1.1 El efecto de la corriente en el moldeo de lacapa de revestimiento
Actual(A) | Dprofundidad (de fusión)(mm) | Faltura del piso(mm) | ancho(mm) |
70 | 0,19 | 4.26 | 16.41 |
80 | 0.35 | 4.07 | 17.08 |
90 | 0.88 | 3.43 | 17.48 |
100 | 1.03 | 2.73 | 17.58 |
110 | 1.25 | 2.65 | 18.14 |
Tabla 3.1 Geometría de la sección transversal de la capa de revestimiento con diferentes corrientes
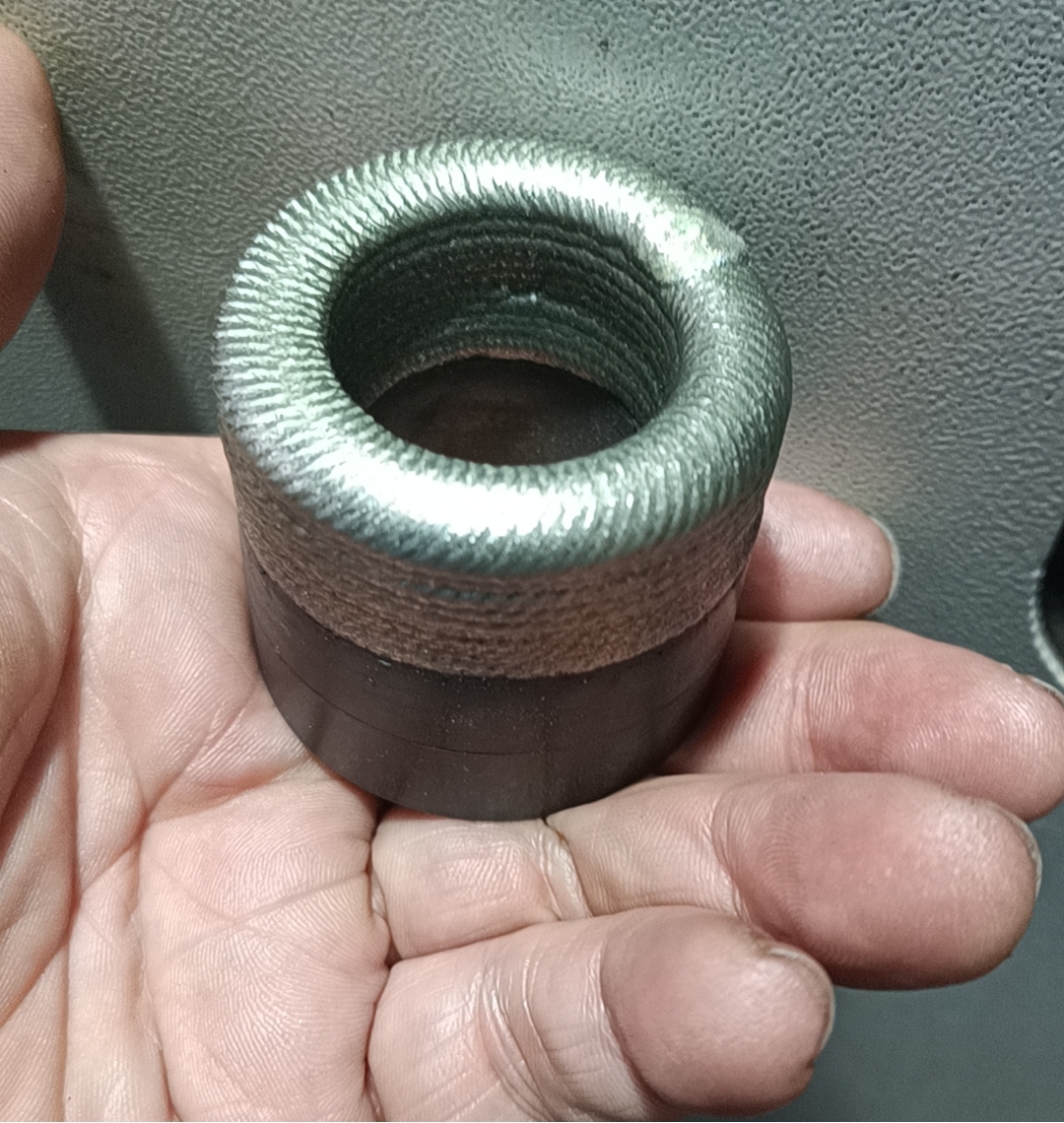
A medida que aumenta la corriente, la profundidad y el ancho de la capa de revestimiento aumentan, mientras que su altura disminuye. Esto se debe a que el calor generado no solo funde el metal del revestimiento, sino que también se funde parte del sustrato, lo que provoca la mezcla entre el revestimiento y el sustrato. Esto provoca la subsidencia de la capa de revestimiento, lo que aumenta la profundidad de fusión y disminuye la altura de la capa. Al aumentar la corriente, el arco de plasma es más grueso y el rango de temperatura de la fuente de calor aumenta, lo que aumenta la capacidad de expansión del baño de fusión en el sustrato y, por lo tanto, su ancho.
1.2 El efecto desoldaduraVelocidad en el moldeo de la capa de revestimiento fundido
Velocidad de soldadura(mm/s) | Dprofundidad (de fusión)(mm) | Faltura del piso(mm) | ancho(mm) |
4 | 1.17 | 4.34 | 17.61 |
5 | 1.06 | 2.73 | 17.58 |
6 | 0.35 | 2.61 | 16.96 |
7 | 0.13 | 2.55 | 15.01 |
8 | — | — | — |
Tabla 3.2 Geometría de la sección transversal de las capas de revestimiento fundido con diferentes velocidades de soldadura
