Principio e introducción del revestimiento láser
Proceso de revestimiento: El revestimiento láser se puede dividir aproximadamente en dos categorías según el método de suministro de materiales de revestimiento, a saber, revestimiento láser preestablecido y revestimiento láser sincrónico.
El revestimiento láser preajustado consiste en colocar el material de revestimiento sobre la superficie del sustrato con antelación y, posteriormente, utilizar la irradiación láser para escanearlo y fundirlo. El material de revestimiento se añade en forma de polvo o alambre, siendo el polvo el más común.
El revestimiento láser síncrono consiste en enviar materiales de revestimiento en polvo o alambre al baño de fusión de forma sincronizada a través de la boquilla durante el proceso. El material de revestimiento se añade en forma de polvo o alambre, siendo el polvo el más común.
El proceso principal del revestimiento láser preestablecido es: pretratamiento de la superficie del revestimiento del sustrato --- material de revestimiento preestablecido --- precalentamiento --- revestimiento láser --- tratamiento térmico posterior.
El flujo del proceso principal del revestimiento láser sincrónico es: pretratamiento de la superficie del revestimiento del sustrato, precalentamiento, revestimiento láser sincrónico y tratamiento térmico posterior.
Según el flujo del proceso, los procesos relacionados con el revestimiento láser son principalmente el método de pretratamiento de la superficie del sustrato, el método de alimentación del material de revestimiento, el precalentamiento y el tratamiento térmico posterior.
Principio de funcionamiento del láser:
El conjunto completo del equipo de revestimiento láser consta de: láser, unidad de enfriamiento, mecanismo de alimentación de polvo, mesa de procesamiento, etc.
Selección de láseres: los principales tipos de láser admiten el proceso de revestimiento láser, como láseres de CO2, láseres de estado sólido, láseres de fibra, láseres semiconductores, etc.
Parámetros del proceso
Los parámetros del proceso de revestimiento láser incluyen principalmente la potencia del láser, el diámetro del punto, la velocidad de revestimiento, la cantidad de desenfoque, la velocidad de alimentación del polvo, la velocidad de escaneo, la temperatura de precalentamiento, etc. Estos parámetros tienen una gran influencia en la tasa de dilución de la capa de revestimiento, la aparición de grietas, la rugosidad superficial y la compacidad de las piezas revestidas. Estos parámetros también se influyen entre sí, lo que constituye un proceso muy complejo, por lo que se deben utilizar métodos de control razonables para mantenerlos dentro del rango admisible del proceso de revestimiento láser.
El revestimiento láser tiene 3 parámetros de proceso importantes
potencia del láser
Cuanto mayor sea la potencia del láser, mayor será la cantidad de metal de revestimiento fundido y mayor la probabilidad de porosidad. A medida que aumenta la potencia del láser, aumenta la profundidad de la capa de revestimiento, el metal líquido circundante fluctúa violentamente y la solidificación dinámica cristaliza, de modo que el número de poros se reduce gradualmente o incluso se elimina, y las grietas también se reducen gradualmente. Cuando la profundidad de la capa de revestimiento alcanza la profundidad límite, a medida que aumenta la potencia, la temperatura superficial del sustrato aumenta y el fenómeno de deformación y agrietamiento se intensifica. Si la potencia del láser es demasiado baja, solo se funde el revestimiento superficial y el sustrato no. En este momento, se producen grietas locales en la superficie de la capa de revestimiento. La formación de bolitas, huecos, etc., no logra el propósito del revestimiento de la superficie.
Diámetro del punto
El haz láser es generalmente circular. El ancho de la capa de revestimiento depende principalmente del diámetro del punto láser; este aumenta y la capa de revestimiento se ensancha. Diferentes tamaños de punto provocan cambios en la distribución de energía en la superficie de la capa de revestimiento, y la morfología y las propiedades microestructurales obtenidas varían considerablemente. En general, la calidad de la capa de revestimiento es mejor cuando el tamaño del punto es pequeño, y disminuye a medida que aumenta. Sin embargo, un diámetro de punto demasiado pequeño impide obtener una capa de revestimiento de gran superficie. [3]
Velocidad de revestimiento
La velocidad de revestimiento V tiene un efecto similar a la potencia del láser P. Si la velocidad de revestimiento es demasiado alta,el polvo de aleaciónno se puede fundir completamente y no se logra el efecto de revestimiento de alta calidad; si la velocidad de revestimiento es demasiado baja, el baño de fusión existe durante demasiado tiempo, el polvo se quema demasiado, los elementos de aleación se pierden y la entrada de calor de la matriz es grande. aumentará la cantidad de deformación.
Los parámetros del revestimiento láser no afectan de forma independiente la calidad macroscópica y microscópica de la capa de revestimiento, sino que se influyen mutuamente. Para ilustrar el efecto integral de la potencia láser P, el diámetro del punto D y la velocidad de revestimiento V, se propone el concepto de energía específica Es, a saber:
Es=P/(DV)
Es decir, la energía de irradiación por unidad de área y factores como el láser.densidad de potenciay la velocidad del revestimiento se pueden considerar en conjunto.
La reducción de la energía específica favorece la disminución de la tasa de dilución y también guarda cierta relación con el espesor de la capa de revestimiento. Con una potencia láser constante, la tasa de dilución de la capa de revestimiento disminuye al aumentar el diámetro del punto, mientras que, cuando la velocidad y el diámetro del punto de revestimiento se mantienen constantes, la tasa de dilución de la capa de revestimiento aumenta con el aumento de la potencia del haz láser. Además, al aumentar la velocidad de revestimiento, disminuye la profundidad de fusión del sustrato y, por lo tanto, la tasa de dilución de la capa de revestimiento respecto al material del sustrato.
