Spiral blades are the core components of many mechanical devices, such as conveyors, extruders, concrete mixers, etc.. Since their working environment mostly involves the transfer of highly abrasive, high-impact or highly corrosive materials, the use of plasma cladding technology to strengthen and repair the surface of spiral blades can significantly improve their performance and service life.
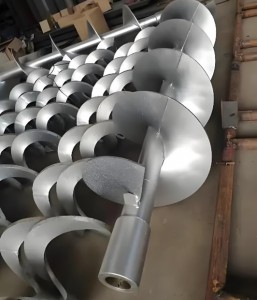
What are the cladding requirements for spiral blades?
The operating environment of spiral blades determines the main performance requirements for their fusion cladding:
• Abrasion resistance
Often in contact with granular materials (e.g. sand, ore, grain, etc.), they need to be resistant to abrasive wear.
• Corrosion resistance
In chemical or high humidity environment, need to resist medium corrosion.
• Impact resistance
In the transportation of large materials or high load work, need to have good impact toughness.
• Repairability
Plasma cladding restores dimensions and improves performance when blades are worn or deformed by long-term use.
Plasma cladding on spiral blades
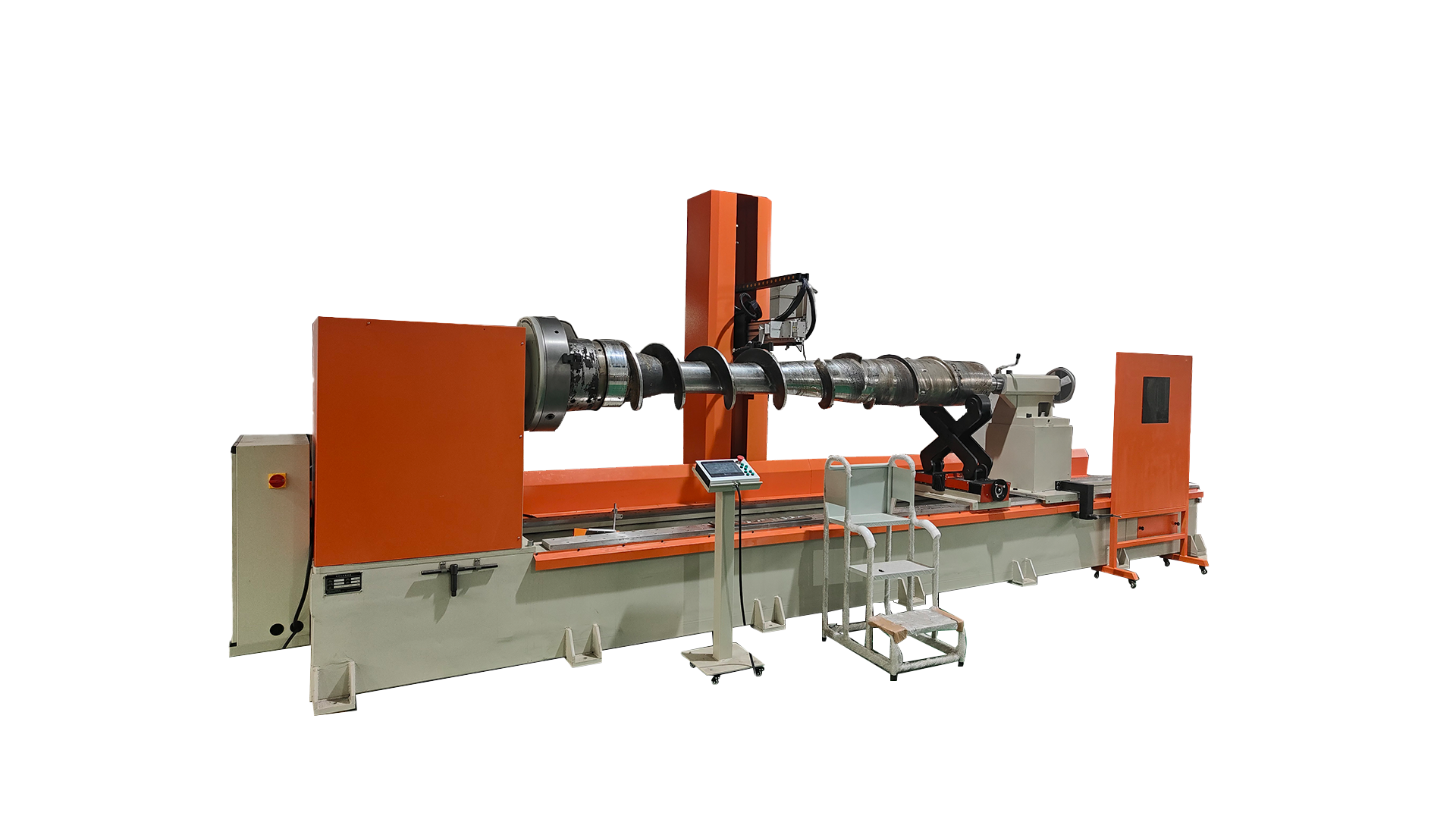
Note: Automated plasma cladding spiral equipment
1. Surface strengthening of new blades
Cladding the surface of newly manufactured spiral blades can significantly improve their working performance:
Use of wear-resistant alloy powders (e.g. cobalt-based, nickel-based or iron-based alloys).
According to the function of the blade, choose a specific thickness (usually 0.5mm~2mm) of fusion cladding layer.
2. Repair of blades
Plasma cladding of worn spiral blades restores their dimensions and performance:
The cladding layer not only fills in the wear area, but also improves its surface properties.
The life of the repaired blades can exceed the original design life.
3. Composite cladding
For complex conditions, spiral blades can be clad with multi-functional cladding technology:
Wear-resistant + corrosion-resistant cladding: to cope with wear and corrosive environments at the same time.
