L'impiego della tecnologia di rivestimento al plasma per rinforzare la superficie delle punte da trapano PDC è un mezzo efficace per migliorarne la resistenza all'usura, agli urti e alla corrosione.
1. Fase di preparazione
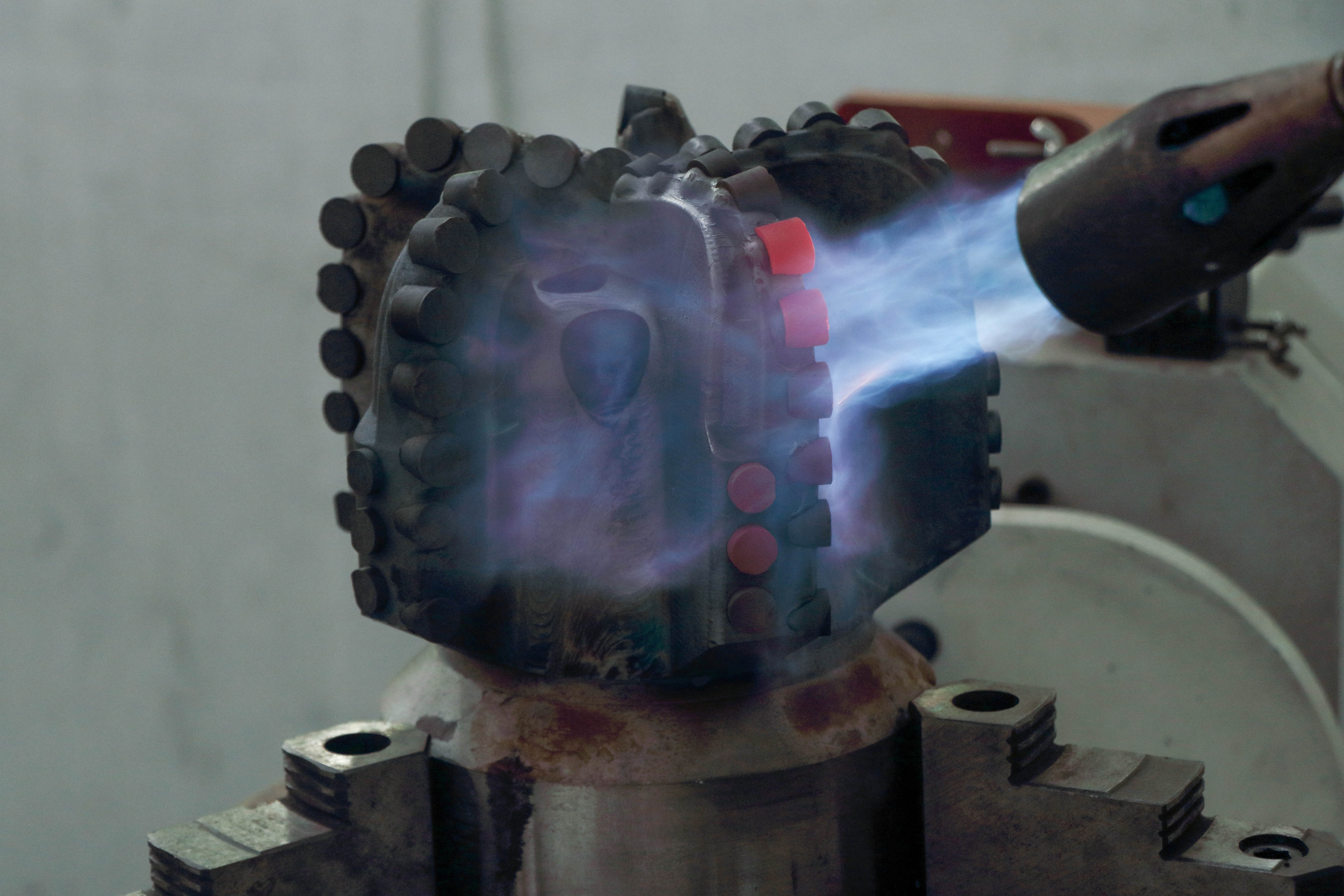
(1) Determinare il materiale di rivestimento
- Materiali di rivestimento comunemente utilizzati:
- Lega a base di cobalto: elevata resistenza all'usura e alla corrosione.