Con el aumento de la velocidad de soldadura, la profundidad de fusión de la capa de revestimiento disminuye, la altura de la capa muestra primero una disminución brusca y luego se vuelve más pequeña lentamente, el ancho disminuye. Cuando la velocidad de soldadura es de 4 mm/s, con el aumento del metal de revestimiento hasta cierto punto, la profundidad de fusión es de 1,17 mm, en este momento, el aporte de calor por unidad de longitud no puede hacer que el material base se funda más, la capa de revestimiento de fusión continúa acumulándose la altura de la capa de 4,34 mm; la velocidad de soldadura aumenta a 5 mm/s, el aporte de calor por unidad de longitud, la cantidad de alimentación de alambre se reducen, por lo que la profundidad de fusión, la altura de la capa, el ancho se reducen; si la velocidad de soldadura continúa aumentando, como se mencionó anteriormente, el aporte de calor es insuficiente en este momento, solo una pequeña parte del material base puede fundirse, la altura de la capa de revestimiento de fusión muestra primero una disminución brusca y luego se vuelve más pequeña lentamente, el ancho se reduce. Si la velocidad de soldadura continúa aumentando, como se mencionó anteriormente, la entrada de calor en este momento es insuficiente, solo se puede fundir una pequeña parte del material base, la capa de revestimiento de fusión no parece combarse, lo que resulta en una mayor reducción en la profundidad de fusión, mientras que la altura de la capa se reduce menos.
1.3 Influencia de la velocidad de alimentación del alambre en el moldeo de la capa de revestimiento
Alimentación de alambre acelerada(mm/s) | Dprofundidad (de fusión)(mm) | Faltura del piso(mm) | ancho(mm) |
40 | 1.43 | 2.24 | 19.91 |
50 | 1.25 | 2.56 | 18.86 |
60 | 1.03 | 2.73 | 17.58 |
70 | 0,71 | 3.46 | 15.82 |
80 | 0.16 | 5.16 | 14.20 |
Tabla 3.3 Dimensiones geométricas de la sección transversal de la capa de revestimiento con diferentes velocidades de alimentación de alambre.
