溶接には様々な方法があり、それぞれ独自の原理、長所と短所、適用分野を有しています。以下では、一般的な溶接方法について、原理、特徴、長所と短所、適用分野、他の溶接方法との比較分析などを含めて詳しく説明します。
1. 溶接方法の分類
溶接方法は、大きく分けて以下の種類に分けられます。
•溶融溶接(アーク溶接、レーザー溶接など):金属を溶融状態まで加熱して融合すること。
•圧力溶接(摩擦溶接、拡散溶接など):溶融せずに圧力の作用によって金属を接合します。
•ろう付け(例:軟ろう付け、硬ろう付け):低融点の充填材を使用してワークピースを接合します。
2. 一般的な溶接方法の説明
2.1 SMAW - シールドメタルアーク溶接
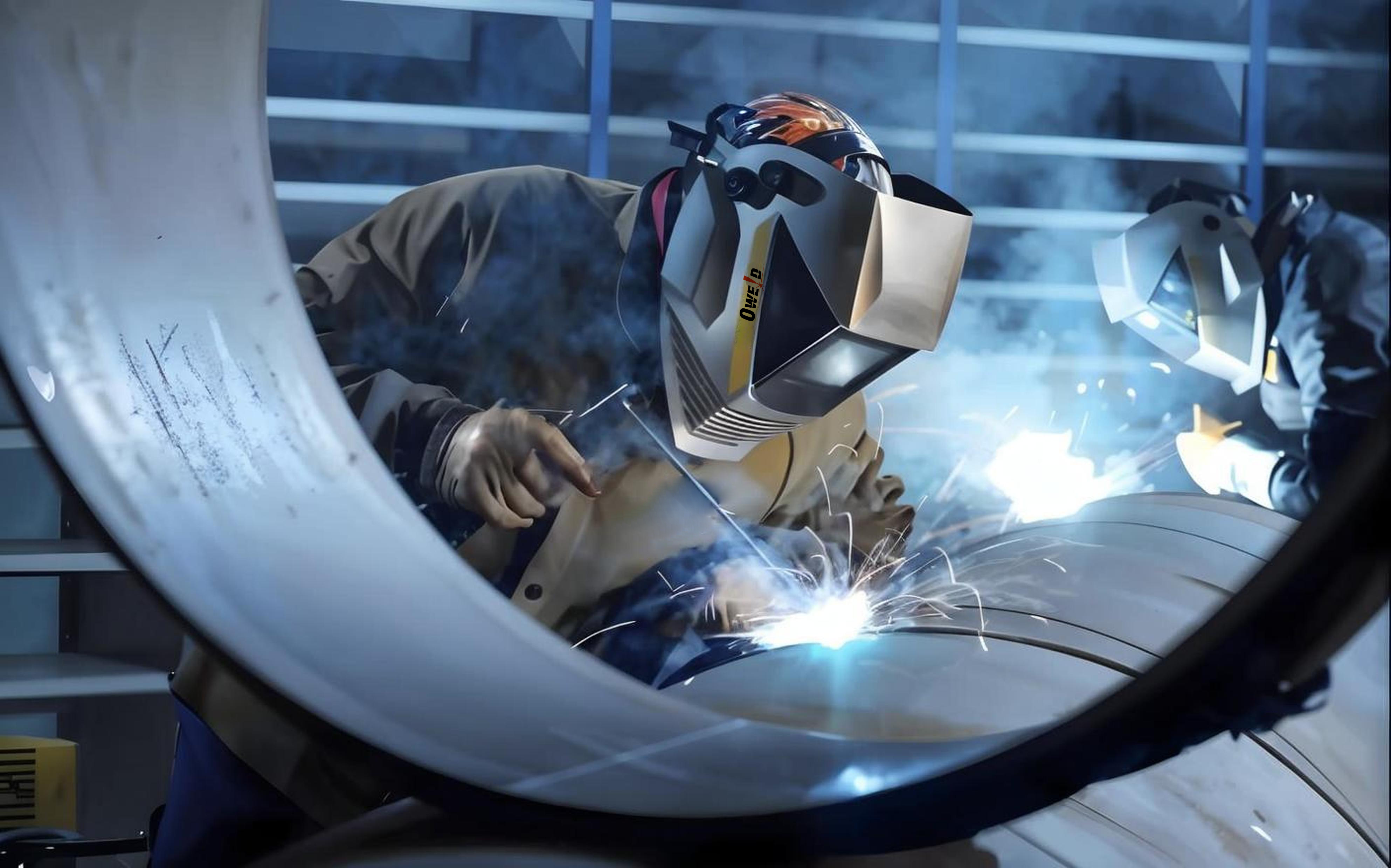
