Zastosowanie technologii powlekania plazmowego w celu wzmocnienia powierzchni wierteł PDC jest skutecznym sposobem na poprawę ich odporności na zużycie, odporności na uderzenia i odporności na korozję.
1. Etap przygotowawczy
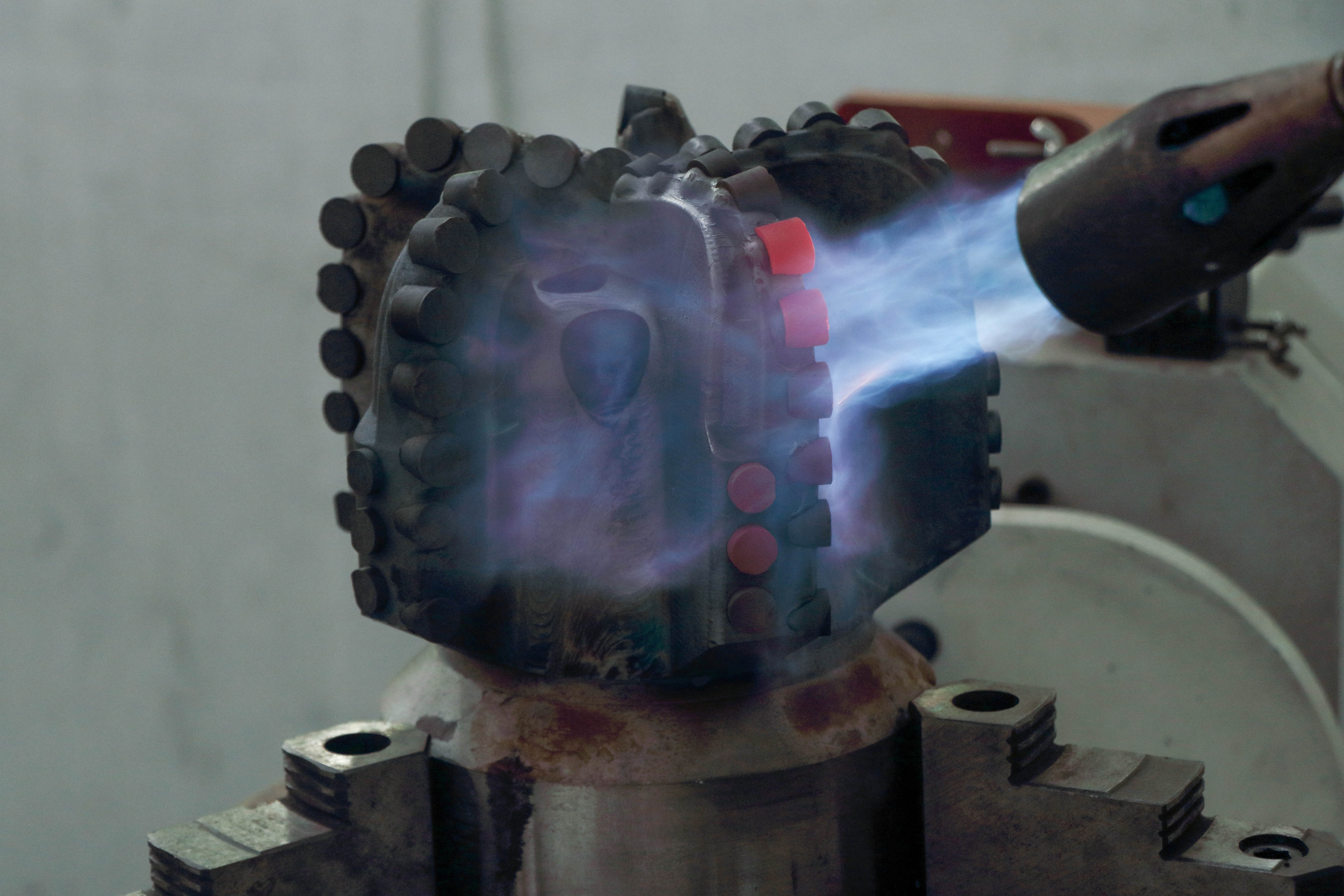
(1) Określ materiał okładziny
- Najczęściej stosowane materiały elewacyjne:
- Stop na bazie kobaltu: wysoka odporność na zużycie i korozję.
