1.1 Strāvas ietekme uz formēšanuapšuvuma slānis
Pašreizējais()A) | Depth (saplūšanas)()mm) | Fgrīdas augstums()mm) | platums()mm) |
70 | 0,19 | 4.26 | 16.41 |
80 | 0,35 | 4.07 | 17.08 |
90 | 0,88 | 3.43 | 17.48 |
100 | 1.03 | 2.73 | 17.58 |
110 | 1.25 | 2.65 | 18.14 |
3.1. tabula. Apšuvuma slāņa šķērsgriezuma ģeometrija ar dažādām strāvām.
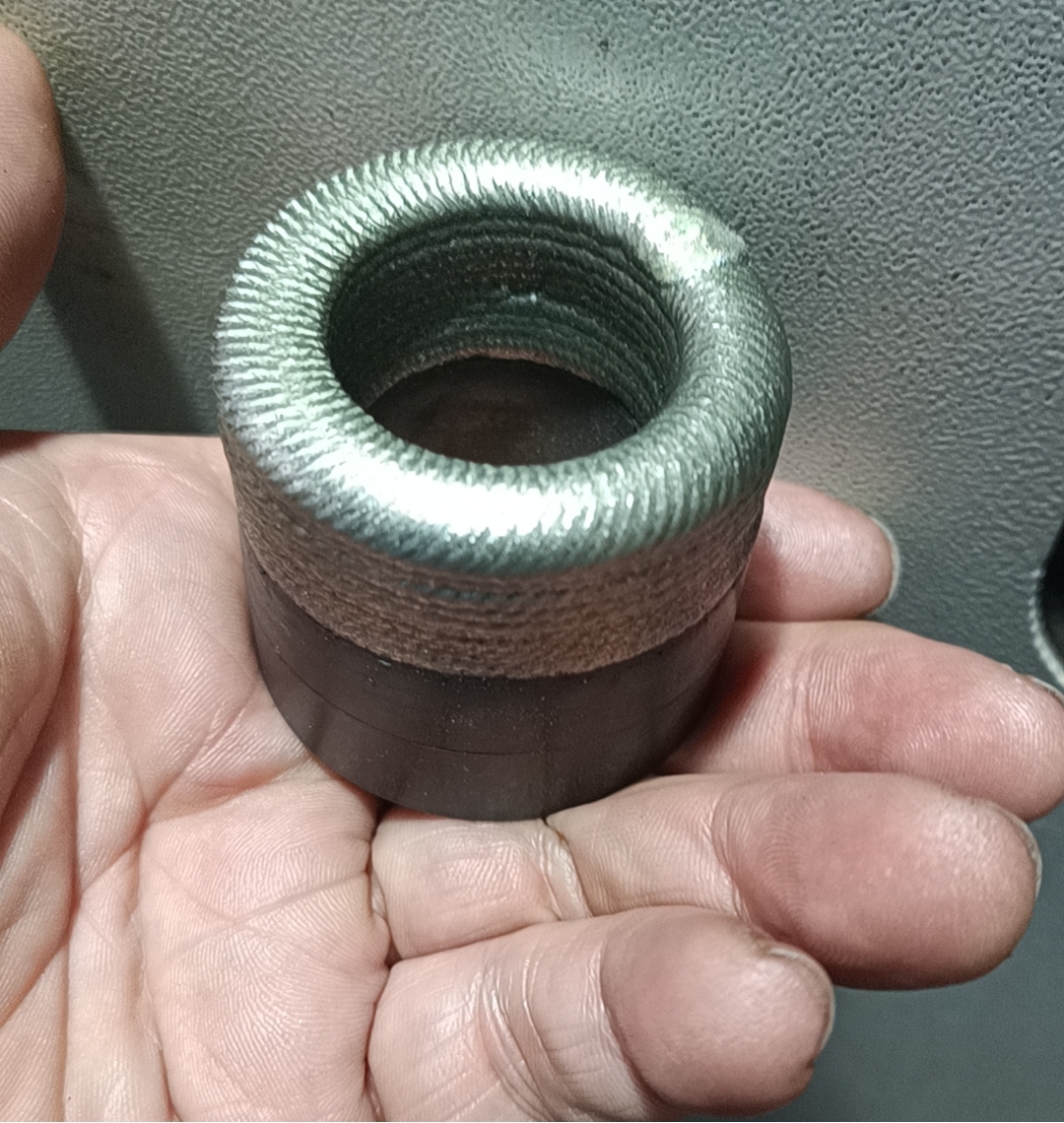
Palielinoties strāvai, palielinās apšuvuma slāņa dziļums un platums, un samazinās slāņa augstums. Tas ir saistīts ar strāvas palielināšanos, un radītais siltums ne tikai izkausēs apšuvuma metālu, bet arī daļu substrāta, notiks apšuvuma un substrāta sajaukšanās, kā rezultātā apšuvuma slānis kopumā iegrims, kā rezultātā palielinās kušanas dziļums un samazinās slāņa augstums; un, palielinoties strāvai, plazmas loks kļūs rupjāks, palielinās siltuma avota temperatūras diapazons, un izkausētās vannas izplatīšanās substrātā būs spēcīgāka, tāpēc izkausētās vannas platums palielinās.
