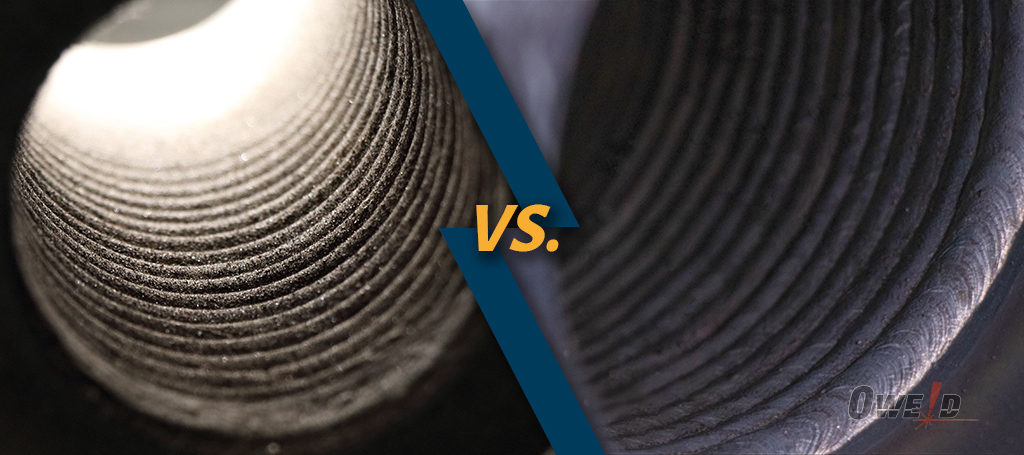
Comparación de PTA con recubrimientos para soldadura TIG y MIG
La tecnología de revestimiento por soldadura es un método importante para mejorar las propiedades superficiales de los metales y se utiliza ampliamente en componentes críticos para la resistencia al desgaste y a la corrosión, así como en entornos de alta temperatura. Entre ellos, los procesos de soldadura PTA, TIG y MIG se han convertido en las tres opciones principales para la preparación de revestimientos gracias a sus ventajas únicas.
Asociación de Padres y Maestrossatisface las necesidades de condiciones de trabajo extremas con una capacidad de deposición precisa y eficiente;TIGEs adecuado para campos de alta precisión gracias a su excelente calidad de soldadura; y el MIG es el preferido en la industria por su alta eficiencia y sus ventajas en aplicaciones de gran superficie. La elección del proceso adecuado no solo afecta el rendimiento de la capa de recubrimiento, sino que también determina la eficiencia y el costo de producción.
¿Cómo elegir el proceso adecuado para crear la capa de recubrimiento ideal? En este artículo, analizaremos brevemente las características y los escenarios de aplicación de los tres procesos para ayudarle a encontrar fácilmente la mejor solución.
PTA (Soldadura por arco de plasma), TIG (soldadura con gas inerte de tungsteno)yMIG (Soldadura por fusión con gas inerte)Existen tres procesos de soldadura comunes. A continuación, se comparan en la aplicación de recubrimientos soldados:
I. Principio de soldadura
1. PTA (Soldadura por arco de plasma transferido)
- Utilizando un arco de plasma de alta temperatura como fuente de calor, el metal fundido se puede depositar con precisión sobre el material base.
- Es adecuado para la preparación de capas de cubierta de alta dureza, resistentes al desgaste y a la corrosión.
2. TIG (soldadura con gas inerte de tungsteno)
- El electrodo está basado en un polo de tungsteno y se utiliza un gas inerte (por ejemplo, argón) para proteger el baño fundido.
- Generalmente requiere la adición manual de metal de relleno, bajo aporte de calor y alta calidad de soldadura.
3. MIG (soldadura de metal con gas inerte)
- El uso de alambre de metal fundido como electrodo, alimentación automática de alambre, el gas protector es principalmente gas inerte o gas mixto.
- Mayor eficiencia de fusión, adecuado para soldadura de capas de cobertura de áreas grandes.
