Применение технологии плазменной наплавки для упрочнения поверхности буровых долот PDC является эффективным средством повышения их износостойкости, ударопрочности и коррозионной стойкости.
1. Подготовительный этап
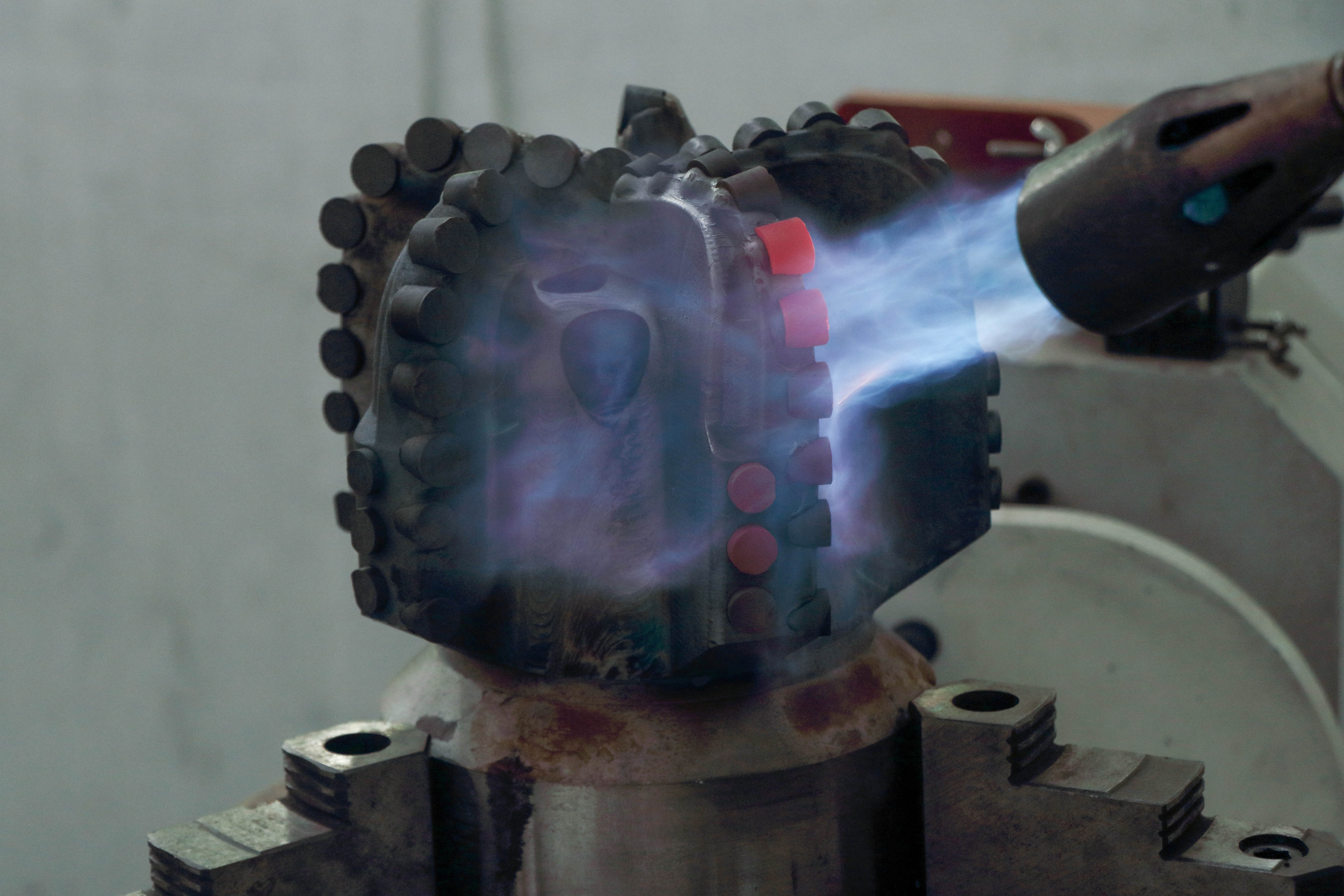
(1) Определить материал облицовки
- Наиболее часто используемые облицовочные материалы:
- Сплав на основе кобальта: высокая износостойкость и коррозионная стойкость.