- Lega a base di nichel: resistente all'ossidazione ad alta temperatura e alla corrosione chimica.
- Leghe a base di ferro: economiche e adatte a requisiti di media resistenza all'usura.
- Leghe rinforzate con particelle ceramiche: ad esempio WC (carburo di tungsteno), TiC (carburo di titanio), ecc. per requisiti di resistenza all'usura molto elevati.
(2) Determinazione della superficie del rivestimento
- La placcatura per fusione delle punte da trapano PDC di solito è mirata a:
- Parte laterale: per migliorare la resistenza all'usura e ridurre l'attrito e le perdite di taglio.
- La superficie della carcassa: per migliorare la resistenza complessiva alla corrosione e agli urti.
(3) Pretrattamento superficiale
- Pulire la zona del rivestimento per rimuovere olio, ossidi, rivestimenti e impurità.
- Trattamento meccanico di levigatura o sabbiatura per aumentare la rugosità della superficie e migliorare l'adesione dello strato di rivestimento fuso al substrato.
2. Implementazione del processo di rivestimento
(1) Impostazione dell'attrezzatura per il rivestimento al plasma
- Composizione dell'attrezzatura:
Pistola per saldatura al plasma, alimentatore di polvere, macchina per saldatura al plasma automatizzata, ecc.
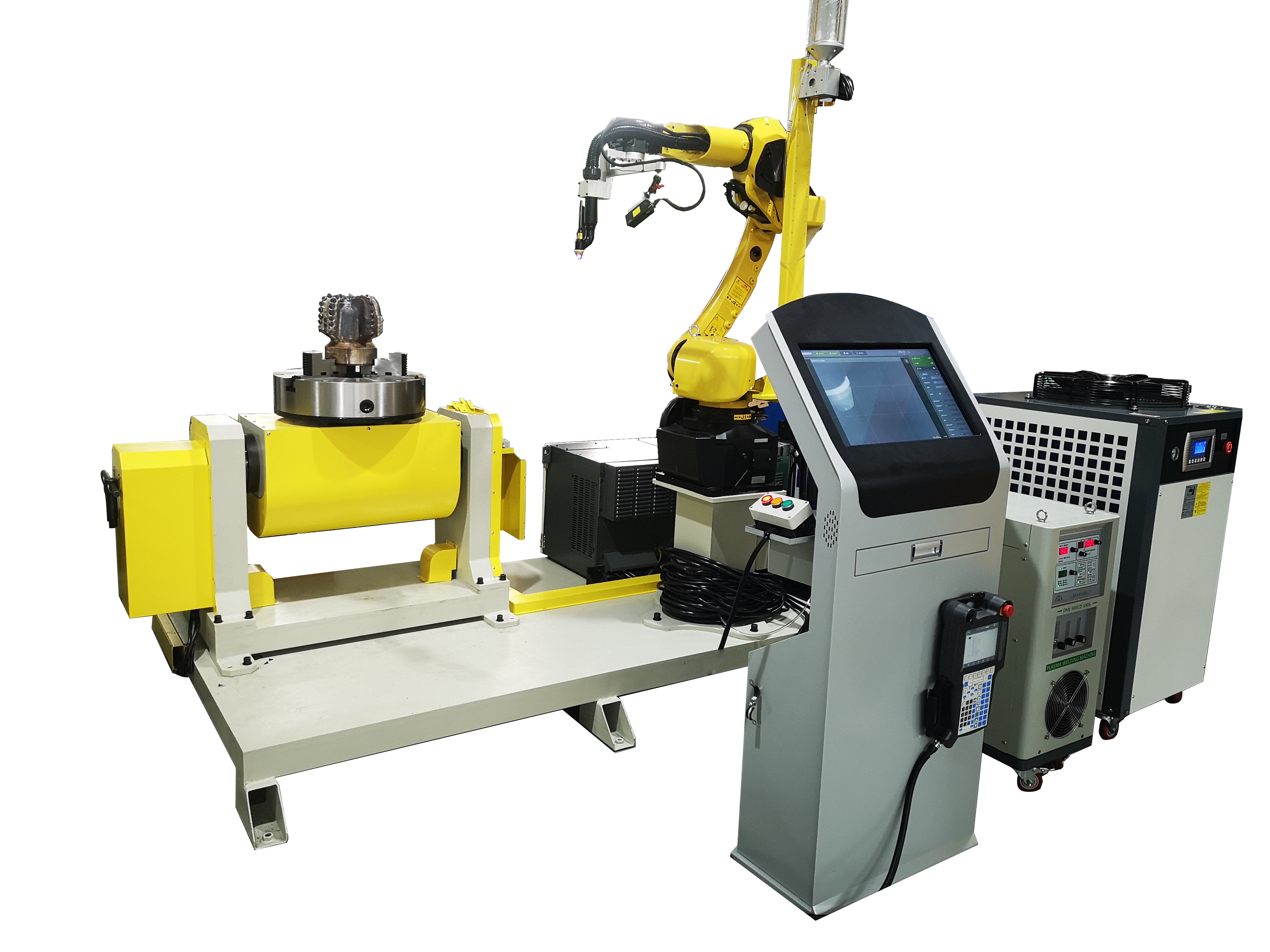
- Impostare i parametri chiave:
- Corrente e tensione dell'arco: selezionare in base al materiale da rivestire, generalmente nell'intervallo 100-300 A.
- Apporto termico: regolare per controllare la deformazione del substrato e il tasso di diluizione.
- Velocità di alimentazione della polvere: solitamente compresa tra 10 e 50 g/min per garantire l'uniformità dello strato di rivestimento.
(2) Esecuzione del rivestimento
- Il processo di rivestimento:
1. Innesco dell'arco al plasma, formazione di un bagno di fusione ad alta temperatura.
2. Attraverso il sistema di alimentazione della polvere, il materiale in polvere viene spruzzato nella piscina fusa e legato metallurgicamente al substrato.