II. Características principales
Características | Asociación de Padres y Maestros | TIG | MIG |
Temperatura de la fuente de calor | Muy alta (>16.000°C) | Alto | Medio |
Eficiencia de fusión | Medio | Bajo | Alto |
Precisión del control de procesos (adecuado para aplicaciones de áreas grandes) | Alto (permite un control preciso) | Muy alto (adecuado para soldadura fina) | Bajo |
Velocidad de soldadura | Medio | Bajo | Alto |
Compatibilidad de materiales | Amplia gama | Amplia gama | Gama bastante amplia |
Calidad de la soldadura (propenso a salpicaduras) | Muy alta (buena unión metalúrgica) | Muy alta (superficie plana, sin porosidad) | Alto |
Zona afectada por el calor | Pequeño | Pequeñito | Grande |
Dificultad de operación | Alto (requiere equipo especializado) | Más alto | Más bajo |
III. Comparación del rendimiento de los recubrimientos soldados
1. Dureza y resistencia al desgaste.
-Asociación de Padres y Maestros:Debido a la alta concentración de temperatura, la capa de revestimiento de fusión tiene una buena unión metalúrgica con el material base y tiene la mejor dureza y resistencia al desgaste.
- TIG: segunda mejor opción, adecuado para escenarios que requieren alta calidad pero menores requisitos de dureza.
- MIG: Debido al alto aporte de calor, la dureza de la capa superpuesta puede ser ligeramente menor y la resistencia al desgaste es moderada.
2. Resistencia a la corrosión
- PTA: Se puede lograr una resistencia a la corrosión extremadamente alta mediante un control preciso de la composición de la aleación.
- TIG: mejor resistencia a la corrosión, pero baja eficiencia de fusión, el espesor de la capa de cobertura puede ser insuficiente.
- MIG: resistencia a la corrosión general, pero adecuado para la preparación de capas de cobertura más gruesas.
3. Fuerza de unión
- PTA: la más alta resistencia de unión, adecuada para condiciones de trabajo de alta resistencia.
- TIG: La fuerza de unión es un poco inferior, pero el acabado superficial es alto.
- MIG: fuerza de unión relativamente baja, fácil producción de poros o inclusiones.
4. Uniformidad de la capa de cobertura
- PTA: Muy alta uniformidad, adecuada para superficies exigentes.
- TIG: Segunda mejor uniformidad, pero la operación manual puede generar una consistencia deficiente.
- MIG: La capa de cobertura es más gruesa y la uniformidad puede no ser tan buena como la de los otros dos métodos.
IV. Ámbito de aplicación
1. Asociación de Padres y Maestros
- Se utiliza para preparar recubrimientos funcionales con alta dureza, resistencia al desgaste y a la corrosión.
- Aplicaciones típicas: industria aeroespacial, industria nuclear, refuerzo de superficies de moldes.
2. TIG
- Se utiliza para requisitos de alta calidad de piezas pequeñas o piezas de precisión de la capa de cubierta.
- Aplicaciones típicas: equipos para la industria alimentaria, reparación de tuberías de acero inoxidable, etc.
3. MIG
- Se utiliza para cubrir un área grande, ocasiones de alta productividad.
- Aplicaciones típicas: reparación de piezas estructurales de gran tamaño, revestimiento de capas resistentes al desgaste, etc.
V. Resumen
Características | Asociación de Padres y Maestros | TIG | MIG |
ventaja | Alta precisión, alta dureza, alta resistencia al desgaste. | Alto acabado superficial. Funcionamiento flexible. | Alta eficiencia, aplicaciones de áreas grandes |
desventajas | Equipos complejos y costosos | Revestimiento ineficiente y que consume mucho tiempo | Mala homogeneidad y grandes áreas afectadas por el calor |
Escenarios aplicables | Equipos de revestimiento de alta gama | Restauraciones y superposiciones de alta calidad | Revestimiento y reparación rápidos |
Dependiendo de las necesidades específicas de las condiciones de trabajo, se puede seleccionar un proceso de soldadura adecuado para lograr el equilibrio entre los requisitos de productividad y rendimiento.
Hora de publicación: 12 de diciembre de 2024