A medida que aumenta la velocidad de alimentación del alambre, la profundidad y el ancho de la capa de revestimiento disminuyen, mientras que su altura aumenta. Esto se debe a que, cuando la corriente y la velocidad de soldadura son constantes, el aporte de calor por unidad de longitud también lo es. Al aumentar la velocidad de alimentación del alambre, aumenta la cantidad de alambre de relleno por unidad de longitud, lo que obliga al metal de revestimiento a absorber más calor. Cuando el aporte de calor no logra fundir completamente la capa de revestimiento, la parte del material base se funde menos, por lo que la profundidad de fusión disminuye, la altura de la capa aumenta y la capacidad de expansión del metal de revestimiento cerca de la parte del material base se deteriora, lo que provoca una rápida disminución del ancho.
En resumen, los parámetros del proceso efectivo de revestimiento de arco de plasma con capa de acero inoxidable dúplex 2205 varían de: corriente 90 A ~ 110 A, velocidad de soldadura 4 mm/s ~ 6 mm/s, velocidad de alimentación de alambre 50 mm/s ~ 70 mm/s, caudal de gas iónico de 1,5 L/min.
2 Basado en el método de superficie de respuesta de la optimización de los parámetros del proceso de formación de la capa de revestimiento de fusión
El método de superficie de respuesta (Método de superficie de respuesta, MRS) combina el diseño experimental con técnicas estadísticas de optimización. El análisis de los datos de prueba, derivado del factor de impacto y el valor de respuesta de la función de ajuste y el mapa tridimensional de la superficie, refleja intuitivamente la relación entre el factor de impacto y el valor de respuesta de la prueba real, lo que tiene un papel predictivo y de optimización. Por estas razones, se ha seleccionado el MRS en el diseño compuesto central (DCC) para desarrollar un programa de optimización de procesos, con el fin de explorar la corriente, la velocidad de soldadura, la velocidad de alimentación del alambre y la tasa de dilución de la capa de revestimiento de fusión, la relación de aspecto de la relación entre la corriente, la velocidad de soldadura, la velocidad de alimentación del alambre y la tasa de dilución de la capa de revestimiento de fusión, y el modelado matemático, derivado de los parámetros del proceso, la tasa de dilución y la relación de aspecto de la función, para predecir la calidad de la capa de revestimiento de fusión.
2.1 Influencia de los parámetros del proceso en la tasa de dilución de la capa de revestimiento.
Tabla 3.8 Resultados de optimización de procesos y verificación
Grupo | X1(A) | X2(mm·s-1) | X3(mm·s-1) | relación de dilución(%) | relación de aspecto |
Grupo de predicción | 99 | 6 | 50 | 14.8 | 4.36 |
Grupo de prueba 1 | 99 | 6 | 50 | 13.9 | 4.13 |
Grupo de prueba 2 | 99 | 6 | 50 | 15.5 | 4.56 |
Grupo de prueba 3 | 99 | 6 | 50 | 14.3 | 4.27 |
Error promedio | 2.9 | 2.3 |
(Soldadura PTA de Shanghai Duomu)
Figura 3.16 Resultados de la prueba de parámetros óptimos del proceso (a) Grupo de prueba 1; (b) Grupo de prueba 2; (c) Grupo de prueba 3
Una capa de revestimiento de alta calidad busca una tasa de dilución baja y una relación de aspecto amplia. Los parámetros óptimos del proceso son: corriente de 99 A, velocidad de soldadura de 6 mm-s⁻¹ y velocidad de alimentación del alambre de 50 mm-s⁻¹. La tasa de dilución promedio de la capa de revestimiento preparada con el proceso óptimo es de aproximadamente el 14,6 %, la relación de aspecto promedio es de 4,33 y el error promedio entre el valor de predicción del modelo y el valor experimental es inferior al 5 %, lo que indica una alta precisión del modelo y una buena calidad de la capa de revestimiento formada con el proceso óptimo.
Hora de publicación: 31 de enero de 2024