PDC 드릴 비트의 표면을 강화하기 위해 플라즈마 클래딩 기술을 사용하는 것은 내마모성, 내충격성 및 내부식성을 개선하는 효과적인 수단입니다.
1. 준비 단계
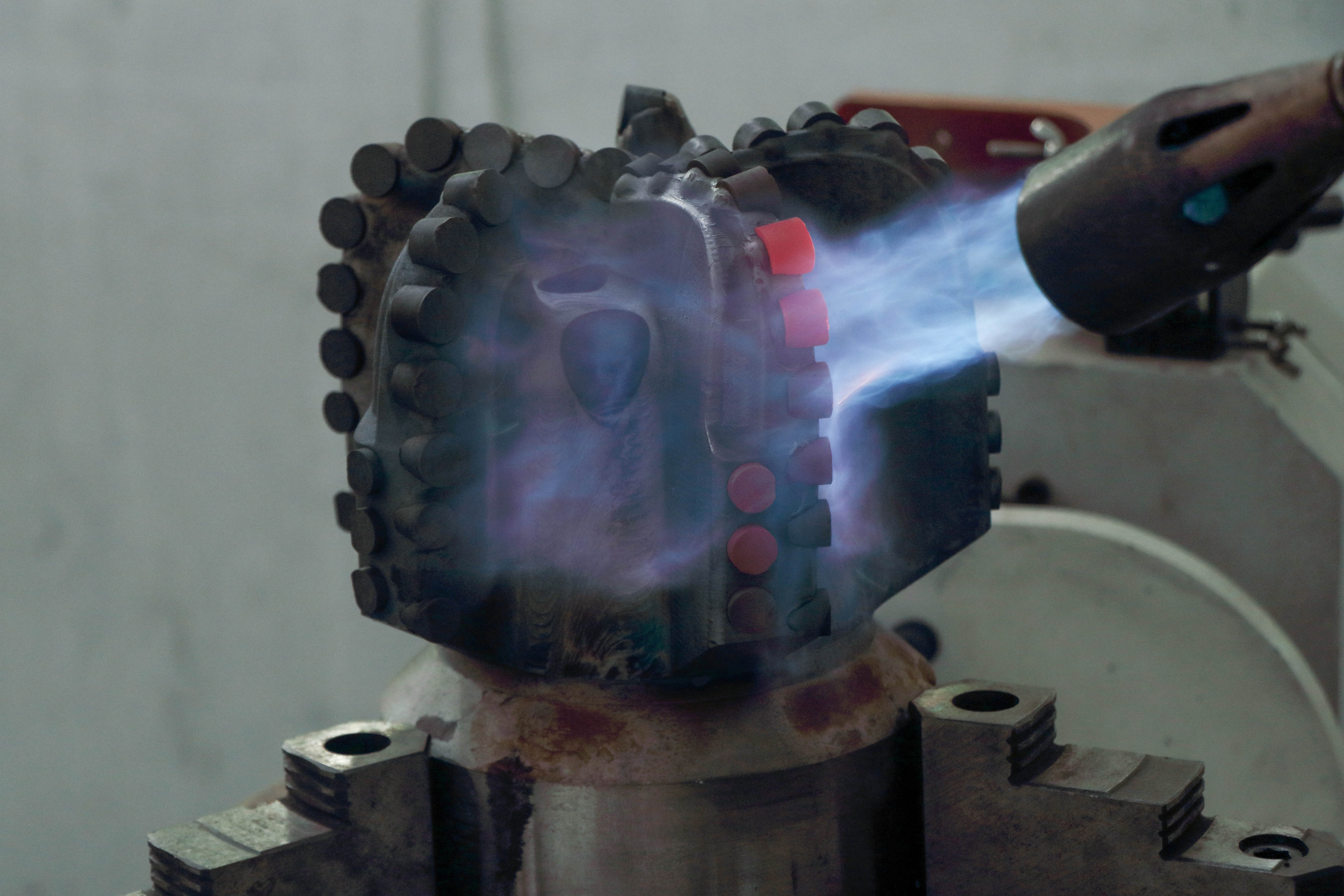
(1) 클래딩 재료 결정
- 일반적으로 사용되는 클래딩 재료:
- 코발트계 합금 : 내마모성과 내부식성이 우수합니다.
