1.1 Wpływ prądu na kształtowaniewarstwa okładzinowa
Aktualny(A) | Depth (fuzji)(mm) | Fwysokość piętra(mm) | szerokość(mm) |
70 | 0,19 | 4.26 | 16.41 |
80 | 0,35 | 4.07 | 17.08 |
90 | 0,88 | 3.43 | 17,48 |
100 | 1.03 | 2,73 | 17,58 |
110 | 1,25 | 2,65 | 18.14 |
Tabela 3.1 Geometria przekroju warstwy okładzinowej przy różnych prądach
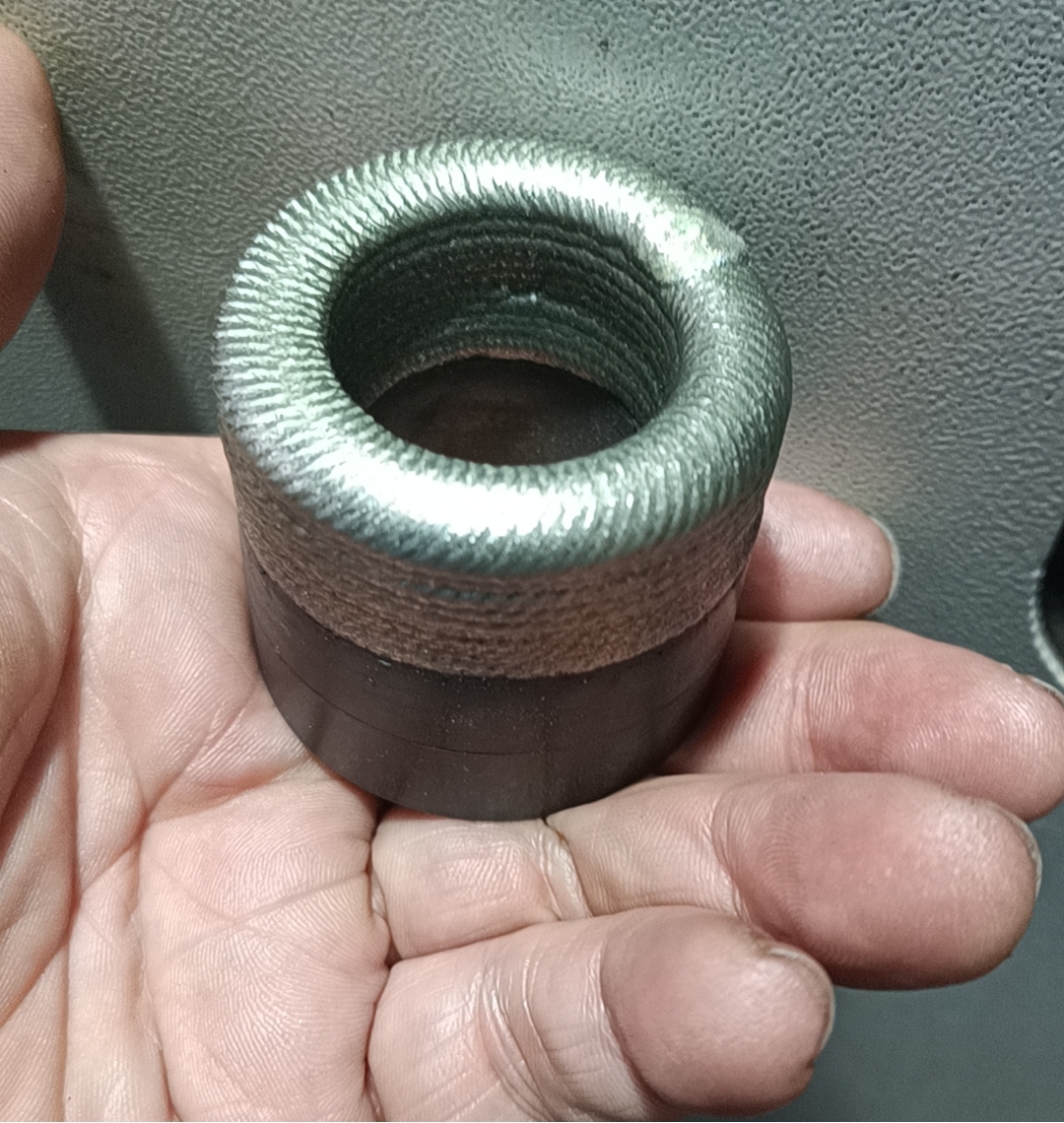
W miarę wzrostu prądu głębokość i szerokość warstwy płaszcza wzrasta, a wysokość warstwy maleje. Dzieje się tak ze względu na wzrost prądu, generowane ciepło nie tylko stopi metal płaszcza, ale także część topnienia podłoża, płaszcz i mieszanie podłoża, tak że warstwa płaszcza jako całość osiada, co powoduje wzrost głębokości stopienia, wysokość warstwy maleje; i zwiększa prąd, sprawiając, że łuk plazmowy jest grubszy, zwiększa zakres temperatur źródła ciepła, zdolność rozpływu stopionego jeziorka w podłożu jest większa, więc szerokość stopionego jeziorka wzrasta.