- Сплав на основе никеля: устойчив к высокотемпературному окислению и химической коррозии.
- Сплавы на основе железа: экономичны и подходят для случаев, когда требуются средние требования к износостойкости.
- Сплавы, армированные керамическими частицами: например, WC (карбид вольфрама), TiC (карбид титана) и т. д. для очень высоких требований к износостойкости.
(2) Определение площади облицовки
- Наплавка буровых долот PDC обычно применяется для:
- Боковая часть: для повышения износостойкости, снижения трения и потерь при резании.
- Поверхность каркаса: для повышения общей коррозионной и ударопрочности.
(3) Предварительная обработка поверхности
- Очистите область наплавки от масла, окислов, покрытий и загрязнений.
- Механическая шлифовка или пескоструйная обработка для повышения шероховатости поверхности и улучшения сцепления наплавленного слоя облицовки с основанием.
2. Реализация процесса плакирования
(1) Настройка оборудования для плазменной наплавки
- Состав оборудования:
Плазменный сварочный пистолет, податчик порошка, автоматизированная плазменная сварочная машина, и т. д..
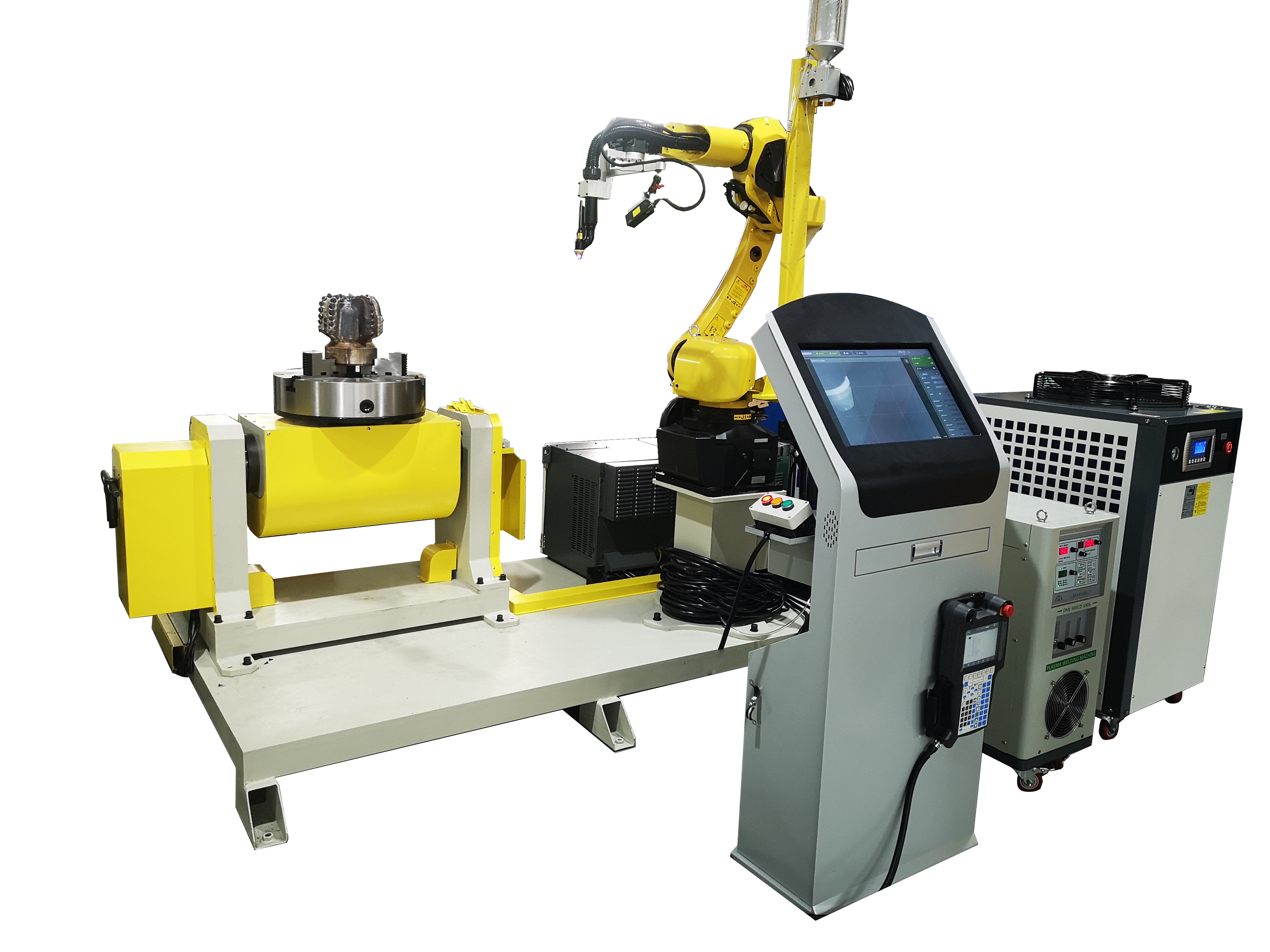
- Установите ключевые параметры:
- Ток и напряжение дуги: выбираются в зависимости от покрываемого материала, обычно в диапазоне 100-300 А.
- Подача тепла: отрегулируйте для контроля деформации субстрата и скорости разбавления.
- Скорость подачи порошка: обычно в диапазоне 10~50 г/мин для обеспечения равномерности наплавляемого слоя.
(2) Выполнение облицовки
- Процесс плакирования:
1. Зажигание плазменной дуги, образование высокотемпературной плавильной ванны.
2. Через систему подачи порошка порошковый материал распыляется в расплавленную ванну и металлургически связывается с подложкой.
3. в соответствии с формой сверла, по заданной траектории для равномерной наплавки, чтобы гарантировать отсутствие утечки наплавки или переплавления.
