Как использовать плазменную обработку для наплавки подшипников TC?Подшипники TC обычно относятся к шарикоподшипникам с глубокими канавками и резиновыми уплотнениями, которые широко используются в различном механическом оборудовании, особенно там, где требуются хорошие уплотнительные характеристики. Длительное воздействие этой среды неизбежно приведет к износу и коррозии. Плазма используется для расплавления и покрытия внутренней части подшипников TC для получения износостойкого и коррозионностойкого покрытия высокой твердости. Это экономит расходы на замену.
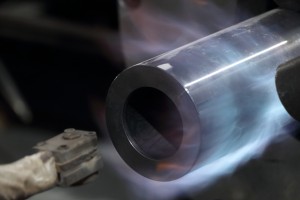
Принцип технологии плазменной наплавки
Плазменная наплавкаэто процесс, в котором порошок сплава расплавляется плазменной дугой и распыляется на поверхность подложки для формирования высокоэффективного покрытия. Он характеризуется образованием металлургической связи между покрытием и подложкой, что значительно улучшает эксплуатационные характеристики подложки.
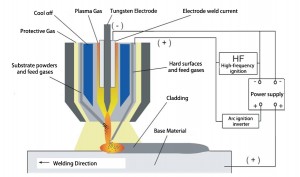
Подготовительные работы перед плазменной наплавкой отверстия подшипника TC
Ниже представлен полный набор решений для плазменной наплавки отверстий подшипников TC, охватывающий технологический процесс, технические параметры, выбор материалов и методы последующей обработки, позволяющие обеспечить эффективный ремонт или улучшение эксплуатационных характеристик отверстий подшипников.
Какова цель покрытия подшипников TC?
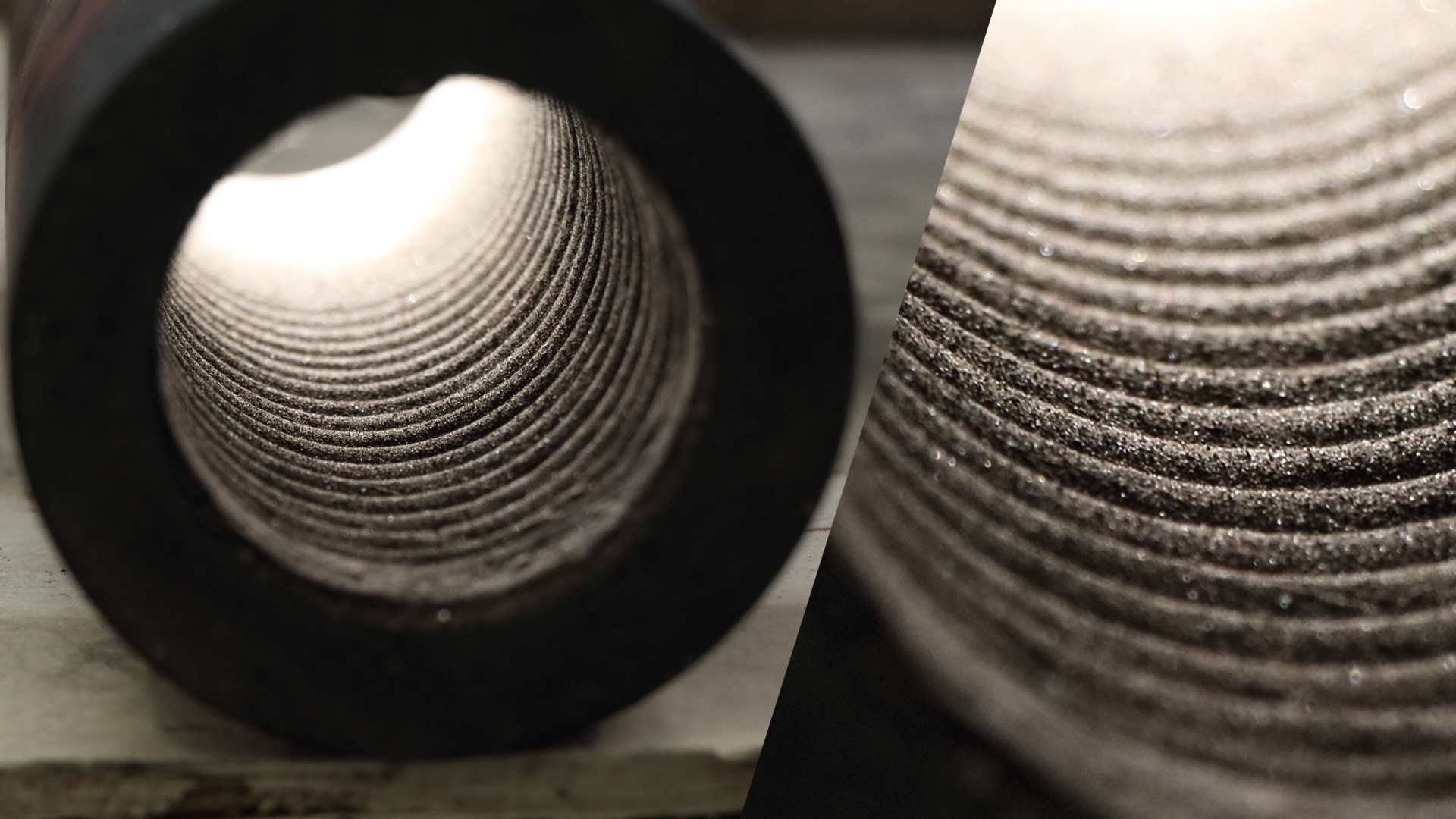
1. Восстановите изношенные или корродированные размеры отверстий и повысьте точность.
2. Повышение износостойкости, коррозионной стойкости и высокотемпературных характеристик поверхности отверстия.
