How to surfacing the ball Valve with PTA Welding
Shanghai Duomu has a copious experience in surfacing valve with PTA welding.
It is surfacing Co 6 that the deposite pool is clear and fluid, The dilution rate is contrable and it is no crack.
Notice:
A. It would be oxidized of the beads when the surfacing material encount the high tempreture that it is easy to the result in
oxides to enter the molten pool, If you didn't operate well that it is accessible to emerge the pore.
B. The welding surfacing is the shape of arc, it is cinch to come out slag inclusion on the both side of beads in the proceess of wiggle. So it is necessary to add the pause time.
C. The Mode of welding suggested is wiggle + progrssion with low rate to ease the speed too fast of lap which generated the bead joint to be possible to appear crack by cause of excessive stress.
The parameters as follow, as your reference
Workpiece | Ball Valve | ||||
Diameter | 165 mm | ||||
Surfacing powder | Co 6 | ||||
Surfacing thickness | 2.5 mm | ||||
Sufacing type | PTA | ||||
Equipemnt Mode | V03BD+ball valve tooling | ||||
Time preheat | 2H | ||||
Mode preheat | Electrical heating | ||||
Min. temperature preheat | 150 ℃ | ||||
Max. temperature interpass | 350℃ | ||||
Surfacing Mode | Wiggle + Progression | Current parameter | Sheild gas | ||
Turning speed | 0.31r/min | Main arc current | 80A | Gas | Ar |
Wiggle width | 8.8 mm | Base value current | 45A | Powder feeding gas | 3.5L/min |
Wiggle speed | 20mm/s | Pilot arc current | 20A | Ion gas | 1.2L/min |
Time left pause | 0.3 s | Powder feeding rate | 20g/min | Shield gas | 10L/min |
Time right pause | 0 s | Raise time | 0.1s | ||
Progression distance | 6.7mm | Drop time | 0.5s | ||
Progression speed | 1.4mm/s | Shield time | 10s | ||
Heat preservation temperature | 450℃ for 2h-2.5h | ||||
Tapping temperature | Cool in still air as 300℃ |

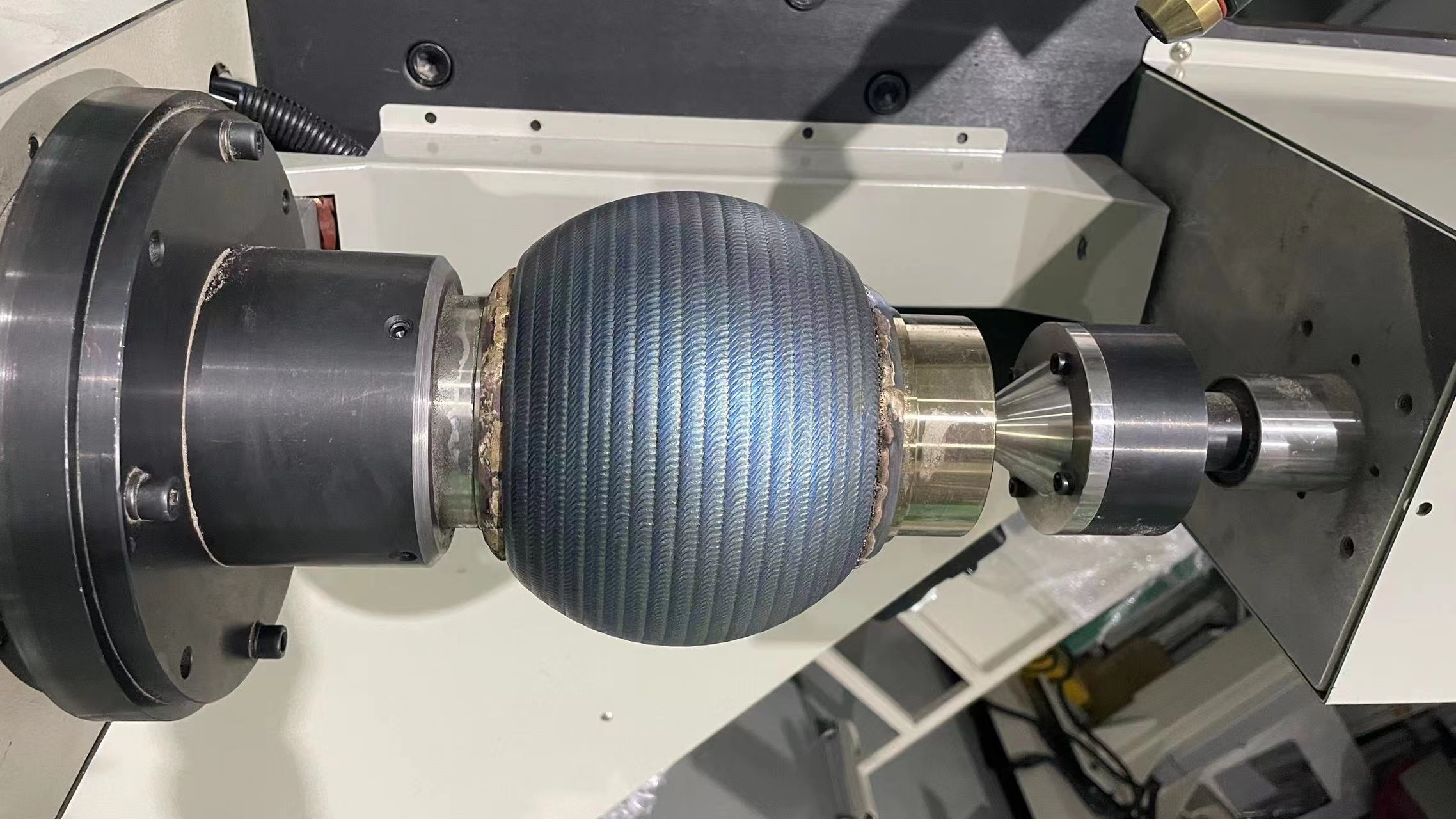
Video
Post time: Nov-03-2022