1.2 Efektspawalniczyszybkość formowania stopionej warstwy okładzinowej
Prędkość spawania(mm/s) | Depth (fuzji)(mm) | Fwysokość piętra(mm) | szerokość(mm) |
4 | 1.17 | 4.34 | 17.61 |
5 | 1.06 | 2,73 | 17,58 |
6 | 0,35 | 2.61 | 16,96 |
7 | 0,13 | 2,55 | 15.01 |
8 | — | — | — |
Tabela 3.2 Geometria przekroju poprzecznego warstw napawanych stopionym metalem przy różnych prędkościach spawania
Wraz ze wzrostem prędkości spawania głębokość stopienia warstwy powłoki maleje, wysokość warstwy najpierw gwałtownie spada, a następnie powoli staje się mniejsza, szerokość maleje. Gdy prędkość spawania wynosi 4 mm/s, wraz ze wzrostem metalu powłoki do pewnego stopnia, głębokość stopienia wynosi 1,17 mm, w tym czasie ciepło doprowadzone na jednostkę długości nie może spowodować dalszego stopienia materiału bazowego, stopiona warstwa powłoki nadal się piętrzy, osiągając wysokość warstwy 4,34 mm; prędkość spawania wzrasta do 5 mm/s, ciepło doprowadzone na jednostkę długości, ilość podawanego drutu są zmniejszone, więc głębokość stopienia, wysokość warstwy, szerokość są zmniejszone; jeśli prędkość spawania nadal rośnie, jak wspomniano powyżej, ciepło doprowadzone jest w tym czasie niewystarczające, może stopić się tylko niewielka część materiału bazowego, wysokość stopionej warstwy powłoki najpierw gwałtownie spada, a następnie powoli staje się mniejsza, szerokość jest zmniejszona. Jeżeli prędkość spawania nadal wzrasta, jak wspomniano powyżej, ilość dostarczonego ciepła w tym momencie jest niewystarczająca, stopić można tylko niewielką część materiału bazowego, warstwa okładziny nie wydaje się uginać, co skutkuje większą redukcją głębokości stopienia, podczas gdy wysokość warstwy zmniejsza się w mniejszym stopniu.
1.3 Wpływ prędkości podawania drutu na formowanie warstwy pokrycia
Prędkość podawania drutu(mm/s) | Depth (fuzji)(mm) | Fwysokość piętra(mm) | szerokość(mm) |
40 | 1.43 | 2.24 | 19,91 |
50 | 1,25 | 2,56 | 18,86 |
60 | 1.03 | 2,73 | 17,58 |
70 | 0,71 | 3.46 | 15.82 |
80 | 0,16 | 5.16 | 14.20 |
Tabela 3.3 Wymiary geometryczne przekroju poprzecznego warstwy osłonowej przy różnych prędkościach podawania drutu.
