製造業における溶接の品質、効率、精度に対する要求が高まるにつれ、ますます多くの企業が次のような高度な溶接技術に注目しています。プラズマトランスファーアーク溶接(PTAW)そしてレーザー溶接これら2つの技術は、航空宇宙、エネルギー機器、自動車、金型修理などの分野で極めて重要な役割を果たしています。では、これら2つの技術にはどのような違いがあるのでしょうか?そして、生産ニーズに最適な溶接プロセスをどのように選択すればよいのでしょうか?この記事では、その原理、利点、適用シナリオ、その他の側面について詳細に分析します。
PTA溶接技術とレーザー溶接技術の動作原理
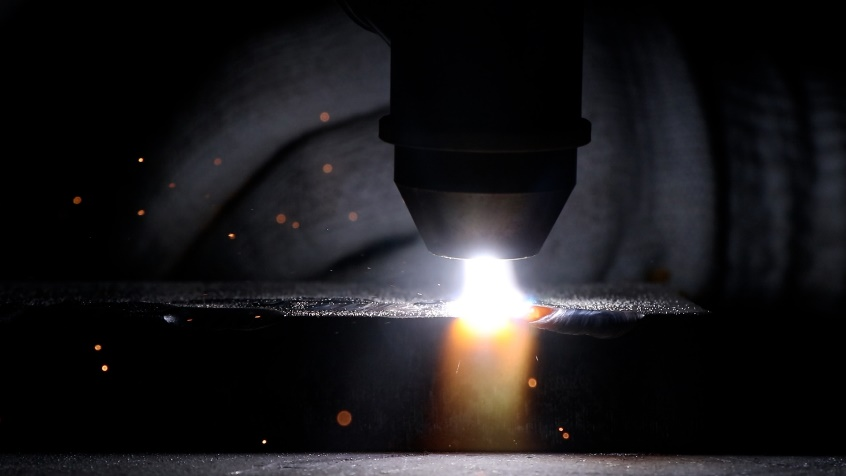
プラズマトランスファーアーク溶接(PTAW)は、金属粉末を高温プラズマアークで溶融し、母材と冶金結合させる溶接またはクラッディングプロセスです。その主な利点は、緻密で耐摩耗性と耐腐食性に優れた表面補強層を形成できることです。そのため、重工業における設備の修理や寿命延長に最も多く利用されているプロセスの一つとなっています。
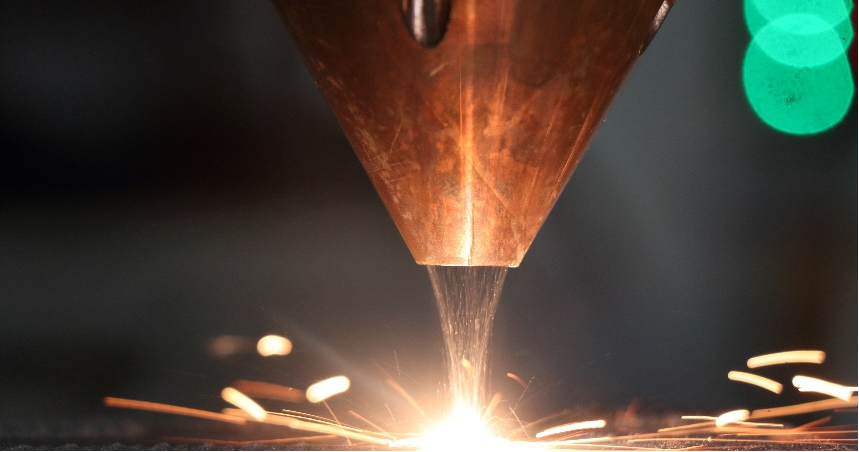
レーザー溶接高エネルギー密度のレーザービームを材料表面に照射し、急速な溶融と溶接形成を実現する技術です。レーザービームの優れた集光性により、熱影響部が非常に小さく、高い溶接精度を実現できるため、精密製造、電子パッケージング、医療機器など、溶接継ぎ目の美観と均一性が極めて重要となる用途に適しています。
PTA プロセスとレーザー プロセスの利点の比較: 本当に必要なのは精度ですか、それとも耐久性ですか?
クラッディング能力と層制御
バルブ、金型、石油掘削機などの保護層など、厚く強固で耐腐食性に優れたトップコートが必要な場合は、PTAWが最適です。PTAWは、0.5mmから5mmの膜厚を制御でき、溶接層と母材を強固に密着させます。
対照的に、レーザー溶接実現するのが得意超薄層, ゼロギャップ接続そして歪みのない溶接小型ステンレス鋼管、携帯電話ハウジング、精密ギアなど、寸法が要求される部品に適しています。
熱衝撃制御とワークの変形
PTAWは熱を集中させますが、レーザー溶接よりも入熱量が大きいため、局所的な変形が生じやすくなります。そのため、構造剛性の高いワークピースや後加工が可能なワークピースに適しています。
レーザー溶接は、極めて低い入熱量と高い溶接速度により、ほぼ「熱影響のない」溶接を実現し、「非破壊美観」加工の代表的な技術です。
適用可能な材料の多様性
PTAW は主に鉄系、コバルト系、ニッケル系合金などの金属の表面強化処理に適用され、大型鋼部品の局所的な肉盛溶接、再生、修理のニーズに適しています。
レーザー溶接の材料適応性は広く、炭素鋼、ステンレス鋼、アルミニウム合金、チタン合金、さらには銅や金などの反射率の高い金属も特定の波長で簡単に溶接できます。
PTAとレーザークラッディングの適用領域の比較:大きなブロックと細かい作業
PTAWの代表的な用途:
– バルブシール面クラッディング(耐摩耗性および耐腐食性)
– 金型エッジピーニング(耐用年数の延長)
– 石炭採掘設備、搬送スパイラル、ドリルパイプの修理
– 石油、化学高圧装置の壁面クラッディング
一般的なレーザー溶接の用途:
– 携帯電話ケースの溶接(高精度、熱変形なし)
– 医療機器のマイクロ溶接(チタン合金溶接)
– 航空宇宙薄板構造溶接
– バッテリーシェルのカプセル化、太陽光発電の溶接、自動車部品の効率的な組み立て。
コスト、効率、自動化: 誰がより経済的で効率的でしょうか?
経済面では、PTAW設備への投資は比較的控えめですが、粉末供給システム、水冷システム、複雑な制御システムなどのサポートが必要であり、長期的なメンテナンスコストは高くなります。主な利点は、長期的な耐久性とワークピースの寿命延長にあり、高価値ワークピースの再生に適しています。
レーザー溶接、特に高出力ファイバーレーザーシステムへの初期投資は高額ですが、バッチ生産における速度、精度、一貫性により、特に新エネルギー自動車製造、民生用電子機器のパッケージングなどの自動化組立ラインシステムでは、設備コストを効果的に償却できます。
結論: 自分に合った溶接プロセスを選択するにはどうすればよいでしょうか?
選択はPTAWそしてレーザー溶接「上級かどうか」ではなく、アプリケーションシナリオ, 製品形態, パフォーマンス要件と予算:
腐食性、研磨性が高く、高温環境で使用され、強力な表面強化層が必要な大型の工業用部品を扱っている場合、PTAW の方が間違いなく信頼性が高くなります。
電子部品、医療用精密部品、薄肉構造など、製品に高速溶接、高精度、美観、微細変形が求められる場合、レーザー溶接が最適です。
投稿日時: 2025年6月10日