Bore cladding is a process that utilizes a high-energy heat source (e.g., laser, plasma, e-beam, etc.) to melt the cladding material and deposit it on the surface of the bore of the substrate. Through this technology, the hardness, wear resistance and corrosion resistance of the bore surface can be significantly improved, thus extending the service life of the equipment.
Frequently Asked Questions about Bore Cladding
Although bore cladding technology is excellent for improving equipment performance and extending service life, there are still some technical challenges and problems encountered during practical application. The following are some of the common problems and their corresponding solutions for internal hole cladding:
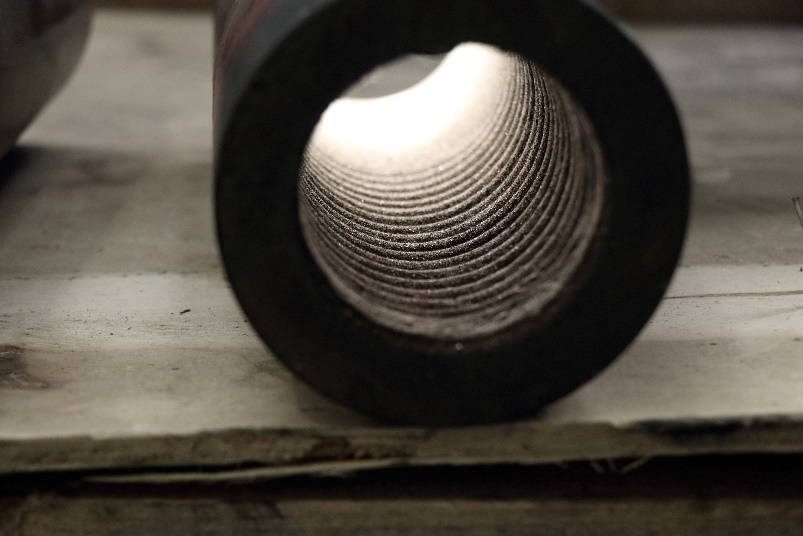
1. poor uniformity of the cladding layer
Problem Description: During the process of bore melting and cladding, improper equipment or operation may lead to non-uniformity of the thickness of the cladding layer, thus affecting the performance and service life of the bore.
Solution:
- Equipment Calibration: Calibrate the cladding equipment regularly to ensure stable energy output from the laser, plasma arc or electric arc.
- Optimization of process parameters: Adjust the welding speed, welding material feeding speed, laser or arc power and other parameters to ensure a uniform welding layer.
- Multi-layer cladding: Adopt multi-layer cladding process, correct the thickness layer by layer to ensure the uniformity of the final cladding layer.
2. Insufficient bonding between the cladding layer and the base material
Problem description: If the bonding between the cladding layer and the substrate is not strong, it may cause the cladding layer to flake off or peel off, thus affecting the usage effect.
Solution:
- Surface pre-treatment: Clean and pre-treat the surface of the substrate before fusion cladding, such as sandblasting, grinding, etc., to improve the roughness of the surface and enhance the bonding force.
- Optimize the cladding material: Select the cladding material with good compatibility with the base material to ensure a good combination between the materials.
- Control the melting temperature: Reasonably control the melting temperature to avoid too high or too low temperature affecting the bonding force.
3. The heat-affected zone is too large
Problem description: Excessive heat input during internal hole cladding may result in a heat affected zone in the substrate, causing material deterioration or deformation.
Solution:
- Control Heat Input: Reduce the heat impact on the substrate by adjusting the energy input of the laser, plasma arc or electric arc.
- Cooling system: Use appropriate cooling system, such as water cooling or air cooling, to dissipate heat in time during the melting and cladding process to reduce the temperature of the substrate.
- Selection of appropriate process: Select the melting and cladding process with smaller heat-affected zone according to the specific application, such as laser melting or cold spraying.
4. Difficulty in operation of internal hole cladding
Problem description: Internal hole cladding is difficult to operate due to space constraints, especially for deep holes or small hole diameters, making it difficult to ensure process stability and consistency.
Solution:
- Specialized cladding equipment: develop and use specialized internal hole cladding equipment, such as internal hole laser cladding head, robotic cladding system, etc., to improve the flexibility and precision of operation.
- Automatic control: adopt automatic control system to reduce manual operation error and ensure the stability of the melting and cladding process.
- Process Optimization: determine the best process parameters through testing and optimization to ensure the quality of cladding under different hole diameters and depths.
5. Improper selection of cladding materials
Problem description: The selected cladding material does not meet the requirements of the use environment, which may lead to poor performance of the cladding layer, such as insufficient abrasion resistance and corrosion resistance.
Solution:
- Material testing: Conduct material testing and evaluation before cladding, and select cladding materials that meet the requirements of the application environment.
- Material Optimization: Optimize the composition of the cladding material to improve its performance according to specific needs.
- Consultation with experts: Work with material experts or suppliers to get professional advice on material selection.
Bore cladding process
The development and application of internal hole melting and cladding technology is promising, but the above problems need to be overcome in actual operation. Through continuous technical improvement and process optimization, internal hole melting and cladding will better meet the needs of modern industry and promote the innovation and progress of manufacturing industry.
Post time: Jul-27-2024