原理手動アーク溶接では、電極と母材の間にアークを発生させ、高温(約4000℃)を発生させて電極と母材を溶融させ、溶接部を形成します。溶接プロセス中、電極コーティングは保護ガスを生成し、溶接部の酸化を防ぎます。
特徴:
溶接棒(コア+フラックスコーティング)で溶接します。
立ち溶接、バックアップ溶接など、さまざまな姿勢での溶接に適しています。
環境要件が低い屋外でも操作できます。
利点:
シンプルな装置、柔軟な操作、現場作業やメンテナンス作業に適しています。
炭素鋼、ステンレス鋼、鋳鉄など、さまざまな金属を溶接できます。
複雑な形状のワークの溶接に適しています。
デメリット:
溶接効率が低いため、溶接棒を頻繁に交換する必要があります。
溶接の品質は溶接工の技術に大きく左右され、溶接欠陥(気孔やスラグなど)が発生しやすくなります。
溶接ではより多くの煙や粉塵が発生し、環境をさらに汚染します。
用途:
建設、メンテナンス、橋梁、パイプライン、造船などの業界に適しています。
小規模プロジェクトや現場作業に適しています。
2.2 GMAW - ガスメタルアーク溶接
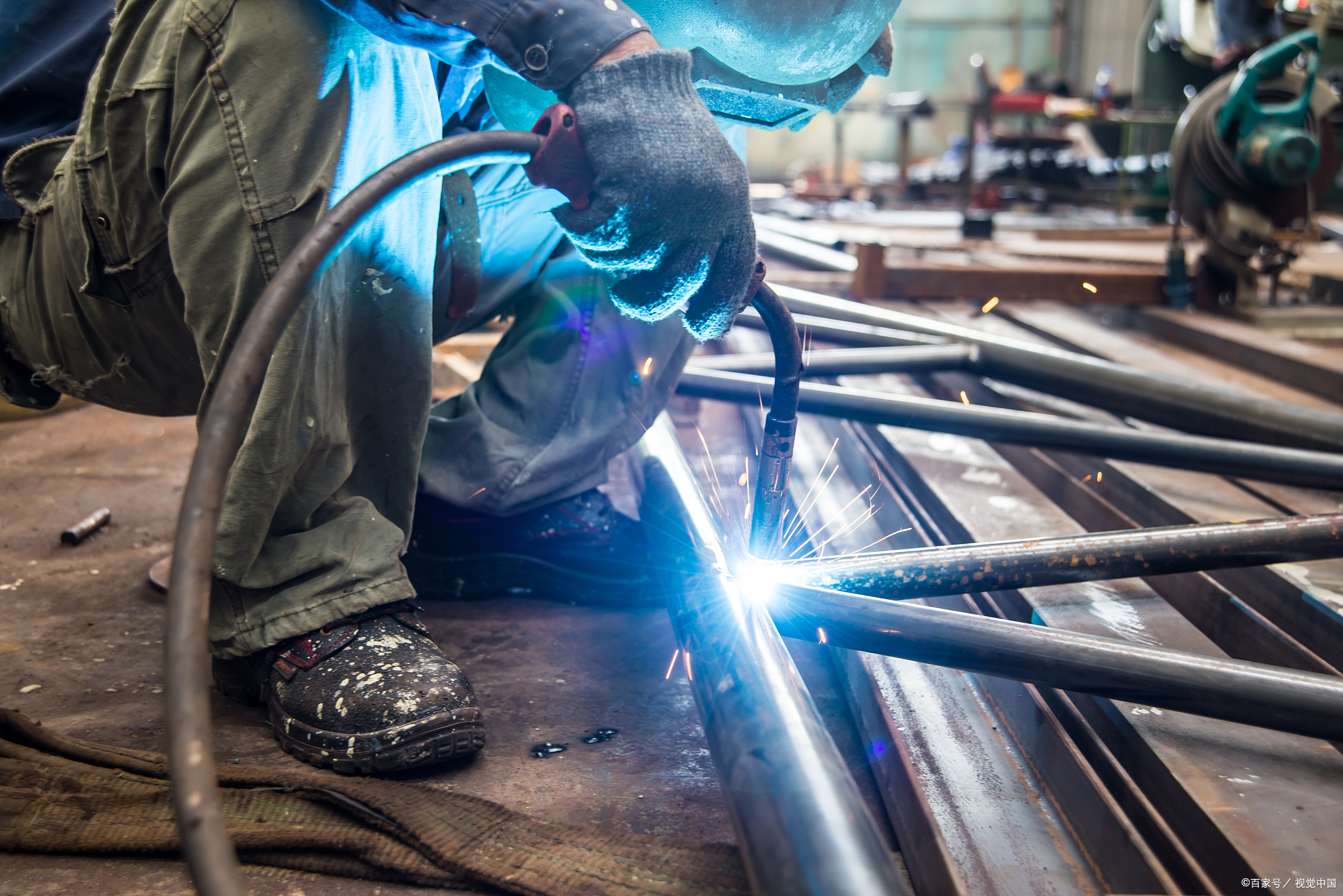
原理:ガスシールド溶接では、連続的に供給されるワイヤを電極として使用し、保護ガス(アルゴン、二酸化炭素など)環境でアークを生成し、ワイヤと母材を溶かして溶接部を形成します。
分類:
MIG(金属不活性ガス)溶接:不活性ガス(アルゴンなど)を使用し、アルミニウム合金、ステンレス鋼、その他の材料に適しています。
MAG (金属活性ガス)溶接: 活性ガス(二酸化炭素または混合ガス)を使用し、軟鋼、構造用鋼の溶接に適しています。
特徴:
自動ワイヤ送給方式を採用し、溶接効率を向上。
滑らかな溶接面と安定した溶接品質。
環境(風、湿度)に敏感なので屋外施工には適していません。
利点:
溶接速度が速く、大量生産に適しています。
