Plasma cladding technology is becoming a key means of surface enhancement in modern industry and manufacturing technology. By utilizing a high temperature plasma arc, the cladding material is melted and deposited on the surface of the substrate to form a dense, high strength coating. Plasma cladding materials are widely used in aerospace, energy, automotive and other fields due to their excellent performance. In this article, we will discuss the classification of plasma cladding materials and their applications in different fields.
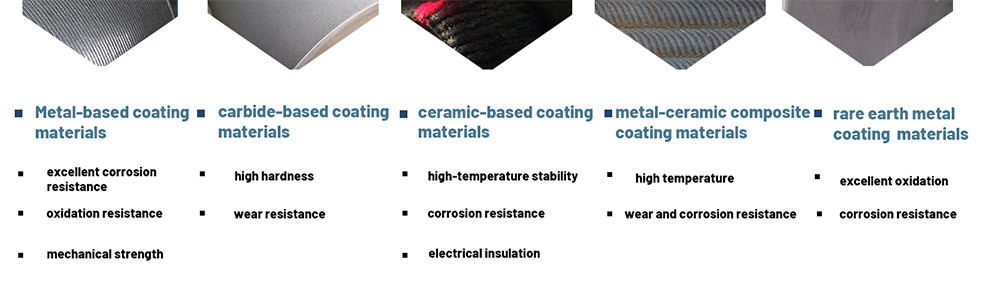
Classification of plasma cladding materials
1. Metal-based coating materials
- Representative materials: nickel-based alloys,[1] cobalt-based alloys[2], [4]stainless steel
- Application areas: turbine engine parts, oil drilling tools, industrial valves
- Advantage: Metal-based coating materials have excellent corrosion resistance, oxidation resistance and mechanical strength, suitable for high temperature, high pressure and corrosive environment.[10]
2. carbide-based coating materials
- Representative materials: tungsten carbide (WC)[3], chromium carbide (Cr3C2)[5]
- Application areas: machinery parts, mining equipment, molds and dies
- Advantage: Carbide-based coating materials are known for their extremely high hardness and wear resistance, which can significantly extend the service life of equipment and parts.[ What is a plasma welding machine?]
3 ceramic-based coating materials
- Representative materials: aluminum oxide (Al2O3)[7], titanium oxide (TiO2)[6], zirconium oxide (ZrO2)[9]
- Application areas: high-temperature insulation components, aircraft engines, semiconductor manufacturing equipment
- Advantage: Ceramic-based coating materials have high-temperature stability, corrosion resistance and electrical insulation, ideal for high-temperature environments and insulation requirements.
4. metal-ceramic composite coating materials
- Representative materials: nickel-based alloy[11] - tungsten carbide composite materials, cobalt-based alloy[8] - chromium carbide composite materials
- Application areas: aerospace, energy equipment, automotive manufacturing
- Advantages: composite coating materials combine the advantages of metals and ceramics, with excellent resistance to high temperature, wear and corrosion resistance, can provide excellent protection in complex working conditions.
5. rare earth metal coating materials
- Representative materials: yttrium, lanthanum, cerium-based alloys
- Application areas: gas turbines, nuclear industry, high-temperature alloy components
- Advantages: rare earth metal coating materials have excellent oxidation and corrosion resistance in high temperature environments, significantly improving the stability and service life of the coating.
Application examples
1. aerospace field: nickel-based alloy and tungsten carbide composite coatings are widely used on aero-engine turbine blades and gas turbine components to improve their wear resistance and high temperature resistance.
2. energy field: cobalt-based alloy coatings are used in oil drilling tools and pipelines to enhance their corrosion and wear resistance and extend the service life of the equipment
3. Automotive: Chromium carbide coatings are used on engine piston rings and valve seat rings to improve wear resistance and fuel efficiency.
Future Prospects
With the continuous progress of material science and process technology, the performance of plasma clad coating materials will be further improved. For example, nanostructured coating materials can provide higher hardness and toughness while exhibiting superior performance in specific applications. In addition, the combination of intelligent manufacturing and automation technologies makes the plasma cladding process more precise and efficient, further promoting the application of this technology in various fields.
Conclusion
As an advanced surface treatment technology, plasma cladding coating materials play an important role in modern industry. By understanding and categorizing these coating materials in depth, we are able to better select materials suitable for specific applications and enhance product performance and reliability. In the future, with the continuous development of new materials and processes, plasma cladding coating technology will continue to show its unique advantages and broad application prospects in various industries.[12]
Post time: Jul-12-2024