- 니켈 기반 합금: 고온 산화 및 화학적 부식에 강함.
- 철 기반 합금: 비용 효율적이며 중간 정도의 내마모성 요구 사항에 적합합니다.
- 세라믹 입자 강화 합금: 예를 들어 WC(텅스텐 카바이드), TiC(티타늄 카바이드) 등은 매우 높은 내마모성이 요구됩니다.
(2) 클래딩 면적의 결정
- PDC 드릴 비트의 퓨전 클래딩은 일반적으로 다음을 대상으로 합니다.
- 플랭크 부분 : 내마모성을 높이고 마찰과 절삭 손실을 줄입니다.
- 몸체 표면: 전반적인 부식 및 충격 저항성을 강화합니다.
(3) 표면 전처리
- 클래딩 부분을 청소하여 오일, 산화물, 코팅 및 불순물을 제거합니다.
- 표면 거칠기를 높이고 융합된 클래딩 층과 기판의 결합력을 개선하기 위한 기계적 연삭 또는 사포 분사 처리.
2. 클래딩 공정 구현
(1) 플라즈마 클래딩 장비 설치
- 장비 구성 :
플라즈마 용접 건, 분말 공급기, 자동 플라즈마 용접기, 등..
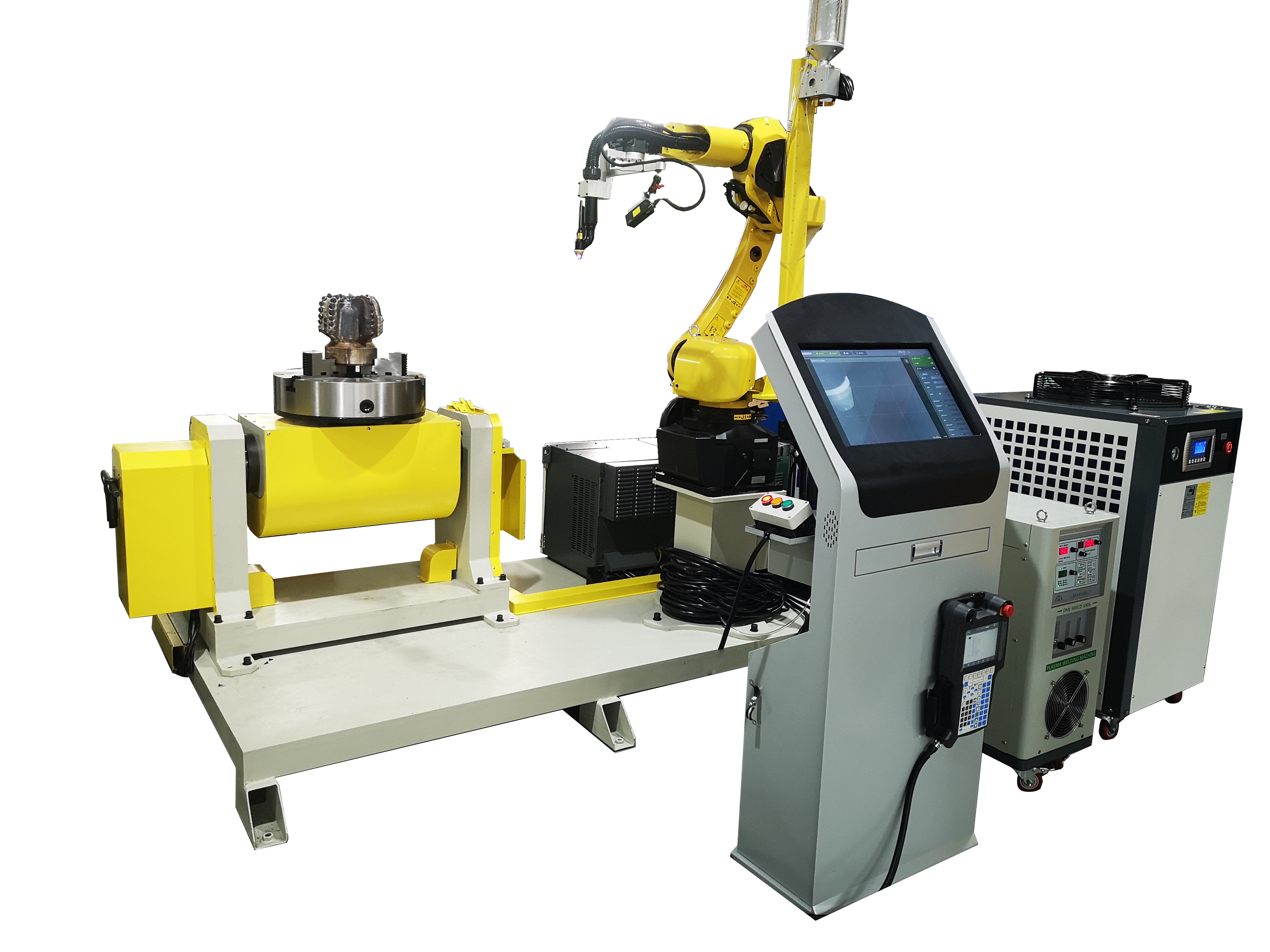
- 주요 매개변수를 설정합니다.
- 아크 전류 및 전압: 코팅할 재료에 따라 선택하며, 일반적으로 100~300A 범위입니다.
- 열 입력: 기판 변형 및 희석률을 제어하도록 조정합니다.
- 분말 공급 속도: 일반적으로 클래딩 층의 균일성을 보장하기 위해 10~50g/min 범위입니다.
(2) 클래딩 시공
- 클래딩 공정:
1. 플라스마 아크 시작, 고온 용융 풀 형성.
2. 분말 공급 시스템을 통해 분말 재료가 용융 풀에 분사되어 기질과 금속적으로 결합됩니다.