3. Увеличить общий срок службы подшипника для соответствия требованиям тяжелых условий эксплуатации.
Решение
1. Подготовка
- Проверка и оценка:
- Используйте КИМ для определения отклонения размеров отверстия подшипника и оценки объема ремонта.
- Проанализируйте рабочую среду и определите эксплуатационные характеристики отверстия, которые необходимо улучшить (например, износостойкость, коррозионная стойкость и т. д.).
- Предварительная обработка поверхности:
- Очистите отверстие подшипника, чтобы удалить масло, окислившийся слой и коррозию с поверхности.
- Используйте пескоструйную обработку или механическую обработку для повышения шероховатости поверхности отверстия (Ra 6,3-12,5 мкм) и улучшить адгезию покрытия.
В зависимости от условий работы подшипников (таких как нагрузка, скорость, температура) следует выбрать соответствующий материал покрытия:
- Порошок сплава на основе никеля:
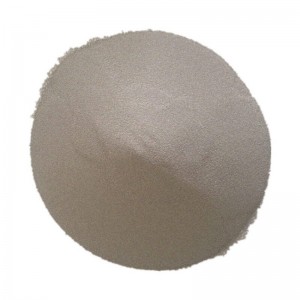
- Область применения: высокая температура, высокая коррозионная среда.
- Характеристики: износостойкий, коррозионностойкий, твердость до50-60 HRC.
- Порошок сплава на основе кобальта (например, серии Stellite):

- Сценарий: высокая температура, высокая нагрузка.
- Характеристики: стойкость к окислению при высоких температурах, хорошая ударопрочность, твердость до40-60 HRC.
- Порошок сплава на основе железа:
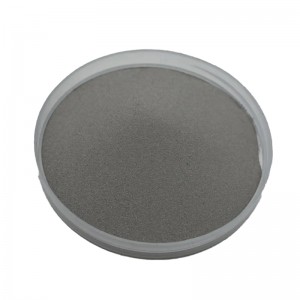
- Сценарий применения: общепромышленное оборудование, экономичный выбор.
- Характеристики: умеренная износостойкость, низкая стоимость.
3. Процесс плазменной наплавки
- Выбор оборудования:
- Использование высокоточного оборудования плазменной наплавки с ЧПУ для обеспечения равномерности наплавочного слоя.
- Оснащен небольшой насадкой для наплавки внутренних отверстий, подходит для деталей с ограниченными внутренними диаметрами подшипников.
- Параметры процесса:
- Ток плавления: 80-120 А (регулируется в зависимости от материала).
- Скорость плавления: 10-50 мм/мин.
- Расход газа: 15-20 л/мин (защитный газ: аргон).
- Толщина плавления: 0,5-2,0 мм, ремонт большего количества послойных плавлений.
- Контроль температуры между слоями: не более 150 °C, чтобы избежать накопления тепла, приводящего к деформации подложки.
- Процесс плавления:
1. Отрегулируйте центр внутреннего отверстия так, чтобы он совпадал с плавильным соплом, что обеспечит равномерность плавления.
2. нижний слой, образующий равномерный металлургический связующий слой.
3. В зависимости от толщины слоистой облицовки каждый слой выполняется с естественным охлаждением или вспомогательным охлаждением.
4. Последующее лечение
- Механическая обработка:
- После завершения плакирования отверстие обрабатывается до проектного размера путем внутреннего шлифования или прецизионного точения, чтобы гарантировать, что допуски размеров и шероховатость поверхности соответствуют требованиям (например, Ra≤0,4 мкм).
- Термическая обработка (по желанию):
- Термическая обработка для снятия напряжений наплавленного слоя оболочки с целью предотвращения образования трещин, вызванных остаточными напряжениями.
- Проверка оболочки:
- Испытание на твердость: твердость поверхности покрытия должна соответствовать проектным требованиям (например, 50-60 HRC).
- Неразрушающий контроль: ультразвуковая или магнитопорошковая дефектоскопия покрытия на наличие трещин и пор.
- Испытание прочности сцепления: прочность сцепления между покрытием и основным материалом должна соответствовать требованиям (обычно ≥30 МПа).
Преимущества плазменной наплавки подшипников TC
1. Экономическая эффективность: по сравнению с заменой подшипников на новые, ремонт методом плазменной наплавки обходится дешевле и позволяет экономить материальные затраты.
2. Улучшение эксплуатационных характеристик: эксплуатационные характеристики материала с покрытием выше, чем у исходного материала, что продлевает срок службы.
3. Гибкость процесса: можно выбирать различные материалы покрытия в зависимости от фактических условий работы подшипников.
4. Многоразовое использование: подшипники можно ремонтировать много раз после повреждения.
На что следует обратить внимание при выборе покрытия подшипника TC?
1. Контроль подводимого тепла:
Избегайте перегрева основного материала в процессе наплавки, так как это может привести к деформации или ухудшению эксплуатационных характеристик подшипника.
2. Допуски размеров:
После наплавки отверстие должно быть подвергнуто точной механической обработке в пределах допуска (например, уровня H7 или H6).
3. Адаптация к среде эксплуатации:
Оптимизируйте материал покрытия и параметры процесса в соответствии с условиями эксплуатации подшипника (например, температура, среда).
Области применения плазменной наплавки подшипников скольжения
•Горнодобывающее оборудование: отверстия подшипников требуют ремонта из-за сильного износа под нагрузкой.
•Автомобильная промышленность: ремонт отверстий высокоточных подшипников для повышения их долговечности.
•Строительная техника: повышение износостойкости и коррозионной стойкости подшипников гидравлических систем.
•Общепромышленное оборудование: увеличение срока службы подшипников общего назначения.
Время публикации: 24 декабря 2024 г.