- Контролируйте тепловое воздействие: избегайте перегрева или деформации основания буровой коронки PDC, регулируя параметры плазменной дуги и метод охлаждения.
(3) Охлаждающая обработка
- Естественное охлаждение или метод контролируемого охлаждения с контролируемой скоростью для предотвращения трещин, вызванных термическим напряжением.
3. Постлечебный этап
(1) Проверка качества облицовки
- Внешний осмотр: проверьте, является ли облицовочный слой однородным, не имеет ли он трещин и воздушных полостей.
- Тестирование производительности: измерение твердости, толщины (обычно 0,5 ~ 3 мм), прочности сцепления и других показателей.
- Неразрушающий контроль: используйте ультразвуковой или рентгеновский контроль для выявления внутренних дефектов.
(2) Отделка
- Если после наплавки поверхность шероховатая, требуется токарная или шлифовальная обработка для соответствия требованиям к размеру и форме буровых долот PDC.
(3) Оптимизация производительности
- Термическая обработка: при необходимости закалка или отпуск наплавленного слоя оболочки для дальнейшей оптимизации его организационных свойств.
4. Меры предосторожности
1. Избегайте перегрева.
- Во время плазменной наплавки необходимо строго контролировать подачу тепла, чтобы избежать термического повреждения вставки PDC и подложки.
2. Соответствие материалов
- Материал покрытия должен соответствовать материалу основания долота PDC, чтобы обеспечить прочность соединения и постоянство эксплуатационных характеристик.
3. Экологический контроль
- По возможности в условиях низкой влажности или защитной газовой среды, чтобы избежать окисления, влияющего на качество облицовки.
Этот процесс можно использовать для повышения производительности новых долот PDC, а также для ремонта изношенных долот.
Время публикации: 09.01.2025