レーザークラッディングと溶接は、原理、用途、目的が大きく異なる2つの異なる材料加工技術です。この記事では、溶接とクラッディングの原理、材料、用途、入熱の影響、そして加工方法について解説します。主な違いは以下のとおりです。
原則と目的
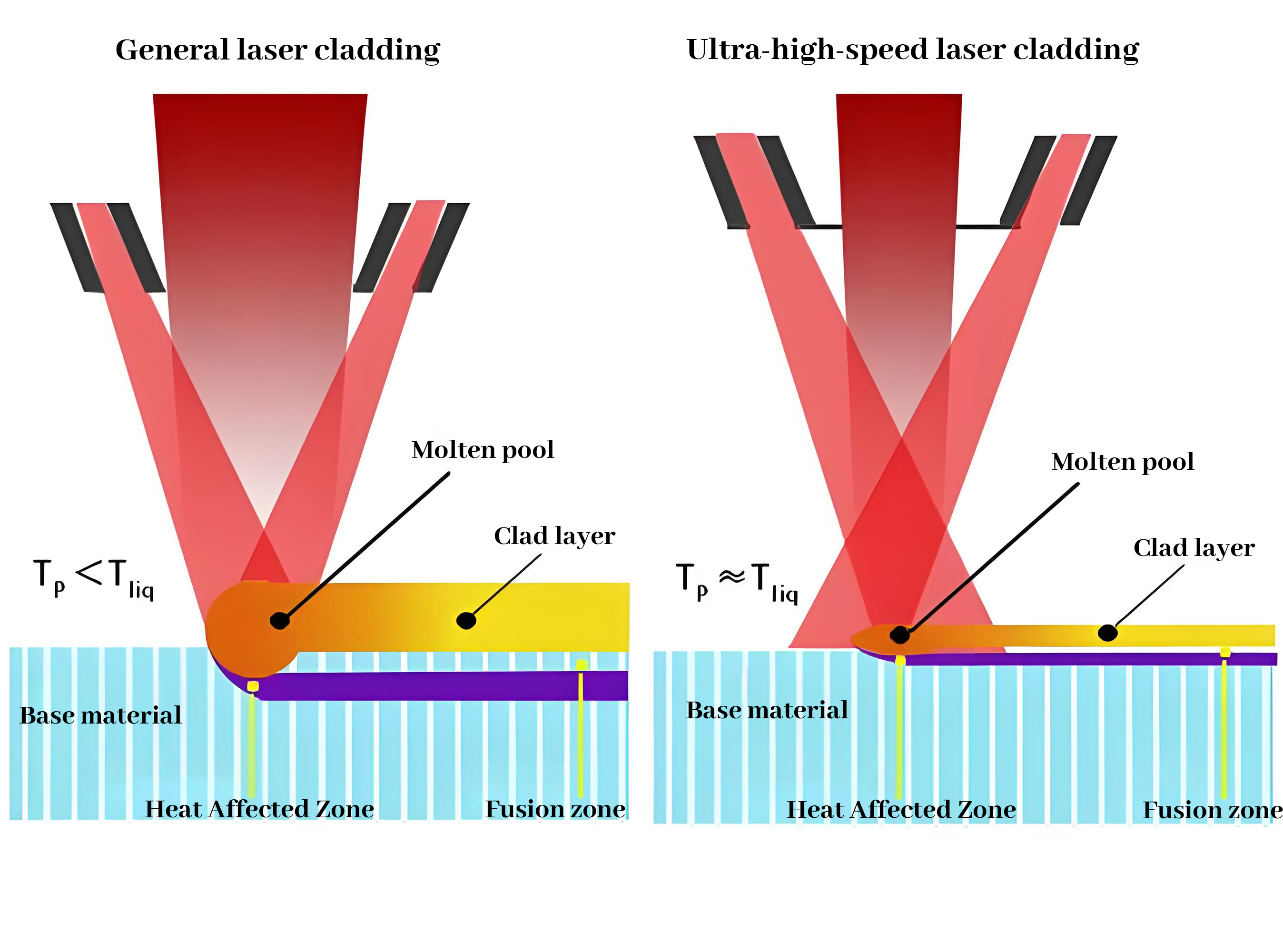
-レーザークラッディング:
- レーザークラッディングは、高エネルギーレーザービームを用いてコーティング材料を溶融し、基材の表面に融合させる表面改質技術です。主な目的は、基材の表面に特殊な特性(耐摩耗性、耐腐食性など)を有するコーティング層を形成し、材料の表面特性を向上させることです。
- クラッディングプロセスでは、コーティング材料(通常は粉末またはフィラメント)がレーザービームによって溶融され、同時に基材の表面の小さな部分も溶融され、コーティングと基材の間に冶金結合が形成されます。