1.2 Ietekmemetināšanaātrums izkausētā apšuvuma slāņa formēšanā
Metināšanas ātrums()mm/s) | Depth (saplūšanas)()mm) | Fgrīdas augstums()mm) | platums()mm) |
4 | 1.17 | 4.34 | 17.61 |
5 | 1.06 | 2.73 | 17.58 |
6 | 0,35 | 2.61 | 16,96 |
7 | 0,13 | 2.55 | 15.01 |
8 | — | — | — |
3.2. tabula. Izkausētu apšuvuma slāņu šķērsgriezuma ģeometrija ar dažādiem metināšanas ātrumiem.
Palielinoties metināšanas ātrumam, apšuvuma slāņa kušanas dziļums samazinās, slāņa augstums vispirms strauji samazinās un pēc tam lēnām samazinās, platums samazinās. Kad metināšanas ātrums ir 4 mm/s, apšuvuma metāla biezumam zināmā mērā palielinoties, kušanas dziļums sasniedz 1,17 mm, šajā laikā siltuma padeve uz garuma vienību nevar likt pamatmateriālam tālāk izkust, kausētais apšuvuma slānis turpina uzkrāties līdz 4,34 mm augstumam; metināšanas ātrumam palielinoties līdz 5 mm/s, siltuma padeve uz garuma vienību samazinās, stieples padeves daudzums samazinās, līdz ar to samazinās kausēšanas dziļums, slāņa augstums un platums; ja metināšanas ātrums turpina palielināties, kā minēts iepriekš, siltuma padeve šajā laikā nav pietiekama, var izkust tikai neliela daļa pamatmateriāla, kausētā apšuvuma slāņa augstums vispirms strauji samazinās un pēc tam lēnām samazinās, platums samazinās. Ja metināšanas ātrums turpina palielināties, kā minēts iepriekš, siltuma padeve šajā laikā ir nepietiekama, var izkausēt tikai nelielu daļu no pamatmateriāla, kausēšanas apšuvuma slānis nešķiet noslīdējis, kā rezultātā kausēšanas dziļums samazinās vairāk, savukārt slāņa augstums samazinās mazāk.
1.3 Stieples padeves ātruma ietekme uz apšuvuma slāņa formēšanu
Stieples padeves ātrums()mm/s) | Depth (saplūšanas)()mm) | Fgrīdas augstums()mm) | platums()mm) |
40 | 1.43 | 2.24 | 19,91 |
50 | 1.25 | 2.56 | 18,86 |
60 | 1.03 | 2.73 | 17.58 |
70 | 0,71 | 3.46 | 15.82 |
80 | 0,16 | 5.16 | 14.20 |
3.3. tabula. Apšuvuma slāņa šķērsgriezuma ģeometriskie izmēri ar dažādiem stieples padeves ātrumiem.
