Cietā pārklāšana ir metode, kurā uz metāla virsmas ar metināšanas, termiskās izsmidzināšanas vai citiem procesiem uzklāj nodilumizturīga, korozijizturīga vai augstas stiprības materiāla slāni, ko galvenokārt izmanto, lai uzlabotu iekārtu un mehānisko detaļu nodilumizturību, triecienizturību un korozijizturību, lai pagarinātu to kalpošanas laiku.
Cietās metināšanas metodes
Metināšanas pārklājums
Apšuvums ir visizplatītākā cietās pārklāšanas metode, izmantojot tādas metodes kā metināšanas stieņus,loka metināšana,TIG, MIG or plazmas metināšanalai piekausētu nodilumizturīgus materiālus pamatmateriāla virsmai.
•Bieži izmantotās metodes
Manuālā loka metināšana (SMAW)Piemērots nelieliem un vidējiem remontdarbiem, zemas izmaksas.
Gāzes aizsargloka metināšana (MIG/MAG/GMAW)Piemērots nepārtrauktai metināšanai, ātrs metināšanas ātrums.
Volframa argona loka metināšana (TIG/GTAW):piemērots smalkām sagatavēm ar labu kontroli.
Plazmas pārneses loka metināšana (PTA)Piemērots augstas cietības materiāliem, augstas precizitātes metināšanai.
•Piemērojamie materiāli
Kobalta sakausējumi (piemēram, stellīts)
Niķeļa sakausējumi (piemēram, NiCrMo)
Dzelzs sakausējumi (piemēram, čuguns ar augstu hroma saturu)
Volframa karbīda kompozītmateriāli
Termiskā izsmidzināšana
Liesmas vai plazmas izsmidzināšanas izmantošana pulveru vai stiepļu kausēšanai un izsmidzināšanai uz substrāta virsmas, lai izveidotu mehāniski saistītu nodilumizturīgu slāni.
•Veidi
Liesmas izsmidzināšana
Plazmas izsmidzināšana (APS)
Augsta ātruma skābekļa degvielas izsmidzināšana (HVOF)
•Priekšrocības
Piemērots lielu platību uzlabošanai
Zema deformācija, piemērota plānsienu sagatavēm
Lāzera apšuvums
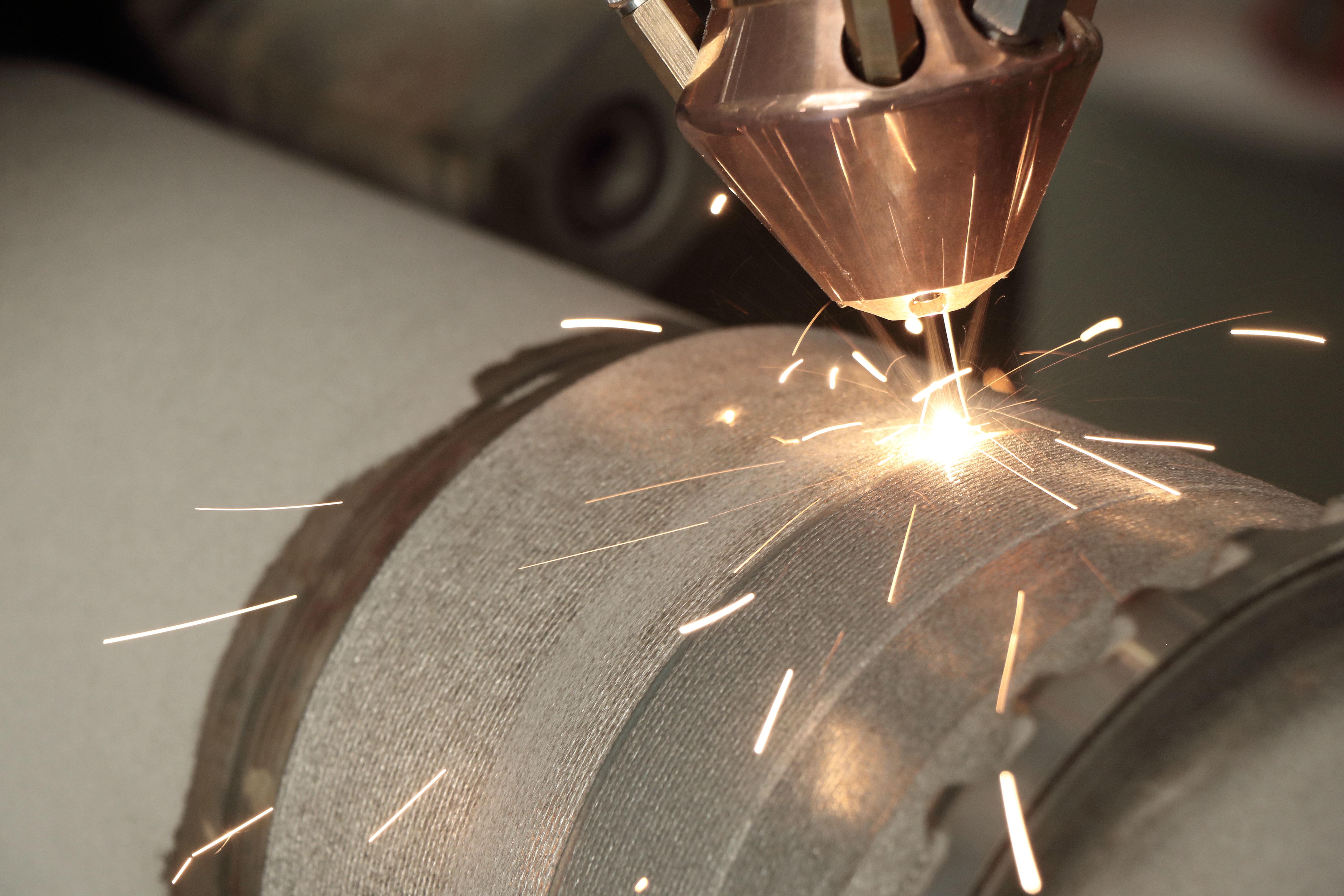
Lāzera apšuvumsizmanto augstas enerģijas lāzera staru, lai izkausētu un uzklātu sakausējuma pulveri uz substrāta virsmas, veidojot augstas veiktspējas pārklājumu.
