1.1 L'effet du courant sur la moulure ducouche de revêtement
Actuel(A) | Depth (de fusion)(mm) | Fhauteur de laine(mm) | largeur(mm) |
70 | 0,19 | 4.26 | 16.41 |
80 | 0,35 | 4.07 | 17.08 |
90 | 0,88 | 3.43 | 17.48 |
100 | 1.03 | 2.73 | 17.58 |
110 | 1.25 | 2.65 | 18.14 |
Tableau 3.1 Géométrie de la coupe transversale de la couche de revêtement avec différents courants
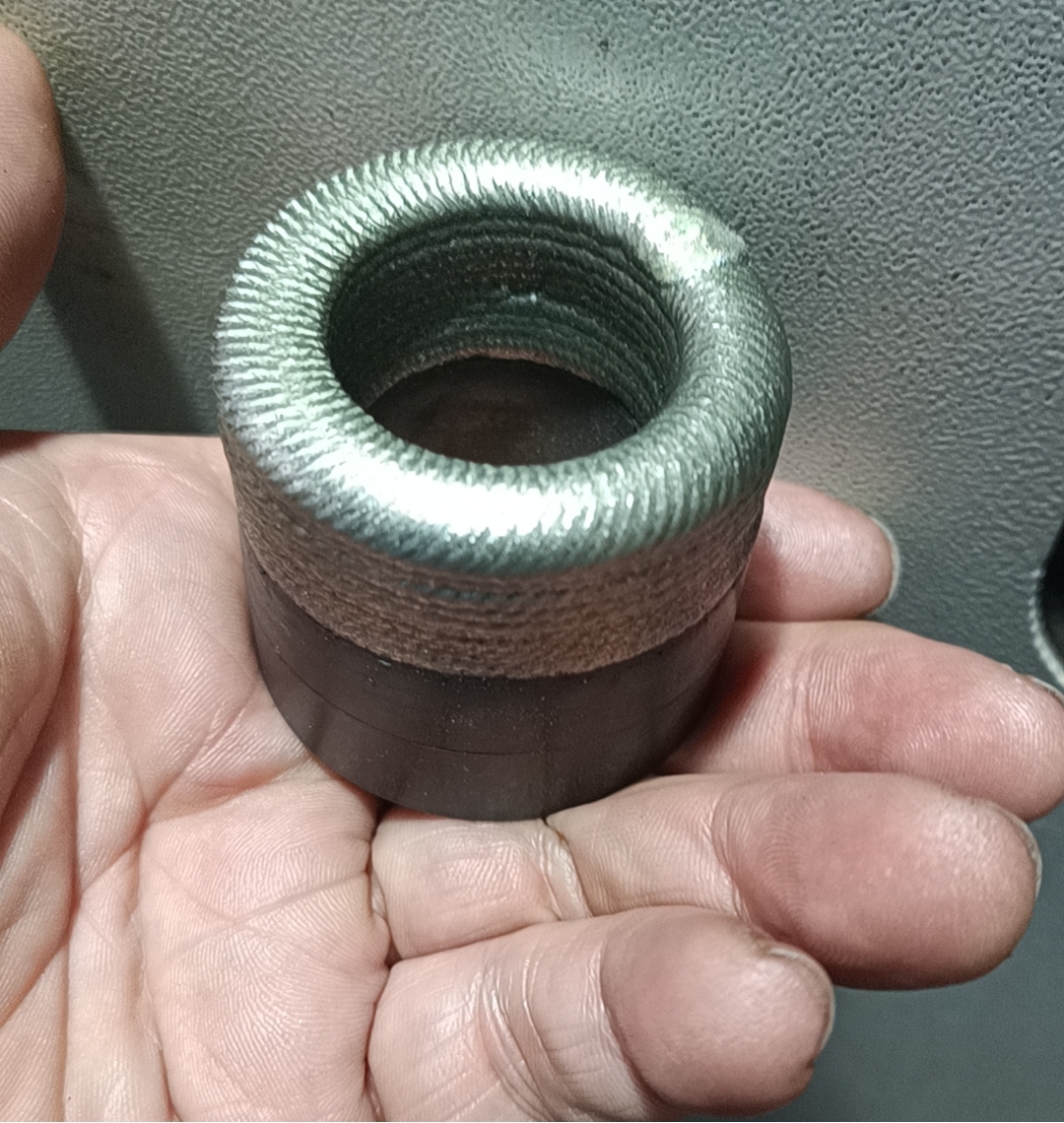
À mesure que le courant augmente, la profondeur et la largeur de la couche de revêtement augmentent et la hauteur de la couche diminue. Cela est dû à l'augmentation du courant, la chaleur générée non seulement fera fondre le métal de revêtement, mais aussi une partie du mélange de fusion, de revêtement et de substrat se produit, de sorte que la couche de revêtement dans son ensemble, entraînant une augmentation de la profondeur de la fusion, la hauteur de la couche diminue; et augmenter le courant, ce qui fait que l'arc plasmatique est plus grossier, augmente la plage de température de la source de chaleur, le pool fondu dans la capacité de propagation du substrat est plus fort, de sorte que la largeur du pool fondu augmente.
