Principe et introduction du revêtement laser
Processus de revêtement : Le revêtement laser peut être grossièrement divisé en deux catégories selon la méthode d'approvisionnement en matériaux de revêtement, à savoir le revêtement laser prédéfini et le revêtement laser synchrone.
Le revêtement laser pré-défini consiste à déposer le matériau de revêtement sur la surface du substrat, puis à utiliser un faisceau laser pour le scanner et le fondre. Le matériau de revêtement est ajouté sous forme de poudre ou de fil, la forme la plus couramment utilisée étant la poudre.
Le revêtement laser synchrone consiste à envoyer de la poudre ou du fil de revêtement dans le bain de fusion de manière synchrone via la buse pendant le processus de revêtement. Le matériau de revêtement est ajouté sous forme de poudre ou de fil, la poudre étant la forme la plus couramment utilisée.
Le processus principal du revêtement laser préréglé est le suivant : prétraitement de la surface du revêtement du substrat ---matériau de revêtement préréglé ---préchauffage ---revêtement laser ---post-traitement thermique.
Le flux de processus principal du revêtement laser synchrone est le suivant : prétraitement de la surface du revêtement du substrat --- préchauffage --- revêtement laser synchrone --- post-traitement thermique.
Selon le flux de processus, les processus liés au revêtement laser sont principalement la méthode de prétraitement de surface du substrat, la méthode d'alimentation en matériau de revêtement, le préchauffage et le post-traitement thermique.
Principe de fonctionnement du laser :
L'ensemble complet d'équipements de revêtement laser comprend : un laser, une unité de refroidissement, un mécanisme d'alimentation en poudre, une table de traitement, etc.
Sélection de lasers : les principaux types de lasers prennent en charge le processus de revêtement laser, tels que les lasers CO2, les lasers à solide, les lasers à fibre, les lasers à semi-conducteurs, etc.
Paramètres du processus
Les paramètres du procédé de placage laser comprennent principalement la puissance laser, le diamètre du spot, la vitesse de placage, la défocalisation, la vitesse d'alimentation en poudre, la vitesse de balayage et la température de préchauffage. Ces paramètres ont une influence considérable sur le taux de dilution de la couche de placage, les fissures, la rugosité de surface et la compacité des pièces plaquées. Ces paramètres s'influencent mutuellement, ce qui rend le procédé très complexe. Des méthodes de contrôle appropriées doivent être utilisées pour maintenir ces paramètres dans les limites autorisées du procédé de placage laser.
Le revêtement laser comporte 3 paramètres de processus importants
puissance laser
Plus la puissance laser est élevée, plus la quantité de métal de revêtement en fusion est importante et plus le risque de porosité est élevé. À mesure que la puissance laser augmente, la profondeur de la couche de revêtement augmente, le métal liquide environnant fluctue violemment et la solidification dynamique cristallise, réduisant progressivement le nombre de pores, voire leur élimination, et les fissures diminuent également. Lorsque la profondeur de la couche de revêtement atteint sa limite, la puissance laser augmente, entraînant une augmentation de la température de surface du substrat et une intensité accrue des phénomènes de déformation et de fissuration. Si la puissance laser est trop faible, seul le revêtement de surface fond, et non le substrat. Des fissures locales apparaissent alors à la surface de la couche de revêtement. Le boulochage, les vides, etc., empêchent le revêtement de surface d'atteindre son objectif.
Diamètre du spot
Le faisceau laser est généralement circulaire. La largeur de la couche de revêtement dépend principalement du diamètre du spot du faisceau laser ; plus le diamètre du spot augmente, plus la couche de revêtement s'élargit. Des tailles de spot différentes modifient la distribution d'énergie à la surface de la couche de revêtement, et la morphologie et les propriétés microstructurales obtenues sont très différentes. En général, la qualité de la couche de revêtement est meilleure lorsque la taille du spot est petite, et elle diminue à mesure que la taille du spot augmente. Cependant, un diamètre de spot trop petit ne permet pas d'obtenir une couche de revêtement de grande surface. [3]
Vitesse de placage
La vitesse de placage V a un effet similaire à la puissance laser P. Si la vitesse de placage est trop élevée,la poudre d'alliagene peut pas être complètement fondu et l'effet de revêtement de haute qualité n'est pas obtenu ; si la vitesse de revêtement est trop faible, le bain de fusion existe trop longtemps, la poudre est trop brûlée, les éléments d'alliage sont perdus et l'apport de chaleur de la matrice est important. augmentera la quantité de déformation.
Les paramètres de placage laser n'influencent pas indépendamment la qualité macroscopique et microscopique de la couche de placage, mais s'influencent mutuellement. Afin d'illustrer l'effet global de la puissance laser P, du diamètre du spot D et de la vitesse de placage V, le concept d'énergie spécifique Es est proposé, à savoir :
Es=P/(DV)
C'est-à-dire l'énergie d'irradiation par unité de surface et des facteurs tels que le laserdensité de puissanceet la vitesse de revêtement peuvent être considérées ensemble.
La réduction de l'énergie spécifique contribue à réduire le taux de dilution et est également liée à l'épaisseur de la couche de placage. À puissance laser constante, le taux de dilution de la couche de placage diminue avec l'augmentation du diamètre du spot. À vitesse et diamètre du spot constants, le taux de dilution augmente avec l'augmentation de la puissance du faisceau laser. De plus, avec l'augmentation de la vitesse de placage, la profondeur de fusion du substrat diminue, et le taux de dilution de la couche de placage diminue également.