Partitioned cladding: selecting cladding materials with different properties according to the different stress areas of the blade.
Advantages of plasma cladding
1. High quality fused cladding
metallurgical bonding ensures that the coating will not flake off easily, is hard and resistant to wear.
2. Process flexibility
Suitable for spiral blades of all shapes and sizes, especially for complex curved surfaces.
3. Cost-effective
Coating repair is more economical and environmentally friendly than replacing the entire component.
4. Extended Life
significantly increases the working life of spiral blades and reduces downtime for maintenance.
Typical application cases of plasma cladding spiral blades
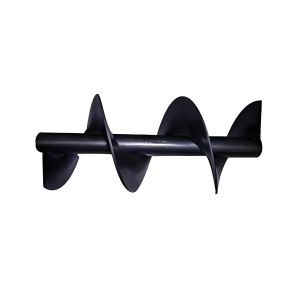
Enhanced durability by cladding with wear-resistant alloys when conveying hard or corrosive materials (e.g. coal ash, ores, salts).
• Extruder Screw Blades
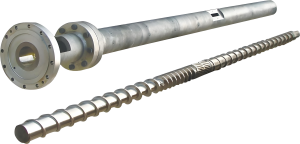
Nickel-based alloys are clad to prevent blade failure due to high temperatures and high wear environments.
• Concrete Mixer Blades
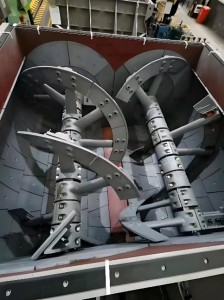
Cobalt-based alloys are clad to enhance impact and wear resistance.
Precautions for plasma cladding
1. Heat-affected zone control
Avoid deformation or performance degradation of blade substrate caused by overheating.
2. Material selection
The cladding material should have similar expansion coefficient with the base material to avoid cracking of the cladding layer.
3. Process consistency
Ensure that the thickness of the cladding layer is uniform to avoid failure caused by stress concentration.
Plasma cladding technology gives the spiral blade excellent wear resistance, corrosion resistance and impact resistance, and at the same time has the ability of high-precision repair and strengthening. Its high efficiency, economic and environmental friendly features make it an ideal choice for spiral blade manufacturing and repair.
Post time: Jan-08-2025