Zasada i wprowadzenie do napawania laserowego
Proces napawania: Napawanie laserowe można podzielić na dwie kategorie, w zależności od metody dostarczania materiałów napawanych, a mianowicie napawanie laserowe z zastosowaniem gotowych elementów i napawanie laserowe synchroniczne.
Wstępnie ustawione nakładanie laserowe polega na wcześniejszym umieszczeniu materiału nakładkowego na części nakładkowej powierzchni podłoża, a następnie naświetlaniu wiązką laserową w celu zeskanowania i stopienia. Materiał nakładkowy jest dodawany w postaci proszku lub drutu, a najczęściej stosowana jest postać proszku.
Synchroniczne napawanie laserowe polega na synchronicznym wysyłaniu materiałów powłokowych w postaci proszku lub drutu do roztopionego jeziorka przez dyszę podczas procesu napawania. Materiał powłoki jest dodawany w postaci proszku lub drutu, spośród których najczęściej stosowana jest postać proszku.
Główny proces napawania laserowego obejmuje: wstępną obróbkę powierzchni podłoża, nałożenie wstępnie przygotowanego materiału napawającego, podgrzewanie wstępne, nakładanie laserowe, obróbkę cieplną.
Główny przebieg procesu synchronicznego napawania laserowego obejmuje: wstępne przygotowanie powierzchni podłoża, podgrzewanie wstępne, synchroniczne napawanie laserowe, obróbkę cieplną.
Zgodnie z przebiegiem procesu, procesy związane z napawaniem laserowym obejmują głównie metodę wstępnej obróbki powierzchni podłoża, metodę podawania materiału napawanego, podgrzewanie wstępne i obróbkę cieplną końcową.
Zasada działania lasera:
Kompletny zestaw urządzeń do napawania laserowego składa się z: lasera, jednostki chłodzącej, mechanizmu podawania proszku, stołu obróbczego itp.
Wybór laserów: powszechnie stosowane typy laserów, takie jak lasery CO2, lasery na ciele stałym, lasery światłowodowe, lasery półprzewodnikowe itp., obsługują proces napawania laserowego.
Parametry procesu
Parametry procesu napawania laserowego obejmują głównie moc lasera, średnicę plamki, prędkość napawania, ilość rozogniskowania, prędkość podawania proszku, prędkość skanowania, temperaturę podgrzewania wstępnego itp. Parametry te mają duży wpływ na szybkość rozcieńczania warstwy napawania, pęknięcia, chropowatość powierzchni i zwartość części napawanych. Parametry te wpływają również na siebie nawzajem, co jest bardzo skomplikowanym procesem, a rozsądne metody kontroli muszą być stosowane w celu kontrolowania tych parametrów w dopuszczalnym zakresie procesu napawania laserowego.
Proces napawania laserowego ma 3 ważne parametry
moc lasera
Im większa moc lasera, tym większa ilość stopionego metalu powłoki i większe prawdopodobieństwo porowatości. Wraz ze wzrostem mocy lasera zwiększa się głębokość warstwy powłoki, otaczający ciekły metal gwałtownie fluktuuje, a dynamiczne krzepnięcie krystalizuje, tak że liczba porów jest stopniowo zmniejszana lub nawet eliminowana, a pęknięcia również stopniowo się zmniejszają. Gdy głębokość warstwy powłoki osiągnie głębokość graniczną, wraz ze wzrostem mocy wzrasta temperatura powierzchni podłoża, a zjawisko odkształceń i pęknięć nasila się. Jeśli moc lasera jest zbyt mała, topi się tylko powłoka powierzchniowa, a podłoże nie. W tym czasie na powierzchni warstwy powłoki występują lokalne pęknięcia. Pilling, pustki itp. nie osiągają celu powłoki powierzchniowej.
