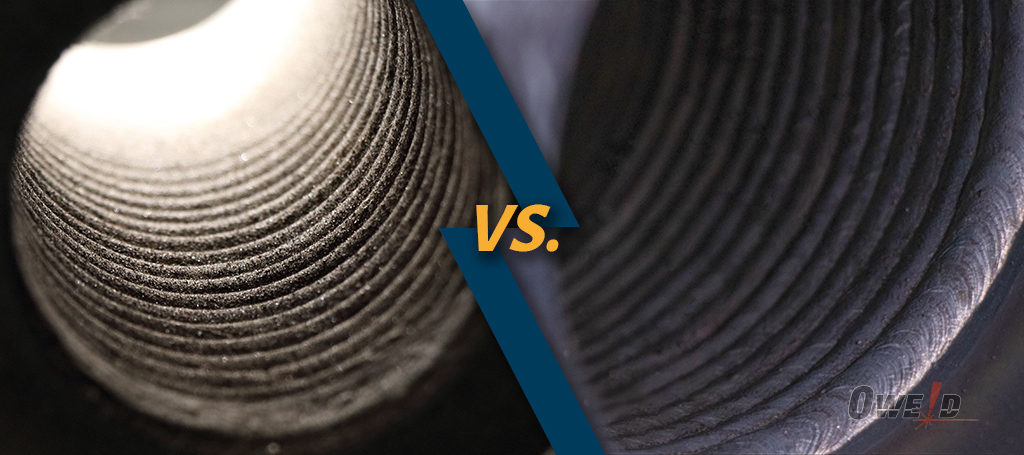
Comparison of PTA with TIG and MIG welding coverings
Welding cladding technology is an important means of enhancing the surface properties of metals, and is widely used in critical components for wear resistance, corrosion resistance and high temperature environments. Among them, PTA, TIG and MIG welding processes have become the three mainstream choices for cladding preparation due to their unique advantages.
PTA meets the needs of extreme working conditions with precise and efficient deposition capability; TIG is suitable for high-precision fields with its excellent welding quality; and MIG is favored by the industry for its high efficiency and large-area application advantages. How to choose the right process not only affects the performance of the covering layer, but also determines the production efficiency and cost.
How to choose the right process to create the ideal cover layer? In this article, we will analyze the characteristics and application scenarios of the three processes in a concise way, and bring you to find the best solution easily.
PTA (Plasma Arc Welding), TIG (Tungsten Inert Gas Welding) and MIG (Melting Inert Gas Welding) are three commonly used welding processes. They are compared below in the application of welded coverings:
I. Welding principle
1. PTA (Plasma Transferred Arc Welding)
- Using a high temperature plasma arc as a heat source, the molten metal can be deposited precisely on the base material.
- It is suitable for the preparation of high hardness, wear-resistant and corrosion-resistant cover layer.
2. TIG (Tungsten Inert Gas Welding)
- The electrode is tungsten-pole based and an inert gas (e.g. argon) is used to protect the molten pool.
- Usually requires manual addition of filler metal, low heat input and high weld quality.
3. MIG (Metal Inert Gas Welding)
- The use of molten metal wire as the electrode, automatic wire feeding, protective gas is mainly inert gas or mixed gas.
- Higher melting efficiency, suitable for large-area cover layer welding.
II. Main features
Characteristics | PTA | TIG | MIG |
Heat source temperature | Very high (>16.000°C) | High | Medium |
Melting efficiency | Medium | Low | High |
Process control accuracy
(suitable for large-area applications) |
High (allows precise control) | Very high (suitable for fine welding) | Low |
Welding speed | Medium | Low | High |
Material compatibility | Wide range | Wide range | Rather Wide range |
Weld quality (spatter prone) | Very high (good metallurgical bond | Very high (flat surface, no porosity) | High |
Heat-affected zone | Small | Very small | Large |
Difficulty of operation | High (requires specialized equipment) | Higher | Lower |
III. Comparison of the performance of welded coverings
1. Hardness and wear resistance
- PTA: Due to the high temperature concentration, the fusion cladding layer has good metallurgical bonding with the base material, and has the best hardness and wear resistance.
- TIG: second best, suitable for scenarios requiring high quality but lower hardness requirements.
- MIG: Due to the high heat input, the hardness of the overlay layer may be slightly lower, and the wear resistance is moderate.
2. Corrosion resistance
- PTA: Extremely high corrosion resistance can be achieved by precise control of the alloy composition.
- TIG: better corrosion resistance, but low melting efficiency, covering layer thickness may be insufficient.
- MIG: general corrosion resistance, but suitable for thicker cover layer preparation.
3. Bonding strength
- PTA: the highest bonding strength, suitable for high strength working conditions.
- TIG: The bonding strength is a little inferior, but the surface finish is high.
- MIG: relatively low bonding strength, easy to produce pores or inclusions.
4. Uniformity of cover layer
- PTA: Very high uniformity, suitable for demanding surfaces.
- TIG: Second best uniformity, but manual operation may lead to poor consistency.
- MIG: The covering layer is thicker and the uniformity may not be as good as the other two methods.
IV. Scope of application
1. PTA
- Used to prepare functional coverings with high hardness, wear and corrosion resistance.
- Typical applications: aerospace, nuclear industry, mold surface strengthening.
2. TIG
- Used for high quality requirements of small parts or precision parts of the cover layer.
- Typical applications: food industry equipment, stainless steel pipe repair, etc.
3. MIG
- Used to cover a large area, high productivity occasions.
- Typical applications: repair of large structural parts, wear-resistant layer surfacing, etc.
V. Summary
Characteristics | PTA | TIG | MIG |
vantage | High precision, high hardness, high wear resistance | High surface finish. Flexible operation | High efficiency, large area applications |
disadvantages | Complex and costly equipment | Inefficient and time-consuming cladding | Poor homogeneity and large heat affected areas |
Applicable Scenarios | High-end cladding equipment | High quality restorations and overlays | Fast cladding and repair |
Depending on the specific needs of the working conditions, a suitable welding process can be selected to meet the balance between productivity and performance requirements.
Post time: Dec-12-2024