1.1 Akımın kalıplama üzerindeki etkisikaplama tabakası
Akım(A) | Dfüzyon (birleşme)(mm) | Fkat yüksekliği(mm) | Genişlik(mm) |
70 | 0,19 | 4.26 | 16.41 |
80 | 0,35 | 4.07 | 17.08 |
90 | 0,88 | 3.43 | 17.48 |
100 | 1.03 | 2,73 | 17.58 |
110 | 1.25 | 2.65 | 18.14 |
Tablo 3.1 Farklı akımlara sahip kaplama tabakasının kesit geometrisi
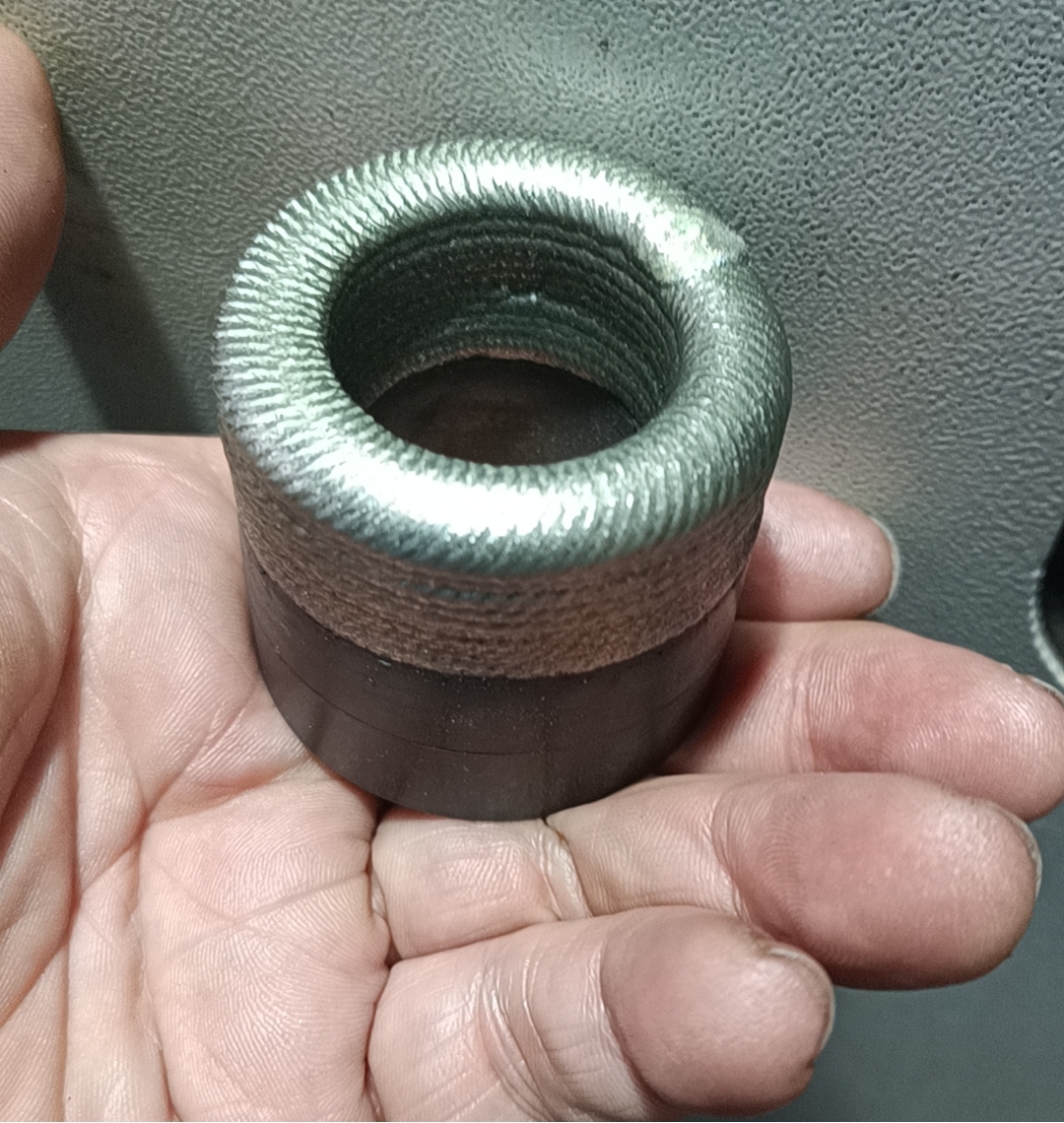
Akım arttıkça, kaplama tabakasının derinliği ve genişliği artar ve tabaka yüksekliği azalır. Bunun nedeni, akımdaki artıştır, üretilen ısı sadece kaplama metalini eritmekle kalmaz, aynı zamanda alt tabakanın bir kısmının erimesi, kaplama ve alt tabakanın karışması meydana gelir, böylece kaplama tabakası bir bütün olarak çöker, bunun sonucunda füzyon derinliği artar, tabaka yüksekliği azalır; ve akımı artırarak plazma arkının daha kaba olmasını sağlar, ısı kaynağının sıcaklık aralığı artar, alt tabaka yayılma yeteneğindeki erimiş havuz daha güçlü olur, böylece erimiş havuzun genişliği artar.