- Stop na bazie niklu: odporny na utlenianie w wysokiej temperaturze i korozję chemiczną.
- Stopy na bazie żelaza: ekonomiczne i odpowiednie do zastosowań wymagających średniej odporności na zużycie.
- Stopy wzmacniane cząstkami ceramicznymi: np. WC (węglik wolframu), TiC (węglik tytanu) itp. spełniające bardzo wysokie wymagania dotyczące odporności na zużycie.
(2) Określenie powierzchni okładziny
- Powłoka ochronna wierteł PDC jest zwykle przeznaczona do:
- Część boczna: w celu zwiększenia odporności na zużycie i zmniejszenia tarcia oraz strat podczas cięcia.
- Powierzchnia karkasu: w celu zwiększenia ogólnej odporności na korozję i uderzenia.
(3) Wstępna obróbka powierzchni
- Oczyścić obszar obudowy, aby usunąć olej, tlenki, powłoki i zanieczyszczenia.
- Obróbka mechaniczna poprzez szlifowanie lub piaskowanie w celu zwiększenia chropowatości powierzchni i polepszenia wiązania zespolonej warstwy okładzinowej z podłożem.
2. Realizacja procesu okładzinowego
(1) Ustawianie urządzeń do napawania plazmowego
- Skład wyposażenia:
Pistolet spawalniczy plazmowy, podajnik proszku, automatyczna spawarka plazmowaitp.
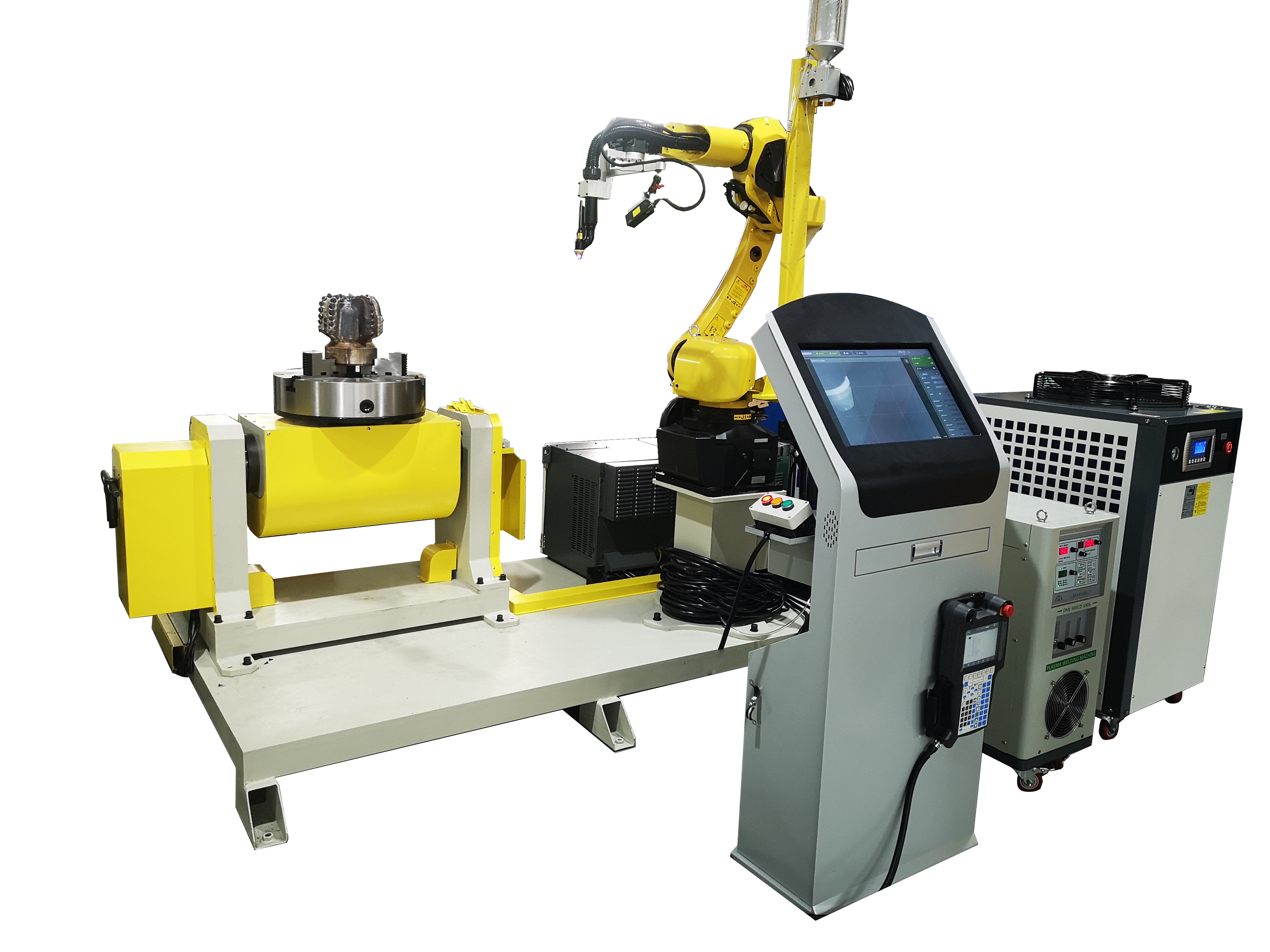
- Ustaw kluczowe parametry:
- Prąd i napięcie łuku: należy dobrać zależnie od materiału, który ma być powlekany, zwykle w zakresie 100–300 A.