3. 드릴 비트 모양에 따라, 균일한 클래딩을 위한 설정된 경로를 따라 클래딩 누출이나 과도한 용융이 없는지 확인합니다.
- 열 영향 제어: 플라즈마 아크 매개변수와 냉각 방법을 조정하여 PDC 드릴 비트 기판의 과열이나 변형을 방지합니다.
(3) 냉각처리
- 열응력으로 인한 균열을 방지하기 위해 자연냉각이나 속도제어냉각 방식을 채택합니다.
3. 치료 후 단계
(1) 클래딩 품질 검사
- 외관 검사: 클래딩 층이 균일하고 균열이나 기포가 없는지 관찰합니다.
- 성능 테스트: 경도, 두께(일반적으로 0.5~3mm), 접합 강도 및 기타 지표를 측정합니다.
- 비파괴 검사: 초음파나 X선 검사를 이용해 내부 결함을 해결합니다.
(2) 마무리
- 퓨전 클래딩 후 표면이 거친 경우 PDC 드릴 비트의 크기 및 모양 요구 사항을 충족시키기 위해 선삭 또는 연삭 처리가 필요합니다.
(3) 성능 최적화
- 열처리: 필요한 경우 융합된 클래딩 층을 담금질하거나 템퍼링하여 조직적 특성을 더욱 최적화합니다.
4. 주의사항
1. 과열로 인한 손상을 방지하세요
- 플라즈마 클래딩 작업 중에는 PDC 인서트와 기판의 열 손상을 방지하기 위해 열 입력을 엄격하게 제어해야 합니다.
2. 재료 매칭
- 클래딩 재료는 접합 강도와 성능 일관성을 보장하기 위해 PDC 비트 기판의 재료와 일치해야 합니다.
3. 환경 관리
- 클래딩의 품질에 영향을 미치는 산화를 피하기 위해 가능한 한 습도가 낮은 환경이나 보호 가스 환경에서 작업합니다.
이 프로세스는 새로운 PDC 비트의 성능을 향상시키고 마모된 비트를 수리하는 데 사용할 수 있습니다.
게시 시간: 2025년 1월 9일