Średnica plamki
Wiązka laserowa jest na ogół okrągła. Szerokość warstwy płaszcza zależy głównie od średnicy plamki wiązki laserowej, średnica plamki wzrasta, a warstwa płaszcza staje się szersza. Różne rozmiary plamki powodują zmiany w rozkładzie energii na powierzchni warstwy płaszcza, a uzyskana morfologia i właściwości mikrostruktury warstwy płaszcza są zupełnie inne. Ogólnie rzecz biorąc, jakość warstwy płaszcza jest lepsza, gdy rozmiar plamki jest mały, a jakość warstwy płaszcza maleje wraz ze wzrostem rozmiaru plamki. Jednak średnica plamki jest zbyt mała, co nie sprzyja uzyskaniu warstwy płaszcza o dużej powierzchni. [3]
Prędkość okładziny
Prędkość napawania V ma podobny wpływ jak moc lasera P. Jeżeli prędkość napawania jest zbyt duża,proszek stopowynie może zostać całkowicie stopiony, a efekt wysokiej jakości pokrycia nie jest osiągnięty; jeśli prędkość pokrycia jest zbyt niska, jeziorko stopu istnieje zbyt długo, proszek jest przepalony, składniki stopu są tracone, a dopływ ciepła do matrycy jest duży. zwiększy to stopień odkształcenia.
Parametry napawania laserowego nie wpływają niezależnie na jakość makroskopową i mikroskopową warstwy napawania, ale wpływają na siebie nawzajem. Aby zilustrować kompleksowy wpływ mocy lasera P, średnicy plamki D i prędkości napawania V, zaproponowano koncepcję energii właściwej Es, a mianowicie:
Es=P/(DV)
Oznacza to energię promieniowania na jednostkę powierzchni i takie czynniki, jak moc lasera.gęstość mocyi prędkość okładziny można rozpatrywać łącznie.
Zmniejszenie energii właściwej jest korzystne dla zmniejszenia szybkości rozcieńczania i ma również pewien związek z grubością warstwy płaszcza. W warunkach stałej mocy lasera szybkość rozcieńczania warstwy płaszcza maleje wraz ze wzrostem średnicy plamki, a gdy prędkość płaszcza i średnica plamki są stałe, szybkość rozcieńczania warstwy płaszcza wzrasta wraz ze wzrostem mocy wiązki laserowej. Ponadto, wraz ze wzrostem prędkości płaszcza, głębokość topnienia podłoża maleje, a szybkość rozcieńczania warstwy płaszcza z materiału podłoża maleje.
W przypadku wieloprzebiegowego napawania laserowego głównym czynnikiem wpływającym na szybkość nakładania się warstw jestchropowatość powierzchniwarstwy okładzinowej. Gdy współczynnik nakładania się wzrasta, chropowatość powierzchni warstwy okładzinowej maleje, ale trudno zagwarantować jednorodność nakładającej się części. Głębokość obszaru nakładania się między ścieżkami okładzinowymi jest inna niż głębokość środka ścieżek okładzinowych, co wpływa na jednorodność całej warstwy okładzinowej. Ponadto resztkowe naprężenie rozciągające wieloprzebiegowej okładziny zostanie nałożone, co zwiększy lokalną wartość naprężenia całkowitego i zwiększy wrażliwość warstwy okładzinowej na pęknięcia. Podgrzewanie i odpuszczanie może zmniejszyć tendencję warstwy okładzinowej do pękania.