Dans le revêtement laser multipasse, le taux de chevauchement est le principal facteur affectantla rugosité de la surfacede la couche de placage. Lorsque le taux de chevauchement augmente, la rugosité de la couche de placage diminue, mais l'uniformité de la partie chevauchée est difficile à garantir. La profondeur de la zone de chevauchement entre les pistes de placage diffère de la profondeur de leur centre, ce qui affecte l'uniformité de l'ensemble de la couche de placage. De plus, la contrainte de traction résiduelle du placage multipasse se superpose, ce qui augmente la contrainte totale locale et la sensibilité à la fissuration de la couche de placage. Le préchauffage et le revenu peuvent réduire la tendance à la fissuration de la couche de placage.
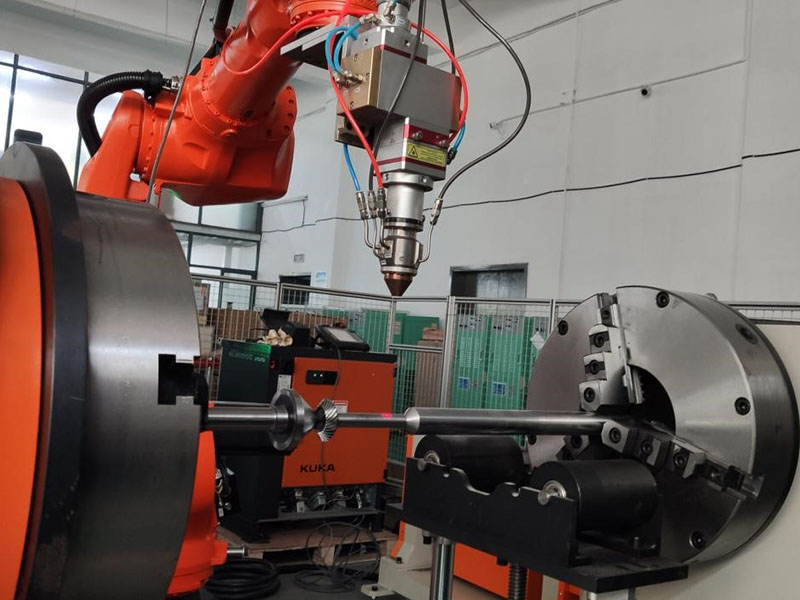
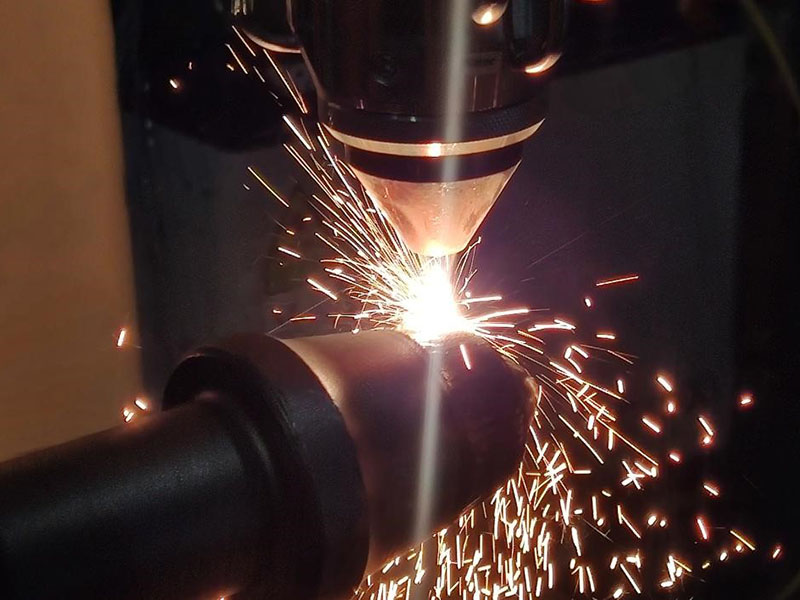
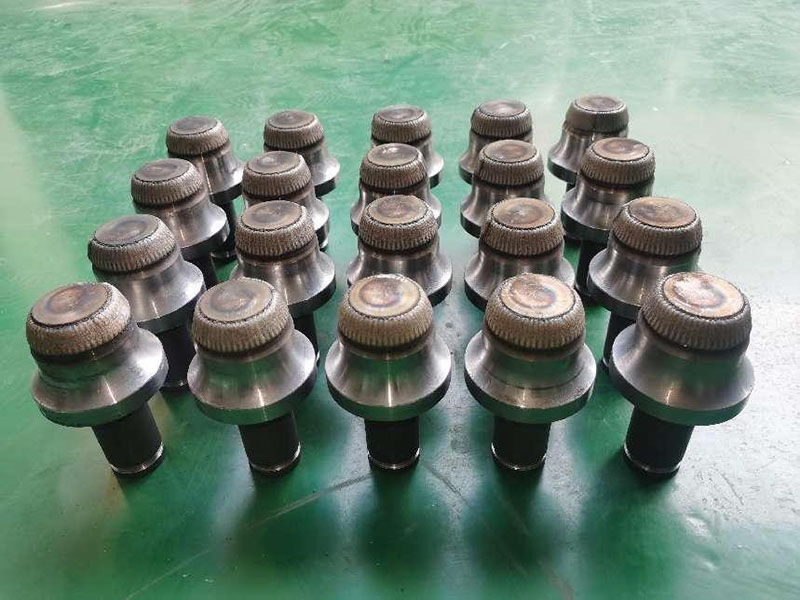
Date de publication : 15 août 2023