- 主な目的: 材料の表面を強化または修復し、表面特性を向上させること。
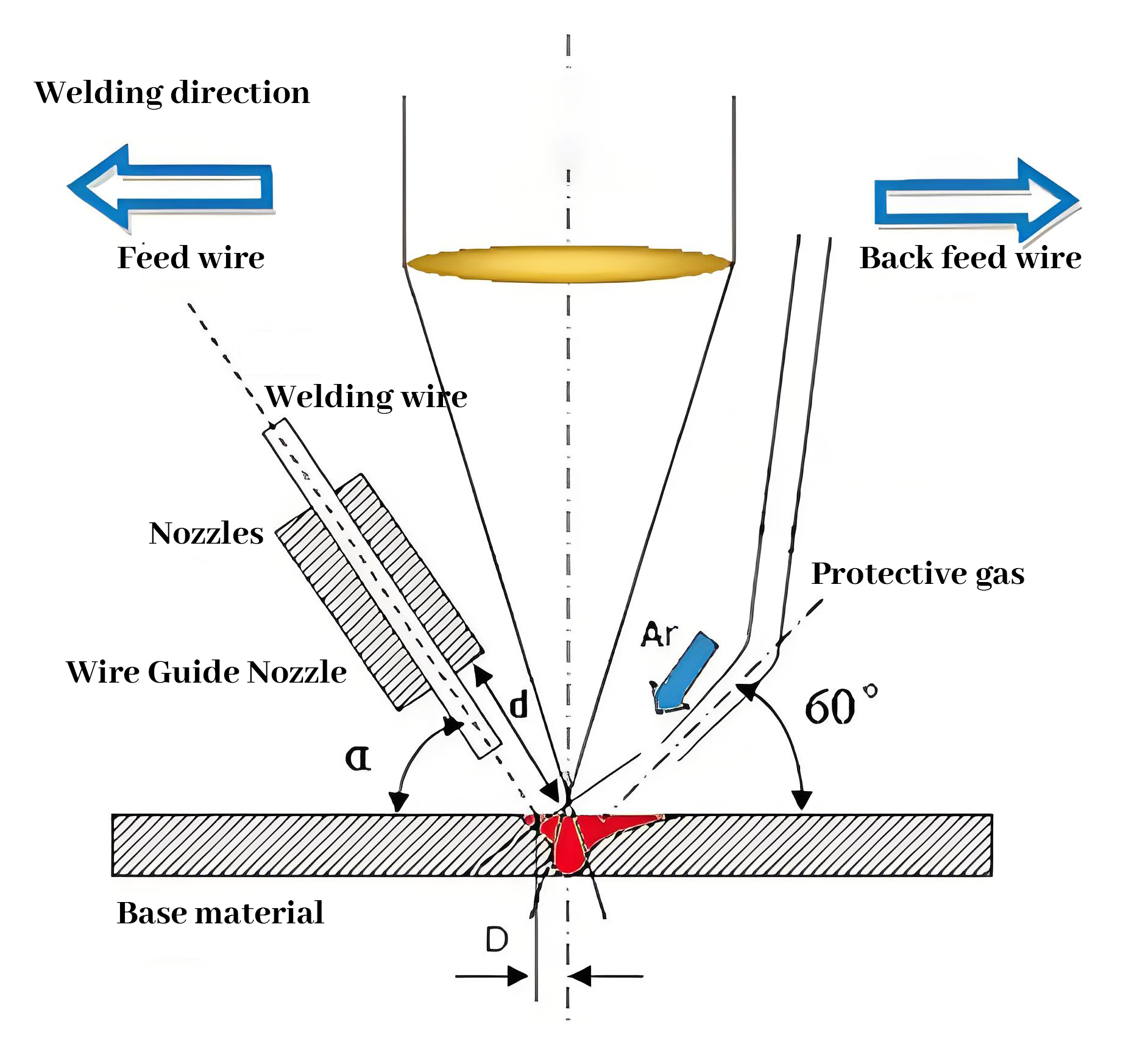
-溶接:
- 溶接とは、2つ以上の材料の接合面を熱、圧力、あるいはその両方によって溶融状態にし、最終的に材料間の恒久的な接合を実現するプロセスです。溶接は主に構造接合、つまり異なる部品の接合に使用されます。
- 溶接では、レーザー、アーク、摩擦など、さまざまな熱源を使用できます。
- 主な目的: 2 つ以上のワークピースを安全に結合すること。
材料処理方法
-レーザークラッディング:
- コーティング材料は通常、粉末またはフィラメントの形で、金属、セラミック、または複合材になります。