薄板溶接、変形の小さい溶接に使用できます。
ロボット溶接などの自動溶接が簡単に実現できます。
デメリット:
設備コストが高く、ガス供給システムが必要です。
強風環境では使用できません。保護ガスが吹き飛ばされ、溶接の品質に影響を及ぼします。
きれいな金属表面には適していますが、ひどい錆や油で汚れたワークピースには適していません。
用途:
自動車製造、船舶、橋梁、家電産業等
高効率、高品質の工業生産に適しています。
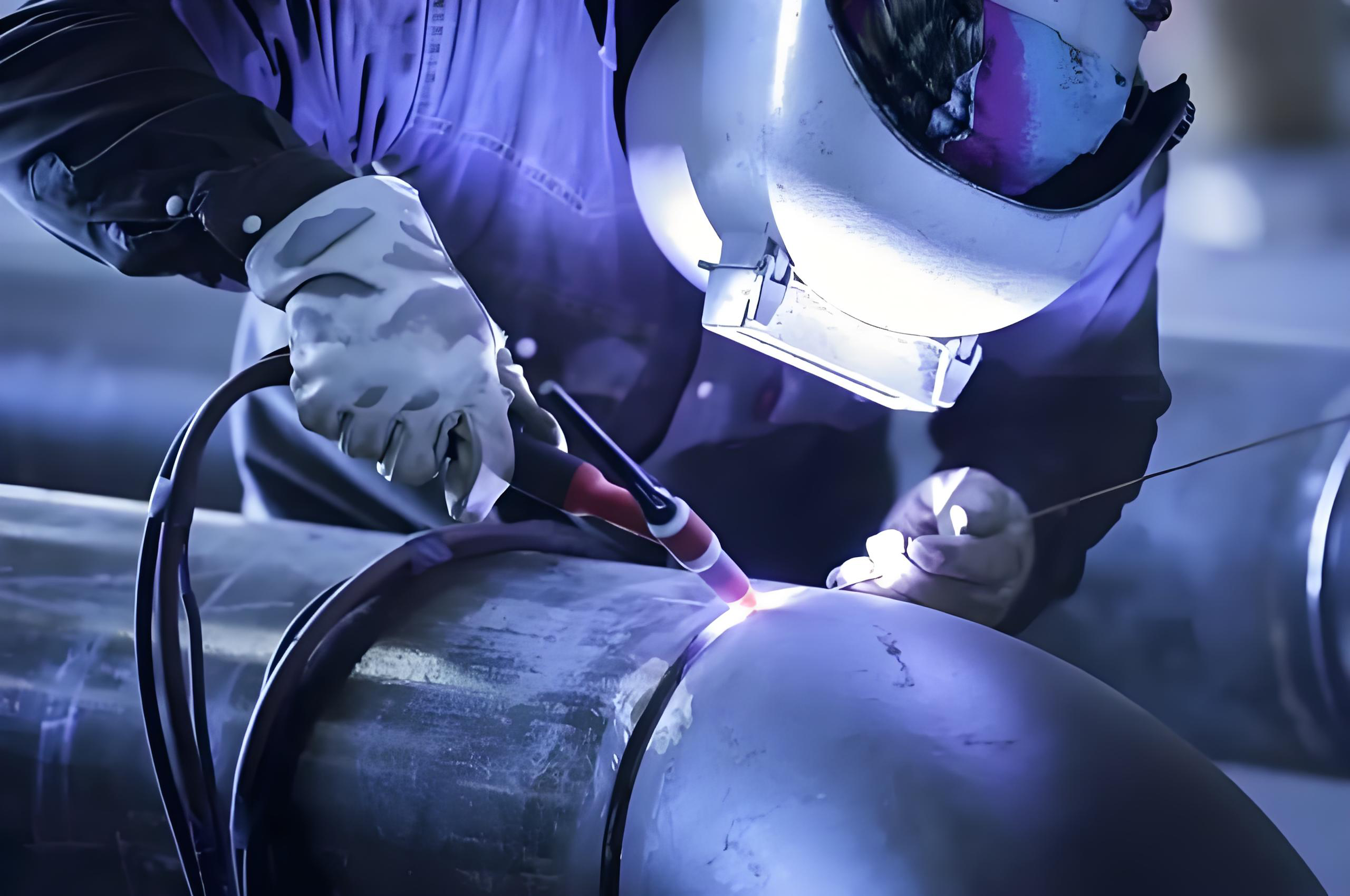
原理TIG 溶接では、溶けないタングステン電極を使用してアークを発生させ、アルゴンの保護下で母材とフィラー金属を溶かして溶接を形成します。
特徴:
高い溶接品質、滑らかで美しい溶接。
航空宇宙、医療機器などの高精度溶接に適しています。
薄板、非鉄金属(アルミニウム、銅、チタン)の溶接に適しています。
