Laser hardening robot
Quality
Laser quenching has high power density, fast cooling speed, no need of water or oil and other cooling media, is a clean and fast quenching process. And induction hardening, and flame hardening, carburizing and quenching process, compared with laser quenching hardened layer, high hardness (generally higher than induction hardening 1-3 HRC), small deformation, heating depth and heating trajectory is easy to control, easy to realize automation, don't need like induction hardening according to different design of the corresponding component size induction coil, The processing of large parts does not need to be carburized quenching and other chemical heat treatment furnace size restrictions, so in many industrial fields are gradually replacing induction quenching and chemical heat treatment and other traditional processes. Especially important is that the deformation of the workpiece before and after laser quenching can be almost ignored, so it is especially suitable for high precision parts surface treatment.
The depth of the laser hardened layer is generally between 0.3 mm and 2.0mm, depending on the component composition, size and shape, and laser process parameters. When the tooth surface of large gear and the journal of large shaft parts are quenched, the surface roughness is basically unchanged, and it can meet the needs of actual working conditions without subsequent mechanical processing.
Laser melting quenching technology is the use of laser beam to heat the surface of the substrate above the melting temperature, due to the internal heat conduction cooling of the substrate, the surface of the melting layer is rapidly cooled and solidified. The obtained melt-quenched microstructure is very dense, and the microstructure along the depth direction is in order of melt-solidification layer, phase change hardening layer, heat affected zone and substrate. Laser melting layer has deeper hardening depth, higher hardness and better wear resistance than laser quenching layer. The disadvantage of this technique is that the roughness of the workpiece surface is damaged to a certain extent, which generally needs to be restored by subsequent machining. In order to reduce the roughness of the parts surface after laser melting treatment and reduce the amount of subsequent processing, Huazhong University of Science and Technology has prepared special laser melting quenching coating, which can greatly reduce the surface roughness of the melting layer. The surface roughness of rolls, guides and other workpieces of various materials in metallurgical industry treated by laser melting has been close to the level of laser quenching.
Applied materials
Laser quenching has been successfully applied to the surface strengthening of wearing parts in metallurgy industry, machinery industry and petrochemical industry, especially in improving the service life of wearing parts such as rolls, guides, gears and cutting edges, the effect is remarkable, and has achieved great economic and social benefits. In recent years, it has been more and more widely used in the surface strengthening of die, gear and other parts.
The practical application
Laser quenching technology can be used to strengthen the surface of various guide rails, large gears, journal, cylinder wall, mold, shock absorber, friction wheel, roller, roller parts. Suitable material for medium and high carbon steel, cast iron.
Application example of laser quenching: the moving drawing book of cast iron engine cylinder strengthened by laser quenching increases its hardness from HB230 to HB680, and its service life increases by 2~3 times.
Gear is a widely used part in machinery manufacturing industry. In order to improve the bearing capacity of gear, it is necessary to harden the surface of gear. There are two main problems in the traditional gear hardening treatment, such as surface chemical treatment such as carburizing and nitride, induction surface quenching, flame surface quenching, etc., that is, the deformation is large after heat treatment and it is not easy to obtain uniform distribution of hardened layer along the tooth profile, which affects the service life of the gear.
Characteristics
1. The quenching parts do not deform and the thermal cycle of laser quenching is fast.
2. Almost no damage to surface roughness by using a thin coating with anti-oxidation protection.
3. Numerical control quenching of laser quenching without cracking quantification.
4. Numerical control quenching for local, groove and groove quenching location.
5. Laser quenching is clean and does not require cooling media such as water or oil.
6. The hardness of quenching is higher than that of conventional method, the microstructure of quenching layer is fine, and the toughness is good.
7. Laser quenching is rapid heating, self-quenching, does not need furnace insulation and coolant quenching, is a pollution-free green environmental protection heat treatment process, can be easily implemented to large mold surface uniform quenching.
8. Due to the fast laser heating speed, small heat affected area, and surface scanning heating quenching, that is, instant local heating quenching, the deformation of the treated mold is very small.
9. Because the laser beam divergence Angle is very small and has good directivity, it can quench the mold surface locally through the light guide system.
10 laser surface hardening hardening layer depth is generally 0.3 ~ 1.5mm.
Composition
laser
The equipment used for laser quenching includes semiconductor fiber output laser, fiber laser, all-solid-state laser, among which semiconductor fiber output laser is widely used in the field of quenching.
The selection of laser should consider the following aspects:
1. Laser output good beam quality, electro-optical conversion rate, fiber numerical aperture, and mode and mode stability.
2. Stability of laser output power.
3. The laser should have high reliability and be able to meet the continuous work in industrial processing environment.
4. The laser itself should have good maintenance, fault diagnosis and linkage functions;
5. The operation is simple and convenient.
6. Equipment sales manufacturer's economic and technical ability, credibility degree. You must avoid penny wise and pound foolish.
