En la industria papelera, la confiabilidad y durabilidad de los equipos de producción afectan directamente la productividad y los costos operativos de una organización. Como uno de los componentes principales de...maquinaria de papel, eltornilloDesempeña un papel vital en el proceso de transferencia y mezcla de pulpa. Sin embargo, las espirales suelen estar expuestas a entornos operativos hostiles, altamente abrasivos y corrosivos, y presentan un riesgo extremadamente alto de desgaste. Para solucionar este problema, se ha desarrollado una tecnología de revestimiento de superficies que mejora significativamente la resistencia al desgaste y la corrosión de las piezas de la espiral al proporcionarles una sólida capa protectora, prolongando así la vida útil del equipo.
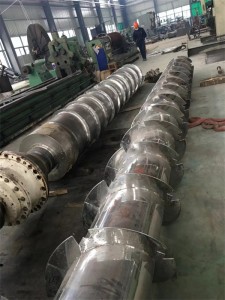
La importancia del revestimiento en espiral
En la línea de producción de papel, las piezas espirales son responsables de la transmisión de pulpa y fibra, y a la vez, de la pulpa para su mezcla. Durante este proceso, la espiral se ve expuesta a partículas abrasivas presentes en la pulpa, a un ambiente de alta humedad y a la erosión química, lo que provoca un rápido desgaste superficial y corrosión. Si no se realiza el mantenimiento y la sustitución a tiempo, una espiral desgastada no solo reducirá la eficiencia operativa del equipo, sino que también puede provocar un estancamiento de la producción, lo que acarrea importantes pérdidas económicas para la empresa.
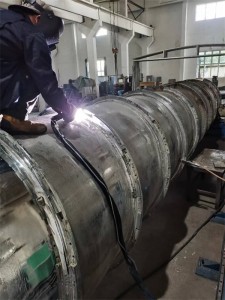
La tecnología de revestimiento de superficies mejora significativamente la vida útil y el rendimiento de las espirales al depositar una capa de aleación resistente al desgaste y a la corrosión sobre la superficie de la espiral para formar una sólida capa protectora. Este proceso proporciona a las empresas papeleras soluciones eficaces para el mantenimiento de sus equipos, reduciendo el tiempo de inactividad y los costos de mantenimiento por fallas, mejorando así la eficiencia general de la producción.
Aplicación y ventajas de la tecnología de revestimiento
La aplicación de la tecnología de revestimiento de superficies en espiral implica diversos aspectos clave, como la selección de materiales, el proceso de revestimiento y el control de calidad. Según las diferentes necesidades del proceso de fabricación de papel, los materiales de revestimiento más utilizados incluyen aleaciones con alto contenido de cromo, aleaciones a base de níquel y carburo de tungsteno. Estos materiales no solo ofrecen una excelente resistencia al desgaste y a la corrosión, sino que también mantienen un rendimiento estable en condiciones de alta temperatura y alta presión.

● Mayor resistencia al desgaste: El desgaste en el proceso de fabricación de papel se debe principalmente a las partículas abrasivas presentes en la pulpa y a la fricción producida por la rotación a alta velocidad. Al revestir con materiales de alta dureza, la resistencia al desgaste de la superficie de la espiral se mejora considerablemente, lo que permite resistir eficazmente la erosión de las partículas abrasivas y mantener la eficiencia de la espiral.
● Mayor resistencia a la corrosión: Los productos químicos utilizados en la fabricación de papel, como la lejía y las soluciones ácidas, tienen un fuerte efecto corrosivo sobre la superficie de la espiral. La alta resistencia a la corrosión del material de revestimiento permite que la espiral funcione de forma estable durante un largo periodo de tiempo en un medio corrosivo y reduce las fallas del material y las paradas del equipo causadas por la corrosión.
● Prolongación de la vida útil: El proceso de revestimiento prolonga la vida útil de la espiral al cubrir uniformemente su superficie con el material de aleación, formando una densa capa protectora. Esto no solo reduce la necesidad de reemplazo frecuente de equipos, sino que también reduce significativamente los costos operativos de la organización.
Reparación y remanufactura: La tecnología de revestimiento también se aplica a piezas espirales desgastadas. Mediante el proceso de revestimiento, las piezas desgastadas de la superficie espiral pueden repararse y restaurarse a sus dimensiones y rendimiento originales, prolongando la vida útil del equipo y evitando el alto costo de reemplazarlas por piezas nuevas.
Proceso de tecnología de superficies y control de calidad
El revestimiento de superficies en espiral es un proceso complejo que consta de múltiples etapas, como el pretratamiento de la superficie, la selección del material de revestimiento, el control del proceso de revestimiento y el tratamiento posterior. Un control estricto de cada etapa es crucial para garantizar la calidad y la estabilidad de la capa superficial.
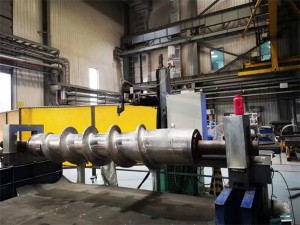
● Pretratamiento de la superficie: Antes del revestimiento, el pretratamiento de la superficie espiral es un paso clave. Primero, es necesario limpiar la superficie espiral para eliminar capas de óxido, aceites y otras impurezas, garantizando así una adhesión firme del material de revestimiento al material base. Los métodos de pretratamiento más comunes incluyen el arenado, el pulido y la limpieza química.