1.2 l'effet desoudagevitesse sur la moulure de la couche de revêtement en fusion
Vitesse de soudage(mm / s) | Depth (de fusion)(mm) | Fhauteur de laine(mm) | largeur(mm) |
4 | 1.17 | 4.34 | 17.61 |
5 | 1.06 | 2.73 | 17.58 |
6 | 0,35 | 2.61 | 16.96 |
7 | 0,13 | 2.55 | 15.01 |
8 | - | - | - |
Tableau 3.2 Géométrie transversale des couches de revêtement en fusion avec différentes vitesses de soudage
Avec l'augmentation de la vitesse de soudage, la profondeur de fusion de la couche de revêtement diminue, la hauteur de la couche montre d'abord une forte diminution puis devient lentement plus petite, la largeur diminue. Lorsque la vitesse de soudage est de 4 mm / s, avec l'augmentation du métal de revêtement dans une certaine mesure, la profondeur de fusion est de 1,17 mm, à l'heure actuelle, l'entrée de chaleur par unité de longueur ne peut pas faire fondre le matériau de base pour plus de 4,34 mm; La vitesse de soudage augmente à 5 mm / s, l'entrée de chaleur par longueur unitaire, la quantité d'alimentation du fil est réduite, de sorte que la profondeur de fusion, la hauteur de la couche, la largeur sont réduites; Si la vitesse de soudage continue d'augmenter, comme mentionné ci-dessus, l'entrée de chaleur est insuffisante à ce moment, seule une petite partie du matériau de base peut fondre, la hauteur de la couche de fusion montre une forte diminution, puis devient lentement plus petite, la largeur est réduite. Si la vitesse de soudage continue d'augmenter, comme mentionné ci-dessus, l'entrée de chaleur à l'heure actuelle est insuffisante, seule une petite partie du matériau de base peut être fondu, la couche de revêtement de fusion ne semble pas s'affaisser, entraînant une plus grande réduction de la profondeur de la fusion, tandis que la hauteur de la couche est réduite moins.
1.3 Influence de la vitesse d'alimentation du fil sur la moulure de la couche de revêtement
Agrafulture(mm / s) | Depth (de fusion)(mm) | Fhauteur de laine(mm) | largeur(mm) |
40 | 1.43 | 2.24 | 19.91 |
50 | 1.25 | 2.56 | 18.86 |
60 | 1.03 | 2.73 | 17.58 |
70 | 0,71 | 3.46 | 15.82 |
80 | 0,16 | 5.16 | 14.20 |
Tableau 3.3 Dimensions géométriques de la coupe transversale de la couche de revêtement avec différentes vitesses d'alimentation en fil.
À mesure que la vitesse d'alimentation du fil augmente, la profondeur et la largeur de la couche de revêtement diminue et la hauteur de la couche augmente. This is due to the fact that when the current and welding speed are certain, the heat input per unit length is certain, and with the increase of wire feeding speed, the amount of filler wire per unit length is increased, and the cladding metal needs to absorb more heat, and when the heat input is unable to completely melt the whole cladding layer, the base material part is less melted, so the depth of melting decreases, and the height of the layer increases, and the spreading capacity of the Le revêtement du métal près de la partie du matériau de base se détériore, de sorte que la largeur diminue rapidement. La largeur diminuera rapidement.
En résumé, l'arc à arc plasmatique 2205 paramètres de processus en acier inoxydable duplex varient de: courant 90 A ~ 110 A, vitesse de soudage 4 mm / s ~ 6 mm / s, vitesse d'alimentation du fil 50 mm / s ~ 70 mm / s, taux d'écoulement de gaz ionique de 1,5 l / min.
2 en fonction de la méthode de surface de réponse de la fusion de la couche de revêtement de couche de formation des paramètres du processus d'optimisation
La méthode de surface de réponse (méthode de surface de réponse, RSM) est une combinaison de conception expérimentale et de techniques statistiques de méthodes d'optimisation, l'analyse des données de test, peut être dérivée du facteur d'impact et la valeur de réponse de la fonction d'ajustement et une carte de surface en trois dimensions, peut refléter intuitivement le facteur d'impact et la valeur de réponse de la relation entre le test réel a un rôle d'optimisation prédictif. Based on the above reasons, the selection of RSM in the central composite design (Central composite design, CCD) to develop process optimization program, to explore the current, welding speed, wire feeding speed and the fusion cladding layer dilution rate, aspect ratio of the relationship between the current, welding speed, wire feeding speed and the fusion cladding layer dilution rate, and mathematical modeling, derived from the process parameters and the dilution rate, aspect rapport de la fonction, pour réaliser la prédiction de la qualité de la couche de revêtement de fusion.
2.1 L'influence des paramètres de processus sur le taux de dilution de la couche de revêtement.
Tableau 3.8 Résultats et vérification d'optimisation du processus
Groupe | X1(A) | X2(mm · s-1) | X3(mm · s-1) | rapport de dilution(%) | rapport d'aspect |
Groupe de prédiction | 99 | 6 | 50 | 14.8 | 4.36 |
Groupe de test 1 | 99 | 6 | 50 | 13.9 | 4.13 |
Groupe de test 2 | 99 | 6 | 50 | 15.5 | 4.56 |
Groupe de test 3 | 99 | 6 | 50 | 14.3 | 4.27 |
Erreur moyenne | 2.9 | 2.3 |
(Soudage PTA par Shanghai Duomu)
Figure 3.16 Paramètres de processus optimaux Résultats du test (a) Groupe de test 1; (b) le groupe de test 2; (c) Test du groupe 3
La couche de revêtement de haute qualité cherche à avoir un petit taux de dilution et un grand rapport d'aspect. Les paramètres de processus optimaux sont: Current 99 A, vitesse de soudage 6 mm-S-1, vitesse d'alimentation du fil 50 mm-S-1. Le taux de dilution moyen de la couche de revêtement préparée dans le processus optimal est d'environ 14,6%, et le rapport d'aspect moyen est de 4,33, et l'erreur moyenne entre la valeur de prédiction du modèle et la valeur expérimentale est inférieure à 5%, ce qui indique que le modèle a un degré élevé de précision, et la qualité de la couche de revêtement formée sous le processus optimal est bonne.
Heure du poste: Jan-31-2024