高速レーザークラッディング粉末の利用率に関係する要因は何ですか?
高速レーザークラッディング技術は飛躍的に進歩しました。加工効率の向上と加工コストの削減への追求は尽きることがなく、いかにして加工コストを継続的に削減していくかが、高速レーザークラッディング研究の重要なテーマとなっています。

レーザークラッディングの総コストのうち、粉末コストは80%~90%を占めるため、粉末の利用率を向上させることは、高速レーザークラッディングにおいて解決すべき重要な技術課題です。したがって、高速レーザークラッディングにおける粉末の利用率に関連する要因を明らかにする必要があります。これらの要因を一つずつ検討し、高速レーザークラッディングにおける粉末の利用率を向上させる方法について考察します。
(1)溶融池のスポットサイズ
高速レーザークラッディングにおける粉末の利用率に影響を与える主な要因は、溶融池のスポットサイズ、つまり基材表面に照射されるレーザーのスポットサイズです。レーザー出力に応じて、高速レーザークラッディングにおける溶融池のスポットサイズは1mm~5mmの範囲で選択できます。実際の作業では、装置のレーザー出力に応じて適切な溶融池スポットサイズを選択する必要があります。
溶融池のスポットが小さすぎると粉末利用率が低くなります。溶融池のスポットが大きすぎると、コーティング面の平坦性が低下します。溶融池のスポットを大きくすると粉末利用率が向上しますが、溶融池のスポットが大きすぎるとコーティング面の平坦性が低下し、その後の研削・研磨工程でも粉末の無駄が発生します。高速レーザークラッディングにおいても、粉末利用率はクラッディング工程のみで考慮するのではなく、クラッディング工程全体における研削・研磨後の粉末の総合的な利用率を考慮する必要があります。
(2)クラッドヘッドの粉末出口穴の直径
クラッディングヘッドの粉末出口孔の直径は、粉末流の厚さを決定します。孔径が小さいほど粉末流は細かくなりますが、粉末流が細かいほど粉末流の分散速度が速くなります。実際の作業では、クラッディングの高さと溶融池のスポットサイズに応じて適切な粉末出口孔の直径を選択し、基材表面における粉末スポット径が溶融池のスポット径よりも小さくなるようにする必要があります。そうしないと、溶融池のスポットサイズを超えた粉末が失われ、無駄になります。
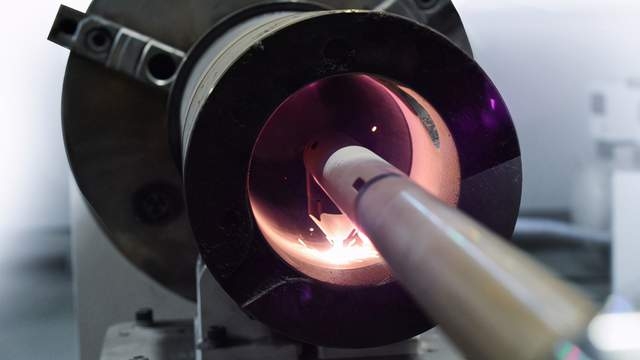
(3)レーザー出力
レーザー出力は、溶融池に落下する粉末が完全に溶融できる程度に大きくなければなりません。粉末供給量などのパラメータが一定の場合、レーザー出力が高いほど粉末利用率は高くなります。
(4)粉末供給量
装置のレーザー出力を決定する際、粉末供給量が少ないほど粉末利用率は高くなります。しかし、粉末供給量を減らすとクラッディング効率に影響します。クラッディング効率を考慮しない場合、粉末供給量を制御することで粉末利用率を100%にまで高めることは可能ですが、この方法は意味がありません。
(5)クラッド線速度
高速レーザークラッディングの線速度は、通常のレーザークラッディングの線速度の数倍から数十倍にもなります。基材とクラッディングヘッドの相対移動速度が大きい場合、基材表面における粉末粒子の運動エネルギーが大きくなるため、粉末の噴出量が多くなり、粉末利用率が低下します。また、レーザー出力を決定する際に、クラッディングヘッドと基材の相対移動速度が高いほど、溶融池の温度が低下し、粉末利用率が低下します。
(6)ワークピース体積
同じクラッディングパラメータの場合、ワークピースの直径(体積)が大きいほど、粉末利用率が低下します。これは、体積が大きいとレーザーエネルギーが母材に吸収されやすくなり、溶融池の温度が十分に高くならないためです。したがって、体積の大きいワークピースの場合、粉末利用率を向上させるには、より高出力のクラッディング装置を使用する必要があります。
(7)粉末粒子径
高速レーザークラッディング用粉末は光との相互作用時間が短いため、レーザー出力の大きさに応じて適切な粒子径の粉末を選択する必要があります。粉末粒子が大きいと、限られた時間内に溶融できず、射出時のスプラッシュロスが発生します。
上記は、高速レーザークラッディングにおける粉末の利用率に影響を与える主な7つの要因です。粉末の利用率を向上させ、クラッディング加工の加工コストを削減するためには、設備とクラッディングワークの具体的な条件に応じて、適切なハードウェア技術パラメータとクラッディング加工パラメータを選択する必要があります。
ここでも強調しておきたいのは、粉末利用率は、単純なクラッディング工程の粉末利用率ではなく、加工プロセス全体の粉末利用率を考慮する必要があるということです。通常のレーザークラッディングでは粉末利用率は100%に達することもありますが、総合的な粉末利用率は50%未満になることがよくあります。
投稿日時: 2022年8月24日