1.2 EtkisikaynakErimiş kaplama tabakasının kalıplanmasında hız
Kaynak hızı(mm/s) | Dfüzyon (birleşme)(mm) | Fkat yüksekliği(mm) | Genişlik(mm) |
4 | 1.17 | 4.34 | 17.61 |
5 | 1.06 | 2,73 | 17.58 |
6 | 0,35 | 2.61 | 16.96 |
7 | 0,13 | 2.55 | 15.01 |
8 | — | — | — |
Tablo 3.2 Farklı kaynak hızlarına sahip erimiş kaplama katmanlarının kesit geometrisi
Kaynak hızının artmasıyla, kaplama tabakasının füzyon derinliği azalır, tabaka yüksekliği önce keskin bir azalma gösterir ve sonra yavaşça küçülür, genişlik azalır. Kaynak hızı 4 mm/s olduğunda, kaplama metalinin belirli bir ölçüde artmasıyla, füzyon derinliği 1,17 mm'dir, bu sırada, birim uzunluk başına ısı girişi temel malzemenin daha fazla erimesini sağlayamaz, füzyon kaplama tabakası 4,34 mm'lik tabaka yüksekliğinin yüksekliğini yığmaya devam eder; kaynak hızı 5 mm/s'ye çıkar, birim uzunluk başına ısı girişi, tel besleme miktarı azalır, böylece füzyon derinliği, tabaka yüksekliği, genişlik azalır; kaynak hızı yukarıda belirtildiği gibi artmaya devam ederse, bu sırada ısı girişi yetersizdir, temel malzemenin sadece küçük bir kısmı eriyebilir, füzyon kaplama tabakası yüksekliği önce keskin bir azalma gösterir ve sonra yavaşça küçülür, genişlik azalır. Yukarıda belirtildiği gibi kaynak hızı artırılmaya devam edilirse, bu sırada ısı girdisi yetersiz kalır, taban malzemesinin sadece küçük bir kısmı eritilebilir, füzyon kaplama tabakası sarkma yapmaz, bunun sonucunda füzyon derinliğinde daha fazla azalma olurken, tabaka yüksekliğinde daha az azalma olur.
1.3 Tel besleme hızının kaplama tabakasının kalıplanmasına etkisi
Tel besleme hızı(mm/s) | Dfüzyon (birleşme)(mm) | Fkat yüksekliği(mm) | Genişlik(mm) |
40 | 1.43 | 2.24 | 19.91 |
50 | 1.25 | 2,56 | 18.86 |
60 | 1.03 | 2,73 | 17.58 |
70 | 0,71 | 3.46 | 15.82 |
80 | 0,16 | 5.16 | 14.20 |
Tablo 3.3 Farklı tel besleme hızlarında kaplama tabakasının kesitinin geometrik boyutları.
