L'utilisation de la technologie de revêtement plasma pour renforcer la surface des forets PDC est un moyen efficace d'améliorer leur résistance à l'usure, leur résistance aux chocs et leur résistance à la corrosion.
1. Étape de préparation
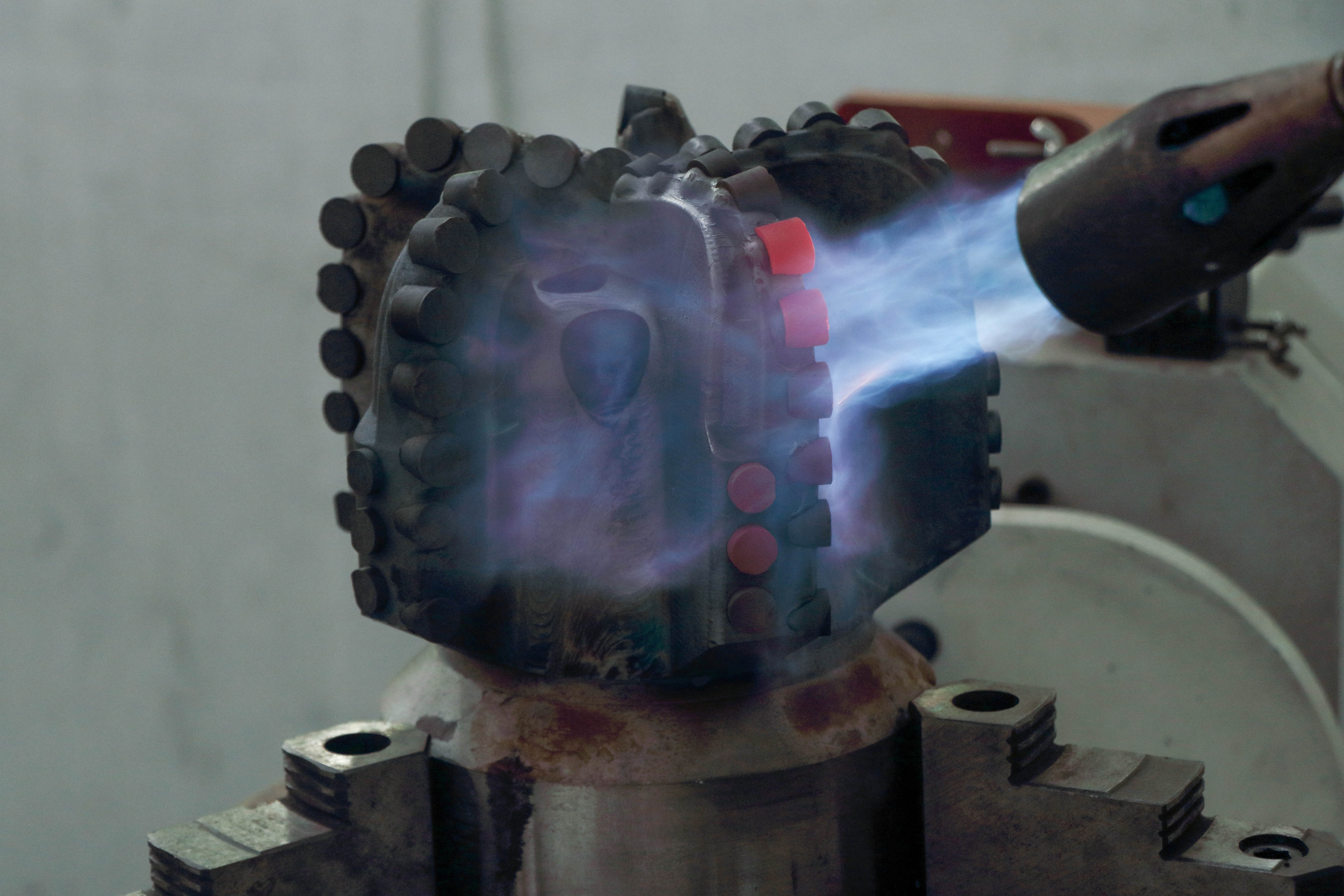
(1) Déterminer le matériau de revêtement
- Matériaux de revêtement couramment utilisés :
- Alliage à base de cobalt : haute résistance à l'usure et à la corrosion.