- クラッド層と基材の間には明確な境界があり、クラッド層の厚さは数十ミクロンから数ミリメートルまで制御可能です。コーティングは材料の表面にのみ作用します。
- コーティングは材料の表面にのみ影響し、基材の主な特性には影響しません。
-溶接:
- 溶接は 2 つ以上のモノリシックなワークピースを接合するもので、溶接材料は通常、ベース材料またはフィラー材料です。
- 溶接部分は永久的に結合されており、溶接部分の周囲の母材は変化する可能性があります (例: 熱影響部)。
- 溶接は表面だけの溶接ではなく、2 つのワークピースを溶かして固めることで一体化した接合部を形成します。
アプリケーションシナリオ
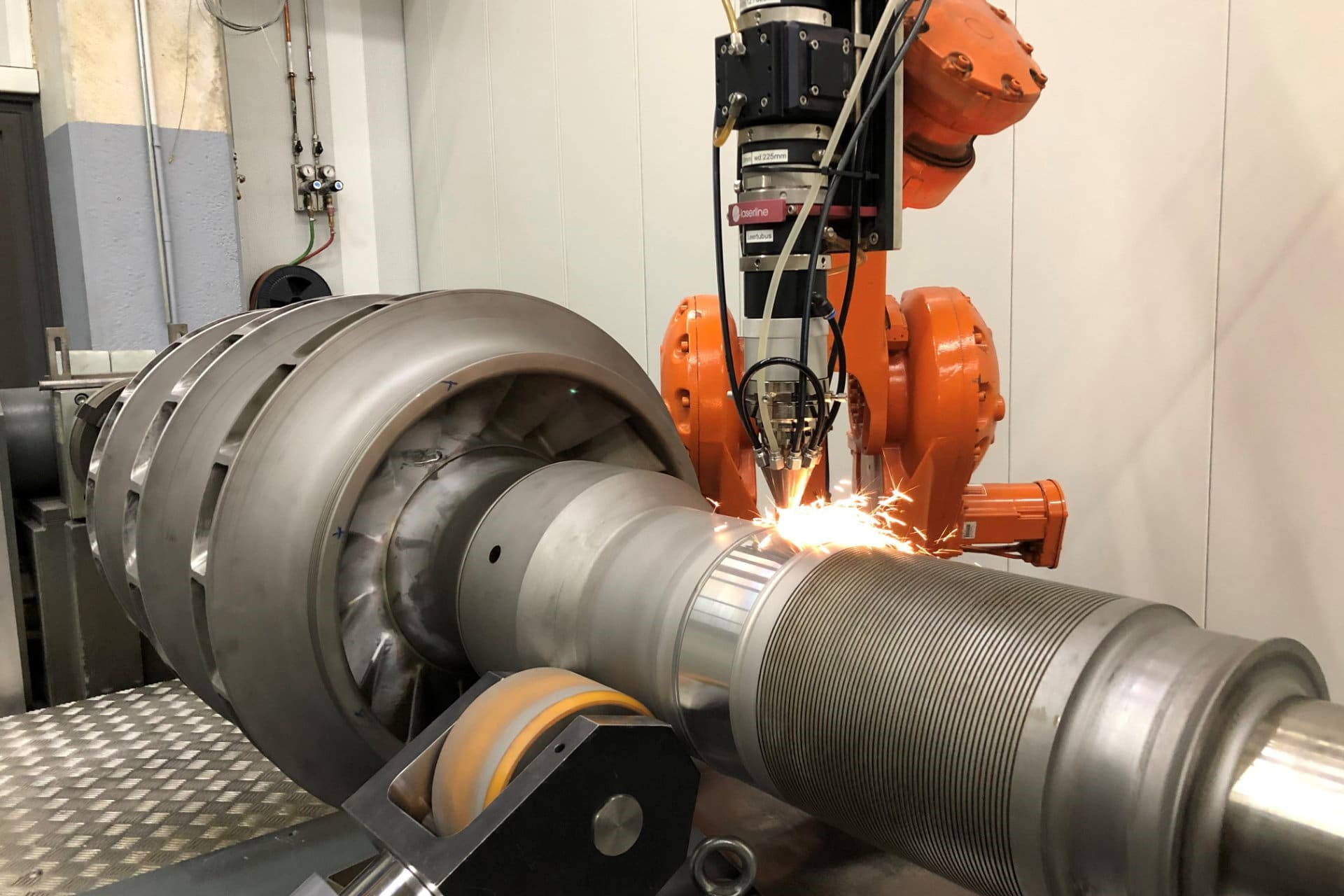
-レーザークラッディング:
- シャフト、ギア、金型などの機械部品の表面補修によく使用されます。また、表面を強化して材料の耐摩耗性や耐腐食性を向上させるためにも使用されます。