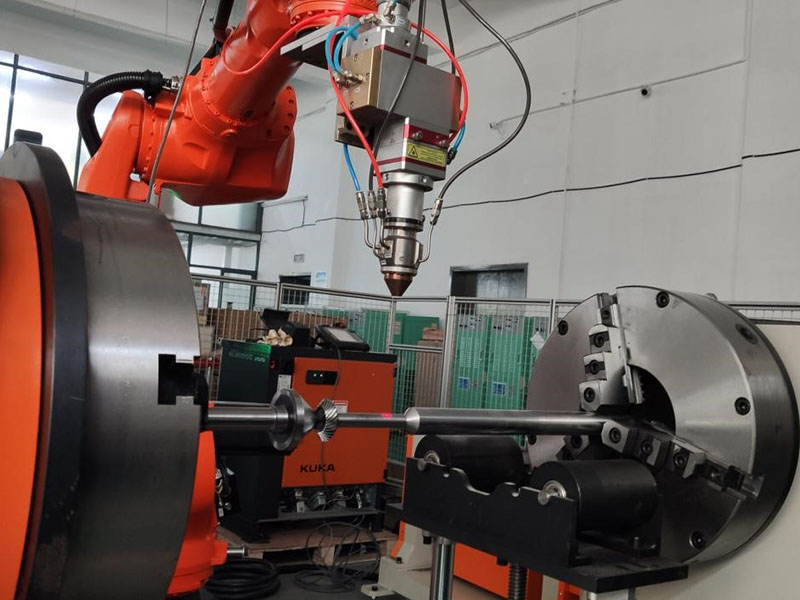
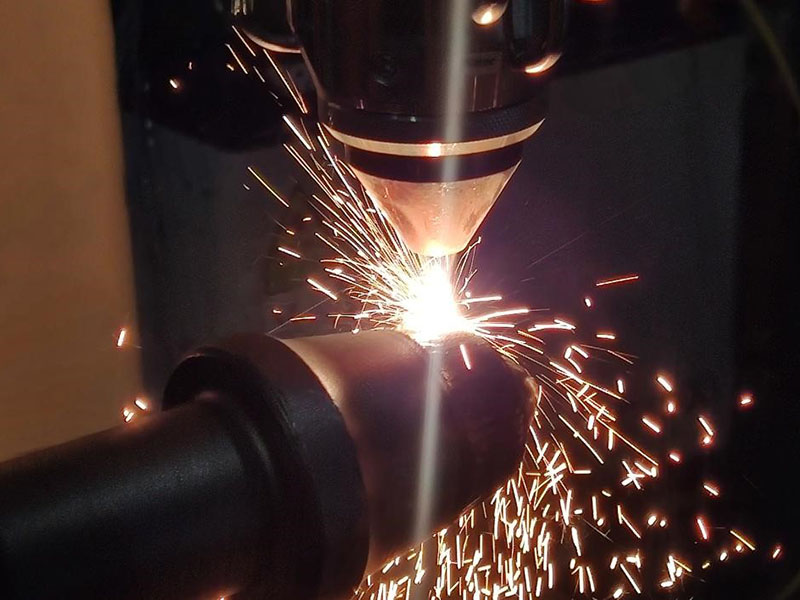
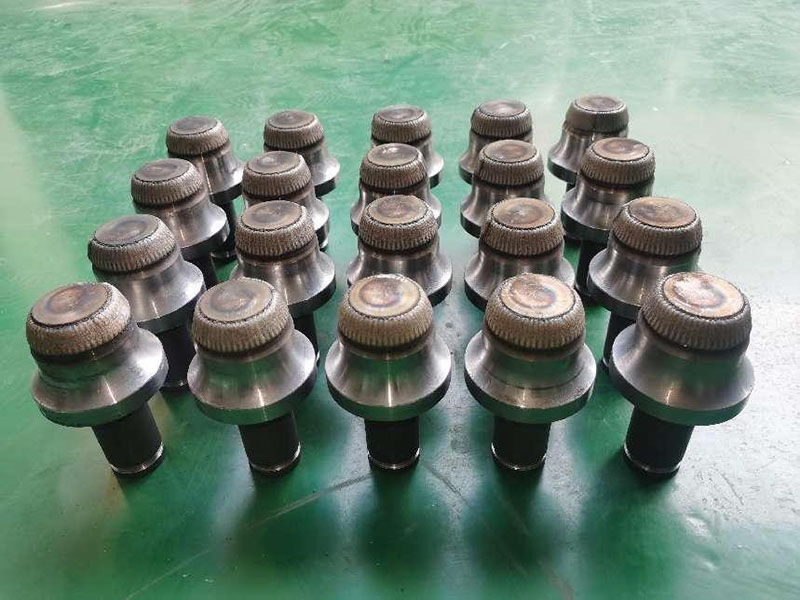
Czas publikacji: 15-08-2023