1.1 전류의 성형에 미치는 영향클래딩 레이어
현재의(A둔다 | DEPTH (퓨전)(mm둔다 | FLOOR 높이(mm둔다 | 너비(mm둔다 |
70 | 0.19 | 4.26 | 16.41 |
80 | 0.35 | 4.07 | 17.08 |
90 | 0.88 | 3.43 | 17.48 |
100 | 1.03 | 2.73 | 17.58 |
110 | 1.25 | 2.65 | 18.14 |
표 3.1 전류가 다른 클래딩 층의 단면 구조
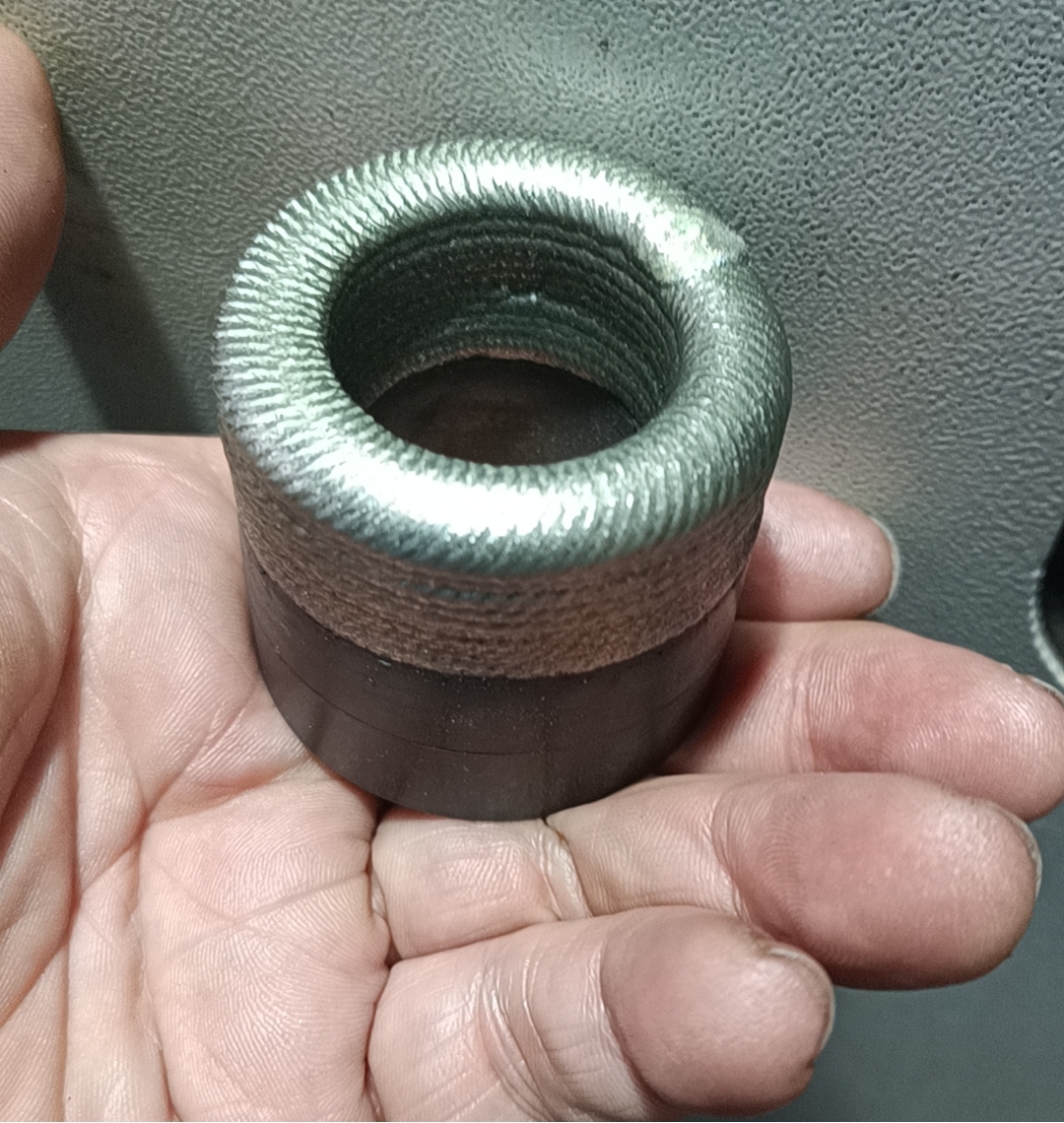
전류가 증가함에 따라 클래딩 층의 깊이와 폭이 증가하고 층 높이가 감소합니다. 이는 전류의 증가로 인해 생성 된 열은 클래딩 금속을 녹일뿐만 아니라 기질 용융, 클래딩 및 기판 혼합의 일부를 녹일 것이므로, 클래딩 층이 전체 침강으로서 융합의 깊이, 층 높이가 감소한다; 전류를 증가시켜 혈장 아크를 더 거칠게 만들고, 열원의 온도 범위를 증가시키고, 기판 스프레드 능력의 용융 풀이 더 강하므로 용융 풀의 폭이 증가합니다.
