1.1 Влияние тока на формованиеоблицовочный слой
Текущий(A) | Depth (слияния)(mm) | Fвысота пола(mm) | ширина(mm) |
70 | 0,19 | 4.26 | 16.41 |
80 | 0,35 | 4.07 | 17.08 |
90 | 0,88 | 3.43 | 17.48 |
100 | 1.03 | 2.73 | 17.58 |
110 | 1.25 | 2.65 | 18.14 |
Таблица 3.1 Геометрия поперечного сечения слоя оболочки при различных токах
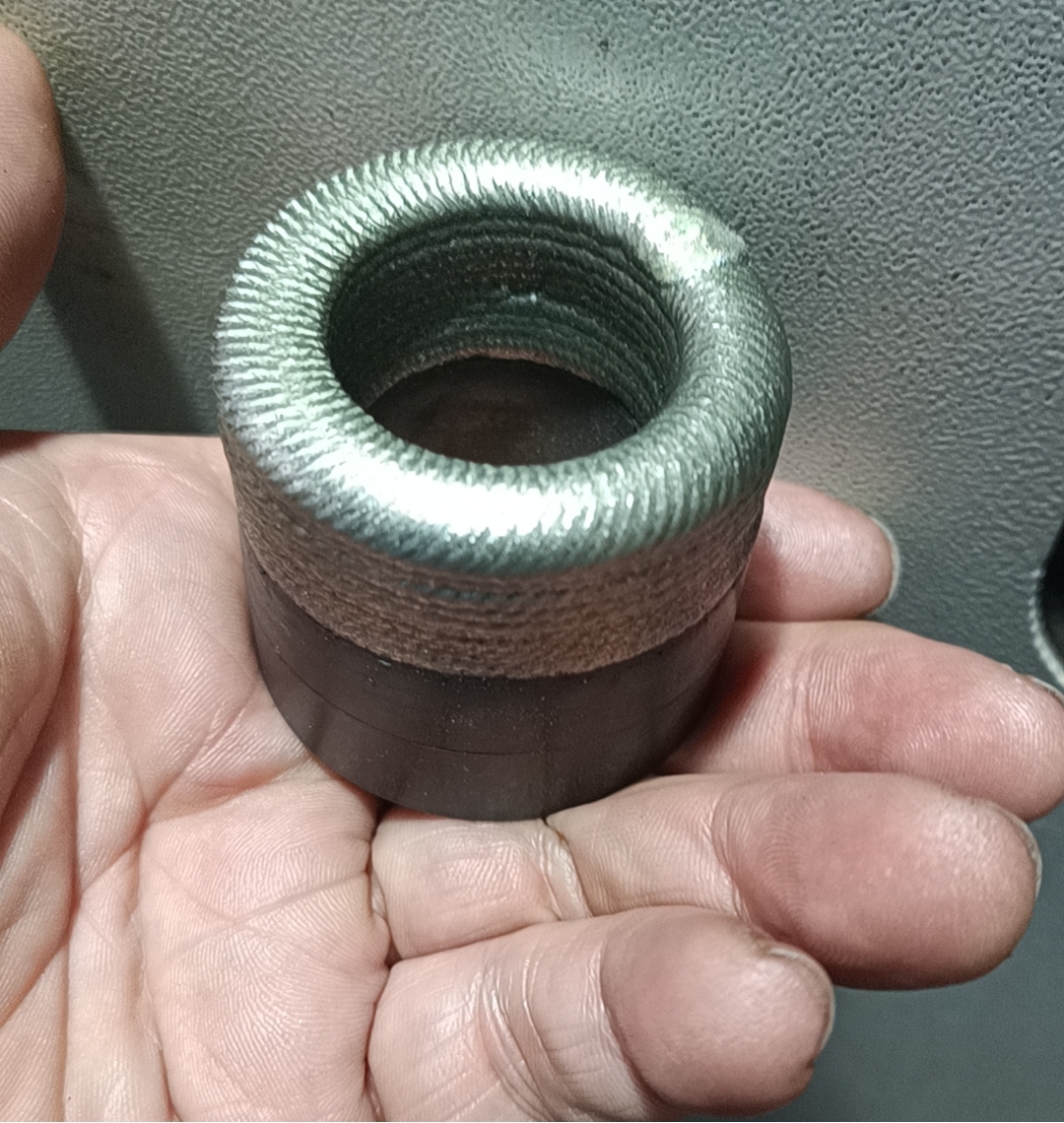
По мере увеличения тока увеличивается глубина и ширина слоя оболочки, а высота слоя уменьшается. Это происходит из-за увеличения тока, выделяемое тепло расплавит не только металл оболочки, но и часть расплавления подложки, происходит смешивание оболочки и подложки, так что слой оболочки в целом оседает, что приводит к увеличению глубины плавления, высота слоя уменьшается; и увеличивая ток, плазменная дуга становится более грубой, увеличивая температурный диапазон источника тепла, расплавленная ванна в подложке имеет более сильную способность распространения, поэтому ширина расплавленной ванны увеличивается.