- Dopływ ciepła: regulacja w celu kontrolowania odkształcenia podłoża i szybkości rozcieńczania.
- Szybkość podawania proszku: zwykle w zakresie 10~50 g/min, aby zapewnić jednorodność warstwy okładzinowej.
(2) Wykonanie obudowy
- Proces powlekania:
1. Zapłon łuku plazmowego, utworzenie jeziorka topionego w wysokiej temperaturze.
2. Za pomocą układu podawania proszku, materiał proszkowy jest rozpylany do stopionego metalu i wiązany metalurgicznie z podłożem.
3. zgodnie z kształtem wiertła, wzdłuż wyznaczonej ścieżki, aby zapewnić równomierne pokrycie, zapobiegając wyciekom pokrycia lub jego nadmiernemu stopieniu.
- Kontrola wpływu temperatury: zapobieganie przegrzaniu lub odkształceniu podłoża wiertła PDC poprzez dostosowanie parametrów łuku plazmowego i metody chłodzenia.
(3) Leczenie chłodzące
- Naturalne chłodzenie lub zastosowanie metody kontrolowanego chłodzenia, aby uniknąć pęknięć spowodowanych naprężeniami termicznymi.
3. Etap po leczeniu
(1) Kontrola jakości okładzin
- Kontrola wyglądu: należy sprawdzić, czy warstwa okładziny jest jednolita, wolna od pęknięć i dziur powietrznych.
- Testowanie wydajności: pomiar twardości, grubości (zwykle w zakresie 0,5 ~ 3 mm), wytrzymałości wiązania i innych wskaźników.
- Badania nieniszczące: Do wykrywania usterek wewnętrznych stosuje się badania ultradźwiękowe lub rentgenowskie.
(2) Wykończenie
- Jeśli powierzchnia po nałożeniu spoiny jest szorstka, konieczne jest toczenie lub szlifowanie, aby spełnić wymagania dotyczące rozmiaru i kształtu wierteł PDC.
(3) Optymalizacja wydajności
- Obróbka cieplna: w razie konieczności hartowanie lub odpuszczanie stopionej warstwy okładzinowej w celu dalszej optymalizacji jej właściwości organizacyjnych.
4. Środki ostrożności
1. Unikaj uszkodzeń spowodowanych przegrzaniem
- Podczas napawania plazmowego należy ściśle kontrolować ilość wprowadzanego ciepła, aby uniknąć uszkodzeń termicznych wkładki PDC i podłoża.
2. Dopasowanie materiałów
- Materiał powłoki powinien być dobrany do materiału podłoża wiertła PDC, aby zapewnić wytrzymałość połączenia i spójność działania.
3. Kontrola środowiska
- W miarę możliwości w środowisku o niskiej wilgotności lub w atmosferze gazu ochronnego, aby uniknąć utleniania, które mogłoby wpłynąć na jakość okładziny.
Proces ten można stosować zarówno do poprawy wydajności nowych bitów PDC, jak i do naprawy bitów zużytych.
Czas publikacji: 09-01-2025