利点:
スパッタのない溶接継ぎ目、高品質、精密溶接に適しています。
異種金属溶接に適しています。
保護ガス(アルゴン)は溶接部の酸化を効果的に防止します。
デメリット:
溶接速度が遅く、効率が低い。
高価な設備、溶接工には高度なスキルが求められます。
風の影響を受けやすいため、屋外での溶接には適していません。
用途:
航空宇宙、電子機器、医療、精密製造業。
ステンレス鋼管、アルミニウム合金構造部品の溶接
2.4 SAW - サブマージアーク溶接
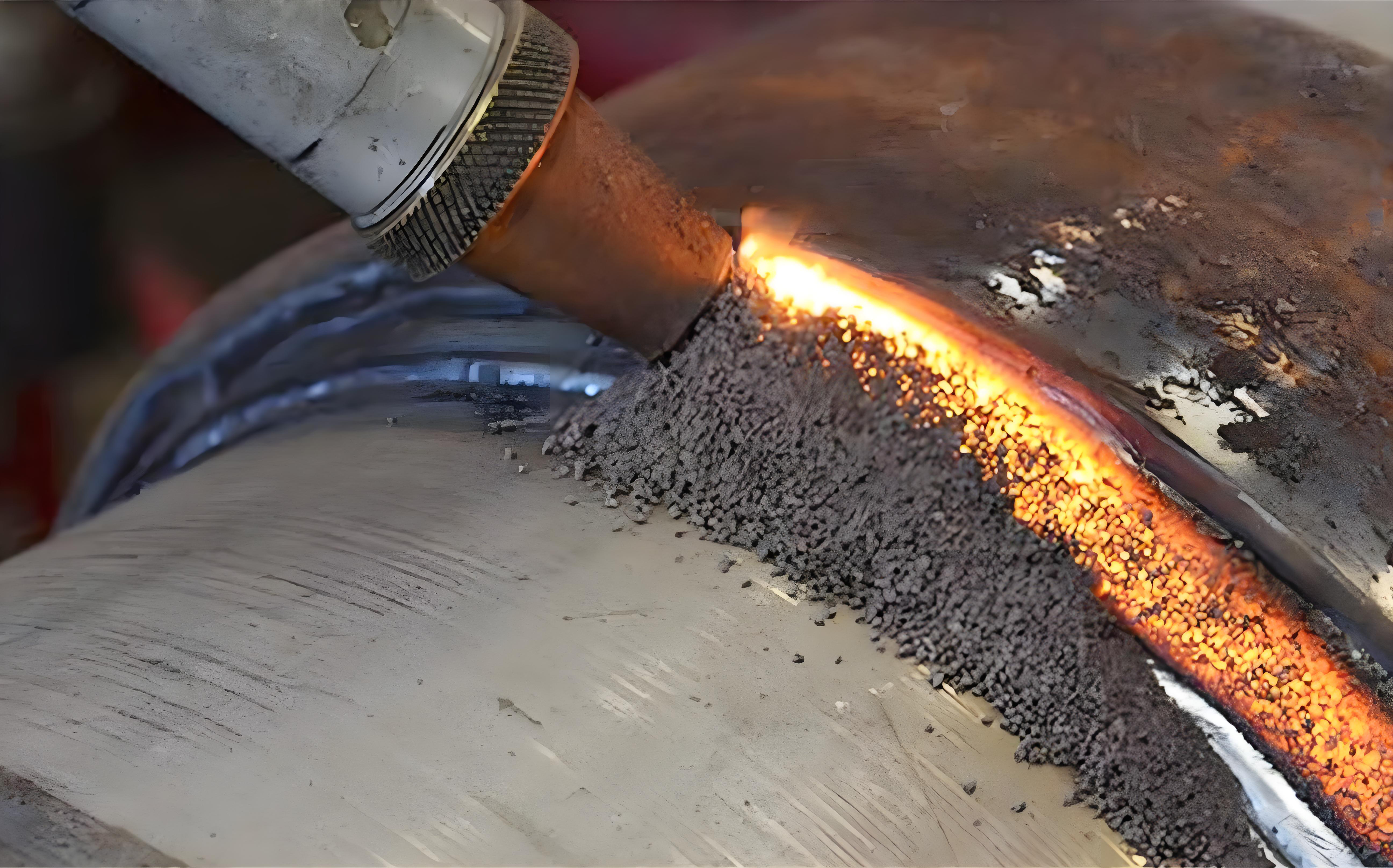
原理:サブマージアーク溶接では、アークを覆うためにフラックスが使用されます。フラックスは高温で溶けて、溶接部を空気から保護する保護層を形成します。
特徴:
橋梁、ボイラー製造などの厚板溶接に適しています。