- Alliage à base de nickel : résistant à l'oxydation à haute température et à la corrosion chimique.
- Alliages à base de fer : économiques et adaptés aux exigences de résistance à l'usure moyenne.
- Alliages renforcés par des particules céramiques : par exemple WC (carbure de tungstène), TiC (carbure de titane), etc. pour des exigences de résistance à l'usure très élevées.
(2) Détermination de la surface de revêtement
- Le revêtement par fusion des trépans PDC cible généralement :
- Partie flanc : pour améliorer la résistance à l'usure et réduire les frottements et les pertes de coupe.
- La surface de la carcasse : pour améliorer la résistance globale à la corrosion et aux chocs.
(3) Prétraitement de surface
- Nettoyer la zone de revêtement pour éliminer l'huile, les oxydes, les revêtements et les impuretés.
- Traitement de meulage mécanique ou de sablage pour augmenter la rugosité de la surface et améliorer l'adhérence de la couche de revêtement fusionnée avec le substrat.
2. Mise en œuvre du procédé de revêtement
(1) Mise en place d'équipements de revêtement plasma
- Composition de l'équipement :
Pistolet de soudage plasma, distributeur de poudre, machine de soudage plasma automatisée, etc..
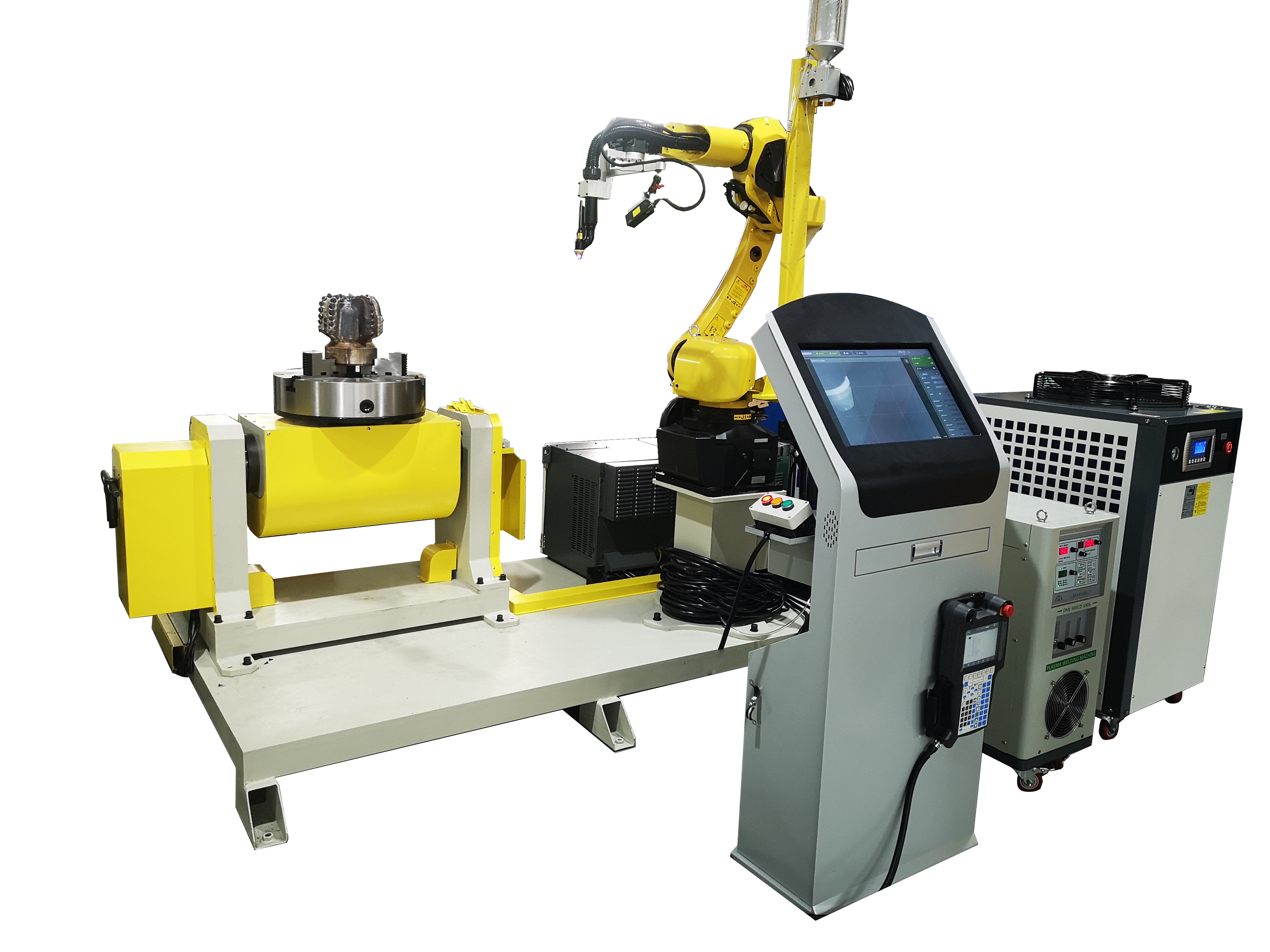
- Définir les paramètres clés :
- Courant et tension de l'arc : à choisir en fonction du matériau à revêtir, généralement dans la plage de 100 à 300 A.
- Apport de chaleur : ajuster pour contrôler la déformation du substrat et le taux de dilution.
- Débit d'alimentation en poudre : généralement compris entre 10 et 50 g/min pour assurer l'uniformité de la couche de revêtement.
(2) Exécution du bardage
- Le procédé de revêtement :
1. Démarrage de l'arc plasma, formation d'un bain de fusion à haute température.
2. Grâce au système d'alimentation en poudre, le matériau en poudre est pulvérisé dans le bain de fusion et lié métallurgiquement au substrat.