En el revestimiento láser de múltiples pasadas, la tasa de superposición es el factor principal que afectala rugosidad de la superficieDe la capa de revestimiento. Al aumentar la tasa de solapamiento, la rugosidad superficial de la capa disminuye, pero es difícil garantizar la uniformidad de la parte solapada. La profundidad del área de solapamiento entre las pistas de revestimiento difiere de la profundidad del centro de las pistas, lo que afecta la uniformidad de toda la capa. Además, la tensión de tracción residual del revestimiento multicapa se superpone, lo que aumenta la tensión total local y la sensibilidad de la capa de revestimiento a las grietas. El precalentamiento y el revenido pueden reducir la tendencia de la capa de revestimiento a las grietas.
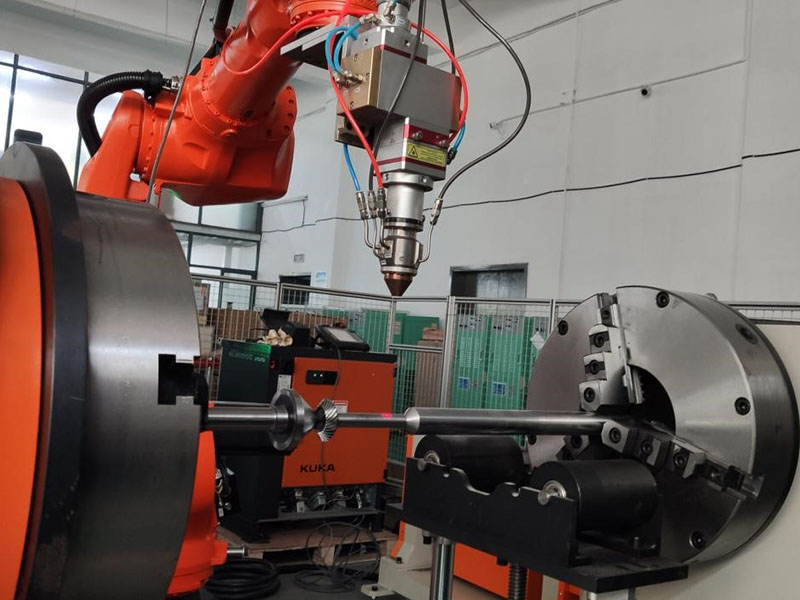
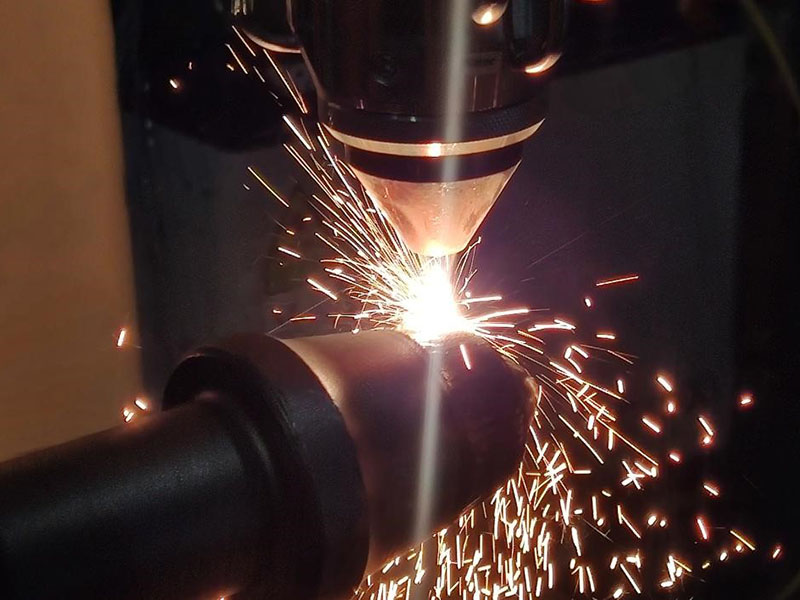
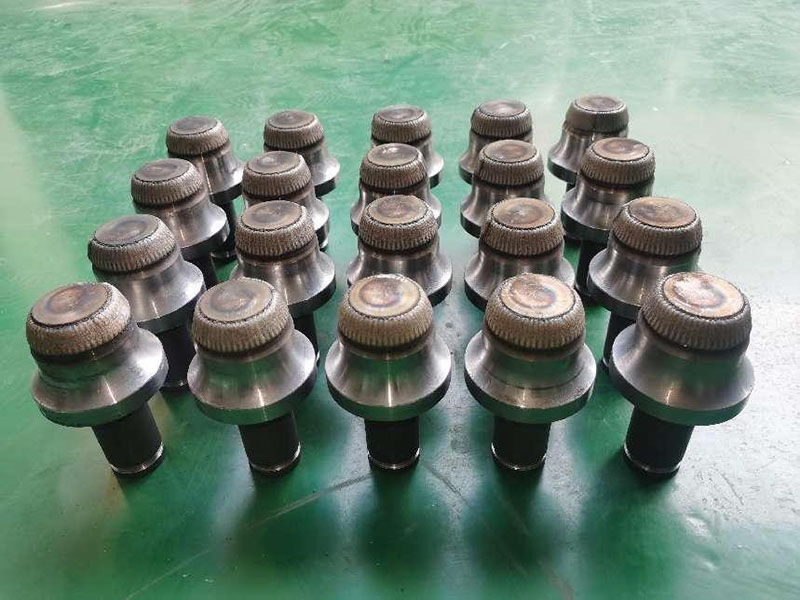
Hora de publicación: 15 de agosto de 2023