Con el continuo desarrollo de la tecnología de fabricación, la tecnología de revestimiento por soldadura se ha convertido en un método importante para mejorar el rendimiento de los materiales metálicos. Elegir el...polvo de revestimiento de soldaduraNo solo mejora la resistencia al desgaste, la corrosión y la fatiga del material, sino que también prolonga la vida útil del equipo. Este artículo analizará en detalle los tipos de polvos de revestimiento de soldadura, sus principios de selección y su aplicación en la industria.
1. Definición y clasificación del polvo de revestimiento de soldadura
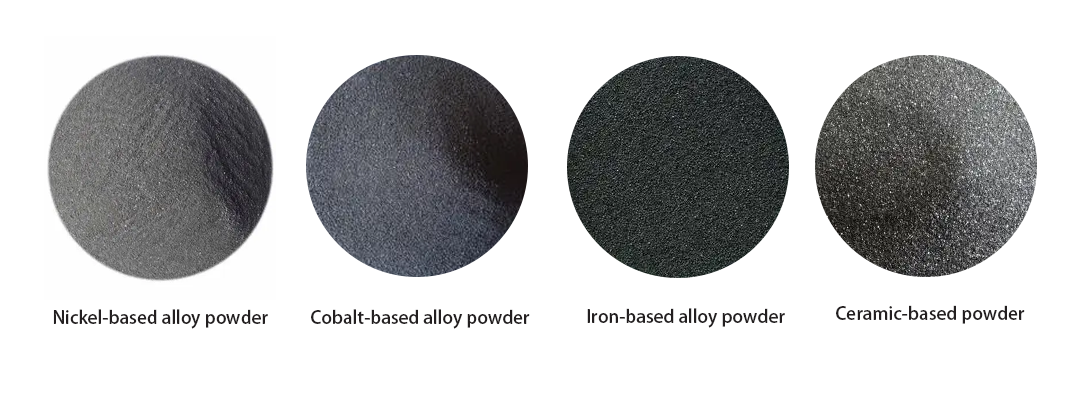
Diagramas 1Máquina de soldadura láser&máquina de soldadura de plasma
El polvo de revestimiento para soldadura es un material utilizado para la modificación y reparación de superficies. Se funde y se deposita sobre la superficie del material base mediante una fuente de calor para formar una capa de revestimiento con propiedades específicas. Según su composición química y uso, los polvos de revestimiento para soldadura se clasifican principalmente en las siguientes categorías:
- Polvo de aleación a base de níquel: con excelente resistencia a altas temperaturas y corrosión, se utiliza comúnmente en entornos de alta temperatura y alta presión, como álabes de turbinas de gas y equipos químicos.
- Polvo de aleación a base de cobalto: con excelente resistencia al desgaste, resistencia a la corrosión y resistencia a la oxidación a altas temperaturas, ampliamente utilizado en válvulas, moldes y otras piezas de alto desgaste.
- Polvo de aleación a base de hierro: relativamente económico, adecuado para requisitos generales de resistencia al desgaste y la corrosión, comúnmente utilizado en equipos de minería, maquinaria agrícola, etc.
- Polvo a base de cerámica: se utiliza principalmente para mejorar la resistencia al desgaste del material, como óxido de aluminio, carburo de tungsteno, etc., adecuado para aplicaciones en condiciones de desgaste extremas.
2. Principios para la selección de polvos de revestimiento para soldadura
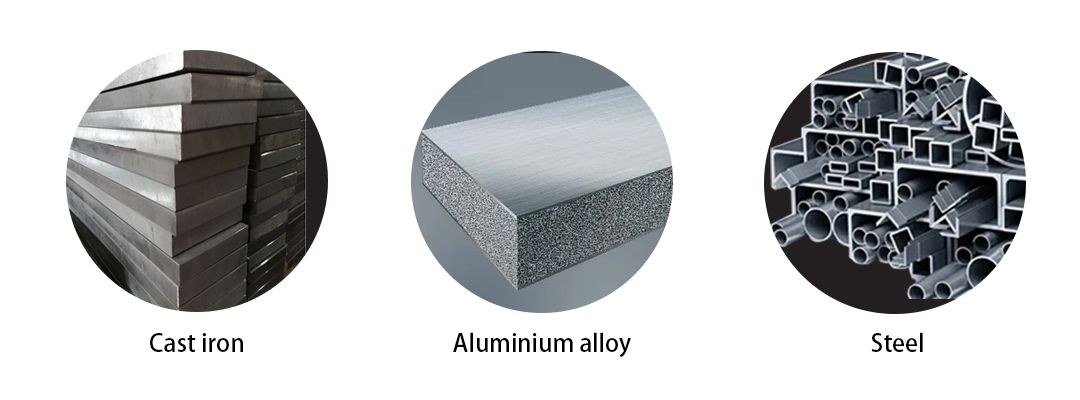
Diagramas 2 Material base
Seleccionar el polvo de revestimiento de soldadura adecuado es fundamental para garantizar la calidad de la capa de revestimiento. A continuación, se presentan varios factores importantes a considerar al seleccionar el polvo de revestimiento de soldadura:
- Propiedades del material base: diferentes materiales base (como acero, hierro fundido, aleaciones de aluminio, etc.) tienen diferentes requisitos de compatibilidad para el polvo de revestimiento, es necesario elegir el polvo adecuado de acuerdo con las propiedades físicas y químicas del material base.