Tel besleme hızı arttıkça, kaplama tabakasının derinliği ve genişliği azalır ve tabaka yüksekliği artar. Bunun nedeni, akım ve kaynak hızı belirli olduğunda, birim uzunluk başına ısı girişinin belirli olması ve tel besleme hızının artmasıyla, birim uzunluk başına dolgu teli miktarının artması ve kaplama metalinin daha fazla ısı emmesi gerekmesidir ve ısı girişi tüm kaplama tabakasını tamamen eritemediğinde, temel malzeme kısmı daha az erir, böylece erime derinliği azalır ve tabakanın yüksekliği artar ve temel malzeme kısmına yakın kaplama metalinin yayılma kapasitesi bozulur, böylece genişlik hızla azalır. Genişlik hızla azalacaktır.
Özetle, plazma ark kaplama 2205 dubleks paslanmaz çelik tabakasının etkili işlem parametreleri şu aralıktadır: akım 90 A ~ 110 A, kaynak hızı 4 mm / s ~ 6 mm / s, tel besleme hızı 50 mm / s ~ 70 mm / s, iyon gazı akış hızı 1,5 L / dak.
2 Füzyon kaplama tabakası oluşturma proses parametrelerinin optimizasyonunun tepki yüzeyi yöntemine dayalı olarak
Tepki yüzey yöntemi (Response surface method, RSM), deneysel tasarım ve optimizasyon yöntemlerinin istatistiksel tekniklerinin bir kombinasyonudur, test verilerinin analizi, etki faktöründen ve uydurma fonksiyonunun tepki değerinden ve üç boyutlu yüzey haritasından türetilebilir, sezgisel olarak etki faktörünü ve tepki değerini gerçek test arasındaki ilişkinin yansıtabilir, öngörücü bir optimizasyon rolü vardır. Yukarıdaki nedenlere dayanarak, süreç optimizasyon programını geliştirmek, akımı, kaynak hızını, tel besleme hızını ve füzyon kaplama tabakası seyreltme oranını, akım, kaynak hızı, tel besleme hızı ve füzyon kaplama tabakası seyreltme oranı arasındaki ilişkinin en boy oranını ve süreç parametrelerinden ve seyreltme oranından türetilen matematiksel modellemeyi, fonksiyonun en boy oranını kullanarak füzyon kaplama tabakası kalitesinin tahminini elde etmek için merkezi kompozit tasarımda (Central composite design, CCD) RSM'nin seçilmesi.
2.1 Kaplama tabakasının seyreltme oranına proses parametrelerinin etkisi.
Tablo 3.8 Proses optimizasyon sonuçları ve doğrulama
Grup | X1(A) | X2(mm·s-1) | X3(mm·s-1) | seyreltme oranı(%) | en boy oranı |
Tahmin Grubu | 99 | 6 | 50 | 14.8 | 4.36 |
Test Grubu 1 | 99 | 6 | 50 | 13.9 | 4.13 |
Test Grubu 2 | 99 | 6 | 50 | 15.5 | 4.56 |
Test Grubu 3 | 99 | 6 | 50 | 14.3 | 4.27 |
Ortalama hata | 2.9 | 2.3 |
(PTA kaynakçılığı Shanghai Duomu tarafından yapıldı)
Şekil 3.16 Optimum işlem parametreleri test sonuçları (a) Test grubu 1; (b) Test grubu 2; (c) Test grubu 3
Yüksek kaliteli kaplama tabakası, küçük bir seyreltme oranına ve büyük bir en boy oranına sahip olmayı hedefler. Optimum işlem parametreleri şunlardır: akım 99 A, kaynak hızı 6 mm-s-1, tel besleme hızı 50 mm-s-1. Optimum işlem altında hazırlanan kaplama tabakasının ortalama seyreltme oranı yaklaşık %14,6'dır ve ortalama en boy oranı 4,33'tür ve model tahmin değeri ile deneysel değer arasındaki ortalama hata %5'ten azdır, bu da modelin yüksek derecede doğruluğa sahip olduğunu ve optimum işlem altında oluşturulan kaplama tabakasının kalitesinin iyi olduğunu gösterir.
Gönderi zamanı: 31-Oca-2024