- 代表的な用途としては、航空宇宙、自動車、エネルギー、金型産業などがあります。
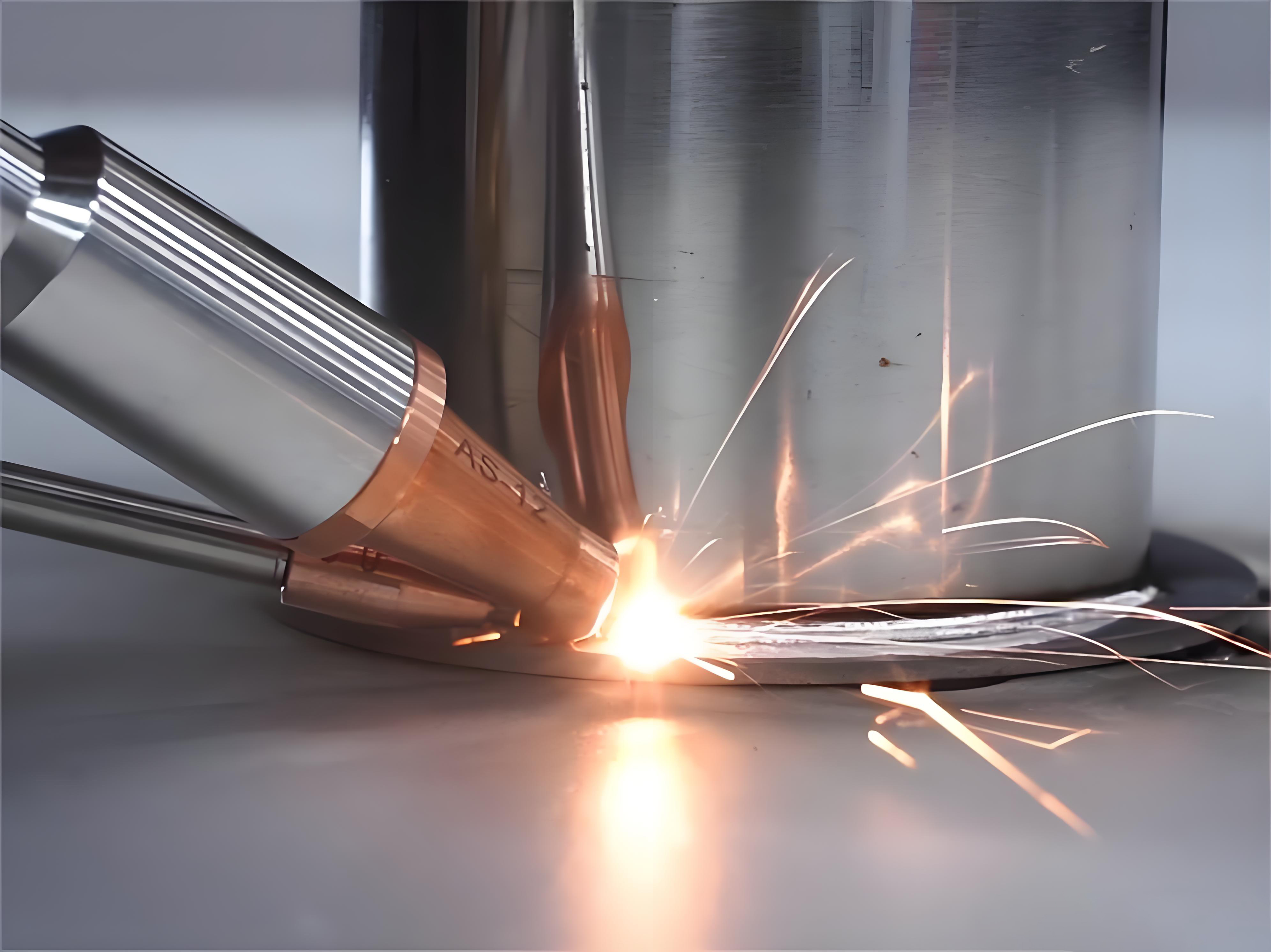
-溶接:
- 製造業および組立業、特に自動車製造業、建設業、造船業、恒久的な接続が必要な配管業で広く使用されています。
- 一般的な溶接方法には、レーザー溶接、アーク溶接、ガスシールド溶接などがあります。
熱入力と衝撃
-レーザークラッディング:
- クラッディングプロセス中、レーザーの高エネルギー密度が狭い領域に集中するため、熱影響領域が小さくなり、材料の変形が少なくなります。
- レーザークラッディングの入熱は比較的低く、母材への影響は限定的です。
-溶接:
- 溶接には通常、大量の熱入力が伴い、溶接領域内および周囲の母材は熱変形と応力変化を経験します。
- 熱影響部が大きくなり、硬度の低下やひび割れの発生など、材料特性の変化が生じる可能性があります。
精度と処理の詳細
-レーザークラッディング:
- レーザークラッディングは高精度で、局所的な微細加工に適しており、制御可能で、複雑な表面コーティング構造を可能にします。
-溶接:
- 溶接精度は比較的低く、特に手溶接や従来のアーク溶接ではその傾向が顕著です。レーザー溶接は高精度ですが、ミクロンレベルの微細表面コーティングには一般的に使用されません。
主な違い
レーザークラッディングは主に表面の修復と改質に使用され、材料の表面に特殊な特性を付与します。一方、溶接は主に材料間の構造的な接合に使用されます。クラッディングは材料の表面改質機能に重点を置き、溶接はワークピース全体を接合します。
投稿日時: 2024年10月10日