1.2의 효과용접용융 클래딩 층의 성형 속도
용접 속도(mm/s둔다 | DEPTH (퓨전)(mm둔다 | FLOOR 높이(mm둔다 | 너비(mm둔다 |
4 | 1.17 | 4.34 | 17.61 |
5 | 1.06 | 2.73 | 17.58 |
6 | 0.35 | 2.61 | 16.96 |
7 | 0.13 | 2.55 | 15.01 |
8 | - | - | - |
표 3.2 용접 속도가 다른 용융 클래딩 층의 단면 형상
용접 속도가 증가하면 클래딩 층의 융합 깊이가 감소하고, 층 높이는 먼저 급격히 감소한 다음 천천히 작아지면 너비가 감소합니다. 용접 속도가 4mm/s 인 경우 클래딩 금속이 어느 정도 증가함에 따라 융합 깊이는 1.17mm이며,이 시점에서는 단위 길이 당 열 입력이 기본 재료를 추가 용해시킬 수 없으며, 융합 클래딩 층은 4.34 mm의 층 높이의 높이를 쌓아 올릴 수 없습니다. 용접 속도는 5 mm/s로 증가하고, 단위 길이 당 열 입력, 와이어 공급량의 양이 감소하므로 융합 깊이, 층 높이, 폭이 줄어 듭니다. 위에서 언급 한 바와 같이, 용접 속도가 계속 증가하면,이 시점에서 열 입력이 불충분하면, 기본 재료의 작은 부분 만 녹을 수 있고, 융합 클래딩 층 높이는 먼저 급격한 감소를 나타내고 천천히 더 작아지면 너비가 줄어 듭니다. 용접 속도가 계속 증가하면, 위에서 언급 한 바와 같이,이 시점의 열 입력이 충분하지 않으면, 기본 재료의 작은 부분 만 녹을 수 있으며, 융합 클래딩 층은 처지는 것처럼 보이지 않아 융합 깊이가 더 크게 감소하는 반면, 층 높이는 감소합니다.
1.3 클래딩 층의 성형에 대한 와이어 공급 속도의 영향
와이어 피드 스핑(mm/s둔다 | DEPTH (퓨전)(mm둔다 | FLOOR 높이(mm둔다 | 너비(mm둔다 |
40 | 1.43 | 2.24 | 19.91 |
50 | 1.25 | 2.56 | 18.86 |
60 | 1.03 | 2.73 | 17.58 |
70 | 0.71 | 3.46 | 15.82 |
80 | 0.16 | 5.16 | 14.20 |
표 3.3 와이어 공급 속도가 다른 클래딩 층의 단면의 기하학적 치수.