Palielinoties stieples padeves ātrumam, samazinās apšuvuma slāņa dziļums un platums, un palielinās slāņa augstums. Tas ir saistīts ar faktu, ka, palielinoties strāvai un metināšanas ātrumam, siltuma padeve uz garuma vienību ir noteikta, un, palielinoties stieples padeves ātrumam, palielinās pildvielas stieples daudzums uz garuma vienību, un apšuvuma metālam ir jāabsorbē vairāk siltuma, un, ja siltuma padeve nespēj pilnībā izkausēt visu apšuvuma slāni, pamatmateriāla daļa ir mazāk izkususi, tāpēc kušanas dziļums samazinās, un slāņa augstums palielinās, un apšuvuma metāla izkliedes spēja pamatmateriāla daļas tuvumā pasliktinās, tāpēc platums strauji samazinās. Platums strauji samazināsies.
Rezumējot, plazmas loka apšuvuma 2205 dupleksa nerūsējošā tērauda slāņa efektīvie procesa parametri ir no: strāva 90 A ~ 110 A, metināšanas ātrums 4 mm/s ~ 6 mm/s, stieples padeves ātrums 50 mm/s ~ 70 mm/s, jonu gāzes plūsmas ātrums 1,5 L/min.
2. Balstoties uz atbildes virsmas metodi, apšuvuma slāņa veidošanas procesa parametru optimizācija
Atbildes virsmas metode (Reakcijas virsmas metode, RSM) ir eksperimentālās projektēšanas un statistisko optimizācijas metožu kombinācija, testa datu analīze, ko var iegūt no trieciena faktora un atbildes vērtības pielāgošanas funkcijas un trīsdimensiju virsmas kartes, var intuitīvi atspoguļot ietekmes faktora un atbildes vērtības attiecību starp faktisko testu, kam ir paredzoša, optimizācijas loma. Pamatojoties uz iepriekš minētajiem iemesliem, RSM izvēle centrālā kompozītmateriāla projektēšanā (Centrālā kompozītmateriāla projektēšana, CCD), lai izstrādātu procesa optimizācijas programmu, izpētītu strāvas, metināšanas ātruma, stieples padeves ātruma un kausēšanas apšuvuma slāņa atšķaidīšanas ātruma attiecību, kā arī matemātisku modelēšanu, kas iegūta no procesa parametriem un atšķaidīšanas ātruma, malu attiecības funkcijas, lai sasniegtu kausēšanas apšuvuma slāņa kvalitātes prognozi.
2.1 Procesa parametru ietekme uz apšuvuma slāņa atšķaidīšanas ātrumu.
3.8. tabula. Procesa optimizācijas rezultāti un pārbaude
Grupa | X1()A) | X2()mm·s-1) | X3()mm·s-1) | atšķaidīšanas attiecība()%) | malu attiecība |
Prognozēšanas grupa | 99 | 6 | 50 | 14.8 | 4.36 |
1. testa grupa | 99 | 6 | 50 | 13.9 | 4.13 |
2. testa grupa | 99 | 6 | 50 | 15,5 | 4.56 |
3. testa grupa | 99 | 6 | 50 | 14.3 | 4.27 |
Vidējā kļūda | 2.9 | 2.3 |
(PTA metināšana, ko veic Šanhajas Duomu)
3.16. attēls. Optimālo procesa parametru testa rezultāti. (a) 1. testa grupa; (b) 2. testa grupa; (c) 3. testa grupa.
Augstas kvalitātes apšuvuma slānim ir nepieciešams mazs atšķaidīšanas ātrums un liela malu attiecība. Optimālie procesa parametri ir: strāva 99 A, metināšanas ātrums 6 mm-s-1, stieples padeves ātrums 50 mm-s-1. Optimālajā procesā sagatavotā apšuvuma slāņa vidējais atšķaidīšanas ātrums ir aptuveni 14,6%, vidējā malu attiecība ir 4,33, un vidējā kļūda starp modeļa prognozēšanas vērtību un eksperimentālo vērtību ir mazāka par 5%, kas norāda, ka modelim ir augsta precizitātes pakāpe un optimālajā procesā izveidotā apšuvuma slāņa kvalitāte ir laba.
Publicēšanas laiks: 2024. gada 31. janvāris