Le revêtement d'alésage est un procédé qui utilise une source de chaleur à haute énergie (par exemple,laser, plasma, faisceau d'électrons, etc.) pour faire fondre le matériau de revêtement et le déposer à la surface de l'alésage du substrat. Cette technologie permet d'améliorer considérablement la dureté, la résistance à l'usure et la résistance à la corrosion de la surface de l'alésage, prolongeant ainsi la durée de vie de l'équipement.
Questions fréquemment posées sur le revêtement des alésages
Bien que la technologie de revêtement interne des trous soit excellente pour améliorer les performances des équipements et prolonger leur durée de vie, elle pose encore des défis et des problèmes techniques lors de son application pratique. Voici quelques problèmes courants et leurs solutions pour le revêtement interne des trous :
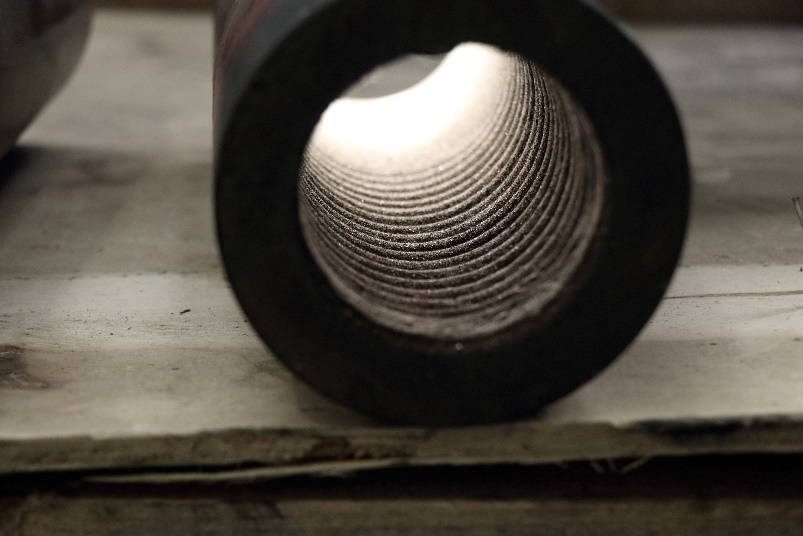
1. mauvaise uniformité de la couche de revêtement
Description du problème : Pendant le processus de fusion et de revêtement de l'alésage, un équipement ou un fonctionnement inapproprié peut entraîner une non-uniformité de l'épaisseur de la couche de revêtement, affectant ainsi les performances et la durée de vie de l'alésage.
Solution:
- Étalonnage de l'équipement : étalonnez régulièrement l'équipement de revêtement pour garantir une production d'énergie stable du laser, de l'arc plasma ou de l'arc électrique.
- Optimisation des paramètres du processus : Ajustez la vitesse de soudage, la vitesse d'alimentation du matériau de soudage, la puissance du laser ou de l'arc et d'autres paramètres pour garantir une couche de soudage uniforme.
- Revêtement multicouche : Adoptez un processus de revêtement multicouche, corrigez l'épaisseur couche par couche pour assurer l'uniformité de la couche de revêtement finale.
2. Adhérence insuffisante entre la couche de revêtement et le matériau de base
Description du problème : Si la liaison entre la couche de revêtement et le substrat n'est pas solide, la couche de revêtement peut s'écailler ou se décoller, affectant ainsi l'effet d'utilisation.
Solution:
- Prétraitement de surface : Nettoyer et prétraiter la surface du substrat avant le revêtement par fusion, comme le sablage, le meulage, etc., pour améliorer la rugosité de la surface et renforcer la force de liaison.
- Optimiser le matériau de revêtement : Sélectionner le matériau de revêtement avec une bonne compatibilité avec le matériau de base pour assurer une bonne combinaison entre les matériaux.
- Contrôler la température de fusion : Contrôler raisonnablement la température de fusion pour éviter qu'une température trop élevée ou trop basse n'affecte la force de liaison.
3. La zone affectée par la chaleur est trop grande
Description du problème : Un apport de chaleur excessif lors du revêtement interne du trou peut entraîner une zone affectée par la chaleur dans le substrat, provoquant une détérioration ou une déformation du matériau.
Solution:
- Contrôle de l'apport de chaleur : Réduisez l'impact de la chaleur sur le substrat en ajustant l'apport d'énergie du laser, de l'arc plasma ou de l'arc électrique.
- Système de refroidissement : utilisez un système de refroidissement approprié, tel que le refroidissement par eau ou par air, pour dissiper la chaleur à temps pendant le processus de fusion et de revêtement afin de réduire la température du substrat.
- Sélection du procédé approprié : Sélectionnez le procédé de fusion et de placage avec une zone affectée thermiquement plus petite en fonction de l'application spécifique, comme la fusion laser ou la projection à froid.
4. Difficulté d'utilisation du revêtement du trou interne
Description du problème : Le revêtement des trous internes est difficile à utiliser en raison des contraintes d'espace, en particulier pour les trous profonds ou les petits diamètres de trous, ce qui rend difficile de garantir la stabilité et la cohérence du processus.
Solution:
- Équipement de revêtement spécialisé : développer et utiliser des équipements de revêtement de trous internes spécialisés, tels qu'une tête de revêtement laser de trous internes, un système de revêtement robotisé, etc., pour améliorer la flexibilité et la précision de l'opération.
- Contrôle automatique : adopter un système de contrôle automatique pour réduire les erreurs de fonctionnement manuel et assurer la stabilité du processus de fusion et de revêtement.
- Optimisation du processus : déterminer les meilleurs paramètres du processus grâce à des tests et à une optimisation pour garantir la qualité du revêtement sous différents diamètres et profondeurs de trous.
5. Mauvaise sélection des matériaux de revêtement
Description du problème : Le matériau de revêtement sélectionné ne répond pas aux exigences de l'environnement d'utilisation, ce qui peut entraîner de mauvaises performances de la couche de revêtement, telles qu'une résistance à l'abrasion et à la corrosion insuffisantes.
Solution:
- Essais de matériaux : Effectuer des essais et des évaluations de matériaux avant le revêtement et sélectionner des matériaux de revêtement qui répondent aux exigences de l'environnement d'application.
- Optimisation des matériaux : Optimiser la composition du matériau de revêtement pour améliorer ses performances en fonction des besoins spécifiques.
- Consultation avec des experts : Travaillez avec des experts en matériaux ou des fournisseurs pour obtenir des conseils professionnels sur le choix des matériaux.
Procédé de revêtement de forage
Le développement et l'application de la technologie de fusion et de placage par trous internes sont prometteurs, mais les problèmes mentionnés ci-dessus doivent être surmontés en pratique. Grâce à l'amélioration continue des techniques et à l'optimisation des procédés, la fusion et le placage par trous internes répondront mieux aux besoins de l'industrie moderne et favoriseront l'innovation et le progrès du secteur manufacturier.
Date de publication : 27 juillet 2024