水平溶接にのみ使用可能です。垂直溶接、仰角溶接、その他の姿勢には適用できません。
利点:
溶接速度が速く、効率が高く、大量生産に適しています。
溶接品質が高く、フラックスにより溶接欠陥(気孔、亀裂)を防止します。
アーク暴露がなく、溶接煙が少なくなり、作業環境が改善されます。
デメリット:
直線溶接にのみ使用可能で、複雑な形状の溶接には適用できません。
大型の装置のため、小型部品の溶接には適していません。
用途:
厚板、パイプ、橋梁、圧力容器の溶接。
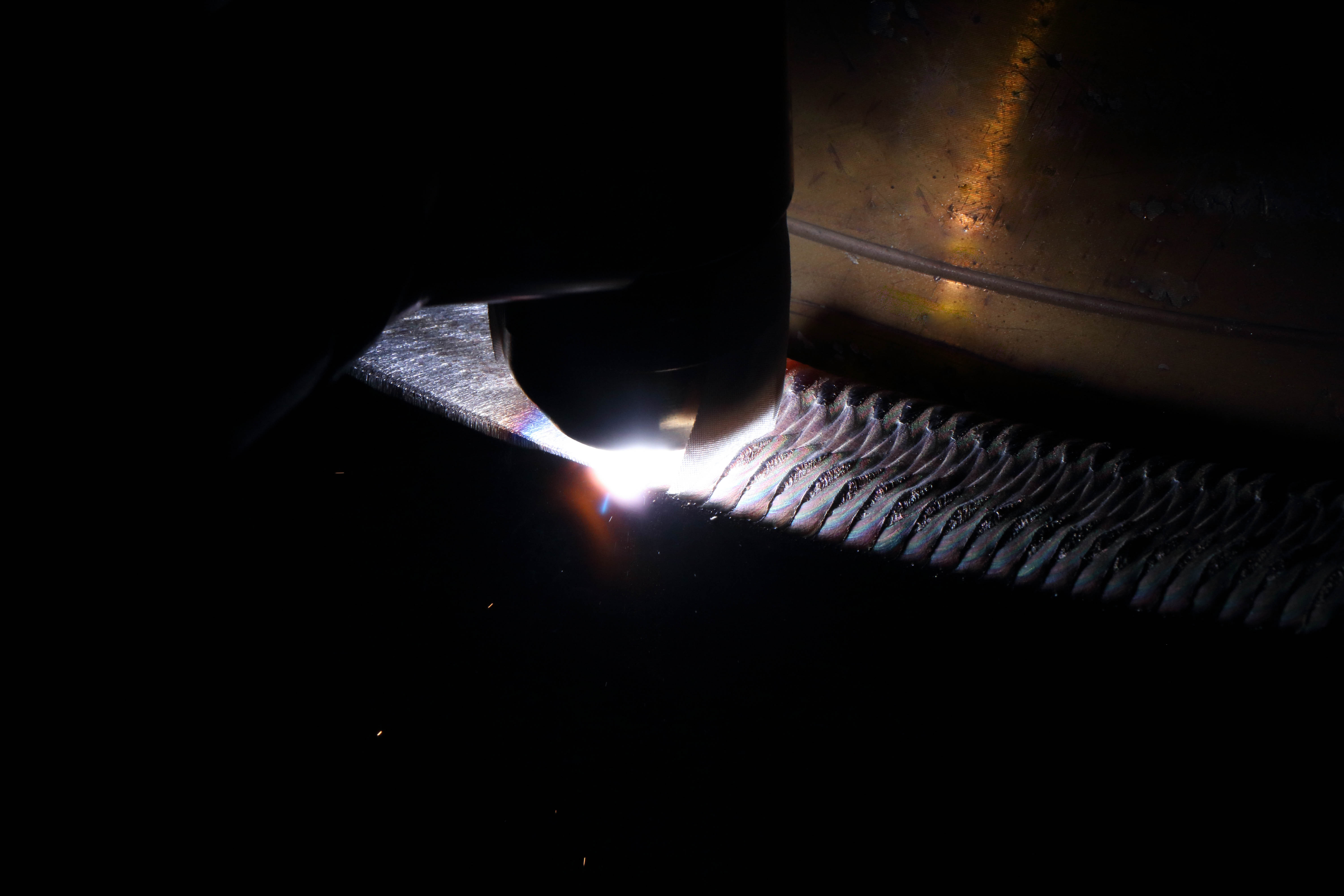
原理:高温のプラズマアークを使用して金属を溶かして溶接します。
利点:
エネルギーを集中し、溶接歪みを小さくします。
薄肉材料などの精密溶接に適しています。
デメリット:
設備コストが高く、メンテナンスが複雑です。
高い操作スキルが要求されます。
用途:航空宇宙、医療機器、電子産業。