1.2 Эффектсваркаскорость формования расплавленного слоя облицовки
Скорость сварки(мм/с) | Depth (слияния)(mm) | Fвысота пола(mm) | ширина(mm) |
4 | 1.17 | 4.34 | 17.61 |
5 | 1.06 | 2.73 | 17.58 |
6 | 0,35 | 2.61 | 16.96 |
7 | 0,13 | 2.55 | 15.01 |
8 | — | — | — |
Таблица 3.2 Геометрия поперечного сечения расплавленных слоев наплавки при различных скоростях сварки
С увеличением скорости сварки глубина проплавления плакирующего слоя уменьшается, высота слоя сначала резко уменьшается, а затем медленно уменьшается, ширина уменьшается. Когда скорость сварки составляет 4 мм/с, с увеличением плакирующего металла до определенной степени глубина проплавления составляет 1,17 мм, в это время подвод тепла на единицу длины не может заставить основной материал дальше расплавиться, слой проплавления плакирования продолжает накапливаться на высоте слоя высотой 4,34 мм; скорость сварки увеличивается до 5 мм/с, подвод тепла на единицу длины, количество подаваемой проволоки уменьшаются, поэтому глубина проплавления, высота слоя, ширина уменьшаются; если скорость сварки продолжает увеличиваться, как упоминалось выше, в это время подвод тепла недостаточен, может расплавиться только небольшая часть основного материала, высота слоя проплавления плакирования сначала резко уменьшается, а затем медленно становится меньше, ширина уменьшается. Если скорость сварки продолжает увеличиваться, как упоминалось выше, то в этот момент подвод тепла недостаточен, расплавляется лишь небольшая часть основного материала, провисание слоя плавления не наблюдается, что приводит к большему уменьшению глубины плавления, тогда как высота слоя уменьшается меньше.
1.3 Влияние скорости подачи проволоки на формование облицовочного слоя
Скорость подачи проволоки(мм/с) | Depth (слияния)(mm) | Fвысота пола(mm) | ширина(mm) |
40 | 1.43 | 2.24 | 19.91 |
50 | 1.25 | 2.56 | 18.86 |
60 | 1.03 | 2.73 | 17.58 |
70 | 0,71 | 3.46 | 15.82 |
80 | 0,16 | 5.16 | 14.20 |
Таблица 3.3 Геометрические размеры поперечного сечения наплавочного слоя при различных скоростях подачи проволоки.
С увеличением скорости подачи проволоки глубина и ширина слоя покрытия уменьшаются, а высота слоя увеличивается. Это связано с тем, что при определенных силе тока и скорости сварки определено количество тепла на единицу длины, а с увеличением скорости подачи проволоки увеличивается количество присадочной проволоки на единицу длины, и металл покрытия должен поглощать больше тепла, а когда количество тепла не может полностью расплавить весь слой покрытия, часть основного материала расплавляется меньше, поэтому глубина плавления уменьшается, а высота слоя увеличивается, а способность к растеканию металла покрытия вблизи части основного материала ухудшается, поэтому ширина быстро уменьшается. Ширина будет быстро уменьшаться.
Подводя итог, можно сказать, что эффективные параметры процесса плазменной дуговой наплавки дуплексного слоя нержавеющей стали 2205 варьируются в диапазоне: ток 90 А ~ 110 А, скорость сварки 4 мм/с ~ 6 мм/с, скорость подачи проволоки 50 мм/с ~ 70 мм/с, расход ионного газа 1,5 л/мин.
2. Оптимизация параметров процесса формирования наплавленного слоя на основе метода поверхности отклика.
Метод поверхности отклика (Response surface method, RSM) представляет собой комбинацию экспериментального проектирования и статистических методов оптимизации, анализа данных испытаний, может быть получен из импакт-фактора и значения отклика подгоночной функции и трехмерной карты поверхности, может интуитивно отражать импакт-фактор и значение отклика отношения между фактическим испытанием имеет предсказательную, оптимизационную роль. Исходя из вышеуказанных причин, выбор RSM в центральном композитном дизайне (Central composite design, CCD) для разработки программы оптимизации процесса, для исследования тока, скорости сварки, скорости подачи проволоки и скорости разбавления слоя наплавления, соотношения сторон взаимосвязи между током, скоростью сварки, скоростью подачи проволоки и скоростью разбавления слоя наплавления, и математического моделирования, полученного из параметров процесса и скорости разбавления, соотношения сторон функции, для достижения прогнозирования качества слоя наплавления.
2.1 Влияние параметров процесса на скорость растворения наплавочного слоя.
Таблица 3.8 Результаты оптимизации процесса и проверка
Группа | X1(A) | X2(мм·с-1) | X3(мм·с-1) | Коэффициент разбавления(%) | соотношение сторон |
Группа прогнозирования | 99 | 6 | 50 | 14.8 | 4.36 |
Тестовая группа 1 | 99 | 6 | 50 | 13.9 | 4.13 |
Тестовая группа 2 | 99 | 6 | 50 | 15.5 | 4.56 |
Тестовая группа 3 | 99 | 6 | 50 | 14.3 | 4.27 |
Средняя ошибка | 2.9 | 2.3 |
(сварка PTA компанией Shanghai Duomu)
Рисунок 3.16 Результаты испытаний оптимальных параметров процесса (a) Тестовая группа 1; (b) Тестовая группа 2; (c) Тестовая группа 3
Высококачественный слой оболочки стремится иметь небольшую скорость разбавления и большое отношение сторон. Оптимальные параметры процесса: ток 99 А, скорость сварки 6 мм-с-1, скорость подачи проволоки 50 мм-с-1. Средняя скорость разбавления слоя оболочки, подготовленного в оптимальном процессе, составляет около 14,6%, а среднее отношение сторон составляет 4,33, а средняя ошибка между значением прогноза модели и экспериментальным значением составляет менее 5%, что указывает на высокую степень точности модели, а качество слоя оболочки, сформированного в оптимальном процессе, хорошее.
Время публикации: 31 января 2024 г.