•Funkcijas
Precīza atšķaidīšanas ātruma kontrole
Piemērots augstas klases detaļām (piemēram, veidnēm, turbīnu lāpstiņām)
Kādas ir cieto pārklājumu metināšanas priekšrocības?
•Paaugstināta nodilumizturība: piemērota darba apstākļiem ar augstu nodilumizturību, pagarinot iekārtu kalpošanas laiku.
•Uzlabojiet izturību pret koroziju: piemērots ķīmiskajai un jūras videi, uzlabojot izturību pret koroziju.
•Samazina apkopes izmaksas: samazina iekārtu nomaiņas biežumu un uzlabo produktivitāti.
•Piemērots remontam un atjaunošanai: var izmantot nolietotu detaļu remontam, samazinot materiālu atkritumus.
Cietās metināšanas pielietojuma gadījumi
1. Kalnrūpniecības tehnika
•Problēma: Drupinātāja āmura galva, kausa zobi utt. ir pakļauti ilgstošam nodilumam un īsam kalpošanas laikam.
•Risinājums: Izmantojiet augsta hroma čuguna vai volframa karbīda cieto pārklāšanas metināšanu, lai 2–5 reizes palielinātu nodilumizturību.
2. Naftas ķīmija
•Problēma: Vārsta blīvējuma virsmu ietekmē korozija un augsta temperatūra.
•Risinājums: Lai uzlabotu izturību pret koroziju, izmantojiet uz kobalta bāzes veidotu sakausējumu (piemēram, Stellite 6) pārklājuma metināšanu.
3. Metalurģijas iekārtas
•Problēma: Ruļļu virsmas bija nodilušas, ietekmējot izstrādājuma precizitāti.
•Risinājums: Izmantojiet plazmas pārneses loka (PTA) metināšanu, lai uzlabotu nodilumizturību un pagarinātu kalpošanas laiku.
Cietās virsmas metināšana ir svarīgs process, lai uzlabotu sagataves nodilumizturību un korozijas izturību, ko plaši izmantoražošana un remontsiekārtām, kurām ir augsts nodiluma līmenis. Attīstoties automatizācijai un intelektuālajai metināšanas tehnoloģijai, cieto pārklāšanas metināšanai būs arvien lielāka nozīme rūpniecības jomā, nodrošinot iekārtu ilgstošas darbības garantiju.
Publicēšanas laiks: 2025. gada 5. marts