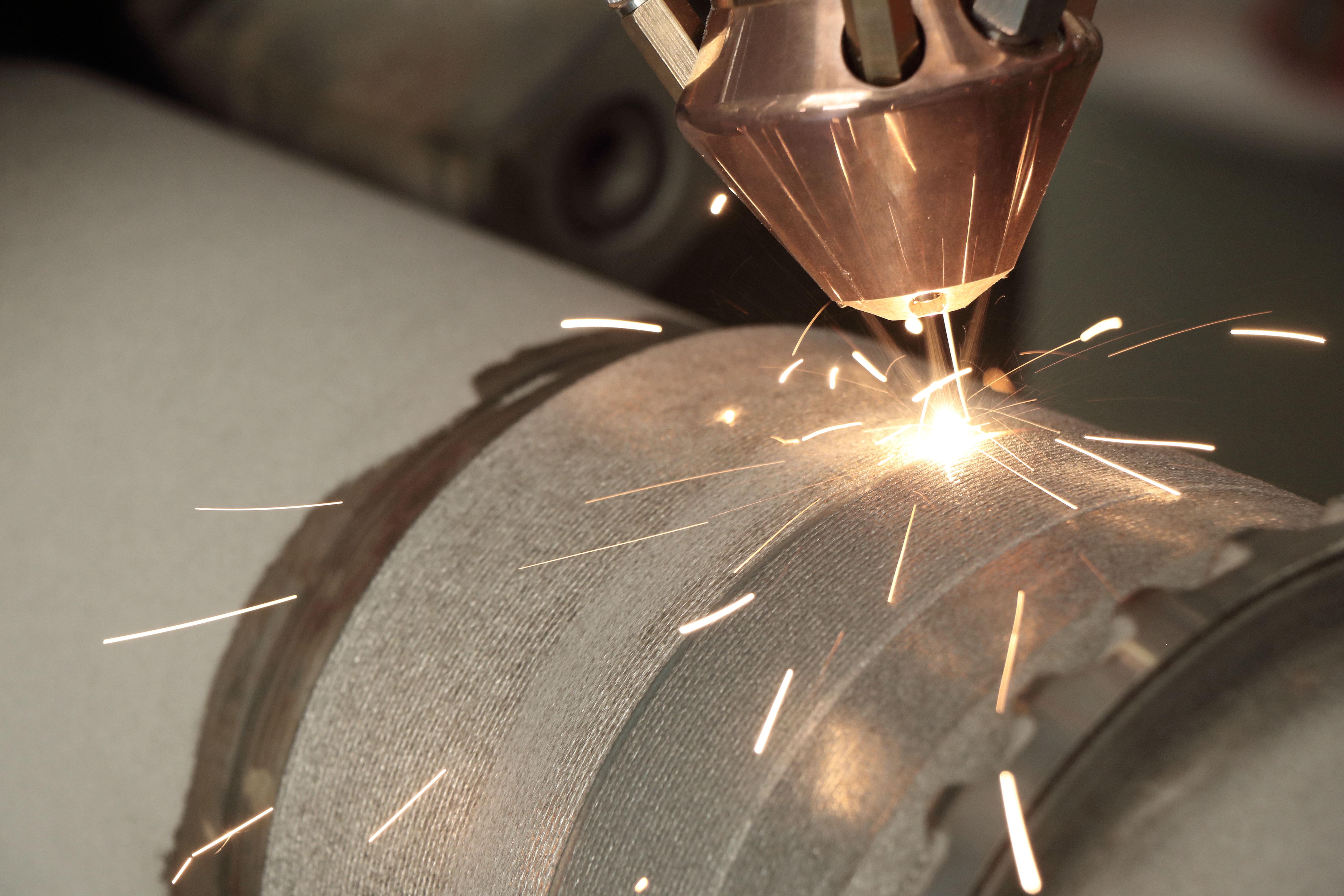
原理: 高エネルギー密度のレーザービームを使用して金属を溶かして溶接するため、溶接継ぎ目が狭く、熱影響部が小さくなります。
利点:
高精度、微細部品の溶接に適しています。
熱影響部が小さく、変形も小さい。
デメリット:
高価な設備、高いメンテナンスコスト。
高精度の組み立て、小さな溶接ギャップが必要です。
用途:電子機器、自動車、医療機器、光学機器。
2.7 EBW - 電子ビーム溶接
原理:真空環境下で高エネルギー電子ビームを使用して溶接材料を溶かします。
利点:
高融点材料(チタン、タングステン、ジルコニウム)の溶接が可能です。
溶接深さが大きく、厚板の溶接に適しています。
デメリット:
真空環境、高価な設備で実行する必要があり。
アプリケーション: 航空宇宙、原子力、精密機器製造。
2.8 FW - 摩擦圧接