3. Selon la forme du foret, le long du chemin défini pour un revêtement uniforme, pour garantir qu'il n'y a pas de fuite de revêtement ou de surfusion.
- Contrôle de l'influence thermique : évitez la surchauffe ou la déformation du substrat du foret PDC en ajustant les paramètres de l'arc plasma et la méthode de refroidissement.
(3) Traitement de refroidissement
- Refroidissement naturel ou adoption d'une méthode de refroidissement à vitesse contrôlée pour éviter les fissures causées par le stress thermique.
3. Étape post-traitement
(1) Contrôle de la qualité du revêtement
- Contrôle de l'apparence : Observer si la couche de revêtement est uniforme, exempte de fissures et de trous d'air.
- Test de performance : mesure de la dureté, de l'épaisseur (généralement de 0,5 à 3 mm), de la force de liaison et d'autres indicateurs.
- Contrôles non destructifs : utilisez des contrôles par ultrasons ou par rayons X pour résoudre les défauts internes.
(2) Finition
- Si la surface est rugueuse après le revêtement par fusion, un traitement de tournage ou de meulage est nécessaire pour répondre aux exigences de taille et de forme des forets PDC.
(3) Optimisation des performances
- Traitement thermique : tremper ou revenu la couche de placage fondue si nécessaire pour optimiser davantage ses propriétés organisationnelles.
4. Précautions
1. Évitez les dommages dus à la surchauffe
- Lors du revêtement plasma, l'apport de chaleur doit être strictement contrôlé pour éviter tout dommage thermique à l'insert PDC et au substrat.
2. Correspondance des matériaux
- Le matériau de revêtement doit être adapté au matériau du substrat du trépan PDC pour garantir la force de liaison et la cohérence des performances.
3. Contrôle environnemental
- Dans la mesure du possible dans un environnement à faible humidité ou sous gaz protecteur pour éviter l'oxydation affectant la qualité du revêtement.
Ce procédé peut être utilisé pour améliorer les performances des nouveaux embouts PDC ainsi que pour réparer les embouts usés.
Date de publication : 09/01/2025