와이어 공급 속도가 증가함에 따라 클래딩 층의 깊이와 폭이 감소하고 층 높이가 증가합니다. 이는 전류 및 용접 속도가 확실 할 때 단위 길이 당 열 입력이 확실하고, 와이어 공급 속도의 증가로 인해 단위 길이 당 필러 와이어의 양이 증가하고 클래딩 금속이 더 많은 열을 흡수해야한다는 사실 때문에, 열 입력이 전체 클래딩 층을 완전히 녹일 수 없을 때, 기본 재료 부품이 감소 할 수 없기 때문에, 깊이가 감소 할 수없고, 깊이가 감소 할 수없고, 높이가 증가하고, 높이가 증가하고, 높이가 증가하고, 높이가 증가하고 기본 재료 부분에 가깝게 클래딩 금속의 금속이 악화되므로 폭이 빠르게 감소합니다. 너비는 빠르게 감소합니다.
요약하면, 혈장 아크 클래딩 2205 이중 스테인리스 스틸 레이어 유효 공정 파라미터는 현재 90 a ~ 110 a, 용접 속도 4 mm / s ~ 6 mm / s, 와이어 공급 속도 50 mm / s ~ 70 mm / s, 이온 가스 유속 1.5 L / 분입니다.
2 융합 클래딩 층 형성 프로세스 매개 변수 최적화의 응답 표면 방법에 기초합니다.
응답 표면 방법 (응답 표면 방법, RSM)은 실험 설계 및 최적화 방법의 통계 기술의 조합이며, 테스트 데이터의 분석은 피팅 기능 및 3 차원 표면 맵의 영향 요인 및 3 차원 표면 맵의 응답 값에서 도출 될 수 있으며, 실제 시험 간의 응답 값은 예측, 최적화 역할을 직관적으로 반영 할 수 있습니다. 위의 이유에 기초하여, 중앙 복합 설계 (중앙 복합 설계, CCD)에서 RSM을 공정 최적화 프로그램을 개발하여 전류, 용접 속도, 와이어 공급 속도 및 퓨전 클래딩 속도 및 퓨전 클래딩 층 희석 속도, 융합 속도, 와이어 공급 속도 및 융합 속도 및 융합 속도의 종횡비, 및 수학적 모델링, 유도, 수학적 모델링, 유도체, 유도체, 유도체, 유도체, 유도체, 그리고 수학적 모델링, 및 수학적 모델링, 및 수학적 모델링, 및 수학적 모델링, 및 수학적 모델링, 및 수학적 모델링, 및 수학적 모델링, 그리고 수학적 모델링, 및 수학적 모델링, 및 수학. 융합 클래딩 층 품질의 예측을 달성하기위한 함수의 비율.
2.1 클래딩 층의 희석 속도에 대한 공정 파라미터의 영향.
표 3.8 프로세스 최적화 결과 및 검증
그룹 | X1(A둔다 | X2(mm · s-1둔다 | X3(mm · s-1둔다 | 희석 비율(%둔다 | 종횡비 |
예측 그룹 | 99 | 6 | 50 | 14.8 | 4.36 |
테스트 그룹 1 | 99 | 6 | 50 | 13.9 | 4.13 |
테스트 그룹 2 | 99 | 6 | 50 | 15.5 | 4.56 |
테스트 그룹 3 | 99 | 6 | 50 | 14.3 | 4.27 |
평균 오류 | 2.9 | 2.3 |
(상하이 Duomu의 PTA 용접)
그림 3.16 최적의 프로세스 매개 변수 테스트 결과 (a) 테스트 그룹 1; (b) 시험 그룹 2; (c) 시험 그룹 3
고품질 클래딩 층은 작은 희석률과 큰 종횡비를 갖기를 추구합니다. 최적의 공정 파라미터는 다음과 같습니다. 현재 99A, 용접 속도 6 mm-S-1, 와이어 공급 속도 50 mm-S-1. 최적 공정에서 제조 된 클래딩 층의 평균 희석률은 약 14.6%이고 평균 종횡비는 4.33이며, 모델 예측 값과 실험 값 사이의 평균 오차는 5%미만이며, 이는 모델이 정확도가 높고 최적 프로세스 하에서 형성된 클래딩 레이어의 품질이 좋음을 나타냅니다.
후 시간 : 1 월 31-2024