W miarę wzrostu prędkości podawania drutu głębokość i szerokość warstwy powłoki zmniejsza się, a wysokość warstwy wzrasta. Wynika to z faktu, że gdy prąd i prędkość spawania są pewne, ciepło doprowadzone na jednostkę długości jest pewne, a wraz ze wzrostem prędkości podawania drutu, ilość drutu wypełniającego na jednostkę długości wzrasta, a metal powłoki musi pochłonąć więcej ciepła, a gdy ciepło doprowadzone nie jest w stanie całkowicie stopić całej warstwy powłoki, część materiału bazowego jest mniej stopiona, więc głębokość stopienia maleje, a wysokość warstwy wzrasta, a zdolność rozprzestrzeniania się metalu powłoki blisko części materiału bazowego pogarsza się, więc szerokość szybko się zmniejsza. Szerokość szybko się zmniejszy.
Podsumowując, efektywne parametry procesu napawania łukiem plazmowym warstwą stali nierdzewnej dupleksowej 2205 mieszczą się w zakresie: natężenie prądu 90 A ~ 110 A, prędkość spawania 4 mm/s ~ 6 mm/s, prędkość podawania drutu 50 mm/s ~ 70 mm/s, szybkość przepływu gazu jonowego 1,5 L/min.
2 W oparciu o metodę powierzchni odpowiedzi optymalizacji parametrów procesu formowania warstwy płaszcza fuzyjnego
Metoda powierzchni odpowiedzi (Response surface method, RSM) jest połączeniem eksperymentalnego projektu i statystycznych technik metod optymalizacji, analiza danych testowych, może być wyprowadzona ze współczynnika wpływu i wartości odpowiedzi funkcji dopasowania i trójwymiarowej mapy powierzchni, może intuicyjnie odzwierciedlać współczynnik wpływu i wartość odpowiedzi relacji między rzeczywistym testem ma predykcyjną, optymalizacyjną rolę. W oparciu o powyższe powody, wybór RSM w centralnym projekcie kompozytowym (Central composite design, CCD) w celu opracowania programu optymalizacji procesu, w celu zbadania prądu, prędkości spawania, prędkości podawania drutu i współczynnika rozcieńczenia warstwy napawania, współczynnika kształtu relacji między prądem, prędkością spawania, prędkością podawania drutu i współczynnikiem rozcieńczenia warstwy napawania oraz modelowania matematycznego, wyprowadzonego z parametrów procesu i współczynnika rozcieńczenia, współczynnika kształtu funkcji, w celu osiągnięcia prognozy jakości warstwy napawania.
2.1 Wpływ parametrów procesu na stopień rozcieńczenia warstwy osłonowej.
Tabela 3.8 Wyniki optymalizacji procesu i weryfikacja
Grupa | X1(A) | X2(mm·s-1) | X3(mm·s-1) | stosunek rozcieńczenia(%) | współczynnik proporcji |
Grupa Predykcyjna | 99 | 6 | 50 | 14.8 | 4.36 |
Grupa testowa 1 | 99 | 6 | 50 | 13.9 | 4.13 |
Grupa testowa 2 | 99 | 6 | 50 | 15,5 | 4,56 |
Grupa testowa 3 | 99 | 6 | 50 | 14.3 | 4.27 |
Średni błąd | 2.9 | 2.3 |
(Spawanie PTA przez Shanghai Duomu)
Rysunek 3.16 Wyniki testów optymalnych parametrów procesu (a) Grupa testowa 1; (b) Grupa testowa 2; (c) Grupa testowa 3
Wysokiej jakości warstwa powłoki ma mieć mały współczynnik rozcieńczenia i duży współczynnik kształtu. Optymalne parametry procesu to: prąd 99 A, prędkość spawania 6 mm-s-1, prędkość podawania drutu 50 mm-s-1. Średni współczynnik rozcieńczenia warstwy powłoki przygotowanej w optymalnym procesie wynosi około 14,6%, a średni współczynnik kształtu wynosi 4,33, a średni błąd między wartością przewidywaną modelu a wartością eksperymentalną jest mniejszy niż 5%, co wskazuje, że model ma wysoki stopień dokładności, a jakość warstwy powłoki utworzonej w optymalnym procesie jest dobra.
Czas publikacji: 31-01-2024