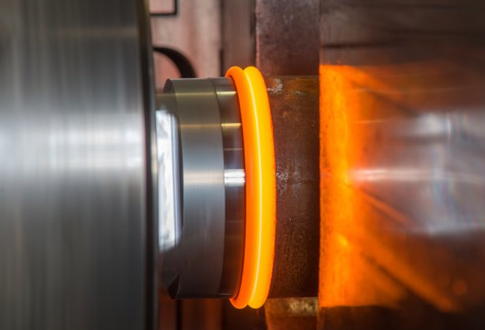
原理:摩擦溶接は、2 つのワークピースを高速で回転させ、互いに接触させることで摩擦熱を発生させ、接触面を柔らかくし、圧力を加えて強力な接続を形成します。
特徴
溶融がなく、固体溶接のため、溶融溶接の欠陥(気孔、亀裂など)を回避します。
アルミニウムと銅、ステンレス鋼と炭素鋼などの異種金属の溶接に適しています。
溶接速度が速く、通常は数秒で完了します。
利点
高い溶接品質、充填材不要
再現性の高い自動生産に適しています。
溶接歪みが少なく、機械的特性に優れます。
デメリット
シャフト部品などの円形または定形ワークに適しています。
設備コストが高くなります。
アプリケーション
自動車のドライブシャフト、掘削工具、宇宙船の部品など
鉄道輸送、航空エンジン製造。
投稿日時: 2025年3月14日