7. Whether the supplementary source of equipment wearing parts is guaranteed and the supply channel is smooth.
Picture display
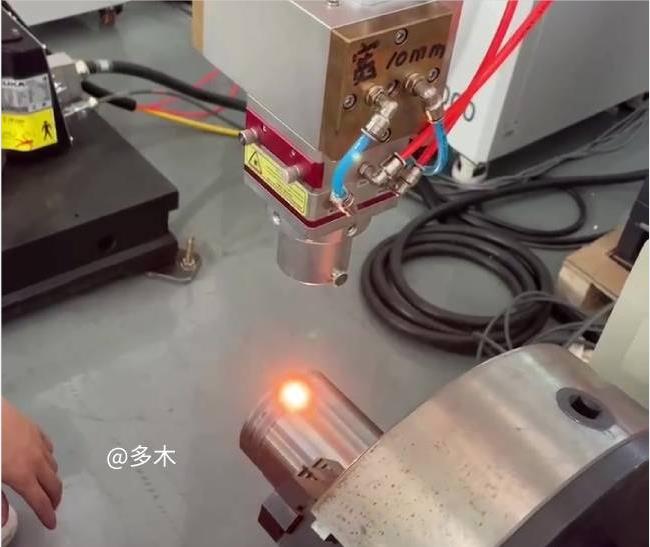
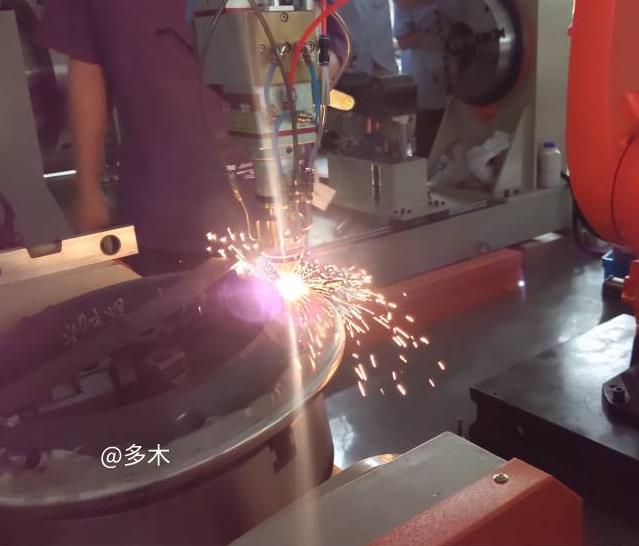
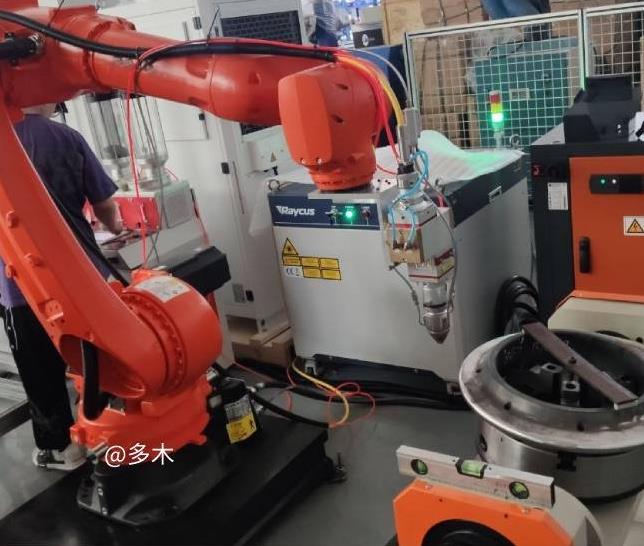
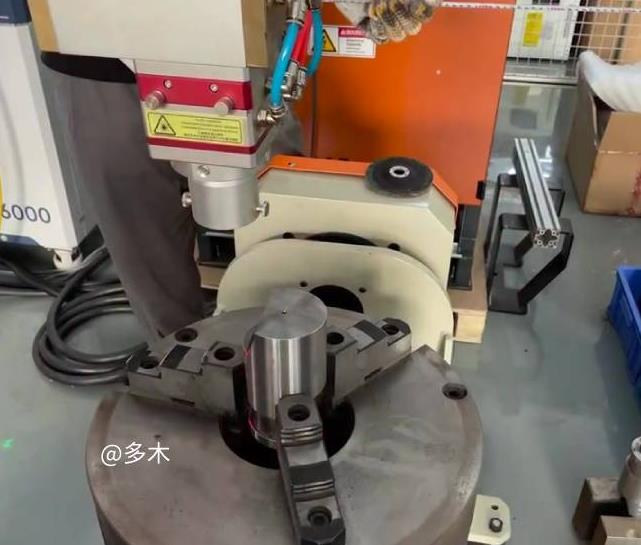
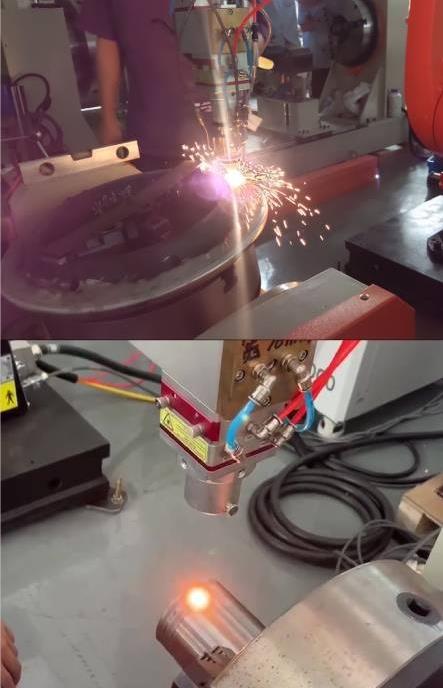