プラズマクラッディングと溶射のどちらを選ぶかは難しい選択です。プラズマクラッディングと溶射はどちらも広く使用されている表面改質技術ですが、それぞれの特性により、異なる用途シナリオに適しています。この記事では、それぞれのプロセスの詳細を詳しく説明し、それぞれのプロセスの特徴、欠点、そしてメリットをより深く理解していただけるようにしています。
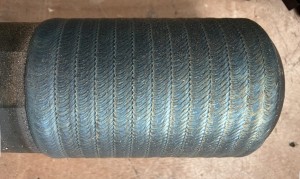
クラッディングとスプレー塗装の理解
•クラッディング
クラッディングとは、添加材を溶融状態まで加熱し、基材の表面に堆積させて保護層または修復層を形成するプロセスです。このプロセスでは、添加材と基材表面との良好な結合を形成するために、通常、高温が必要となります。
•スプレー
スプレー塗装は、保護、装飾、または機能向上を目的とした外装材を形成するために、スプレー状の外装材(液体または固体)を基材の表面に塗布するプロセスです。
プラズマクラッディングと溶射:どちらがあなたにとって良いのでしょうか?
プラズマクラッディングと溶射を比較する最も良い方法は、両方で何ができるかを見ることです。
プラズマクラッディングの利点
プラズマクラッディング高温・高エネルギー処理技術であり、粉末材料をプラズマアークによって高速で溶融し、ワークピースの表面に堆積させます。その利点は以下のとおりです。
• 高い接着強度: クラッド層と基材の接着強度が高いため、表面の耐摩耗性と耐腐食性が大幅に向上します。
• 精密制御:プロセスパラメータを調整することでクラッド層の厚さと形状を正確に制御できるため、複雑な形状のワークピースに適しています。
• 幅広い材料に適用可能:プラズマクラッディングは、金属、セラミック、合金など、さまざまな産業ニーズを満たす幅広い材料に使用できます。
この技術は、航空宇宙、石油・ガス、オフショア、高温高圧機器など、高度な耐摩耗性、耐熱性、耐腐食性が求められる用途に特に適しています。
プラズマクラッディングの欠点
プラズマクラッディングには多くの利点がありますが、いくつかの欠点と制限もあります。
• 設備コストが高い:初期投資とメンテナンスコストが高くなります。
• プロセスの複雑さ: パラメータの正確な制御と高度なスキルを要する操作。
• 材料の制限: すべての材料がクラッディングに適しているわけではありません。特に、一部の高融点材料は適していません。
l 熱影響部: 基板にはまだ若干の熱影響があり、変形につながる可能性があります。
• 厚さの制限: 中程度の厚さのクラッドに適していますが、厚すぎると問題が発生する可能性があります。
溶射の利点
溶射は、材料を加熱してワークピースの表面に噴霧することで保護層を形成する表面処理法です。溶射の主な利点は以下のとおりです。
• 高効率:溶射は処理が速いため、広い面積や高スループットの生産ニーズに適しています。
• コスト効率が高い: プラズマクラッディングと比較して、溶射装置と材料は比較的安価であるため、予算が限られているプロジェクトに適しています。
• 汎用性:熱溶射は、フレーム溶射、プラズマ溶射、アーク溶射など、幅広いプロセスに適しています。詳細については、ニュースウェブサイトをご覧ください。テクノロジーニュース.
溶射は、製紙、繊維、冶金、自動車産業など、ワークピースの表面の耐摩耗性、耐腐食性、または修復が必要な場所で広く使用されています。
溶射の欠点
溶射の欠点は次のとおりです。
• 設備コストが高い:初期の設備投資とメンテナンスコストが高額です。
• 操作の複雑さ: 熟練したオペレーターが必要であり、プロセスパラメータの制御が要求されます。
•クラッドの多孔性: クラッディングには微細な気孔があり、それが密度と耐腐食性に影響することがあります。
• 接着の制限: 場合によっては、クラッディングと基材の接着が、フュージョンクラッディングなどの他のプロセスほど良好でないことがあります。
• 材料の無駄:スプレー工程中の材料利用率が低く、一部の材料が無駄になる可能性があります。
これらの欠点により、一部の用途では溶射の広範な使用が制限される可能性があります。
どうやって選べばいいですか?
プラズマクラッディングと溶射のどちらを選ぶかは、お客様の具体的なニーズによって異なります。高い精度と接合強度が求められる用途で、予算に余裕がある場合は、プラズマクラッディングが最適な選択肢です。一方、迅速な処理、コスト管理、そして比較的緩い表面処理が求められるプロジェクトの場合は、溶射の方が間違いなく費用対効果の高いソリューションです。
要約する
どの技術を選択する場合でも、その特徴とメリットを理解することで、より情報に基づいた意思決定を行い、投資収益率を最大化することができます。当社の専門家チームは、お客様のニーズに最適な表面処理技術をお選びいただけるよう、専門的なアドバイスを提供いたします。
お問い合わせ
詳しい情報や技術サポートについては、お気軽にお問い合わせください。弊社チームにお問い合わせください当社は、お客様に可能な限り最高の表面処理ソリューションを提供することに尽力しています。
投稿日時: 2024年9月4日