3. in base alla forma della punta del trapano, lungo il percorso impostato per un rivestimento uniforme, per garantire che non vi siano perdite di rivestimento o sovrafusione.
- Controllo dell'influenza termica: evitare il surriscaldamento o la deformazione del substrato della punta del trapano PDC regolando i parametri dell'arco al plasma e il metodo di raffreddamento.
(3) Trattamento di raffreddamento
- Raffreddamento naturale o adozione di un metodo di raffreddamento a velocità controllata per evitare crepe causate da stress termico.
3. Fase post-trattamento
(1) Controllo della qualità del rivestimento
- Controllo dell'aspetto: osservare se lo strato di rivestimento è uniforme, privo di crepe e fori d'aria.
- Test delle prestazioni: misurare la durezza, lo spessore (solitamente 0,5 ~ 3 mm), la resistenza dell'adesione e altri indicatori.
- Controlli non distruttivi: utilizzare test a ultrasuoni o a raggi X per individuare difetti interni.
(2) Finitura
- Se la superficie risulta ruvida dopo la placcatura per fusione, è necessario un trattamento di tornitura o rettifica per soddisfare i requisiti di dimensione e forma delle punte da trapano PDC.
(3) Ottimizzazione delle prestazioni
- Trattamento termico: tempra o rinvenimento dello strato di rivestimento fuso, se necessario, per ottimizzarne ulteriormente le proprietà organizzative.
4. Precauzioni
1. Evitare danni da surriscaldamento
- Durante il rivestimento al plasma, l'apporto di calore deve essere rigorosamente controllato per evitare danni termici all'inserto PDC e al substrato.
2. Abbinamento dei materiali
- Il materiale di rivestimento deve essere abbinato al materiale del substrato del bit PDC per garantire la resistenza dell'adesione e la costanza delle prestazioni.
3. Controllo ambientale
- Se possibile in un ambiente con bassa umidità o con gas protettivo, per evitare che l'ossidazione comprometta la qualità del rivestimento.
Questo processo può essere utilizzato per migliorare le prestazioni delle nuove punte PDC e per riparare quelle usurate.
Data di pubblicazione: 09-01-2025