Selección del material de recubrimiento: Según los requisitos específicos de la espiral en el proceso de fabricación de papel, es crucial seleccionar el material de recubrimiento adecuado. Las diferentes aleaciones tienen distinta dureza, resistencia a la abrasión y a la corrosión, por lo que es necesario elegir el material adecuado según el entorno de trabajo y la carga de la espiral. Por ejemplo, una aleación con alto contenido de cromo es adecuada para entornos de alta abrasión, una aleación con base de níquel es adecuada para entornos corrosivos y de alta temperatura, y el carburo de tungsteno es adecuado para requisitos de resistencia al desgaste extremo.
Control del proceso de revestimiento: El control de temperatura, la velocidad de soldadura, el material de relleno y otros parámetros del proceso de revestimiento afectan directamente la calidad de la capa. Los equipos de revestimiento modernos suelen estar equipados con sistemas de control automatizados que ajustan con precisión estos parámetros para garantizar la uniformidad y densidad de la capa de revestimiento y evitar defectos como porosidad y grietas.
Tratamiento posterior: Tras finalizar el revestimiento, suele ser necesario realizar tratamientos posteriores, como el rectificado superficial y el tratamiento térmico, para eliminar la tensión y mejorar la adherencia y la dureza de la capa de revestimiento. El rectificado permite que la superficie espiral alcance la suavidad requerida, reduciendo así la resistencia a la fricción durante el funcionamiento. El tratamiento térmico puede mejorar la estructura organizativa de la capa de revestimiento y optimizar su rendimiento integral.
Inspección de calidad: Tras el revestimiento, la espiral debe someterse a una rigurosa inspección de calidad, que incluye ensayos no destructivos, pruebas de microdureza y medición del espesor del recubrimiento, entre otros, para garantizar que la uniformidad, la densidad y el rendimiento de la capa de revestimiento cumplan con los requisitos de diseño. Estos métodos de prueba permiten detectar eficazmente posibles defectos durante el proceso de revestimiento y garantizar la calidad estable y fiable de cada componente de la espiral.
Desarrollo de la industria y tendencias futuras
Con el rápido desarrollo de la ciencia de los materiales, la tecnología de soldadura y los equipos automatizados, la tecnología de soldadura por superposición de superficies en espiral también está avanzando. En la altamente competitiva industria papelera actual, las empresas exigen cada vez más rendimiento y vida útil de sus equipos, lo que impulsa el desarrollo de la tecnología de revestimiento para lograr una mayor eficiencia y precisión.
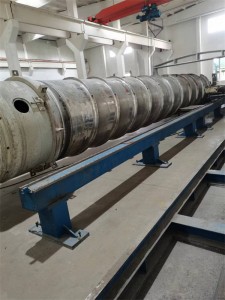
● Aplicación de nuevos materiales: En el futuro, con el avance de la ciencia de los materiales, se desarrollarán y aplicarán más materiales de revestimiento nuevos, como los nanocompuestos y los compuestos de matriz cerámica. Estos materiales no solo ofrecen mayor resistencia al desgaste y a la corrosión, sino que también mantienen un rendimiento estable en condiciones de trabajo extremas para cumplir con los exigentes requisitos del entorno de producción.
● Automatización y Desarrollo Inteligente: Con el desarrollo de la Industria 4.0, la tecnología de revestimiento está incorporando gradualmente la automatización y la inteligencia. Los equipos de revestimiento modernos están equipados con sistemas avanzados de control de automatización que permiten la monitorización y el ajuste en tiempo real del proceso, mejorando así la eficiencia de la producción y la estabilidad de la calidad. En el futuro, la introducción de la inteligencia artificial y el aprendizaje automático optimizará aún más los parámetros del proceso de revestimiento y mejorará la flexibilidad y la precisión de la producción.
Fabricación ecológica y desarrollo sostenible: En el contexto de los crecientes requisitos de protección ambiental, la tecnología de revestimiento también se está desarrollando hacia la fabricación ecológica. La aplicación de materiales de revestimiento ecológicos y procesos de bajo consumo energético no solo reduce el consumo energético y la contaminación en el proceso de revestimiento, sino que también promueve el desarrollo sostenible de la industria papelera. En el futuro, se introducirán tecnologías y materiales más respetuosos con el medio ambiente en el proceso de revestimiento, lo que contribuirá a la transformación ecológica de la industria.
Innovación en tecnología de reparación: Con la prolongación de la vida útil de los equipos, la demanda de reparación de piezas espirales aumentará gradualmente. La futura tecnología de reparación de revestimientos priorizará la eficiencia y la calidad. Gracias a tecnología y equipos más avanzados, se podrá restaurar el rendimiento de la espiral con rapidez y precisión, reduciendo así los costos de mantenimiento.
Hora de publicación: 24 de agosto de 2024