- Ambiente de trabajo: Teniendo en cuenta la temperatura de trabajo de la capa de revestimiento, el tipo de desgaste, los medios corrosivos y otros factores, elija el tipo de polvo que pueda satisfacer las necesidades de un ambiente de trabajo específico.
- Proceso de recubrimiento: los diferentes procesos de recubrimiento (como recubrimiento láser, pulverización de plasma, pulverización con llama oxiacetilénica, etc.) tienen diferentes requisitos en cuanto al tamaño de partícula del polvo, la morfología y la movilidad, y deben basarse en el proceso específico para seleccionar el polvo apropiado.
- Rentabilidad: Bajo la premisa de cumplir con los requisitos de rendimiento, se debe considerar integralmente la economía del polvo y se debe seleccionar el material rentable.
3. Aplicaciones del polvo de revestimiento de soldadura en la industria
3.1 Campo petroquímico
En el sector petroquímico, los equipos suelen estar expuestos a altas temperaturas, altas presiones y medios corrosivos. Por ello, el polvo de aleación a base de níquel se ha convertido en el material predilecto para la reparación de equipos petroquímicos gracias a su excelente resistencia a la corrosión. El proceso de revestimiento permite mejorar considerablemente la durabilidad de los equipos, prolongando su vida útil y reduciendo el tiempo de inactividad y los costos de mantenimiento.
3.2 Aeroespacial
La industria aeroespacial exige materiales ligeros y de alta resistencia, así como resistencia a altas temperaturas. Gracias a su excelente rendimiento a altas temperaturas, el polvo de aleación a base de cobalto se utiliza habitualmente en la reparación y el refuerzo de superficies de piezas de motores aeronáuticos para garantizar un funcionamiento fiable en entornos extremos.
3.3 Fabricación mecánica
En la industria de fabricación mecánica, los polvos de revestimiento se utilizan ampliamente para reparar y mejorar el rendimiento de piezas mecánicas. Gracias a su bajo costo y buena resistencia al desgaste, el polvo de aleación a base de hierro se utiliza comúnmente para reparar piezas desgastadas de maquinaria agrícola, equipos de minería, etc., lo que mejora considerablemente la eficiencia de uso y la vida útil del equipo.
3.4 Industria automotriz
En la industria automotriz, los motores, las transmisiones y otros componentes clave requieren alta resistencia al desgaste y a la corrosión. El revestimiento superficial con polvos cerámicos puede mejorar significativamente el rendimiento de las piezas, prolongar su vida útil y reducir los costos de mantenimiento.
4. Perspectivas futuras
Con el continuo avance de la ciencia y la tecnología, las perspectivas de aplicación del polvo de revestimiento de soldadura en la ciencia y la fabricación de materiales serán más amplias. En el futuro, el desarrollo de polvos de revestimiento más diversificados y funcionalizados se convertirá en tendencia. Mediante la combinación de materiales innovadores y la tecnología avanzada de revestimiento por fusión, se mejorará aún más el rendimiento del material, lo que contribuirá significativamente al desarrollo sostenible de diversas industrias.
Para obtener más información, por favorContáctanos!
Descargo de responsabilidad: La información proporcionada aquí es solo para referencia, seleccione y ajuste según la aplicación real.
Nota: Si desea reimprimir este artículo, indique la fuente.
Hora de publicación: 04-jul-2024